Introduction to Fabrication Capability
Fabrication capability refers to the ability of a manufacturing facility to produce products that meet the required specifications and quality standards. It is a critical factor in determining the overall efficiency and effectiveness of a manufacturing process. Calculating fabrication capability coefficients is essential for manufacturers to assess their production capabilities and identify areas for improvement.
What are Fabrication Capability Coefficients?
Fabrication capability coefficients are statistical measures that quantify the ability of a manufacturing process to produce products within specified tolerances. These coefficients provide insight into the reliability and consistency of the manufacturing process, helping manufacturers make informed decisions about process improvements and quality control.
The two primary fabrication capability coefficients are:
- Cp (Capability Process): This coefficient measures the potential capability of a process, assuming that the process is centered within the specification limits. It is calculated as:
Cp = (USL – LSL) / (6 * σ)
Where:
– USL is the Upper Specification Limit
– LSL is the Lower Specification Limit
– σ is the standard deviation of the process
- Cpk (Capability Process Index): This coefficient measures the actual capability of a process, taking into account the centering of the process within the specification limits. It is calculated as:
Cpk = min((USL – μ) / (3 * σ), (μ – LSL) / (3 * σ))
Where:
– μ is the mean of the process
Importance of Calculating Fabrication Capability Coefficients
Calculating fabrication capability coefficients is crucial for several reasons:
-
Quality Control: By monitoring fabrication capability coefficients, manufacturers can ensure that their processes are capable of producing products that meet the required quality standards consistently.
-
Process Improvement: Analyzing fabrication capability coefficients helps identify areas where the manufacturing process can be improved to increase efficiency and reduce defects.
-
Cost Reduction: Improving fabrication capability can lead to reduced scrap, rework, and warranty costs, ultimately resulting in cost savings for the manufacturer.
-
Customer Satisfaction: Consistently producing high-quality products that meet customer specifications leads to increased customer satisfaction and loyalty.
Steps to Calculate Fabrication Capability Coefficients
To calculate fabrication capability coefficients, follow these steps:
-
Collect Data: Gather a representative sample of data from the manufacturing process, including measurements of critical product characteristics.
-
Calculate Process Parameters: Determine the mean (μ) and standard deviation (σ) of the process using the collected data.
-
Identify Specification Limits: Obtain the Upper Specification Limit (USL) and Lower Specification Limit (LSL) for the product characteristic being analyzed.
-
Calculate Cp: Use the formula Cp = (USL – LSL) / (6 * σ) to calculate the capability process coefficient.
-
Calculate Cpk: Use the formula Cpk = min((USL – μ) / (3 * σ), (μ – LSL) / (3 * σ)) to calculate the capability process index.
-
Interpret Results: Compare the calculated Cp and Cpk values to industry standards and customer requirements to determine if the process is capable of meeting the desired quality levels.
Example Calculation
Let’s consider an example of calculating fabrication capability coefficients for a manufacturing process that produces a critical component with a target dimension of 100 mm ± 0.5 mm.
Given:
– USL = 100.5 mm
– LSL = 99.5 mm
– μ = 100.2 mm
– σ = 0.2 mm
Step 1: Calculate Cp
Cp = (USL – LSL) / (6 * σ)
Cp = (100.5 – 99.5) / (6 * 0.2) = 0.833
Step 2: Calculate Cpk
Cpk = min((USL – μ) / (3 * σ), (μ – LSL) / (3 * σ))
Cpk = min((100.5 – 100.2) / (3 * 0.2), (100.2 – 99.5) / (3 * 0.2))
Cpk = min(0.5, 1.167) = 0.5
Interpretation:
– A Cp value of 0.833 indicates that the process is not capable of meeting the specification limits, as it is less than the generally accepted minimum value of 1.33.
– A Cpk value of 0.5 suggests that the process is not centered within the specification limits and has a high risk of producing defective products.
Based on these results, the manufacturer should investigate ways to improve the process capability, such as reducing process variation, centering the process, or adjusting the specification limits.
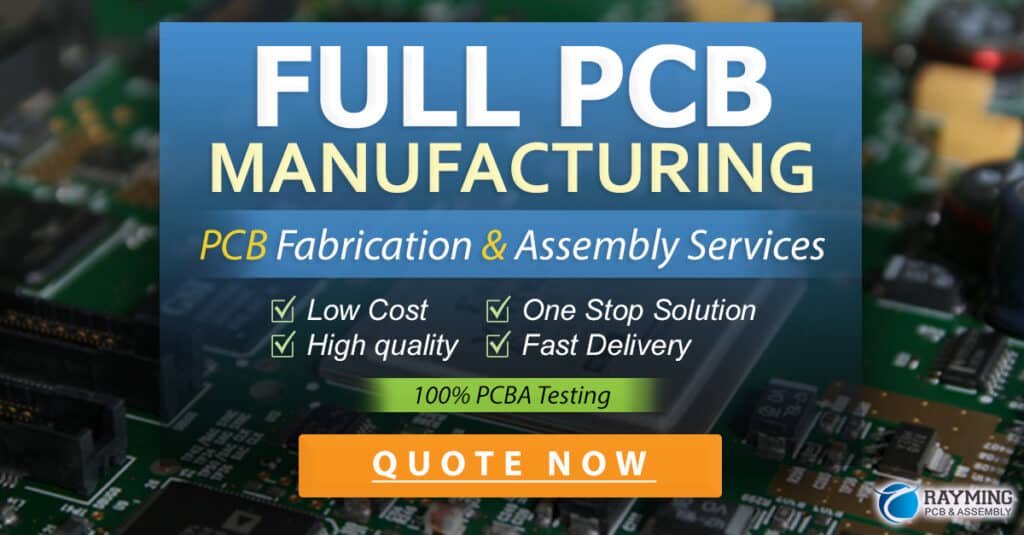
Factors Affecting Fabrication Capability
Several factors can influence a manufacturing process’s fabrication capability, including:
-
Machine Condition: The condition of the manufacturing equipment, including its age, maintenance, and calibration, can impact the process’s ability to produce consistent and accurate results.
-
Operator Skill: The skill level and training of the operators running the manufacturing process can affect the quality and consistency of the output.
-
Raw Materials: Variations in the quality and properties of raw materials can introduce variability into the manufacturing process, affecting the final product’s quality.
-
Process Design: The design of the manufacturing process, including the sequence of operations, tooling, and process parameters, can influence the fabrication capability.
-
Environmental Conditions: Temperature, humidity, and other environmental factors can impact the performance of the manufacturing equipment and the properties of the materials being processed.
Strategies for Improving Fabrication Capability
Manufacturers can employ various strategies to improve their fabrication capability and ensure that their processes consistently produce high-quality products:
-
Statistical Process Control (SPC): Implementing SPC techniques, such as control charts and process capability analysis, can help monitor process performance and identify opportunities for improvement.
-
Process Optimization: Conducting experiments and analyzing process data to optimize process parameters, such as machine settings, cycle times, and tool wear, can enhance fabrication capability.
-
Training and Skill Development: Investing in operator training and skill development programs can improve the consistency and quality of the manufacturing process output.
-
Preventive Maintenance: Implementing a robust preventive maintenance program for manufacturing equipment can minimize downtime, improve machine performance, and ensure consistent product quality.
-
Supplier Quality Management: Working closely with suppliers to ensure the quality and consistency of raw materials can reduce variability in the manufacturing process and improve fabrication capability.
Frequently Asked Questions (FAQ)
-
Q: What is the difference between Cp and Cpk?
A: Cp measures the potential capability of a process, assuming it is centered within the specification limits, while Cpk measures the actual capability, taking into account the centering of the process. -
Q: What are the generally accepted minimum values for Cp and Cpk?
A: The generally accepted minimum values for Cp and Cpk are 1.33 and 1.25, respectively. These values indicate that the process is capable of producing products within the specification limits. -
Q: Can a process have a high Cp value but a low Cpk value?
A: Yes, a process can have a high Cp value, indicating that it is potentially capable of meeting the specification limits, but a low Cpk value, suggesting that the process is not centered within the limits and may produce defective products. -
Q: How often should fabrication capability coefficients be calculated?
A: The frequency of calculating fabrication capability coefficients depends on the nature of the manufacturing process and the criticality of the product characteristics. It is generally recommended to calculate these coefficients regularly, such as monthly or quarterly, or whenever there are significant changes to the process or product specifications. -
Q: What should be done if the fabrication capability coefficients indicate that a process is not capable?
A: If the fabrication capability coefficients indicate that a process is not capable, manufacturers should investigate the root causes of the issue and implement corrective actions. This may involve process optimization, equipment maintenance, operator training, or other improvement initiatives.
Conclusion
Calculating fabrication capability coefficients is a critical aspect of ensuring the quality and consistency of manufactured products. By understanding and monitoring these coefficients, manufacturers can identify areas for improvement, reduce defects, and ultimately enhance customer satisfaction. Implementing strategies such as statistical process control, process optimization, and preventive maintenance can help improve fabrication capability and drive continuous improvement in the manufacturing process.
As the manufacturing landscape continues to evolve, with increasing demands for higher quality, faster delivery, and lower costs, the importance of fabrication capability will only continue to grow. By embracing the tools and techniques for calculating and improving fabrication capability coefficients, manufacturers can position themselves for success in an increasingly competitive market.
Leave a Reply