What is PCB Warping?
PCB warping is a deformation of the printed circuit board, causing it to bend or twist out of its intended flat shape. This can occur during the manufacturing process or as a result of exposure to certain environmental conditions. Warping can be classified into two main types:
- Convex warping: The PCB bends upwards, forming a dome-like shape.
- Concave warping: The PCB bends downwards, forming a bowl-like shape.
The severity of warping can vary from minor, barely noticeable bends to severe deformations that render the PCB unusable.
Causes of PCB Warping
Several factors can contribute to the warping of a PCB:
1. Thermal Stress
One of the most common causes of PCB warping is thermal stress. During the soldering process, the PCB is exposed to high temperatures, which can cause uneven expansion and contraction of the board material. If the temperature changes are not properly managed, the PCB may warp as it cools down.
Additionally, if the PCB is subjected to repeated thermal cycles (heating and cooling) during its operation, it can lead to gradual warping over time. This is particularly common in devices that generate significant heat, such as power electronics or high-performance computing systems.
2. Moisture Absorption
PCBs are typically made from materials that can absorb moisture from the environment, such as FR-4 (a type of fiberglass-reinforced epoxy laminate). When a PCB absorbs moisture, it can expand and cause warping. This is especially problematic in humid environments or if the PCB is not properly stored in a moisture-controlled environment.
3. Mechanical Stress
Mechanical stress can also lead to PCB warping. This can occur during the handling, transportation, or installation of the PCB. Improper mounting of the PCB in an enclosure, or applying excessive force during the assembly process, can cause the board to bend or twist.
4. Unbalanced Copper Distribution
In multi-layer PCBs, the distribution of copper on different layers can impact the overall balance of the board. If there is a significant imbalance in the copper distribution, it can lead to uneven thermal expansion and contraction, resulting in warping.
5. Manufacturing Defects
In some cases, PCB warping can be attributed to manufacturing defects. Improper handling during the fabrication process, incorrect curing of the PCB materials, or poor quality control can all contribute to warping.
Effects of PCB Warping
Warped PCBs can have several negative effects on the functionality and reliability of electronic devices:
1. Component Misalignment
When a PCB is warped, the components mounted on it may become misaligned. This can lead to poor electrical connections, shorter component lifespans, and even complete failure of the device.
2. Soldering Issues
Warped PCBs can make the soldering process more challenging. If the board is not flat, it can be difficult to achieve proper solder joint formation, leading to weak or unstable connections.
3. Mechanical Stress on Components
The bending and twisting of a warped PCB can put mechanical stress on the components mounted on it. This stress can cause components to crack, break, or become dislodged from the board.
4. Reduced Heat Dissipation
In some cases, PCB warping can affect the heat dissipation capabilities of the board. If the PCB is not making proper contact with a heatsink or other cooling solution, it can lead to overheating and potential damage to the components.
5. Fitment Issues
Warped PCBs may not fit properly into their intended enclosures or connectors. This can cause problems during the assembly process and may require rework or replacement of the PCB.
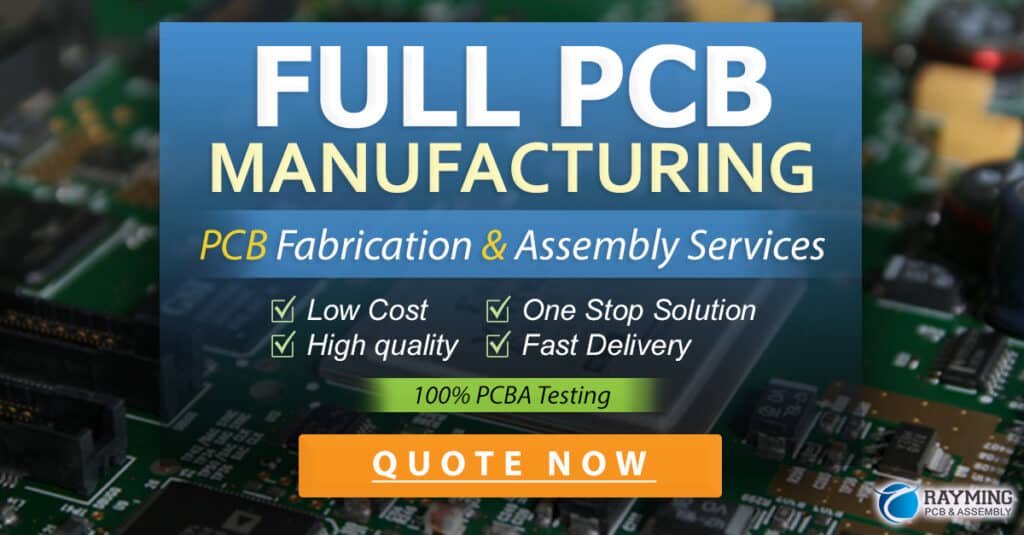
Fixing Warped PCBs
While preventing PCB warping through proper design and manufacturing practices is ideal, there are some methods to fix warped PCBs:
1. Heat Treatment
One common approach to fixing warped PCBs is through heat treatment. This involves carefully heating the PCB to a temperature that allows the board material to become pliable, and then applying pressure to flatten the board. This process should be done gradually and with caution, as excessive heat can damage the PCB and its components.
Here’s a general procedure for heat treatment:
- Preheat the PCB to around 60-70°C (140-158°F) to remove any moisture.
- Gradually increase the temperature to 120-150°C (248-302°F), depending on the PCB material.
- Apply even pressure to the PCB using a flat surface or specialized jig.
- Allow the PCB to cool down slowly while maintaining pressure.
- Inspect the PCB for any remaining warpage and repeat the process if necessary.
2. Mechanical Flattening
For minor warping, mechanical flattening may be sufficient. This involves applying gentle, even pressure to the PCB using a flat surface or specialized tool. Care must be taken not to apply excessive force, as this can damage the PCB or its components.
3. Specialized Repair Services
In some cases, particularly for severe warping or high-value PCBs, it may be necessary to seek the services of a specialized PCB repair company. These companies have the expertise and equipment to safely flatten warped PCBs while minimizing the risk of damage.
Preventing PCB Warping
While it’s possible to fix warped PCBs, it’s always better to prevent warping from occurring in the first place. Here are some strategies for preventing PCB warping:
1. Proper Design
During the PCB design phase, consider factors that can contribute to warping, such as copper distribution, layer stackup, and component placement. Aim for a balanced copper distribution and symmetrical layer stackup to minimize the risk of warping.
2. Material Selection
Choose PCB materials with low moisture absorption and good dimensional stability. High-quality, moisture-resistant laminates can help reduce the likelihood of warping due to humidity.
3. Controlled Manufacturing Environment
Ensure that the PCB manufacturing process takes place in a controlled environment with proper temperature and humidity regulation. This helps minimize the exposure of the PCB to conditions that can cause warping.
4. Proper Handling and Storage
Handle PCBs with care during the manufacturing, assembly, and transportation processes to avoid mechanical stress. Store PCBs in a moisture-controlled environment, preferably in sealed packages with desiccants to prevent moisture absorption.
5. Gradual Temperature Changes
When subjecting PCBs to temperature changes, such as during soldering or thermal cycling, ensure that the temperature changes occur gradually. Rapid temperature fluctuations can lead to uneven expansion and contraction, increasing the risk of warping.
Frequently Asked Questions (FAQ)
-
Can a warped PCB be fixed?
Yes, in many cases, a warped PCB can be fixed using techniques such as heat treatment or mechanical flattening. However, the success of the repair depends on the severity of the warping and the care taken during the repair process. -
Will a slightly warped PCB still work?
A slightly warped PCB may still function, depending on the extent of the warping and the specific design of the board. However, even minor warping can lead to issues such as component misalignment, soldering difficulties, and reduced reliability over time. -
How can I tell if a PCB is warped?
Visually inspect the PCB from various angles to check for any noticeable bending or twisting. You can also place the PCB on a flat surface and check for any rocking or unevenness. In some cases, warping may only be apparent when attempting to mount the PCB in its intended enclosure or during the soldering process. -
Can I prevent PCB warping during reflow soldering?
Yes, you can minimize the risk of PCB warping during reflow soldering by following proper reflow profile guidelines, ensuring gradual temperature changes, and using appropriate support or fixturing to keep the PCB flat during the soldering process. -
Are there any risks associated with fixing a warped PCB?
Attempting to fix a warped PCB can introduce risks such as damage to the PCB substrate, copper traces, or mounted components. It’s essential to use appropriate techniques and take necessary precautions to minimize these risks. In some cases, particularly for severe warping or high-value PCBs, it may be advisable to seek the services of a professional PCB repair company.
Conclusion
PCB warping is a common issue that can affect the functionality and reliability of electronic devices. By understanding the causes, effects, and potential solutions for warped PCBs, engineers and technicians can make informed decisions on how to address this problem.
While it is possible to fix warped PCBs through techniques such as heat treatment or mechanical flattening, preventing warping from occurring in the first place is always the best approach. This can be achieved through proper PCB design, material selection, controlled manufacturing environments, careful handling, and storage, and gradual temperature changes during processing.
By taking steps to minimize the risk of PCB warping and addressing any warping issues promptly, manufacturers can ensure the quality and longevity of their electronic products.
Cause of Warping | Prevention Strategy |
---|---|
Thermal Stress | Gradual temperature changes, proper reflow profile |
Moisture Absorption | Moisture-resistant materials, controlled storage environment |
Mechanical Stress | Careful handling, proper mounting and assembly |
Unbalanced Copper Distribution | Balanced copper distribution in PCB design |
Manufacturing Defects | Strict quality control, proper handling during fabrication |
In summary, while PCB warping can be a challenging issue, it is not an insurmountable one. With the right knowledge, techniques, and preventive measures, engineers and technicians can effectively address warped PCBs and ensure the reliable performance of electronic devices.
Leave a Reply