Introduction to PCB Complexity and First Pass Yields
Printed Circuit Board (PCB) complexity and first pass yields are critical factors in the manufacturing process of electronic devices. PCB complexity refers to the intricacy of the board’s design, including the number of layers, components, and interconnections. First pass yield (FPY) is a metric that measures the percentage of boards that pass all quality tests and inspections on the first attempt, without requiring rework or repair.
Calculating and optimizing PCB complexity and first pass yields is essential for manufacturers to reduce costs, improve efficiency, and deliver high-quality products to their customers. In this article, we will delve into the factors that influence PCB complexity, the importance of first pass yields, and strategies for calculating and improving these metrics.
Factors Influencing PCB Complexity
Several factors contribute to the complexity of a PCB design:
-
Number of Layers: Multi-layer PCBs are more complex than single or double-layer boards, as they require precise alignment and interconnections between layers.
-
Component Density: Higher component density, measured in components per square inch, increases the complexity of the board.
-
Miniaturization: As electronic devices become smaller, PCBs must accommodate more components in a smaller space, leading to increased complexity.
-
High-Speed Signals: Boards designed for high-speed applications require careful consideration of signal integrity, EMI, and impedance matching, adding to the complexity.
-
Advanced Manufacturing Techniques: The use of advanced manufacturing techniques, such as HDI (High Density Interconnect) and embedded components, can increase PCB complexity.
The Importance of First Pass Yields
First pass yields are a critical metric for PCB manufacturers, as they directly impact production costs, throughput, and customer satisfaction. Some key benefits of high first pass yields include:
-
Reduced Rework and Scrap Costs: Higher FPY means fewer boards require rework or repair, reducing material and labor costs associated with these processes.
-
Improved Production Efficiency: With fewer boards requiring rework, production lines can operate more efficiently, increasing overall throughput.
-
Shorter Lead Times: High FPY enables manufacturers to deliver products to customers more quickly, as less time is spent on rework and repairs.
-
Enhanced Customer Satisfaction: Consistently delivering high-quality products with minimal defects leads to increased customer satisfaction and loyalty.
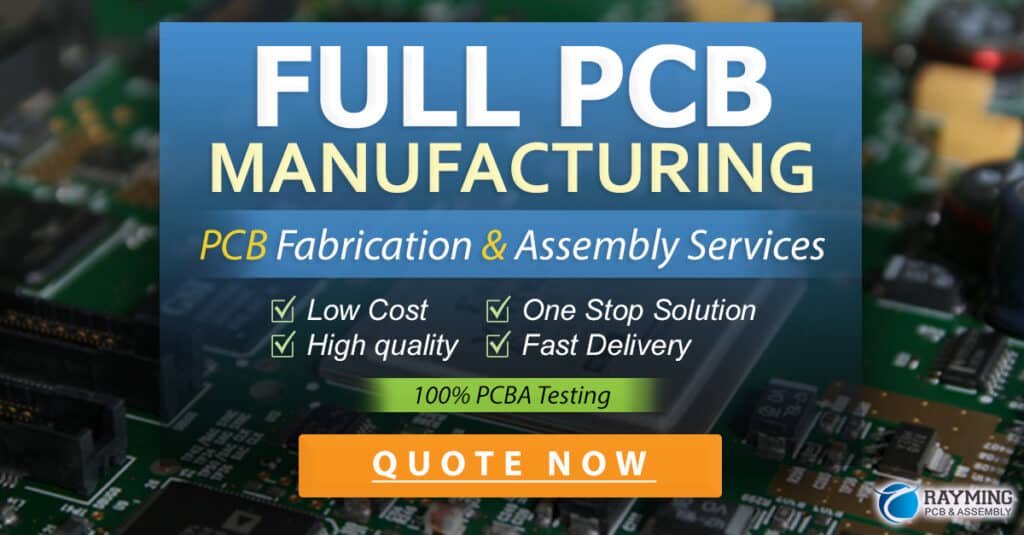
Calculating PCB Complexity
To calculate PCB complexity, manufacturers use a combination of factors to develop a complexity index. One common method is to assign weights to each complexity factor and calculate a weighted average. For example:
Factor | Weight |
---|---|
Number of Layers | 30% |
Component Density | 25% |
Miniaturization | 20% |
High-Speed Signals | 15% |
Manufacturing Techniques | 10% |
Using this method, a manufacturer can calculate a PCB complexity index on a scale of 1 to 10, with higher values indicating greater complexity.
Strategies for Improving First Pass Yields
To improve first pass yields, manufacturers can implement several strategies:
-
Design for Manufacturability (DFM): Collaborating with PCB designers to ensure designs are optimized for manufacturing can significantly improve FPY.
-
Process Control: Implementing strict process controls, such as Statistical Process Control (SPC), can help identify and correct issues before they lead to defects.
-
Automated Inspection: Utilizing automated optical inspection (AOI) and X-ray inspection systems can detect defects early in the manufacturing process, reducing the number of defective boards that progress to later stages.
-
Employee Training: Investing in comprehensive training programs for production staff can help reduce human errors and improve overall quality.
-
Continuous Improvement: Regularly reviewing and analyzing first pass yield data to identify trends and areas for improvement can help manufacturers continuously optimize their processes.
Case Study: Improving FPY Through DFM
To illustrate the impact of Design for Manufacturability on first pass yields, consider the following case study:
Company XYZ, a leading electronics manufacturer, was experiencing low first pass yields on a complex, multi-layer PCB for a new product. The initial FPY was only 65%, leading to significant rework costs and production delays.
To address this issue, the company formed a cross-functional team consisting of PCB designers, manufacturing engineers, and quality specialists. The team conducted a thorough review of the PCB design, identifying several areas where the design could be optimized for manufacturing.
Some of the key changes implemented included:
- Increasing the minimum trace width and spacing to reduce the risk of short circuits
- Adjusting the placement of components to improve accessibility for automated assembly equipment
- Modifying the solder mask design to improve the reliability of solder joints
After implementing these DFM changes, Company XYZ saw a dramatic improvement in first pass yields. The FPY for the complex PCB increased from 65% to 92%, resulting in significant cost savings and improved customer satisfaction.
This case study demonstrates the power of collaboration between design and manufacturing teams to optimize PCB complexity and improve first pass yields.
FAQ
-
Q: What is PCB complexity, and why is it important?
A: PCB complexity refers to the intricacy of a printed circuit board’s design, including factors such as the number of layers, component density, and advanced manufacturing techniques. It is important because higher complexity can impact manufacturing costs, reliability, and first pass yields. -
Q: How does first pass yield affect PCB manufacturing?
A: First pass yield (FPY) is the percentage of PCBs that pass all quality inspections and tests on the first attempt, without requiring rework or repair. Higher FPY leads to lower production costs, improved efficiency, and faster delivery times to customers. -
Q: What are some strategies for improving first pass yields?
A: Strategies for improving first pass yields include implementing Design for Manufacturability (DFM) practices, enhancing process control, utilizing automated inspection systems, investing in employee training, and continuously reviewing and analyzing FPY data to identify areas for improvement. -
Q: How can PCB designers contribute to improving first pass yields?
A: PCB designers can contribute to improving first pass yields by collaborating with manufacturing teams to ensure designs are optimized for manufacturability. This includes considering factors such as trace width and spacing, component placement, and solder mask design. -
Q: What role does automated inspection play in improving first pass yields?
A: Automated inspection systems, such as automated optical inspection (AOI) and X-ray inspection, can detect defects early in the manufacturing process. This helps reduce the number of defective boards that progress to later stages, ultimately improving first pass yields and reducing rework costs.
Conclusion
Calculating and optimizing PCB complexity and first pass yields are critical for electronics manufacturers to remain competitive in today’s market. By understanding the factors that contribute to PCB complexity and implementing strategies to improve first pass yields, manufacturers can reduce costs, enhance efficiency, and deliver high-quality products to their customers.
Key strategies for success include fostering collaboration between design and manufacturing teams, implementing robust process controls, investing in automated inspection systems, and continuously monitoring and analyzing first pass yield data. By adopting these best practices, manufacturers can navigate the challenges of increasing PCB complexity and achieve sustainable growth in the dynamic electronics industry.
Leave a Reply