Types of Import File Formats in CAM Editors
STEP (Standard for the Exchange of Product Model Data)
STEP (ISO 10303) is a widely used neutral file format for exchanging 3D CAD data between different software systems. It can represent both geometrical and non-geometrical data, such as product structure, metadata, and PMI (Product Manufacturing Information). STEP files have the extension .step
or .stp
.
Advantages:
– Preserves the complete product definition, including geometry, topology, and metadata
– Supports both solid and surface models
– Widely supported by CAD and CAM software
Limitations:
– Large file sizes compared to other formats
– May require additional processing time for complex models
IGES (Initial Graphics Exchange Specification)
IGES (ANSI Y14.26M) is another neutral file format for exchanging 2D and 3D CAD data between different systems. It represents geometry, annotations, and other product definition data. IGES files have the extension .iges
or .igs
.
Advantages:
– Supports a wide range of geometrical entities and non-geometrical data
– Widely supported by CAD and CAM software
– Suitable for both 2D and 3D data exchange
Limitations:
– Limited support for solid modeling compared to STEP
– Potential loss of data or accuracy during translation
Parasolid
Parasolid is a proprietary 3D geometric modeling kernel developed by Siemens PLM Software. It is used as the underlying geometry engine in many CAD and CAM systems. Parasolid files have the extension .x_t
or .x_b
.
Advantages:
– High-quality representation of solid and surface models
– Supports advanced geometric modeling operations
– Maintains model integrity and associativity
Limitations:
– Proprietary format with limited direct support in third-party software
– May require additional translators or plugins for import/export
STL (Standard Tessellation Language)
STL is a simple file format used for representing 3D geometry as a triangular mesh. It is commonly used in additive manufacturing (3D printing) and rapid prototyping. STL files have the extension .stl
.
Advantages:
– Simplicity and ease of processing
– Widely supported by CAM software and 3D printing systems
– Suitable for representing complex freeform surfaces
Limitations:
– Lacks information about color, texture, and material properties
– Prone to errors and inconsistencies in the triangular mesh
– Large file sizes for high-resolution models
Native CAD Formats
In addition to neutral file formats, CAM editors often support direct import of native CAD file formats from popular software packages, such as:
- SOLIDWORKS (
.sldprt
,.sldasm
) - Autodesk Inventor (
.ipt
,.iam
) - PTC Creo (
.prt
,.asm
) - Siemens NX (
.prt
) - CATIA (
.catpart
,.catproduct
)
Advantages:
– Preserves the original design intent and associativity
– Supports advanced features and parameters specific to the CAD system
– Minimizes data loss and translation errors
Limitations:
– Requires the specific CAD software or a compatible viewer/translator
– Compatibility issues between different versions of the same CAD system
Best Practices for Importing Files into CAM Editors
-
Choose the appropriate file format: Consider factors such as the type of geometry (2D/3D, solid/surface), the level of detail required, and the compatibility with the target CAM system when selecting the file format for import.
-
Ensure model integrity: Before importing, check the CAD model for errors, inconsistencies, and incomplete or overlapping geometry. Repair or simplify the model if necessary to avoid issues during the import process.
-
Use the latest file versions: Whenever possible, use the most recent versions of the file formats and software to ensure optimal compatibility and minimize translation errors.
-
Verify the imported geometry: After importing the file into the CAM editor, visually inspect the geometry for accuracy and completeness. Check for missing features, distorted surfaces, or unintended changes in dimensions.
-
Maintain a consistent coordinate system: Ensure that the imported model is properly positioned and oriented in the CAM editor’s coordinate system. Apply necessary transformations or alignments to match the desired setup for machining.
-
Organize and label imported components: When working with multi-component assemblies, organize and label the imported components clearly in the CAM editor’s interface. This helps in selecting the appropriate components for machining operations and avoiding confusion.
-
Validate the machining setup: Before proceeding with toolpath generation, validate the machining setup, including the stock material, fixture, and machine tool configuration, to ensure compatibility with the imported model.
Types of Export File Formats in CAM Editors
G-code
G-code is the most common format for exporting machining instructions from CAM editors to CNC machines. It consists of a sequence of commands that control the motion and functions of the machine tool. G-code files have various extensions, such as .nc
, .ngc
, .cnc
, or .tap
, depending on the machine controller.
Advantages:
– Direct compatibility with most CNC machine controllers
– Human-readable and editable format
– Supports a wide range of machining operations and functions
Limitations:
– Lack of standardization across different machine controllers and CAM systems
– Limited support for advanced features like tool radius compensation and adaptive feedrates
APT (Automatically Programmed Tool)
APT is a high-level programming language used for describing machining operations and toolpaths. It serves as an intermediate format between CAM editors and post-processors that generate machine-specific G-code. APT files have the extension .apt
.
Advantages:
– Provides a machine-independent description of machining operations
– Supports advanced features like cutter radius compensation and parametric programming
– Enables the use of custom macros and subroutines
Limitations:
– Requires a post-processor to generate machine-specific G-code
– Limited direct support in modern CNC machine controllers
STEP-NC
STEP-NC (ISO 14649) is an extension of the STEP standard that aims to provide a more intelligent and feature-based approach to CNC machining. It describes machining operations, tools, and strategies using a high-level, machine-independent format. STEP-NC files have the extension .p21
or .p21e
.
Advantages:
– Enables bi-directional data exchange between CAD, CAM, and CNC systems
– Supports feature-based machining and advanced optimization techniques
– Provides a more efficient and flexible approach to CNC programming
Limitations:
– Limited industry adoption and support in current CNC machine controllers
– Requires compatible CAM software and post-processors
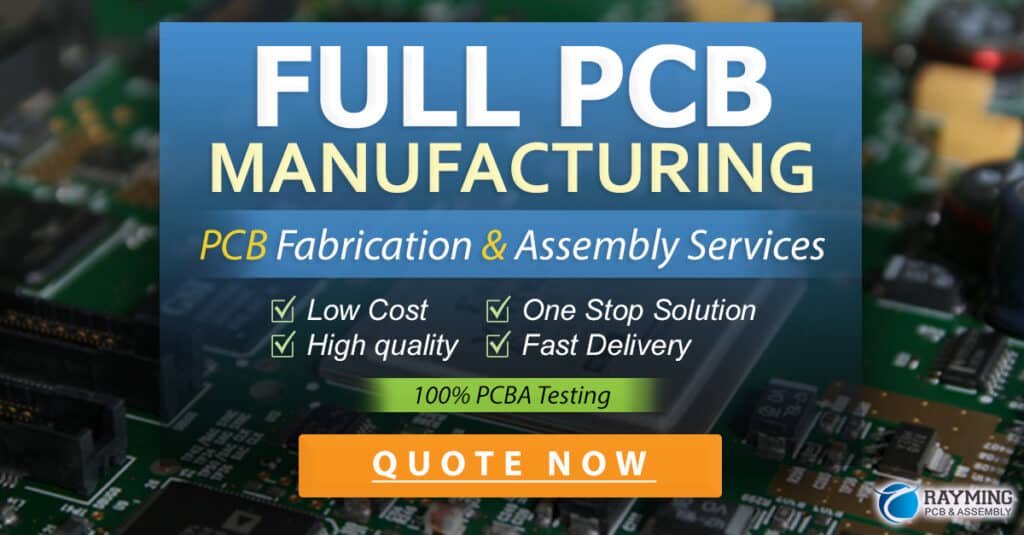
Best Practices for Exporting Files from CAM Editors
-
Select the appropriate post-processor: Choose a post-processor that matches the specific make, model, and configuration of the target CNC machine. Ensure that the post-processor is up-to-date and properly configured.
-
Verify the exported G-code: Before sending the exported G-code to the machine, verify it using a G-code simulator or viewer. Check for any errors, collisions, or unintended motions that may cause issues during machining.
-
Optimize the machining parameters: Adjust the machining parameters, such as feedrates, spindle speeds, and tool selections, to optimize the performance and quality of the machining process. Consider factors like material properties, tool wear, and machine capabilities.
-
Include necessary setup information: When exporting the machining data, include relevant setup information, such as tool lists, work offsets, and fixture details, to ensure proper setup and execution on the CNC machine.
-
Use a consistent file naming convention: Adopt a clear and consistent file naming convention for exported files, including information like part number, revision, and date. This helps in organizing and tracking the machining data effectively.
-
Document any custom settings or modifications: If any custom settings, macros, or modifications are used in the post-processor or CNC machine controller, document them clearly to ensure repeatability and ease of maintenance.
-
Collaborate with the machine operator: Work closely with the CNC machine operator to ensure smooth communication and understanding of the exported machining data. Provide necessary instructions, clarifications, or support to achieve the desired machining results.
Frequently Asked Questions (FAQ)
1. What is the difference between STEP and IGES file formats?
STEP and IGES are both neutral file formats used for exchanging CAD data between different systems. The main differences are:
- STEP is a newer and more advanced standard that supports a wider range of data, including solid modeling, product structure, and metadata.
- IGES is an older format that primarily focuses on representing geometric entities and has limited support for solid modeling.
- STEP files are generally larger in size compared to IGES files.
2. Can I import a CAD file directly into a CAM editor without using a neutral file format?
Yes, many CAM editors support direct import of native CAD file formats from popular software packages like SOLIDWORKS, Autodesk Inventor, and PTC Creo. This allows for a more seamless data exchange and preserves the original design intent and associativity. However, it requires the specific CAD software or a compatible viewer/translator.
3. What should I do if the imported geometry has errors or inconsistencies?
If the imported geometry has errors or inconsistencies, you should:
- Check the original CAD model for any issues and repair or simplify it if necessary before importing.
- Use the CAM editor’s built-in healing tools or geometry repair functions to fix any detected problems.
- If the errors persist, consider re-exporting the model using a different file format or consult with the CAD designer for assistance.
4. How do I choose the right post-processor for my CNC machine?
To choose the right post-processor for your CNC machine, follow these steps:
- Identify the specific make, model, and controller type of your CNC machine.
- Consult with the machine manufacturer or CAM software vendor for recommended post-processors.
- Look for a post-processor that matches your machine’s specifications and supports the required machining functions and features.
- Test the post-processor with sample parts and verify the generated G-code for accuracy and compatibility.
5. What are the benefits of using STEP-NC over traditional G-code?
STEP-NC offers several benefits over traditional G-code:
- It provides a more intelligent and feature-based approach to CNC programming, allowing for easier data exchange between CAD, CAM, and CNC systems.
- It supports advanced machining strategies and optimization techniques, leading to more efficient and flexible manufacturing processes.
- It enables bi-directional communication between the machine controller and the CAM system, allowing for real-time feedback and process monitoring.
- It reduces the reliance on machine-specific post-processors and promotes standardization in CNC programming.
However, the adoption of STEP-NC is still limited in the industry, and it requires compatible CAM software and machine controllers.
Conclusion
CAM editor imports and exports play a crucial role in the smooth and efficient exchange of data between CAD, CAM, and CNC systems. By understanding the various file formats, their advantages and limitations, and following best practices for importing and exporting, users can ensure successful data transfer and optimize their machining processes.
As technology advances, new standards and formats like STEP-NC are emerging to provide more intelligent and feature-based approaches to CNC programming. While the adoption of these new technologies is still in progress, it is essential for CAM users to stay updated with the latest developments and evaluate their potential benefits for their specific manufacturing needs.
Ultimately, effective communication and collaboration between CAD designers, CAM programmers, and CNC machine operators are key to achieving the desired machining results. By working together and leveraging the capabilities of CAM editors and related technologies, manufacturers can streamline their processes, reduce errors, and improve the overall quality and efficiency of their products.
Leave a Reply