What are PCBs?
Before diving into the world of 3D printed pcbs, let’s first understand what PCBs are and their importance in electronic devices. PCBs are the backbone of modern electronics, providing a platform for connecting electronic components and enabling the flow of electrical signals. They are found in almost every electronic device, from smartphones and computers to home appliances and medical equipment.
PCBs are typically made of a non-conductive substrate, such as fiberglass or plastic, with conductive traces etched onto the surface. These traces, usually made of copper, form the pathways for electrical signals to travel between components. The components, such as resistors, capacitors, and integrated circuits, are soldered onto the PCB to create a functional electronic circuit.
Traditional PCB Manufacturing Methods
Traditionally, PCBs are manufactured using a subtractive process. This involves starting with a substrate material that is fully coated with a layer of copper. The desired circuit pattern is then etched away using a chemical process, leaving behind the conductive traces. This process is repeated for each layer of the PCB, and the layers are then laminated together to form the final board.
While this method has been the standard for PCB manufacturing for decades, it has some limitations. It requires specialized equipment and chemicals, which can be expensive and environmentally hazardous. Additionally, the process is limited in terms of the complexity and precision of the circuits that can be created.
The Emergence of 3D Printed PCBs
In recent years, researchers and engineers have been exploring the potential of 3D printing technology for creating PCBs. 3D printing, also known as additive manufacturing, involves building up an object layer by layer using a digital model as a guide. This technology has already been used to create a wide range of objects, from plastic toys to metal parts for aerospace applications.
The idea of using 3D printing for PCBs is attractive for several reasons. First, it has the potential to simplify the manufacturing process and reduce costs. Instead of requiring specialized equipment and chemicals, a 3D printer can create a PCB using a single machine and a conductive material. Second, 3D printing allows for greater design flexibility and customization. Complex shapes and structures that are difficult or impossible to create using traditional methods can be easily produced with a 3D printer.
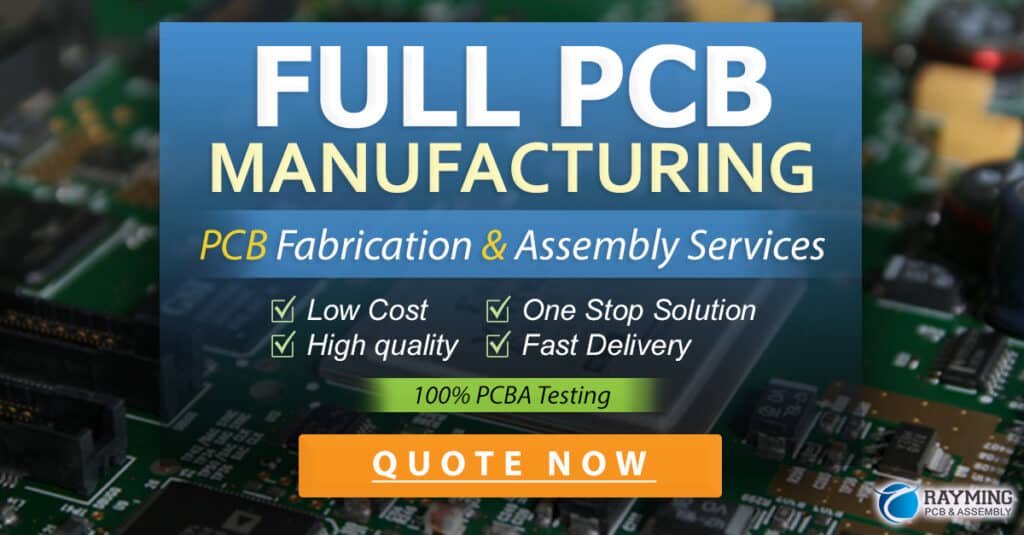
Current State of 3D Printed PCB Technology
While the concept of 3D printed PCBs is promising, the technology is still in its early stages. Researchers and companies are exploring various approaches to creating conductive traces and integrating components into 3D printed structures.
One approach is to use conductive filaments, such as those made from a mixture of plastic and metal particles. These filaments can be used in a standard 3D printer to create conductive traces within a printed object. However, the conductivity of these materials is often lower than that of traditional copper traces, which can limit their applications.
Another approach is to use a multi-material 3D printer that can deposit both conductive and non-conductive materials. This allows for the creation of more complex structures with embedded electronic components. Some researchers have even developed methods for 3D printing entire functional electronic devices, such as sensors and actuators, in a single print.
Despite these advancements, there are still challenges to overcome before 3D printed PCBs can become a viable alternative to traditional manufacturing methods. One challenge is the resolution and precision of the printed traces. While 3D printers can create fine details, they may not be able to match the precision of traditional etching methods, which can limit the density and complexity of the circuits that can be created.
Another challenge is the integration of components onto the 3D printed PCB. While it is possible to embed components within the printed structure, ensuring proper alignment and connectivity can be difficult. Additionally, the thermal and mechanical properties of the printed materials may not be suitable for certain components or applications.
Advantages of 3D Printed PCBs
Despite the challenges, 3D printed PCBs offer several potential advantages over traditional manufacturing methods:
-
Rapid Prototyping: 3D printing allows for quick and easy creation of prototype PCBs, enabling faster iteration and testing of designs.
-
Customization: 3D printing enables the creation of custom PCB designs with unique shapes and features that may not be possible with traditional methods.
-
Cost Reduction: For small-scale production or prototyping, 3D printing can be more cost-effective than traditional methods, as it does not require expensive tooling or setup costs.
-
Environmental Benefits: 3D printing can potentially reduce waste and environmental impact compared to traditional methods, as it uses only the necessary amount of material and does not require harmful chemicals for etching.
Applications of 3D Printed PCBs
While 3D printed PCBs may not replace traditional manufacturing methods for large-scale production, they have several potential applications:
-
Prototyping and Testing: 3D printed PCBs can be used for rapid prototyping and testing of new designs, allowing for faster iteration and validation.
-
Custom and Limited-Run Products: For products that require unique or customized PCB designs, or for limited-run productions, 3D printing can be a cost-effective solution.
-
Wearable Electronics: 3D printing can enable the creation of flexible and conformable PCBs that can be integrated into wearable devices and smart textiles.
-
Aerospace and Defense: In applications where weight and space are critical, 3D printed PCBs can offer advantages in terms of customization and integration with other components.
Future Outlook
As 3D printing technology continues to advance, the possibilities for 3D printed PCBs will likely expand. Researchers are exploring new materials and techniques for improving the conductivity and resolution of printed traces, as well as methods for integrating active and passive components into printed structures.
One area of research is the development of multi-functional 3D printed electronics, where the printed structure serves not only as a PCB but also provides mechanical support, thermal management, and other functions. This could lead to the creation of more compact and efficient electronic devices.
Another potential direction is the integration of 3D printed PCBs with other advanced manufacturing technologies, such as printed electronics and flexible hybrid electronics. This could enable the creation of complex, multi-functional electronic systems that are customized for specific applications.
FAQ
-
Can any 3D printer be used to create PCBs?
Not all 3D printers are suitable for creating PCBs. The printer must be capable of using conductive materials and have sufficient resolution to create fine traces. Some specialized 3D printers are designed specifically for printing electronics. -
Are 3D printed PCBs as reliable as traditionally manufactured PCBs?
Currently, 3D printed PCBs may not match the reliability and performance of traditionally manufactured PCBs, particularly for high-density or high-frequency applications. However, as the technology improves, the reliability of 3D printed PCBs is expected to increase. -
What materials are used for 3D printing PCBs?
Various materials can be used, including conductive filaments that contain metal particles, conductive inks or pastes, and even metal powders that can be sintered after printing. The choice of material depends on the specific application and the capabilities of the 3D printer. -
Can components be integrated into 3D printed PCBs?
Yes, it is possible to integrate electronic components into 3D printed PCBs, either by embedding them within the printed structure or by adding them after printing using traditional assembly methods. However, ensuring proper alignment and connectivity can be challenging. -
Are 3D printed PCBs suitable for mass production?
Currently, 3D printed PCBs are more suitable for prototyping, custom designs, and low-volume production. For mass production, traditional manufacturing methods are still more cost-effective and reliable. However, as the technology advances, 3D printing may become a viable option for larger-scale production in the future.
Conclusion
3D printed PCBs represent an exciting development in the field of electronics manufacturing. While the technology is still in its early stages, it offers the potential for faster prototyping, greater customization, and cost reduction for certain applications. As researchers continue to develop new materials and techniques, the capabilities of 3D printed PCBs will likely expand, enabling the creation of more complex and multi-functional electronic devices.
However, it is important to recognize the current limitations and challenges of 3D printed PCBs, particularly in terms of conductivity, resolution, and reliability compared to traditional manufacturing methods. For now, 3D printed PCBs are most suitable for prototyping, custom designs, and low-volume production, while traditional methods remain the standard for large-scale manufacturing.
As the technology continues to evolve, it will be interesting to see how 3D printed PCBs are integrated with other advanced manufacturing technologies and applied to various industries, from consumer electronics to aerospace and beyond. While there is still much work to be done, the potential for 3D printed PCBs to revolutionize electronics manufacturing is undeniable, and it will be exciting to see how this technology develops in the coming years.
Leave a Reply