Introduction
When designing a printed circuit board (PCB), one of the most critical aspects to consider is the electrical clearance between various components, traces, and vias. Electrical clearance refers to the minimum distance that must be maintained between conductive elements to prevent unintended electrical connections or short circuits. In this article, we will explore the importance of setting electrical clearance in the design rules for the route tool path and how it can be achieved using various PCB design software.
What is Electrical Clearance?
Electrical clearance, also known as spacing or isolation, is the minimum distance required between two conductive elements on a PCB to prevent electrical short circuits or unintended connections. This distance is typically measured in mils (thousandths of an inch) or millimeters and varies depending on factors such as the voltage level, the manufacturing process, and the PCB material.
Maintaining proper electrical clearance is essential for several reasons:
-
Preventing short circuits: Insufficient clearance between conductive elements can lead to short circuits, which can cause the PCB to malfunction or even damage the components.
-
Ensuring signal integrity: Proper clearance helps maintain the integrity of signals by reducing crosstalk and electromagnetic interference (EMI) between adjacent traces.
-
Meeting industry standards: Various industry standards, such as IPC (Association Connecting Electronics Industries), specify minimum clearance requirements for different voltage levels and PCB classes.
-
Facilitating manufacturing: Adequate clearance makes the PCB easier to manufacture and reduces the likelihood of defects during the fabrication process.
Setting Electrical Clearance in Design Rules
To ensure that your PCB design adheres to the required electrical clearance, you need to set the appropriate design rules in your PCB design software. Design rules are a set of constraints that define the minimum and maximum values for various parameters, such as trace width, via size, and clearance between objects.
Most PCB design software packages, such as Altium Designer, KiCad, and Eagle, allow you to set electrical clearance rules for different net classes or object types. Here’s a general overview of how to set electrical clearance in design rules:
-
Define net classes: Group nets with similar characteristics (e.g., power, ground, signal) into classes. This allows you to assign specific clearance rules to each class.
-
Set clearance rules: In the design rules editor, create clearance rules for each net class or object type. Specify the minimum clearance required between objects of the same class or between different classes.
-
Assign net classes: Assign the appropriate net class to each net in your design. This ensures that the clearance rules associated with the net class are applied to the nets.
-
Run design rule checks (DRC): Perform a DRC to verify that your design complies with the specified clearance rules. The DRC will identify any violations and provide feedback on how to resolve them.
Here’s an example of how to set electrical clearance rules in Altium Designer:
- Open the PCB file and navigate to the “Design” menu.
- Select “Rules” to open the PCB Rules and Constraints Editor.
- In the left pane, expand the “Electrical” category and select “Clearance.”
- Create a new clearance rule by clicking the “New Rule” button.
- Specify the scope of the rule (e.g., All), the object types (e.g., Tracks, Pads), and the minimum clearance value.
- Click “Apply” to save the rule.
Object Type | Clearance Value (mils) |
---|---|
Tracks | 10 |
Pads | 15 |
Vias | 20 |
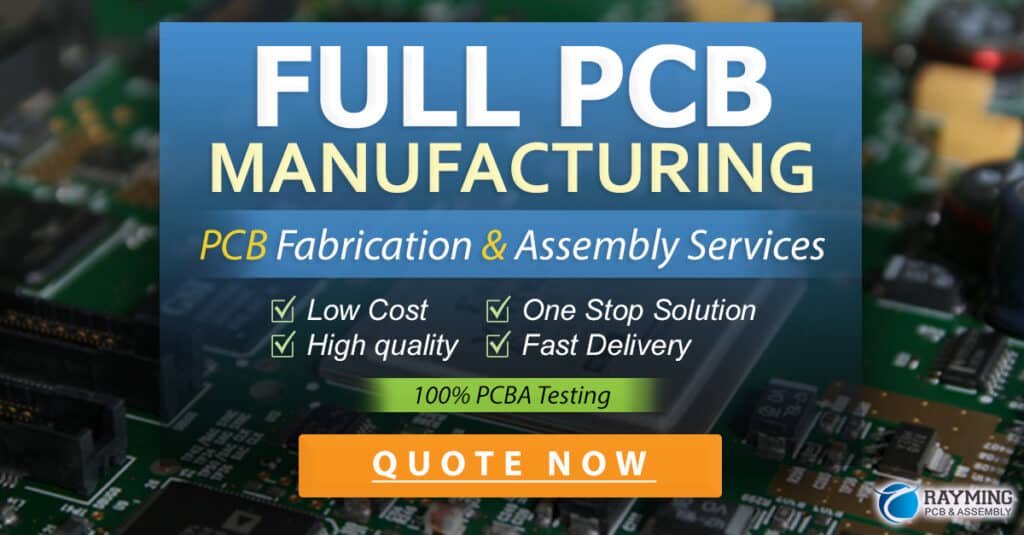
Electrical Clearance and the Route Tool Path
The route tool path in PCB design software is used to create connections between components by routing traces on the PCB. When routing traces, it is crucial to consider the electrical clearance rules to ensure that the routed traces maintain the required minimum distance from other objects.
Most PCB design software packages have built-in features that help you route traces while adhering to the clearance rules:
-
Online DRC: Some software, like Altium Designer, perform real-time DRC checks as you route traces. This feature alerts you if a trace violates any clearance rules, allowing you to make immediate adjustments.
-
Interactive routing: Interactive routing tools, such as the “Follow Me” router in KiCad, automatically maintain the specified clearance between the trace being routed and other objects on the PCB.
-
Push and shove: Push and shove routing algorithms automatically move existing traces to accommodate the trace being routed while maintaining the required clearance.
-
Differential pair routing: When routing differential pairs, the software ensures that the traces maintain the specified clearance and symmetry to minimize crosstalk and maintain signal integrity.
Routing Feature | Description |
---|---|
Online DRC | Real-time DRC checks during routing |
Interactive routing | Automatically maintains clearance while routing |
Push and shove | Adjusts existing traces to maintain clearance |
Differential pair routing | Ensures clearance and symmetry for differential pairs |
By leveraging these routing features and adhering to the electrical clearance rules, you can create a PCB design that is both functional and manufacturable.
Best Practices for Setting Electrical Clearance
When setting electrical clearance rules for your PCB design, consider the following best practices:
-
Consult the manufacturer: Discuss the minimum clearance requirements with your PCB manufacturer to ensure that your design is compatible with their fabrication processes.
-
Follow industry standards: Adhere to the minimum clearance requirements specified by industry standards, such as IPC-2221, for your specific application and voltage levels.
-
Consider the voltage level: Adjust the clearance values based on the voltage levels present in your design. Higher voltages generally require greater clearance to prevent arcing and ensure safety.
-
Account for manufacturing tolerances: Include additional clearance to accommodate manufacturing tolerances and variations in the fabrication process.
-
Use net classes: Group nets with similar characteristics into classes and assign appropriate clearance rules to each class. This helps keep your design organized and ensures that the correct rules are applied throughout the design.
-
Perform frequent DRC checks: Run DRC checks regularly during the design process to identify and resolve any clearance violations early on.
Voltage Level | Minimum Clearance (mils) |
---|---|
< 50V | 5 |
50V – 100V | 10 |
100V – 150V | 15 |
> 150V | 20 |
Conclusion
Setting electrical clearance in the design rules for the route tool path is a critical step in creating a reliable and manufacturable PCB. By understanding the importance of electrical clearance, setting appropriate design rules, and leveraging the routing features of your PCB design software, you can ensure that your PCB design maintains the required minimum distances between conductive elements.
Remember to consult with your PCB manufacturer, follow industry standards, and perform frequent DRC checks to identify and resolve any clearance issues. By adhering to best practices and considering factors such as voltage levels and manufacturing tolerances, you can create a PCB design that meets both functional and manufacturing requirements.
FAQs
-
What is the difference between electrical clearance and creepage distance?
Electrical clearance refers to the shortest distance through air between two conductive elements, while creepage distance is the shortest path along the surface of the insulating material between two conductive elements. -
How do I determine the appropriate electrical clearance for my PCB design?
The appropriate electrical clearance depends on factors such as the voltage level, the PCB material, and the manufacturing process. Consult industry standards, such as IPC-2221, and discuss the requirements with your PCB manufacturer to determine the suitable clearance values for your design. -
Can I set different electrical clearance rules for different layers of my PCB?
Yes, most PCB design software allows you to set specific clearance rules for each layer of your PCB. This is useful when you have different voltage levels or signal types on different layers. -
What happens if I violate the electrical clearance rules in my PCB design?
Violating electrical clearance rules can lead to various issues, such as short circuits, signal integrity problems, and manufacturing defects. It is essential to identify and resolve any clearance violations before sending your design for fabrication. -
How can I ensure that my PCB design maintains electrical clearance during the routing process?
To ensure that your PCB design maintains electrical clearance during routing, use the built-in features of your PCB design software, such as online DRC checks, interactive routing tools, and push and shove algorithms. These features help you route traces while adhering to the specified clearance rules.
Leave a Reply