What is Laser Cutting?
Laser cutting is a precise and versatile manufacturing process that uses a high-powered laser beam to cut, engrave, or mark various materials. The laser beam is focused onto the material surface, and the intense heat generated by the laser vaporizes or melts the material along the cut path. Laser cutting offers several advantages over traditional cutting methods, including:
- High precision and accuracy
- Minimal material waste
- Reduced processing time
- Flexibility in design and customization
- Non-contact process, minimizing contamination
Laser cutting has found applications in a wide range of industries, including automotive, aerospace, medical, and electronics.
Laser Cutting PCBs: Possibilities and Challenges
Possibilities
Laser cutting technology has the potential to revolutionize PCB manufacturing by offering several advantages over traditional chemical etching processes:
-
Rapid Prototyping: Laser cutting enables quick and efficient prototyping of PCBs. Designers can iterate and test their designs faster, reducing the overall development time.
-
Customization: Laser cutting allows for high flexibility in PCB design. Complex shapes, intricate patterns, and fine features can be easily achieved using laser cutting technology.
-
Environmentally Friendly: Unlike chemical etching, laser cutting does not involve the use of harmful chemicals, making it a more environmentally friendly option for PCB manufacturing.
-
Cost-Effective: For small-scale production or prototyping, laser cutting can be a cost-effective alternative to traditional PCB manufacturing methods, as it eliminates the need for expensive tooling and setup costs.
Challenges
While laser cutting PCBs offers several advantages, there are also some challenges and limitations to consider:
-
Material Compatibility: Not all PCB materials are suitable for laser cutting. Some materials, such as FR4 (a common PCB substrate), may release harmful fumes or produce inconsistent results when subjected to laser cutting.
-
Conductor Integrity: Laser cutting can potentially damage or remove the conductive traces on the PCB, especially if the laser power and settings are not optimized. Ensuring the integrity of the conductive paths is crucial for the proper functioning of the PCB.
-
Heat Affected Zone: The high-intensity laser beam generates heat during the cutting process, which can lead to a heat-affected zone (HAZ) around the cut edges. The HAZ may cause localized changes in the material properties, potentially affecting the performance of the PCB.
-
Dimensional Accuracy: While laser cutting offers high precision, achieving tight tolerances and maintaining consistent dimensions across the entire PCB can be challenging. Factors such as material thickness, laser power, and cutting speed need to be carefully controlled to ensure accurate results.
Laser Cutting PCB Materials
When considering laser cutting PCBs, it is essential to choose the appropriate material that is compatible with the laser cutting process. Some commonly used PCB materials for laser cutting include:
-
Polyimide: Polyimide is a high-performance polymer that offers excellent thermal stability, mechanical strength, and electrical insulation properties. It is well-suited for laser cutting and is often used in flexible PCBs.
-
Teflon: Teflon, or Polytetrafluoroethylene (PTFE), is a fluoropolymer known for its low dielectric constant, low loss tangent, and high-temperature resistance. Teflon PCBs can be effectively laser cut, making them suitable for high-frequency applications.
-
Ceramics: Ceramic PCBs, such as Alumina (Al2O3) and Aluminum Nitride (AlN), offer excellent thermal conductivity, high dielectric strength, and low dielectric loss. Laser cutting is a viable option for machining ceramic PCBs, although specialized laser systems may be required.
It is important to note that the choice of PCB material depends on the specific application requirements, such as operating temperature, frequency, and mechanical stresses. Consulting with PCB manufacturers or laser cutting service providers can help in selecting the most suitable material for laser cutting PCBs.
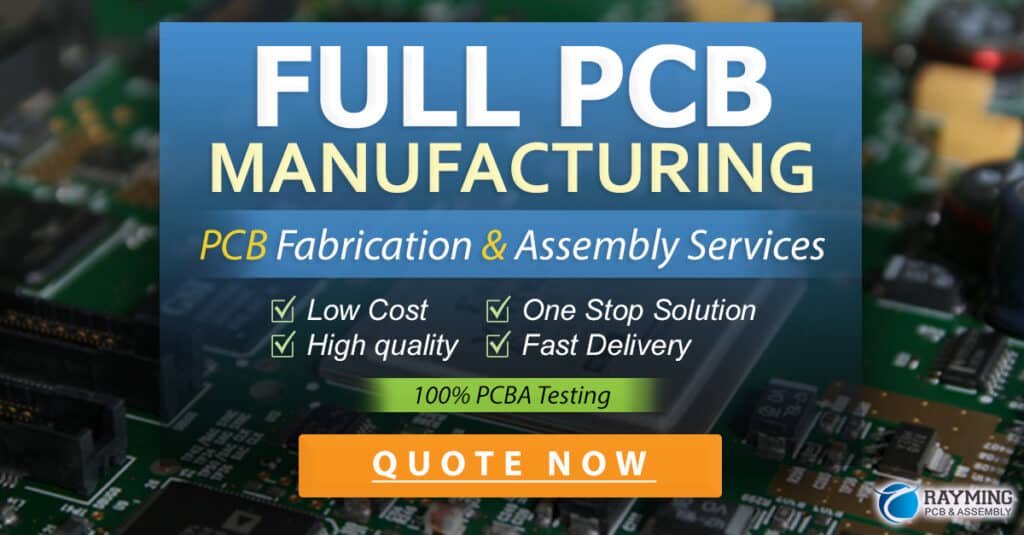
Optimizing Laser Cutting Parameters for PCBs
To achieve the best results when laser cutting PCBs, it is crucial to optimize the laser cutting parameters. The key parameters to consider include:
-
Laser Power: The laser power determines the amount of energy delivered to the material during the cutting process. Too low power may result in incomplete cutting, while excessive power can cause damage to the PCB or surrounding components.
-
Cutting Speed: The cutting speed refers to the rate at which the laser beam moves along the cut path. Slower cutting speeds allow for more precise and controlled cutting but may increase the processing time. Faster speeds can improve productivity but may compromise the cut quality.
-
Focal Point: The focal point is the point where the laser beam is focused on the material surface. Proper focusing ensures that the laser energy is concentrated at the desired location, resulting in clean and precise cuts.
-
Assist Gas: Assist gas, such as nitrogen or compressed air, is often used during laser cutting to protect the cut edges from oxidation and to remove debris from the cutting area. The type and pressure of the assist gas can influence the cut quality and surface finish.
Optimizing these parameters requires experimentation and fine-tuning based on the specific PCB material, thickness, and desired cut quality. Conducting test cuts on sample materials and analyzing the results can help in determining the optimal settings for laser cutting PCBs.
Designing PCBs for Laser Cutting
When designing PCBs for laser cutting, there are several considerations to keep in mind:
-
Clearance and Spacing: Ensure sufficient clearance and spacing between components, traces, and cut edges to accommodate the laser beam diameter and to avoid unintentional damage during the cutting process.
-
Fiducial Marks: Include fiducial marks or registration holes on the PCB design to facilitate accurate alignment and positioning during the laser cutting process. These marks serve as reference points for the laser system to ensure precise cutting.
-
Minimize Thermal Stress: Design the PCB layout in a way that minimizes thermal stress during laser cutting. Avoid placing sensitive components or traces near the cut edges to reduce the risk of damage due to heat exposure.
-
Consider Material Thickness: The thickness of the PCB material influences the laser cutting parameters and the achievable feature sizes. Thicker materials may require higher laser power and slower cutting speeds to achieve clean and accurate cuts.
-
Optimize Trace Width: When designing conductive traces for laser-cut PCBs, consider optimizing the trace width to ensure robust electrical connections. Wider traces can withstand potential damage during the cutting process better than narrow traces.
Collaborating with experienced PCB designers and laser cutting service providers can help in creating PCB designs that are optimized for laser cutting, ensuring successful fabrication and functionality.
FAQs
-
Q: Can all types of lasers be used for cutting PCBs?
A: Not all lasers are suitable for cutting PCBs. CO2 lasers and fiber lasers are commonly used for PCB cutting due to their ability to efficiently cut non-metallic materials and their high precision capabilities. -
Q: Is laser cutting PCBs a cost-effective option for mass production?
A: Laser cutting PCBs may not be the most cost-effective option for mass production. Traditional PCB manufacturing methods, such as chemical etching, are generally more economical for high-volume production. Laser cutting is more suitable for prototyping, small-scale production, or specialized applications. -
Q: Can laser cutting be used to create multi-layer PCBs?
A: Laser cutting can be used to create individual layers of a multi-layer PCB, but the assembly and lamination of the layers typically require additional processes. Laser cutting is more commonly used for single-layer or double-sided PCBs. -
Q: What is the minimum feature size achievable with laser cutting PCBs?
A: The minimum feature size achievable with laser cutting depends on various factors, including the laser system, material properties, and cutting parameters. Generally, laser cutting can achieve feature sizes down to a few hundred microns (typically around 200-300 microns), but it may vary based on the specific setup and requirements. -
Q: Are there any post-processing steps required after laser cutting PCBs?
A: After laser cutting PCBs, some post-processing steps may be necessary, such as cleaning the cut edges to remove any debris or oxidation, applying surface finishes (e.g., solder mask, silkscreen), and populating the PCB with components. The specific post-processing steps depend on the application and the desired final product.
Conclusion
Laser cutting technology offers an innovative approach to PCB manufacturing, providing advantages such as rapid prototyping, customization, and environmental friendliness. However, it is essential to consider the challenges and limitations associated with laser cutting PCBs, including material compatibility, conductor integrity, and dimensional accuracy.
By selecting the appropriate PCB materials, optimizing laser cutting parameters, and designing PCBs with laser cutting considerations in mind, it is possible to successfully laser cut PCBs for various applications. Collaborating with experienced PCB manufacturers and laser cutting service providers can help in navigating the complexities and achieving the desired results.
As laser cutting technology continues to evolve and improve, it is likely to play an increasingly important role in PCB manufacturing, particularly for prototyping, small-scale production, and specialized applications. By understanding the possibilities and challenges of laser cutting PCBs, designers and manufacturers can leverage this technology to create innovative and efficient electronic devices.
Aspect | Traditional PCB Manufacturing | Laser Cutting PCBs |
---|---|---|
Prototyping Speed | Slower | Faster |
Design Flexibility | Limited | High |
Environmental Impact | Uses harmful chemicals | Environmentally friendly |
Cost-Effectiveness | Economical for mass production | Suitable for small-scale production |
Material Compatibility | Wide range of materials | Limited materials |
Conductor Integrity | Generally maintained | Potential for damage |
Heat Affected Zone | Minimal | Can be significant |
Dimensional Accuracy | High | Requires optimization |
In conclusion, laser cutting PCBs presents both opportunities and challenges. While it offers advantages in terms of prototyping speed, design flexibility, and environmental friendliness, it also has limitations in material compatibility, conductor integrity, and dimensional accuracy. By carefully considering these factors and working with experienced professionals, it is possible to harness the potential of laser cutting technology for PCB manufacturing and create innovative electronic solutions.
Leave a Reply