What is a Faraday Cage?
A Faraday cage, also known as a Faraday shield, is an enclosure made of conductive material that blocks external electromagnetic fields (EMF) from interfering with the contents inside the cage. The cage is named after the English scientist Michael Faraday, who invented it in 1836.
The principle behind a Faraday cage is that the external electromagnetic field causes the electric charges within the cage’s conducting material to be distributed such that they cancel the field’s effect in the cage’s interior. This phenomenon is known as electrostatic shielding.
Applications of Faraday Cages
Faraday cages are used in various applications to protect sensitive electronic equipment from electromagnetic interference (EMI). Some common applications include:
- Shielding electronic devices from external radio frequency interference (RFI)
- Protecting medical equipment, such as MRI machines, from external EMI
- Shielding sensitive measuring equipment in laboratories
- Protecting electronic equipment in industrial environments with high EMI levels
- Shielding government and military facilities to prevent eavesdropping and data theft
Why Build a Faraday Cage?
In today’s world, electronic devices are ubiquitous, and with the increasing use of wireless technologies, EMI has become a significant concern. EMI can cause various issues, ranging from minor disturbances to complete equipment failure. Building a Faraday cage can help mitigate these issues by providing a shielded environment for sensitive electronic devices.
Common Sources of EMI
EMI can originate from various sources, both natural and human-made. Some common sources of EMI include:
- Radio and television broadcasts
- Mobile phones and wireless networks
- Microwave ovens
- Power lines and electrical equipment
- Lightning and solar flares
Effects of EMI on Electronic Devices
EMI can have various effects on electronic devices, depending on the intensity and frequency of the interference. Some common effects include:
- Noise and distortion in audio and video systems
- Data corruption and loss in computer systems
- Malfunctioning of sensitive measuring equipment
- Reduced performance and efficiency of electronic devices
- Complete failure of electronic components
Designing a Faraday Cage
When designing a Faraday cage, several factors must be considered to ensure optimal shielding performance. These factors include the choice of materials, the size and shape of the cage, and the frequency range of the EMI to be shielded.
Choosing the Right Materials
The most common materials used for building Faraday cages are:
- Copper
- Aluminum
- Steel
- Brass
The choice of material depends on the specific application and the frequency range of the EMI to be shielded. Copper and aluminum are the most effective materials for shielding high-frequency EMI, while steel and brass are more suitable for low-frequency EMI.
Material | Shielding Effectiveness (dB) | Frequency Range |
---|---|---|
Copper | 100+ | 10 kHz – 10 GHz |
Aluminum | 80 – 100 | 10 kHz – 1 GHz |
Steel | 60 – 80 | 10 kHz – 100 MHz |
Brass | 50 – 70 | 10 kHz – 10 MHz |
Determining the Size and Shape of the Cage
The size and shape of the Faraday cage depend on the size and shape of the electronic device to be shielded. The cage should be large enough to accommodate the device and any necessary connections, such as power and data cables.
The shape of the cage can also affect its shielding performance. A spherical or cylindrical cage provides better shielding than a rectangular or square cage, as it minimizes the number of edges and corners where EMI can penetrate.
Calculating the Shielding Effectiveness
The shielding effectiveness of a Faraday cage is measured in decibels (dB) and is defined as the ratio of the electric field strength outside the cage to the electric field strength inside the cage. The higher the shielding effectiveness, the better the cage’s ability to block EMI.
The shielding effectiveness of a Faraday cage can be calculated using the following formula:
SE = 20 log₁₀(E₀/E₁)
Where:
– SE is the shielding effectiveness in dB
– E₀ is the electric field strength outside the cage
– E₁ is the electric field strength inside the cage
For example, if the electric field strength outside the cage is 100 V/m and the electric field strength inside the cage is 1 V/m, the shielding effectiveness would be:
SE = 20 log₁₀(100/1) = 40 dB
This means that the Faraday cage reduces the electric field strength inside the cage by a factor of 100, or 40 dB.
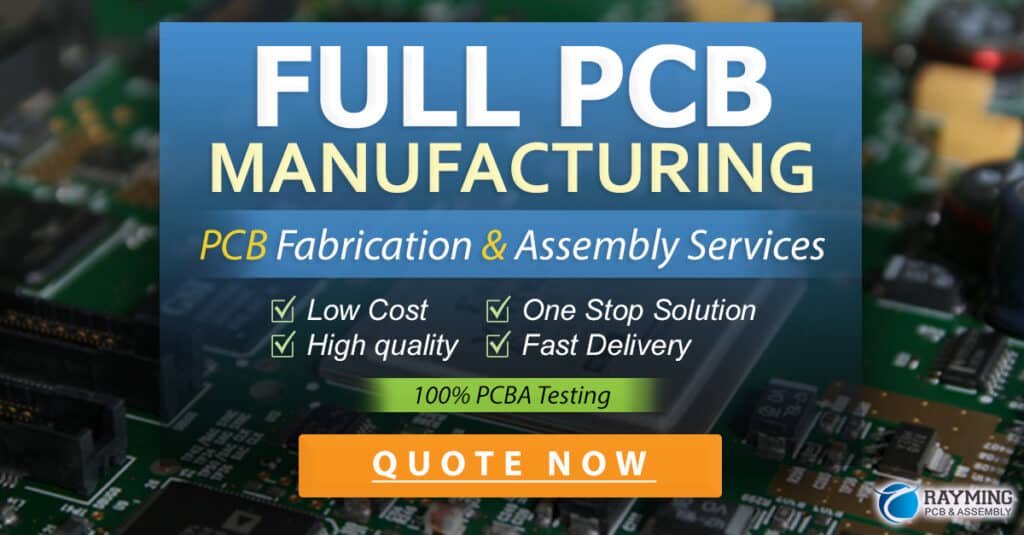
Building a Faraday Cage
Building a Faraday cage requires careful planning and execution to ensure optimal shielding performance. The following steps outline the general process for building a Faraday cage:
- Determine the size and shape of the cage based on the electronic device to be shielded.
- Choose the appropriate material for the cage based on the frequency range of the EMI to be shielded.
- Cut the material to the desired size and shape, allowing for overlaps at the seams.
- Join the pieces of the cage together using conductive adhesive, solder, or welding.
- Ensure that all seams are properly sealed and that there are no gaps or holes in the cage.
- Test the shielding effectiveness of the cage using an EMI meter or spectrum analyzer.
Tools and Materials Required
To build a Faraday cage, you will need the following tools and materials:
- Conductive material (copper, aluminum, steel, or brass)
- Cutting tools (tin snips, hacksaw, or CNC machine)
- Conductive adhesive, solder, or welding equipment
- EMI meter or spectrum analyzer
- Safety equipment (gloves, safety glasses, and respirator)
Step-by-Step Guide
- Cut the conductive material to the desired size and shape, allowing for overlaps at the seams.
- Clean the surfaces of the material to ensure good electrical contact.
- Apply conductive adhesive, solder, or weld the seams together, ensuring a continuous conductive path.
- Inspect the cage for any gaps or holes and seal them with conductive material.
- Connect the cage to a common ground point to ensure proper shielding.
- Test the shielding effectiveness of the cage using an EMI meter or spectrum analyzer.
Testing and Validation
Once the Faraday cage is built, it is essential to test and validate its shielding effectiveness to ensure that it meets the required specifications. Testing can be performed using various methods, including:
- EMI meter: Measures the electric field strength inside and outside the cage to determine the shielding effectiveness.
- Spectrum analyzer: Measures the frequency spectrum of the EMI inside and outside the cage to determine the shielding effectiveness at specific frequencies.
- Antenna and receiver: Transmits a known signal outside the cage and measures the signal strength inside the cage to determine the shielding effectiveness.
Interpreting Test Results
The test results should be compared to the required specifications to determine if the Faraday cage meets the shielding requirements. If the shielding effectiveness is lower than expected, the following factors should be considered:
- Material choice: Ensure that the appropriate material is used for the frequency range of the EMI to be shielded.
- Seam integrity: Check the seams for any gaps or holes that may allow EMI to penetrate the cage.
- Grounding: Ensure that the cage is properly grounded to a common ground point.
Maintenance and Repair
Regular maintenance and repair of the Faraday cage are essential to ensure its continued shielding effectiveness. Periodic inspections should be performed to check for any damage or degradation of the conductive material, and repairs should be made as necessary.
Frequently Asked Questions (FAQ)
-
Q: Can a Faraday cage block all types of EMI?
A: A Faraday cage can effectively shield against most types of EMI, but its effectiveness depends on the frequency range of the EMI and the materials used to construct the cage. -
Q: How thick should the walls of a Faraday cage be?
A: The thickness of the walls depends on the frequency range of the EMI to be shielded. For high-frequency EMI, a thin layer of conductive material (e.g., copper or aluminum foil) may be sufficient, while for low-frequency EMI, thicker walls may be required. -
Q: Can a Faraday cage be made from non-conductive materials?
A: No, a Faraday cage must be made from conductive materials to provide effective shielding against EMI. -
Q: Can a Faraday cage protect against EMP (electromagnetic pulse)?
A: Yes, a properly designed and constructed Faraday cage can protect electronic devices from the effects of an EMP. -
Q: How often should a Faraday cage be tested for shielding effectiveness?
A: The frequency of testing depends on the specific application and the criticality of the shielded equipment. In general, testing should be performed at least annually or whenever modifications are made to the cage or the shielded equipment.
Conclusion
Building a Faraday cage is an effective way to protect sensitive electronic equipment from the harmful effects of EMI. By understanding the principles of electromagnetic shielding and following the proper design and construction techniques, a Faraday cage can provide a high level of shielding effectiveness against a wide range of EMI sources.
When designing and building a Faraday cage, it is essential to consider factors such as material choice, size and shape, and seam integrity to ensure optimal shielding performance. Testing and validation of the cage’s shielding effectiveness should be performed regularly to ensure that it continues to meet the required specifications.
In conclusion, a well-designed and constructed Faraday cage can provide a reliable and effective solution for protecting electronic equipment from the ever-increasing levels of EMI in today’s world.
Leave a Reply