Introduction to Multilayer PCBs
Multilayer printed circuit boards (PCBs) are essential components in modern electronics, offering increased circuit density, improved signal integrity, and reduced electromagnetic interference (EMI). When designing a multilayer PCB, one of the critical decisions is choosing the right substrate material. Two common options are ceramic and FR4. In this article, we will explore the differences between ceramic and FR4 multilayer PCBs, their respective advantages and disadvantages, and when to use each type.
What are Ceramic Multilayer PCBs?
Ceramic multilayer PCBs are constructed using thin layers of ceramic substrate, typically alumina (Al2O3) or aluminum nitride (AlN). These layers are stacked together with conductive traces and vias to form a complete circuit. Ceramic PCBs offer several advantages over traditional FR4 boards, including:
- High thermal conductivity
- Low dielectric constant
- Excellent dimensional stability
- High resistance to moisture and chemicals
Advantages of Ceramic Multilayer PCBs
-
Thermal management: Ceramic substrates have high thermal conductivity, allowing for efficient heat dissipation. This makes them ideal for high-power applications or circuits with high operating temperatures.
-
High-frequency performance: The low dielectric constant of ceramic materials results in lower signal loss and reduced crosstalk, making ceramic PCBs suitable for high-frequency applications such as RF and microwave circuits.
-
Dimensional stability: Ceramic materials have a low coefficient of thermal expansion (CTE), which means they maintain their dimensions even under varying temperatures. This stability is crucial for applications requiring tight tolerances, such as aerospace and military electronics.
-
Environmental resistance: Ceramic PCBs are highly resistant to moisture, chemicals, and other environmental factors, making them suitable for harsh operating conditions.
Disadvantages of Ceramic Multilayer PCBs
-
Higher cost: Ceramic substrates are more expensive than FR4, and the manufacturing process for ceramic PCBs is more complex, resulting in higher overall costs.
-
Limited flexibility: Ceramic materials are brittle and have limited flexibility compared to FR4. This can make them less suitable for applications requiring flexible or bendable PCBs.
-
Manufacturing challenges: Drilling and machining ceramic substrates require specialized equipment and techniques, which can increase production time and costs.
What are FR4 Multilayer PCBs?
FR4 (Flame Retardant 4) is a glass-reinforced epoxy laminate material commonly used in PCB manufacturing. FR4 multilayer PCBs are constructed by stacking multiple layers of FR4 substrate with conductive traces and vias. FR4 is the most widely used substrate material for PCBs due to its balanced properties and cost-effectiveness.
Advantages of FR4 Multilayer PCBs
-
Cost-effective: FR4 is less expensive than ceramic substrates, making it a more economical choice for many applications.
-
Versatility: FR4 PCBs can be used in a wide range of applications, from consumer electronics to industrial control systems.
-
Easier manufacturing: FR4 is easier to drill, machine, and process compared to ceramic substrates, resulting in faster production times and lower manufacturing costs.
-
Good electrical properties: FR4 has a relatively low dielectric constant and good insulation properties, making it suitable for most general-purpose electronic applications.
Disadvantages of FR4 Multilayer PCBs
-
Lower thermal conductivity: FR4 has a lower thermal conductivity compared to ceramic substrates, which can limit its use in high-power or high-temperature applications.
-
Higher signal loss: The higher dielectric constant of FR4 can result in higher signal loss and crosstalk, especially at high frequencies.
-
Moisture absorption: FR4 can absorb moisture, which can lead to dimensional changes and degradation of electrical properties over time.
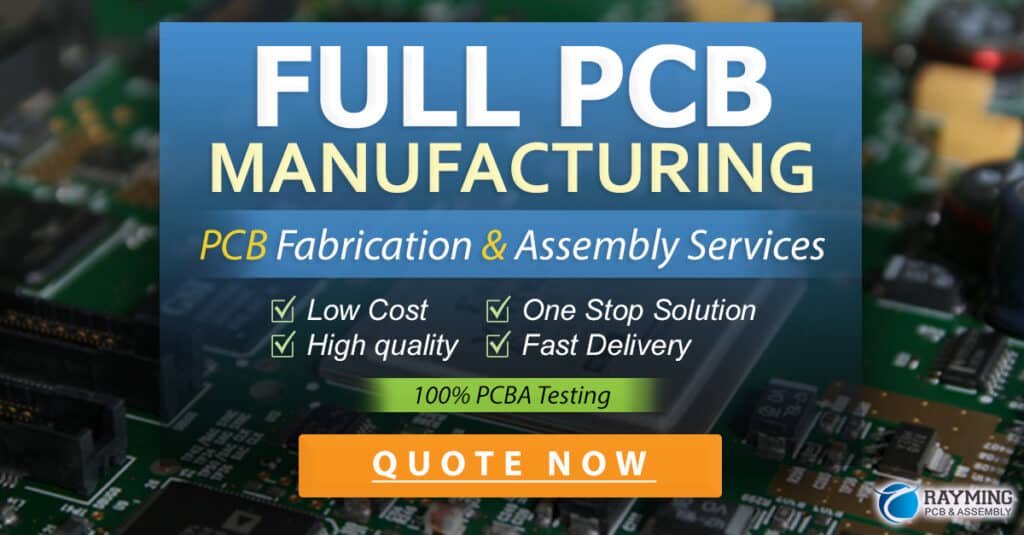
Comparing Ceramic and FR4 Multilayer PCBs
Property | Ceramic | FR4 |
---|---|---|
Thermal conductivity | High | Low to moderate |
Dielectric constant | Low | Moderate |
Dimensional stability | Excellent | Good |
Environmental resistance | High | Moderate |
Cost | High | Low to moderate |
Flexibility | Limited | Good |
Manufacturing ease | Challenging | Easier |
Typical applications | High-power, RF, aerospace, military | General-purpose, consumer electronics, industrial control |
When to Use Ceramic Multilayer PCBs
Ceramic multilayer PCBs are the preferred choice in the following situations:
-
High-power applications: When dealing with circuits that generate a significant amount of heat, such as power amplifiers or high-current power supplies, ceramic PCBs offer superior thermal management.
-
High-frequency applications: For RF, microwave, and other high-frequency circuits, ceramic PCBs provide lower signal loss and reduced crosstalk, ensuring better signal integrity.
-
Harsh environments: In applications exposed to extreme temperatures, moisture, or chemicals, ceramic PCBs offer excellent resistance and reliability.
-
Tight tolerance requirements: When dimensional stability is critical, such as in aerospace or military electronics, ceramic PCBs maintain their dimensions even under varying temperatures.
When to Use FR4 Multilayer PCBs
FR4 multilayer PCBs are the preferred choice in the following situations:
-
General-purpose electronics: For most consumer electronics, industrial control systems, and other general-purpose applications, FR4 PCBs offer a cost-effective and versatile solution.
-
Budget-constrained projects: When cost is a primary concern, FR4 PCBs are a more economical choice compared to ceramic PCBs.
-
Flexible or bendable circuits: FR4 PCBs can be designed with a certain degree of flexibility, making them suitable for applications requiring bendable or flexible circuits.
-
Rapid prototyping and production: The easier manufacturing process and wider availability of FR4 PCBs make them ideal for rapid prototyping and faster production times.
How to Design and Manufacture Ceramic Multilayer PCBs
Designing and manufacturing ceramic multilayer PCBs requires specialized knowledge and equipment. Here are some key considerations:
-
Substrate selection: Choose the appropriate ceramic substrate (alumina or aluminum nitride) based on the application requirements, such as thermal conductivity and dielectric constant.
-
Layer stack-up: Design the layer stack-up, considering the number of layers, layer thickness, and via placement to ensure optimal signal integrity and manufacturability.
-
Thermal management: Incorporate thermal vias and heat spreaders to efficiently dissipate heat generated by components.
-
Manufacturing process: Work with a PCB manufacturer experienced in ceramic PCB fabrication, as the process involves specialized techniques such as co-firing and laser drilling.
-
Testing and quality control: Implement rigorous testing and quality control measures to ensure the ceramic PCBs meet the required specifications and reliability standards.
How to Design and Manufacture FR4 Multilayer PCBs
Designing and manufacturing FR4 multilayer PCBs is a more standardized process compared to ceramic PCBs. Here are some key considerations:
-
Layer stack-up: Design the layer stack-up, considering the number of layers, layer thickness, and via placement to ensure optimal signal integrity and manufacturability.
-
Material selection: Choose the appropriate FR4 laminate based on the application requirements, such as the glass transition temperature (Tg) and dielectric constant.
-
Signal integrity: Implement proper signal integrity techniques, such as impedance matching, termination, and ground planes, to minimize signal loss and crosstalk.
-
Manufacturing process: Work with a reputable PCB manufacturer and provide accurate design files and specifications to ensure a smooth fabrication process.
-
Testing and quality control: Perform necessary testing and quality control measures to ensure the FR4 PCBs meet the required specifications and reliability standards.
Frequently Asked Questions (FAQ)
-
Q: Can ceramic and FR4 materials be combined in a single multilayer PCB?
A: Yes, it is possible to create a hybrid multilayer PCB that combines ceramic and FR4 layers. This approach can offer the benefits of both materials in specific applications, such as using ceramic layers for high-power or RF sections and FR4 layers for general-purpose circuitry. -
Q: What is the typical cost difference between ceramic and FR4 multilayer PCBs?
A: Ceramic multilayer PCBs can be several times more expensive than FR4 PCBs, depending on the specific material, layer count, and manufacturing complexity. In general, ceramic PCBs can cost 3 to 10 times more than equivalent FR4 PCBs. -
Q: Are there any environmental concerns associated with the use of ceramic or FR4 PCBs?
A: Both ceramic and FR4 PCBs can be manufactured in an environmentally friendly manner. However, some FR4 laminates may contain halogenated flame retardants, which can be a concern for disposal and recycling. Ceramic PCBs are generally considered more environmentally friendly due to their inert nature and long-term stability. -
Q: What are the limitations on the minimum feature sizes for ceramic and FR4 multilayer PCBs?
A: The minimum feature sizes for ceramic and FR4 multilayer PCBs depend on the specific manufacturing process and equipment used. In general, FR4 PCBs can achieve smaller feature sizes and tighter tolerances compared to ceramic PCBs. However, advanced ceramic PCB manufacturing techniques, such as laser drilling and high-resolution patterning, can enable feature sizes comparable to FR4 PCBs. -
Q: How do the lead times compare for ceramic and FR4 multilayer PCB manufacturing?
A: Lead times for ceramic multilayer PCBs are typically longer than those for FR4 PCBs due to the more complex manufacturing process and specialized equipment required. Ceramic PCBs may have lead times of several weeks to months, while FR4 PCBs can often be manufactured within days to weeks, depending on the complexity and volume of the order.
Conclusion
Choosing between ceramic and FR4 multilayer PCBs depends on the specific application requirements, such as thermal management, high-frequency performance, environmental resistance, and cost constraints. Ceramic PCBs excel in high-power, high-frequency, and harsh environment applications, while FR4 PCBs offer a cost-effective and versatile solution for general-purpose electronics.
When designing and manufacturing multilayer PCBs, it is essential to consider factors such as substrate selection, layer stack-up, signal integrity, thermal management, and manufacturing processes. Working with experienced PCB manufacturers and following best practices in design and quality control can help ensure the successful development and production of both ceramic and FR4 multilayer PCBs.
As technology advances, new materials and manufacturing techniques may emerge, offering even better performance and cost-effectiveness for multilayer PCBs. Staying informed about the latest developments in PCB technology and working closely with PCB manufacturers can help engineers and designers make the best choices for their specific applications.
Leave a Reply