Introduction to Rotation-Proof Connectors
Rotation-proof connectors are essential components in various industries, including automotive, aerospace, and consumer electronics. These connectors are designed to maintain a stable and reliable connection even when subjected to rotational forces or vibrations. A well-designed rotation-proof connector pinout ensures that the electrical connection remains intact and prevents any potential damage to the connected devices.
What is a Connector Pinout?
A connector pinout refers to the arrangement and configuration of the pins within a connector. It defines the function and purpose of each pin, such as power supply, ground, data transmission, and control signals. The pinout design is crucial for ensuring proper connectivity and compatibility between different components and devices.
The Importance of Rotation-Proof Connector Pinouts
Rotation-proof connector pinouts are particularly important in applications where the connector is likely to experience rotational forces or vibrations. Some examples include:
-
Automotive industry: Connectors used in vehicles are subjected to constant vibrations and rotational forces due to the movement of the vehicle and the operation of various mechanical components.
-
Aerospace industry: Connectors used in aircraft and spacecraft must withstand extreme conditions, including vibrations, shocks, and rotational forces during takeoff, landing, and in-flight maneuvers.
-
Industrial machinery: Connectors used in industrial equipment, such as robots and CNC machines, are exposed to rotational forces and vibrations during operation.
A rotation-proof connector pinout ensures that the electrical connection remains stable and reliable, preventing any interruptions in power supply, data transmission, or control signals. This is essential for maintaining the proper functioning of the connected devices and avoiding any potential safety hazards.
Designing a Rotation-Proof Connector Pinout
Designing a rotation-proof connector pinout involves several key considerations and best practices. In this section, we will discuss the various factors that need to be taken into account when creating a robust and reliable connector pinout.
Understanding the Application Requirements
The first step in designing a rotation-proof connector pinout is to understand the specific requirements of the application. This includes:
- The number of pins required for power supply, ground, data transmission, and control signals.
- The voltage and current ratings of the connected devices.
- The expected level of vibration and rotational forces that the connector will be subjected to.
- The environmental conditions, such as temperature, humidity, and chemical exposure.
By understanding these requirements, you can select the appropriate connector type, material, and pinout configuration that will meet the demands of the application.
Selecting the Appropriate Connector Type
There are various types of connectors available, each with its own advantages and limitations. Some common connector types used in rotation-proof applications include:
- Circular connectors: These connectors have a circular shape and are well-suited for applications that require high-density pin counts and resistance to rotational forces.
- Bayonet connectors: These connectors feature a twist-lock mechanism that provides a secure and rotation-proof connection.
- Threaded connectors: These connectors use a threaded coupling mechanism to establish a robust and rotation-resistant connection.
- Keyed connectors: These connectors have a unique keying feature that ensures proper orientation and prevents accidental disconnection or rotation.
The choice of connector type will depend on the specific requirements of the application, such as the required pin count, the level of environmental protection, and the ease of installation and maintenance.
Pin Arrangement and Configuration
Once the connector type has been selected, the next step is to determine the pin arrangement and configuration. This involves:
- Assigning specific functions to each pin, such as power supply, ground, data transmission, and control signals.
- Ensuring that the pin arrangement is symmetrical and balanced to minimize the effects of rotational forces.
- Providing sufficient spacing between pins to prevent any potential short circuits or crosstalk.
- Incorporating keying features or polarization to prevent incorrect mating or rotation.
The pin arrangement and configuration should be carefully designed to optimize the electrical performance, mechanical stability, and ease of use of the connector.
Pin Number | Function | Description |
---|---|---|
1 | Power | +5V DC power supply |
2 | Ground | Common ground reference |
3 | Data TX+ | Positive data transmission signal |
4 | Data TX- | Negative data transmission signal |
5 | Data RX+ | Positive data reception signal |
6 | Data RX- | Negative data reception signal |
7 | Control 1 | Control signal 1 for device configuration |
8 | Control 2 | Control signal 2 for device configuration |
Table 1: Example pinout configuration for an 8-pin rotation-proof connector
Material Selection and Plating
The choice of materials and plating for the connector pins and housing is critical for ensuring the durability, reliability, and performance of the rotation-proof connector. Some key considerations include:
- Selecting materials with high strength, corrosion resistance, and thermal stability, such as copper alloys, stainless steel, or high-performance plastics.
- Choosing appropriate plating options, such as gold, silver, or nickel, to enhance the electrical conductivity, wear resistance, and corrosion protection of the pins.
- Ensuring that the materials and plating are compatible with the expected environmental conditions and the mating connector materials.
Proper material selection and plating will help to extend the service life of the connector and maintain its performance under demanding conditions.
Shielding and Grounding
Shielding and grounding are essential for minimizing electromagnetic interference (EMI) and ensuring the integrity of the electrical signals in rotation-proof connectors. Some best practices include:
- Incorporating a conductive shell or housing to provide electromagnetic shielding and prevent interference from external sources.
- Using shielded cables or twisted pair wires to minimize crosstalk and interference between adjacent pins.
- Providing a dedicated ground pin or multiple ground pins to establish a low-impedance path for any induced currents or noise.
- Ensuring that the shielding and grounding are properly connected to the system-level shielding and grounding scheme.
Effective shielding and grounding techniques will help to maintain signal integrity and prevent any potential issues related to EMI or signal degradation.
Testing and Validation
Once the rotation-proof connector pinout has been designed, it is essential to perform thorough testing and validation to ensure that it meets the required performance and reliability standards. This involves:
- Conducting mechanical tests to verify the connector’s ability to withstand the expected level of vibration and rotational forces.
- Performing electrical tests to validate the signal integrity, insulation resistance, and contact resistance of the connector.
- Subjecting the connector to environmental tests, such as temperature cycling, humidity exposure, and salt spray, to assess its durability and corrosion resistance.
- Conducting mating and unmating tests to ensure that the connector can be easily and reliably connected and disconnected.
Test | Standard | Requirement |
---|---|---|
Vibration | MIL-STD-810 | Withstand 10 g vibration, 10-2000 Hz, 3 axes |
Rotational Force | Custom | Maintain connection under 50 N-cm of rotational torque |
Temperature Cycling | MIL-STD-810 | -55°C to +125°C, 500 cycles |
Humidity | MIL-STD-810 | 95% RH, 60°C, 1000 hours |
Salt Spray | ASTM B117 | 5% salt solution, 35°C, 1000 hours |
Mating/Unmating | IEC 61076 | 500 mating cycles without degradation |
Table 2: Example test requirements for a rotation-proof connector
By conducting comprehensive testing and validation, you can ensure that the rotation-proof connector pinout meets the required performance and reliability standards and is suitable for use in the intended application.
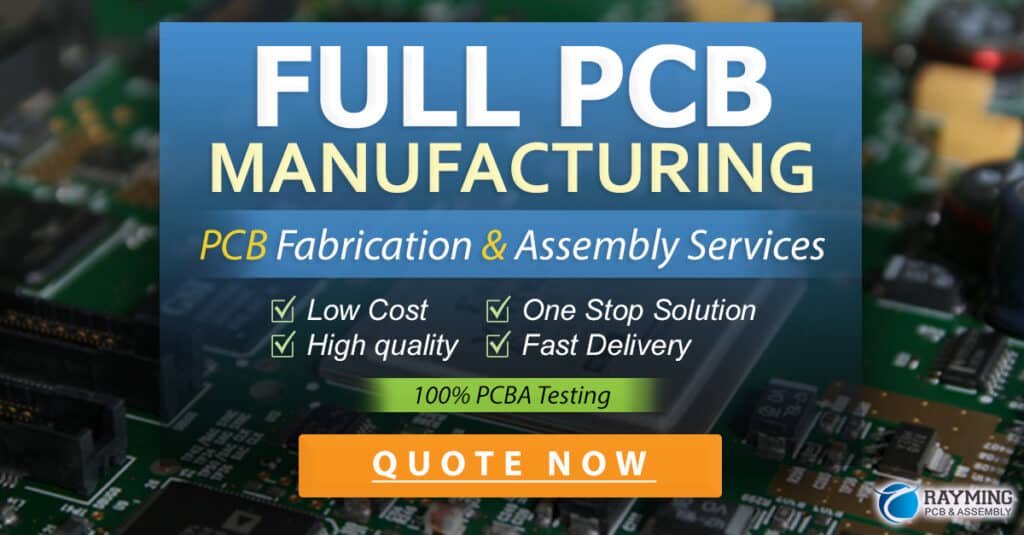
Implementation and Integration
After the rotation-proof connector pinout has been designed, tested, and validated, the next step is to implement it in the actual application and integrate it with the connected devices. This involves:
- Developing detailed assembly and installation instructions to ensure that the connector is properly installed and mated.
- Providing clear and concise labeling and marking of the connector pins and housing to facilitate correct installation and troubleshooting.
- Collaborating with the device manufacturers to ensure that the connector pinout is compatible with their devices and meets their performance and reliability requirements.
- Conducting system-level testing and validation to verify that the connector performs as expected when integrated with the connected devices.
Proper implementation and integration of the rotation-proof connector pinout will help to ensure a smooth and reliable operation of the connected devices and minimize any potential issues related to connectivity or signal integrity.
Maintenance and Troubleshooting
To ensure the long-term reliability and performance of the rotation-proof connector, it is essential to establish proper maintenance and troubleshooting procedures. This includes:
- Developing a regular inspection and cleaning schedule to prevent any buildup of contaminants or corrosion on the connector pins and housing.
- Providing training and guidance to the end-users on the proper handling, mating, and unmating of the connector to prevent any damage or wear.
- Establishing a troubleshooting guide and diagnostic procedures to help identify and resolve any connectivity or signal issues related to the connector.
- Maintaining a spare parts inventory and a repair and replacement policy to minimize downtime and ensure the continuous operation of the connected devices.
Effective maintenance and troubleshooting procedures will help to extend the service life of the rotation-proof connector and minimize any potential disruptions or failures in the connected devices.
Future Trends and Innovations
As technology continues to advance and new applications emerge, there will be a growing demand for more advanced and innovative rotation-proof connector pinouts. Some future trends and innovations to watch out for include:
- Miniaturization: The development of smaller and more compact connectors that can accommodate higher pin counts and signal densities while maintaining rotation-proof performance.
- Wireless connectivity: The integration of wireless technologies, such as Bluetooth or Wi-Fi, into rotation-proof connectors to enable wireless data transmission and eliminate the need for physical connections.
- Smart connectors: The incorporation of sensors, microcontrollers, and other intelligent features into rotation-proof connectors to enable real-time monitoring, diagnostics, and adaptive control of the connected devices.
- High-speed data transmission: The development of rotation-proof connectors that can support higher data rates and bandwidth to accommodate the growing demand for high-speed data transmission in applications such as video streaming, machine vision, and industrial automation.
- Sustainable materials: The use of eco-friendly and sustainable materials, such as biodegradable plastics or recycled metals, in the manufacturing of rotation-proof connectors to reduce environmental impact and promote sustainability.
By staying up-to-date with the latest trends and innovations in rotation-proof connector pinouts, you can ensure that your designs remain competitive and meet the evolving needs of the market.
FAQ
-
What is a rotation-proof connector?
A rotation-proof connector is a type of electrical connector that is designed to maintain a stable and reliable connection even when subjected to rotational forces or vibrations. It prevents the accidental disconnection or rotation of the connector, ensuring the integrity of the electrical connection. -
Why are rotation-proof connectors important?
Rotation-proof connectors are important in applications where the connector is likely to experience rotational forces or vibrations, such as in the automotive, aerospace, and industrial machinery industries. They ensure that the electrical connection remains stable and reliable, preventing any interruptions in power supply, data transmission, or control signals, which is essential for maintaining the proper functioning of the connected devices and avoiding any potential safety hazards. -
What are the key considerations when designing a rotation-proof connector pinout?
The key considerations when designing a rotation-proof connector pinout include understanding the application requirements, selecting the appropriate connector type, determining the pin arrangement and configuration, choosing the right materials and plating, and implementing effective shielding and grounding techniques. It is also essential to conduct thorough testing and validation to ensure that the connector meets the required performance and reliability standards. -
How can I ensure the long-term reliability and performance of a rotation-proof connector?
To ensure the long-term reliability and performance of a rotation-proof connector, it is essential to establish proper maintenance and troubleshooting procedures. This includes developing a regular inspection and cleaning schedule, providing training and guidance to the end-users on the proper handling and mating of the connector, establishing a troubleshooting guide and diagnostic procedures, and maintaining a spare parts inventory and a repair and replacement policy. -
What are some future trends and innovations in rotation-proof connector pinouts?
Some future trends and innovations in rotation-proof connector pinouts include miniaturization, wireless connectivity, smart connectors, high-speed data transmission, and the use of sustainable materials. By staying up-to-date with these trends and innovations, designers can ensure that their rotation-proof connector pinouts remain competitive and meet the evolving needs of the market.
Conclusion
Designing a rotation-proof connector pinout requires careful consideration of various factors, including the application requirements, connector type, pin arrangement, materials, shielding, and grounding. By following the best practices and guidelines discussed in this article, you can create a robust and reliable rotation-proof connector pinout that meets the performance and reliability standards of your application.
Testing and validation are critical steps in ensuring that the connector can withstand the expected level of vibration and rotational forces, maintain signal integrity, and operate reliably under the specified environmental conditions. Proper implementation and integration of the connector into the connected devices are also essential for a smooth and trouble-free operation.
Regular maintenance, troubleshooting, and staying informed about the latest trends and innovations in rotation-proof connector pinouts will help you to keep your designs competitive and adapt to the evolving needs of the market. By investing in the development of advanced and innovative rotation-proof connector pinouts, you can contribute to the advancement of technology and the growth of various industries that rely on these critical components.
Leave a Reply