Understanding the Limitations of Moving Parts
When designing and manufacturing various mechanical systems, engineers and designers often face the challenge of moving parts and their limitations. One of the most significant constraints is the inability to move parts too close to each other due to various factors such as physical size, material properties, and operational requirements. This article will explore the reasons behind this limitation and discuss strategies to optimize the design and functionality of moving parts while respecting the necessary clearances.
Factors Affecting the Proximity of Moving Parts
Several factors contribute to the limitations in moving parts close to each other:
-
Physical Size: The dimensions of the components themselves restrict how close they can be placed. Each part requires a certain amount of space to function correctly and avoid interference with adjacent components.
-
Material Properties: The materials used in the construction of the parts play a crucial role in determining the minimum clearance required. Factors such as thermal expansion, wear resistance, and surface finish can impact the necessary spacing between parts.
-
Operational Requirements: The intended function and operating conditions of the system also influence the proximity of moving parts. Considerations such as speed, load, and lubrication requirements may necessitate larger clearances to ensure reliable performance and longevity.
Strategies for Optimizing Moving Part Design
Despite the limitations in moving parts close to each other, engineers and designers can employ various strategies to optimize the design and functionality of the system:
1. Miniaturization
One approach to minimize the spacing between moving parts is through miniaturization. By reducing the overall size of the components, designers can achieve tighter clearances while still maintaining the necessary functionality. Advances in manufacturing technologies, such as 3D printing and micro-machining, have enabled the production of smaller, more precise parts.
However, miniaturization comes with its own set of challenges. As parts become smaller, they become more susceptible to wear, deformation, and manufacturing imperfections. Designers must carefully consider the trade-offs between size reduction and the maintainability and durability of the system.
2. Material Selection
Choosing the right materials for moving parts can significantly impact their ability to operate in close proximity. Materials with low coefficients of thermal expansion, such as Invar or ceramic composites, can minimize the dimensional changes caused by temperature fluctuations. This stability allows for tighter clearances between parts, as the risk of interference due to thermal expansion is reduced.
Additionally, materials with excellent wear resistance and low friction coefficients can help minimize the need for large clearances. By reducing wear and friction, parts can operate more efficiently and with less risk of damage, even when positioned close to each other.
3. Lubrication and Sealing
Proper lubrication and sealing play a vital role in enabling moving parts to function effectively in close proximity. Lubricants help reduce friction and wear between surfaces, allowing for smoother operation and longer component life. By selecting appropriate lubricants and designing efficient lubrication systems, engineers can minimize the required clearances between parts.
Sealing is another critical aspect of moving part design. Effective sealing prevents contaminants from entering the system and causing damage or impeding performance. By implementing robust sealing solutions, such as labyrinth seals or elastomeric seals, designers can maintain the integrity of the system while allowing for closer positioning of moving parts.
4. Precision Manufacturing
Achieving tight tolerances and high precision during the manufacturing process is essential for moving parts that operate in close proximity. Advanced manufacturing techniques, such as computer numerical control (CNC) machining and precision grinding, enable the production of parts with extremely accurate dimensions and surface finishes.
By investing in precision manufacturing capabilities, companies can produce components that fit together seamlessly, reducing the need for excessive clearances. This precision also contributes to improved system performance, as the parts can operate with minimal friction and wear.
5. Simulation and Analysis
Before finalizing the design of a system with moving parts, engineers rely on simulation and analysis tools to predict the behavior and performance of the components. Finite element analysis (FEA) software allows designers to model the stresses, deformations, and thermal effects on the parts under various operating conditions.
Through simulation, engineers can identify potential interference issues and optimize the design to ensure adequate clearances between moving parts. This virtual testing helps minimize the need for physical prototypes and reduces the risk of costly redesigns later in the development process.
FAQs
-
Q: Why can’t moving parts be placed too close to each other?
A: Moving parts cannot be placed too close to each other due to several factors, including physical size limitations, material properties, and operational requirements. Each part needs a certain amount of space to function correctly and avoid interference with adjacent components. -
Q: How does miniaturization help in reducing the spacing between moving parts?
A: Miniaturization involves reducing the overall size of the components, allowing for tighter clearances while maintaining functionality. Advances in manufacturing technologies, such as 3D printing and micro-machining, have enabled the production of smaller, more precise parts. -
Q: What role does material selection play in enabling moving parts to operate in close proximity?
A: Choosing materials with low coefficients of thermal expansion, excellent wear resistance, and low friction coefficients can help minimize the need for large clearances between moving parts. These properties allow for tighter clearances while reducing the risk of interference and wear. -
Q: How do lubrication and sealing contribute to the performance of moving parts in close proximity?
A: Proper lubrication helps reduce friction and wear between surfaces, allowing for smoother operation and longer component life. Effective sealing prevents contaminants from entering the system and causing damage or impeding performance. Both lubrication and sealing enable closer positioning of moving parts. -
Q: What role does simulation and analysis play in optimizing the design of moving parts?
A: Simulation and analysis tools, such as finite element analysis (FEA) software, allow engineers to model the stresses, deformations, and thermal effects on the parts under various operating conditions. This virtual testing helps identify potential interference issues and optimize the design to ensure adequate clearances between moving parts.
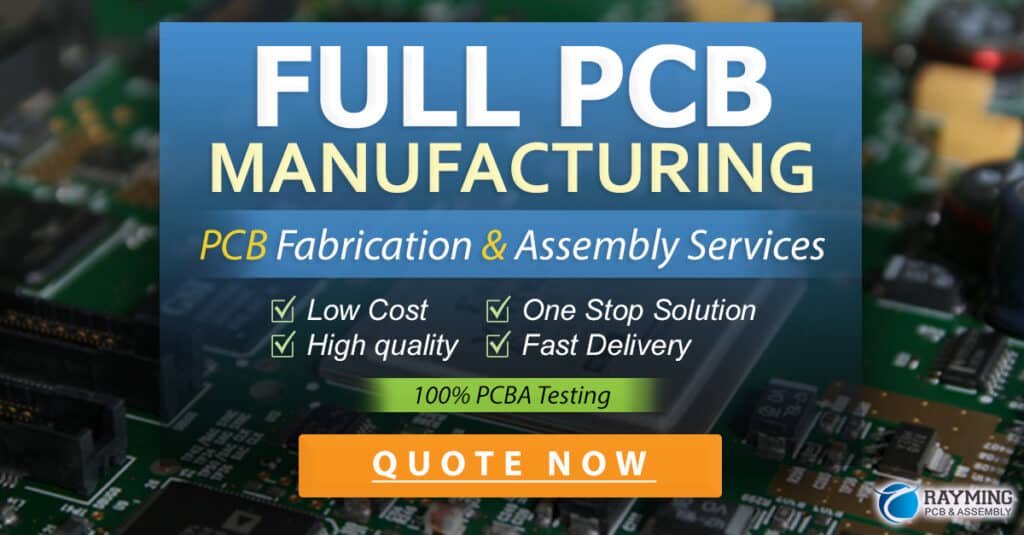
Conclusion
The limitation of moving parts being unable to be placed too close to each other presents a significant challenge in the design and manufacturing of mechanical systems. Factors such as physical size, material properties, and operational requirements contribute to the necessary clearances between components.
However, engineers and designers can employ various strategies to optimize the design and functionality of moving parts while respecting the proximity constraints. Miniaturization, material selection, lubrication and sealing, precision manufacturing, and simulation and analysis all play crucial roles in achieving tighter clearances and improved system performance.
By understanding the limitations and implementing these strategies, engineers can create mechanical systems that operate efficiently, reliably, and with minimal interference between moving parts. As technology advances, new materials and manufacturing techniques will continue to push the boundaries of what is possible in the design and optimization of moving part systems.
Strategy | Description | Benefits |
---|---|---|
Miniaturization | Reducing the overall size of components | Allows for tighter clearances while maintaining functionality |
Material Selection | Choosing materials with low thermal expansion, high wear resistance, and low friction | Minimizes the need for large clearances and reduces the risk of interference and wear |
Lubrication and Sealing | Implementing proper lubrication and sealing solutions | Reduces friction, prevents contaminants, and enables closer positioning of moving parts |
Precision Manufacturing | Achieving tight tolerances and high precision during manufacturing | Produces components that fit together seamlessly, reducing the need for excessive clearances |
Simulation and Analysis | Using tools like FEA to model stresses, deformations, and thermal effects | Identifies potential interference issues and optimizes the design to ensure adequate clearances |
By employing these strategies and continually innovating in the field of moving part design, engineers can overcome the limitations of proximity and create systems that push the boundaries of performance and efficiency.
Leave a Reply