Introduction to Cave Markings and PCBs
In ancient times, humans used cave markings to record information and communicate ideas. These early forms of visual communication paved the way for more advanced methods like written language. In the modern era, another type of “cave marking” is used extensively in electronics – the printed circuit board (PCB) assembly drawing.
PCBs are the building blocks of nearly all electronic devices. They mechanically support and electrically connect electronic components using conductive tracks, pads and other features etched from one or more sheet layers of copper laminated onto and/or between sheet layers of a non-conductive substrate. Components are generally soldered onto the PCB to both electrically connect and mechanically fasten them to it.
Just as cave markings were essential for conveying key information to ancient peoples, PCB assembly drawings are critical for communicating the design intent to the manufacturers who will build the board. Being able to properly read and interpret these drawings is a fundamental skill for anyone involved in electronics design or manufacturing.
The Basics of PCB Assembly Drawings
A PCB assembly drawing, also known as a PCB layout or PCB artwork, is a 2D representation of the printed circuit board. It shows the exact size and location of all the components, tracks, holes, and text on the board. The drawing is used by PCB fabrication houses to manufacture the bare board, and by assembly shops to place and solder components onto the board.
PCB assembly drawings are typically created using specialized PCB design software like Altium Designer, Eagle, or KiCad. The software allows the designer to layout the board virtually, routing connections between components. Once the design is complete, the software can generate the fabrication and assembly files needed for manufacturing.
The most common file format for PCB assembly drawings is Gerber, which has been the industry standard for over 50 years. Gerber files are ASCII vector format files that describe each layer of the board – copper, solder mask, silk screen, drill holes, etc. Each layer gets its own Gerber file, so a complete PCB design will have multiple Gerbers associated with it.
In addition to the Gerber files, a complete PCB design package will also include drill files (typically Excellon format), a bill of materials (BOM), and placement files (like CSV or IPC-D-356) that specify where each component goes on the board. Some designs may also include 3D models, schematics, and test procedures.
Interpreting the PCB Assembly Drawing
Now that we understand what a PCB assembly drawing is and what files are typically included, let’s dive into how to actually read and interpret the drawing. We’ll focus primarily on the Gerber files, as they contain the bulk of the information needed for assembly.
Board Outline and Dimensions
The first thing to check on any PCB assembly drawing is the board outline and dimensions. The board outline shows the actual shape and size of the PCB. It’s important to verify that the outline matches your expectations and will fit properly in the intended enclosure or device.
PCB dimensions are typically specified using metric units (millimeters), although some designs may use imperial units (inches). The dimensions should be clearly labeled on the drawing, along with any special features like cutouts, notches, or bevels.
It’s also important to check the board thickness and the number of layers. These specifications impact the manufacturing process and can affect the cost and lead time for the project.
Layer Stackup
The layer stackup is a cross-sectional view of the PCB that shows the arrangement of copper and insulating layers. It specifies the thickness and material of each layer, as well as their order in the stack. The stackup is critical for ensuring proper impedance control, signal integrity, and manufacturability.
Most PCB assembly drawings will include a stackup table or diagram. It’s important to review this information carefully and make sure it matches the design intent. Pay close attention to the copper weights (thickness) and the dielectric constants of the insulating layers.
Drill Holes and Vias
Drill holes and vias are used to make connections between layers on the PCB. Drill holes are used for through-hole components, while vias are used for interlayer connections in multi-layer boards. The size and location of these features are specified in the drill files.
When reviewing the drill files, check the hole sizes and make sure they match the components being used. Also verify that the holes are properly located and will not interfere with other features on the board. Some designs may use special types of vias, like blind or buried vias, which are important to note.
Components and Footprints
The component footprints show where each part will be placed on the PCB. The footprints should match the actual dimensions of the components being used, including the pad size, shape, and pitch. It’s important to verify that the footprints are correct and properly oriented on the board.
Pay close attention to polarized components like electrolytic capacitors, diodes, and ICs. The polarity marking on the footprint should match the marking on the actual component. Also check for any special requirements like thermal pads, keep-out areas, or fiducial markers.
The component designators (reference designators) should be clearly marked on the silk screen layer. These designators are used to identify each component on the BOM and placement files. Make sure the designators are correct and match the schematic.
Routing and Copper Pour
The copper traces on the PCB are used to make electrical connections between components. The width and spacing of these traces impact the current carrying capacity and impedance of the signal. It’s important to verify that the traces are properly sized for the expected current load and that they maintain the required clearance from other features.
Copper pour (also known as a ground plane or power plane) is used to provide a low-impedance path for power and ground connections. The pour should be properly connected to the relevant nets and should not create any unintended short circuits. Check the Gerber files to make sure the pour is correct and free of any defects.
Silk Screen and Assembly Notes
The silk screen layer is used to print text and graphics on the PCB. This can include component designators, company logos, warning labels, and other important information. Check the silk screen for clarity and accuracy, and make sure it does not overlap with any pads or other features.
Assembly notes are special instructions for the manufacturer that are typically printed on the silk screen or included as a separate document. These notes can cover things like special handling requirements, testing procedures, or packaging instructions. Make sure to review these notes carefully and verify that they are complete and accurate.
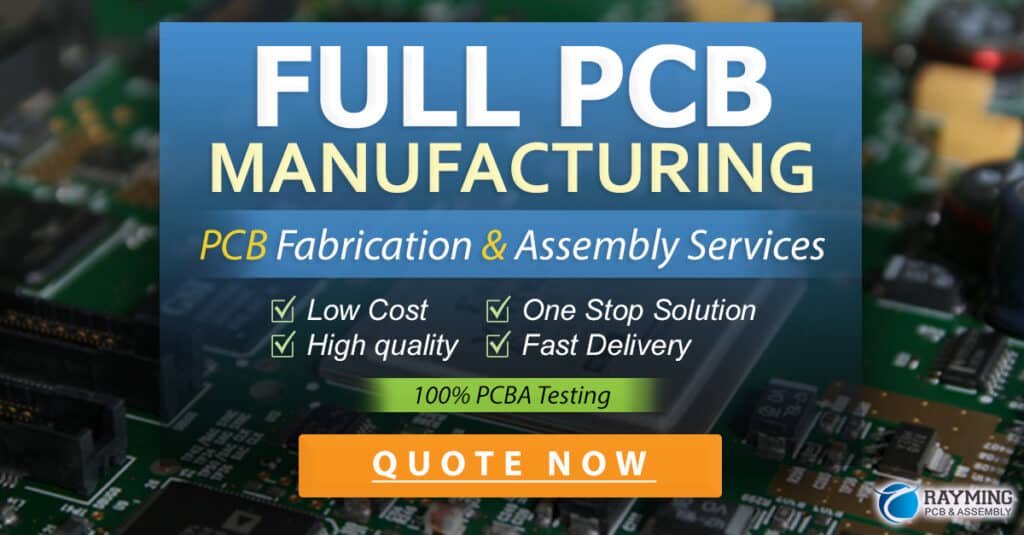
Common Pitfalls and Best Practices
Reading PCB assembly drawings can be challenging, especially for complex designs. Here are some common pitfalls to watch out for:
- Incorrect units: Make sure all dimensions and measurements are specified in the correct units (metric or imperial). Mixing units can lead to costly errors.
- Incorrect layer mapping: Verify that the Gerber files are properly mapped to the correct layers in the stackup. Incorrect mapping can cause shorts, opens, or other defects.
- Inaccurate BOM: The bill of materials should match the components used in the design. Inaccurate or incomplete BOMs can cause assembly errors and delays.
- Outdated or incomplete files: Make sure all files (Gerbers, drill files, BOM, etc.) are up to date and complete. Using outdated or incomplete data can result in manufacturing errors.
To avoid these pitfalls and ensure a successful PCB assembly, follow these best practices:
- Use a checklist to review each aspect of the assembly drawing systematically
- Double-check all dimensions, components, and special requirements
- Use automated DFM (design for manufacturability) tools to check for errors and potential issues
- Communicate clearly with the manufacturer and provide complete, accurate data
- Request a design review or prototype before committing to a full production run
FAQ
Q: What is a Gerber file?
A: A Gerber file is a standard file format used for specifying the printed circuit board (PCB) design data. It is an ASCII vector format that describes the copper layers, solder mask, legend, and other aspects of the PCB. Gerber files are used by PCB manufacturers to produce the actual boards.
Q: What is a drill file?
A: A drill file (typically in Excellon format) specifies the location, size and type of holes to be drilled in the PCB. These holes are used for through-hole components, vias, and mounting. The drill file is used in conjunction with the Gerber files to fully specify the PCB design.
Q: What is a BOM?
A: BOM stands for bill of materials. It is a list of all the components used in the PCB assembly, including their reference designators, descriptions, quantities, manufacturers, and part numbers. The BOM is used by the assembly shop to ensure the correct components are ordered and placed on the board.
Q: What are fiducial markers?
A: Fiducial markers are small copper pads or other features placed on the PCB that serve as reference points for the assembly machines. They are used to align the board correctly and ensure accurate component placement, especially for surface-mount parts. Fiducial markers are typically specified on the assembly drawing.
Q: What is DFM?
A: DFM stands for design for manufacturability. It is the practice of designing products in such a way that they are easy to manufacture reliably and cost-effectively. In PCB design, DFM involves following certain rules and guidelines to ensure the board can be fabricated and assembled without issues. Many PCB design software tools include DFM checking features to help identify and correct potential problems.
Conclusion
PCB assembly drawings are the “cave markings” of the electronics world – they provide essential information for fabricating and assembling printed circuit boards. Being able to read and interpret these drawings is a critical skill for anyone involved in electronics design or manufacturing.
By understanding the different aspects of the assembly drawing – the board outline, drill holes, components, routing, silk screen, and more – you can ensure that your PCB design is accurately communicated to the manufacturer. Following best practices and using automated tools can help catch errors and improve the overall quality of the final product.
As PCB technology continues to evolve, with smaller components, higher frequencies, and greater complexity, the ability to effectively interpret and communicate design intent through assembly drawings will only become more important. By mastering this skill, you can help bring your electronic “cave markings” to life in the form of successful, reliable PCBs.
Leave a Reply