Introduction
Circuit testability is a crucial aspect of circuit board design that ensures the reliability and functionality of electronic devices. In today’s rapidly evolving technological landscape, the complexity of circuit boards continues to increase, making it essential to incorporate testability considerations into the design process. This article explores the importance of circuit testability, the techniques used to enhance it, and the benefits it brings to the manufacturing and maintenance of electronic products.
What is Circuit Testability?
Circuit testability refers to the ease and effectiveness with which a circuit board can be tested for defects, faults, and functionality. It is a measure of how well a circuit board is designed to facilitate testing, both during the manufacturing process and throughout its operational lifetime. A highly testable circuit board allows for efficient fault detection, isolation, and diagnosis, reducing the time and cost associated with troubleshooting and repair.
Key Aspects of Circuit Testability
- Accessibility: The ability to access test points and components on the circuit board for testing purposes.
- Controllability: The ease with which input signals can be applied to the circuit board to stimulate specific parts of the circuit.
- Observability: The ability to observe and measure the output signals and internal states of the circuit board during testing.
- Fault Coverage: The percentage of potential faults that can be detected and isolated through testing.
Importance of Circuit Testability
Incorporating testability into circuit board design offers numerous benefits, including:
- Early Fault Detection: Testability enables the identification of defects and faults early in the manufacturing process, reducing the chances of defective products reaching the market.
- Reduced Manufacturing Costs: Early fault detection minimizes the need for rework and reduces the overall manufacturing costs.
- Improved Product Quality: Testable designs ensure that only high-quality, fully functional products are delivered to customers.
- Simplified Maintenance: Testability features facilitate easier troubleshooting and repair during the product’s operational lifetime, reducing downtime and maintenance costs.
- Enhanced Reliability: Thorough testing and fault isolation contribute to the overall reliability and longevity of the electronic device.
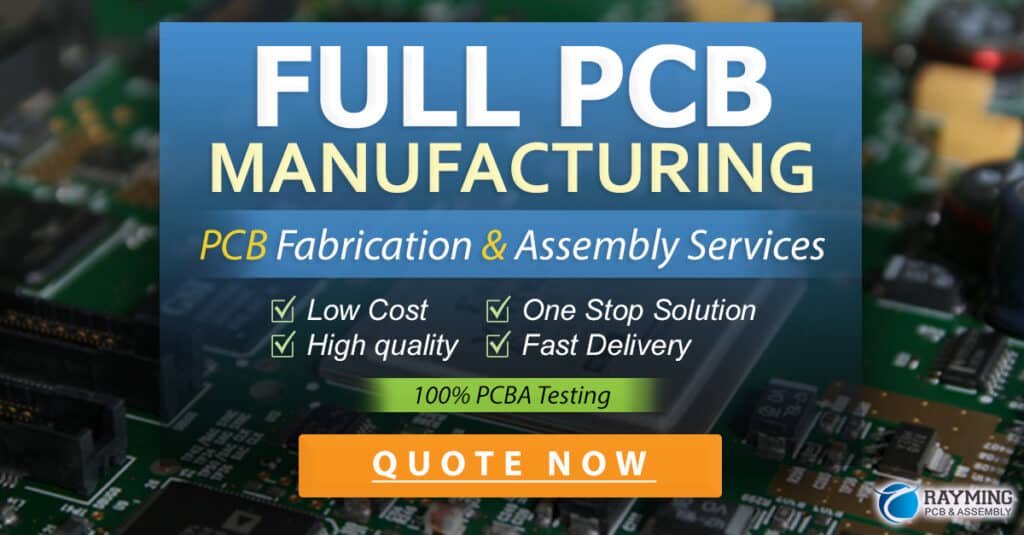
Techniques for Enhancing Circuit Testability
1. Design for Test (DFT)
Design for Test (DFT) is a methodology that incorporates testability features into the circuit board design from the early stages. DFT techniques include:
- Boundary Scan: Implementing boundary scan architecture, such as IEEE 1149.1 (JTAG), enables access to internal nodes and components for testing.
- Built-In Self-Test (BIST): Integrating self-test capabilities into the circuit board allows for autonomous testing and fault detection.
- Scan Chain Design: Designing scan chains facilitates access to internal flip-flops and registers for testing purposes.
2. Test Point Placement
Strategic placement of test points on the circuit board enhances accessibility and observability during testing. Considerations for test point placement include:
- Critical Nodes: Placing test points at critical nodes, such as clock signals, power supplies, and key interfaces, enables effective monitoring and fault isolation.
- Component Access: Ensuring test points are accessible for probing and measurement, considering component packaging and board layout.
- Signal Integrity: Choosing test point locations that minimize signal integrity issues, such as reflections and crosstalk.
3. Boundary Scan Testing
Boundary scan testing, based on the IEEE 1149.1 standard, is a powerful technique for testing complex circuit boards. It involves:
- Boundary Scan Cells: Incorporating boundary scan cells at the input and output pins of selected components enables controllability and observability.
- Test Access Port (TAP): Providing a dedicated test access port for controlling the boundary scan architecture and accessing internal nodes.
- Boundary Scan Description Language (BSDL): Using BSDL to describe the boundary scan architecture and enable automated test pattern generation.
4. Automatic Test Pattern Generation (ATPG)
ATPG is a software-based technique that automatically generates test patterns for fault detection and isolation. ATPG tools analyze the circuit design and generate optimized test vectors to achieve maximum fault coverage. Benefits of ATPG include:
- Improved Fault Coverage: ATPG algorithms generate test patterns that target specific faults, ensuring high fault coverage.
- Reduced Test Development Time: Automated test pattern generation reduces the time and effort required for manual test development.
- Optimized Test Sequences: ATPG tools optimize test sequences to minimize test time and maximize fault detection efficiency.
5. Testability Analysis and Optimization
Testability analysis involves evaluating the testability of a circuit board design and identifying areas for improvement. Tools and techniques for testability analysis include:
- Testability Metrics: Calculating testability metrics, such as controllability and observability, to assess the overall testability of the design.
- Fault Simulation: Performing fault simulation to determine the fault coverage and identify hard-to-detect faults.
- Design Optimization: Iteratively optimizing the design based on testability analysis results to improve fault coverage and reduce test complexity.
Best Practices for Testable Circuit Board Design
To achieve optimal circuit testability, consider the following best practices:
- Early Testability Planning: Incorporate testability considerations from the initial stages of the design process, ensuring alignment with overall product requirements.
- Modular Design: Adopt a modular design approach, breaking down the circuit into smaller, testable blocks to facilitate fault isolation and troubleshooting.
- Standardized Interfaces: Use standardized interfaces, such as JTAG or I2C, to enable compatibility with existing test equipment and methodologies.
- Clear Documentation: Maintain clear and comprehensive documentation, including schematics, layout files, and test specifications, to support effective testing and maintenance.
- Collaboration with Test Engineers: Foster close collaboration between design and test engineers to ensure testability requirements are met and to optimize test strategies.
Case Studies
Case Study 1: Aerospace Electronics Manufacturer
An aerospace electronics manufacturer faced challenges in testing complex circuit boards for their avionics systems. By implementing boundary scan testing and ATPG techniques, they achieved:
- 95% fault coverage, ensuring the reliability of their critical systems.
- 40% reduction in test development time, accelerating their time-to-market.
- 60% reduction in manufacturing defects, improving overall product quality.
Case Study 2: Automotive Electronics Supplier
An automotive electronics supplier struggled with the testability of their engine control modules (ECMs). By adopting DFT principles and optimizing test point placement, they accomplished:
- 90% reduction in test time, enabling faster production throughput.
- 80% improvement in fault isolation capability, facilitating efficient troubleshooting.
- 50% reduction in warranty claims related to ECM failures, enhancing customer satisfaction.
Frequently Asked Questions (FAQ)
-
Q: What is the difference between testability and reliability?
A: Testability refers to the ease and effectiveness of testing a circuit board for defects and functionality, while reliability is the ability of the circuit board to perform its intended function over a specified period without failure. Testability contributes to reliability by enabling the detection and removal of defects before the product reaches the market. -
Q: Can testability be added to an existing circuit board design?
A: While it is more challenging to add testability features to an existing design, it is possible to improve testability through techniques such as test point addition, boundary scan integration, and targeted design modifications. However, incorporating testability from the early stages of the design process is more effective and efficient. -
Q: How does testability impact product cost?
A: Incorporating testability features may slightly increase the initial design and manufacturing costs. However, the long-term benefits, such as reduced manufacturing defects, faster troubleshooting, and lower maintenance costs, often outweigh the initial investment. Testability ultimately contributes to cost savings throughout the product lifecycle. -
Q: What are the challenges in implementing testability in high-speed designs?
A: High-speed designs pose challenges for testability due to signal integrity issues, such as reflections, crosstalk, and timing constraints. Careful test point placement, impedance matching, and signal integrity analysis are crucial to ensure reliable testing without compromising the performance of the high-speed circuits. -
Q: How can testability be measured and evaluated?
A: Testability can be measured and evaluated using various metrics and techniques, such as fault coverage, controllability, observability, and test coverage. Testability analysis tools and fault simulation can provide quantitative measures of testability, helping designers identify areas for improvement and optimize the design for enhanced testability.
Conclusion
Circuit testability is a vital aspect of circuit board design that directly impacts the quality, reliability, and maintainability of electronic products. By incorporating testability considerations into the design process, manufacturers can detect and isolate faults early, reduce manufacturing costs, and improve overall product performance. Techniques such as Design for Test (DFT), strategic test point placement, boundary scan testing, and automatic test pattern generation (ATPG) enable designers to create highly testable circuit boards.
As the complexity of electronic systems continues to grow, prioritizing circuit testability becomes increasingly important. By adopting best practices and leveraging advanced tools and methodologies, designers can overcome the challenges associated with testing complex circuits and deliver reliable, high-quality products to the market. Investing in circuit testability not only benefits manufacturers but also ensures customer satisfaction and long-term success in the competitive electronics industry.
Leave a Reply