Introduction to Cam Editor Panelization
Cam editor panelization is an important process in PCB manufacturing that involves arranging multiple printed circuit board designs onto a larger panel for more efficient fabrication. By panelizing PCB designs, manufacturers can produce a higher volume of boards while reducing material waste and minimizing handling.
In this comprehensive guide, we’ll dive deep into cam editor panelization, covering the basics of what it is and why it’s used, as well as more advanced topics like panelization techniques, design considerations, and troubleshooting common issues. Whether you’re a PCB designer, manufacturer, or just curious to learn more, this article will provide a thorough overview of cam editor panelization.
What is Cam Editor Panelization?
Cam editor panelization refers to the process of arranging multiple individual printed circuit board (PCB) designs onto a larger panel layout for manufacturing. A CAM (computer-aided manufacturing) editor is used to create the panelized layout by replicating the individual board designs in an array, adding tooling features, and exporting manufacturing files.
The main goal of panelization is to maximize the number of boards that can be produced on a single panel while maintaining proper spacing and meeting design requirements. This helps improve efficiency and reduce costs in the PCB fabrication process.
Benefits of Panelization
Panelizing PCB designs offers several key benefits for manufacturers:
- Increased production efficiency
- Reduced material waste
- Lower cost per board
- Easier handling and assembly
- Faster turnaround times
By fabricating multiple boards on a single panel, manufacturers can streamline the production process and minimize the time and labor required for each individual board.
Panelization Techniques
There are several techniques used in cam editor panelization to arrange and optimize PCB layouts on a panel. The choice of technique depends on factors like the board size, shape, quantity, and design requirements.
Regular Grid Panelization
The most basic panelization technique is regular grid panelization, where the individual board designs are arranged in a uniform grid pattern on the panel. This method is suitable for simple, rectangular boards of the same size.
To create a regular grid panel, the CAM editor is used to define the spacing between boards (rails) and the number of rows and columns in the grid. The individual board designs are then replicated and arranged according to the grid layout.
Irregular Panelization
For boards with irregular shapes or sizes, irregular panelization techniques can be used to optimize panel usage. These techniques involve nesting the board designs on the panel in a non-uniform pattern to minimize wasted space.
Some common irregular panelization techniques include:
- Tabbed arrays: Boards are connected by small tabs to form an array, allowing for non-rectangular layouts.
- Step and repeat: Boards are arranged in a step-like pattern, with each row offset from the previous one.
- Interlock: Boards are nested together like puzzle pieces to maximize panel utilization.
Irregular panelization requires more advanced CAM editor tools and may involve manual placement of boards on the panel.
Sub-Panelization
Sub-panelization is a technique where smaller panels (sub-panels) are created and then arranged onto a larger master panel. This is useful for manufacturing boards of different sizes or designs in the same production run.
Each sub-panel is created using regular or irregular panelization techniques, and then the sub-panels are arranged onto the master panel using a regular grid or irregular pattern.
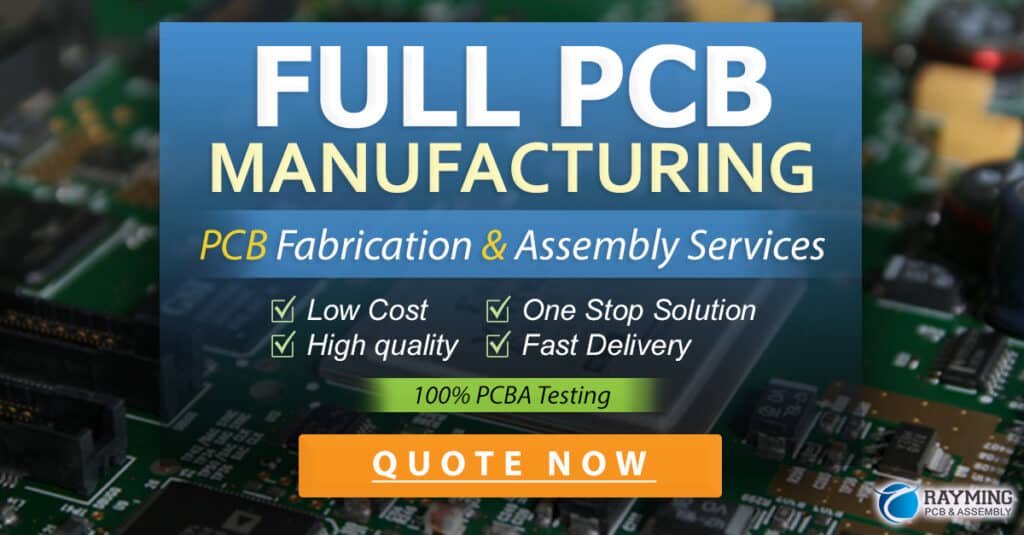
Panelization Design Considerations
When designing a panelized PCB layout, there are several important considerations to keep in mind to ensure manufacturability and quality.
Board Spacing and Rails
Proper spacing between individual boards on the panel is crucial for manufacturability. The space between boards, known as rails or gutters, allows for the boards to be separated after fabrication.
The width of the rails depends on the PCB thickness, material, and depaneling method. Thinner rails can reduce waste but may require more precise tooling for depaneling. Wider rails provide more stability during handling but increase material waste.
Typical rail widths range from 2mm to 5mm, but the exact specification should be confirmed with the manufacturer.
Fiducial Marks
Fiducial marks are reference points used for aligning the panel during fabrication and assembly. They are typically small circular pads placed in the corners or edges of the panel.
Fiducial marks should be positioned consistently on each panel and sized appropriately for the manufacturing equipment. The CAM editor is used to add fiducial marks to the panelized layout.
Tooling Holes and Slots
Tooling holes and slots are used to secure the panel during fabrication and assembly processes. They provide a way for machines to grip and align the panel accurately.
The size, shape, and location of tooling holes and slots depend on the specific manufacturing equipment and requirements. Common types include:
- Round holes: Used for pin registration and drilling.
- Obround holes: Provide some flexibility for alignment.
- Edge slots: Used for clamping the panel in place.
The CAM editor is used to add tooling holes and slots to the panel layout according to the manufacturer’s specifications.
Breakaway Tabs
Breakaway tabs, also known as mouse bites or v-grooves, are small perforations or cuts in the rails between boards that allow for easy separation (depaneling) after fabrication.
The size and spacing of breakaway tabs depend on the board thickness and depaneling method. Smaller tabs create a cleaner edge but may require more precise tooling. Larger tabs are easier to break but may leave more residual material on the board edge.
The CAM editor is used to add breakaway tabs to the panel layout, typically as a series of small drilled holes or v-shaped cuts.
Orientation and Asymmetry
When panelizing boards, it’s important to consider the orientation and asymmetry of the design. Boards should be oriented consistently on the panel to ensure proper assembly and minimize confusion.
If the board design is asymmetrical, it may be necessary to include additional fiducial marks or labeling to indicate the correct orientation.
The CAM editor can be used to rotate and mirror board designs as needed to create a consistent panel layout.
Cam Editor Panelization Workflow
The cam editor panelization workflow typically involves the following steps:
- Import individual board designs into the CAM editor.
- Create a new panel layout and set the panel size and margins.
- Arrange the board designs on the panel using regular or irregular panelization techniques.
- Add tooling features like fiducial marks, tooling holes, and breakaway tabs.
- Verify the panel layout meets manufacturing requirements and design rules.
- Export manufacturing files (Gerber, drill, etc.) for the panelized layout.
The specific steps and tools used may vary depending on the CAM editor software and manufacturer’s requirements.
Common Panelization Issues and Troubleshooting
While cam editor panelization is a reliable process, there are some common issues that can arise. Here are a few examples and troubleshooting tips:
Incorrect Board Spacing
If the spacing between boards is too small, it can cause issues with depaneling and assembly. If the spacing is too large, it can result in wasted material and higher costs.
To troubleshoot, double-check the rail width and spacing against the manufacturer’s specifications and adjust the panel layout accordingly.
Missing or Incorrect Tooling Features
If tooling features like fiducial marks or holes are missing or incorrectly placed, it can cause alignment issues during fabrication and assembly.
To troubleshoot, review the manufacturer’s requirements for tooling features and verify they are correctly added to the panel layout.
Incorrect Board Orientation
If boards are oriented inconsistently or incorrectly on the panel, it can lead to assembly errors and delays.
To troubleshoot, check the board orientation and asymmetry, and ensure the panel layout is consistent and properly labeled.
Manufacturability Issues
If the panelized layout violates manufacturing constraints or design rules, it can result in production delays or quality issues.
To troubleshoot, review the manufacturer’s design rules and specifications, and verify the panel layout meets all requirements. Use the CAM editor’s design rule checking (DRC) tools to identify and correct any violations.
Panelization Best Practices
To optimize the panelization process and ensure the best results, follow these best practices:
- Communicate with the manufacturer early and often to understand their specific requirements and capabilities.
- Keep the board design as simple and consistent as possible to facilitate efficient panelization.
- Use standard panel sizes and tooling features whenever possible to reduce setup time and costs.
- Optimize the panel layout to maximize board count and minimize waste.
- Verify the panelized layout against manufacturing constraints and design rules before exporting files.
- Label the panel clearly and consistently to avoid confusion during fabrication and assembly.
By following these best practices and working closely with the manufacturer, you can streamline the panelization process and ensure high-quality results.
Frequently Asked Questions (FAQ)
What is the purpose of panelization in PCB manufacturing?
Panelization allows multiple individual PCB designs to be fabricated together on a single panel, improving production efficiency and reducing costs.
How do I choose the right panelization technique for my design?
The choice of panelization technique depends on factors like the board size, shape, quantity, and design requirements. Regular grid panelization is suitable for simple, rectangular boards, while irregular techniques like tabbed arrays or step and repeat are used for more complex designs.
What is the minimum spacing between boards on a panel?
The minimum spacing between boards, or rail width, depends on the PCB thickness, material, and depaneling method. Typical rail widths range from 2mm to 5mm, but the exact specification should be confirmed with the manufacturer.
How do I add tooling features to a panelized layout?
Tooling features like fiducial marks, holes, and slots are added to the panel layout using the CAM editor software. The size, shape, and location of these features depend on the manufacturer’s requirements and should be confirmed before finalizing the layout.
What should I do if my panelized layout violates manufacturing constraints?
If the panelized layout violates manufacturing constraints or design rules, review the manufacturer’s specifications and use the CAM editor’s design rule checking (DRC) tools to identify and correct any issues. Communicate with the manufacturer to ensure the layout meets their requirements before exporting files.
Conclusion
Cam editor panelization is a critical process in PCB manufacturing that enables efficient and cost-effective production of high-quality boards. By understanding the techniques, design considerations, and best practices involved in panelization, PCB designers and manufacturers can optimize their workflows and ensure successful results.
This comprehensive guide has covered the fundamentals of cam editor panelization, including its benefits, techniques, design considerations, workflow, and troubleshooting. By applying this knowledge and working closely with manufacturers, you can streamline your panelization process and achieve the best possible outcomes for your PCB projects.
Leave a Reply