Introduction to Patch Antennas
Patch antennas, also known as microstrip antennas, are popular choices for wireless communication systems due to their low profile, low cost, and ease of fabrication. These antennas are widely used in various applications, such as mobile devices, wireless routers, and GPS receivers. In this article, we will guide you through the process of designing and building your own patch antenna for your next printed circuit board (PCB) project.
What is a Patch Antenna?
A patch antenna consists of a metallic patch, typically made of copper, printed on a dielectric substrate. The patch is usually rectangular or circular in shape and is designed to resonate at a specific frequency. The dimensions of the patch, the properties of the substrate, and the feeding technique determine the antenna’s performance characteristics, such as resonant frequency, bandwidth, and radiation pattern.
Advantages of Patch Antennas
- Low profile and lightweight
- Easy to fabricate and integrate with PCBs
- Cost-effective
- Versatile in terms of resonant frequency and polarization
- Suitable for array configurations
Designing a Patch Antenna
To design a patch antenna, you need to consider several factors, such as the desired resonant frequency, substrate material, and feeding technique. In this section, we will walk you through the steps involved in designing a rectangular patch antenna.
Step 1: Choose the Resonant Frequency and Substrate
The first step in designing a patch antenna is to determine the desired resonant frequency (fr) and choose a suitable substrate material. The resonant frequency depends on the application and the available frequency band. Common frequency bands for patch antennas include:
- 2.4 GHz (IEEE 802.11b/g/n, Bluetooth)
- 5 GHz (IEEE 802.11a/n/ac)
- 1.575 GHz (GPS L1 band)
The substrate material affects the antenna’s performance and size. A substrate with a higher dielectric constant (εr) results in a smaller antenna but may reduce the bandwidth and efficiency. Popular substrate materials for patch antennas include:
- FR-4 (εr ≈ 4.4)
- Rogers RO4003C (εr = 3.55)
- Duroid 5880 (εr = 2.2)
Step 2: Calculate the Patch Dimensions
To calculate the dimensions of the rectangular patch, use the following equations:
- Effective dielectric constant (εreff):
εreff = (εr + 1) / 2 + (εr – 1) / 2 * (1 + 12 * h / W)-0.5
where:
– εr is the dielectric constant of the substrate
– h is the substrate thickness
– W is the patch width
- Patch width (W):
W = c / (2 * fr * sqrt((εr + 1) / 2))
where:
– c is the speed of light (3 × 108 m/s)
– fr is the resonant frequency
- Effective length (Leff):
Leff = c / (2 * fr * sqrt(εreff))
- Patch length (L):
L = Leff – 2 * ΔL
where:
– ΔL = 0.412 * h * (εreff + 0.3) * (W / h + 0.264) / ((εreff – 0.258) * (W / h + 0.8))
Step 3: Choose the Feeding Technique
There are several feeding techniques for patch antennas, each with its advantages and disadvantages. The most common feeding techniques are:
- Microstrip line feed
- Coaxial probe feed
- Aperture-coupled feed
- Proximity-coupled feed
For simplicity, we will focus on the microstrip line feed, which is easy to fabricate and provides good impedance matching.
Simulating and Optimizing the Patch Antenna
Before fabricating the patch antenna, it is essential to simulate its performance using electromagnetic simulation software, such as CST Studio Suite, ANSYS HFSS, or Sonnet. These tools allow you to optimize the antenna’s dimensions, substrate properties, and feeding technique to achieve the desired performance characteristics.
During the simulation process, pay attention to the following parameters:
- Return loss (S11): Aim for a return loss below -10 dB at the resonant frequency.
- Bandwidth: Ensure that the antenna’s bandwidth covers the desired frequency range.
- Radiation pattern: Verify that the antenna’s radiation pattern meets the application’s requirements.
Based on the simulation results, fine-tune the antenna’s dimensions and feeding technique to optimize its performance.
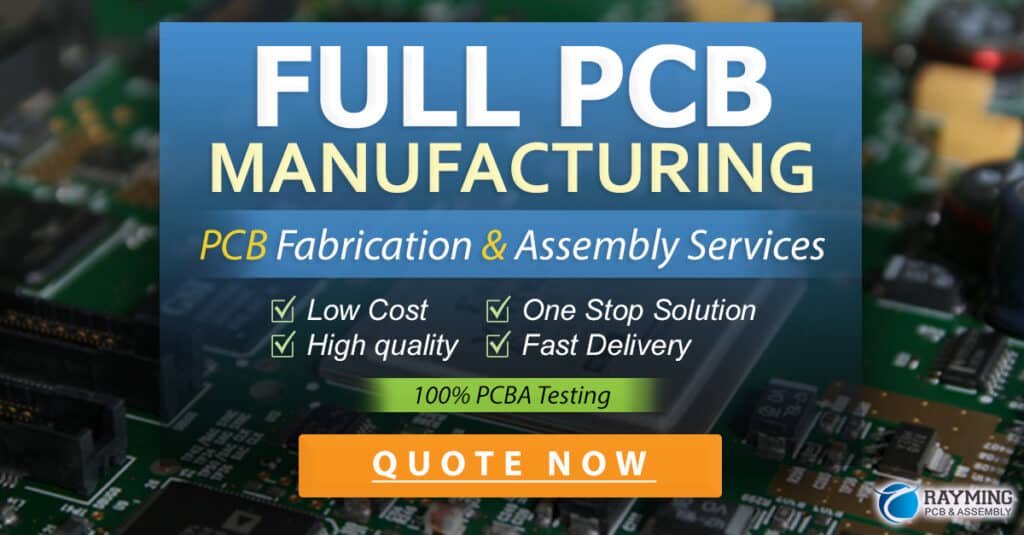
Fabricating the Patch Antenna
Once you have finalized the patch antenna design, you can proceed with the fabrication process. Follow these steps to fabricate the antenna on your PCB:
-
Create the PCB layout: Use PCB design software, such as Altium Designer, Eagle, or KiCad, to create the layout of the patch antenna based on the optimized dimensions.
-
Define the substrate stackup: Specify the substrate material, thickness, and copper layer thickness in the PCB design software.
-
Add the microstrip line feed: Draw the microstrip line feed, connecting it to the patch antenna and the PCB’s ground plane.
-
Generate manufacturing files: Export the Gerber and drill files required for PCB fabrication.
-
Send the files to a PCB manufacturer: Submit the manufacturing files to a PCB fabrication service provider, specifying the substrate material and copper thickness.
-
Assemble the PCB: Once you receive the fabricated PCB, solder the required components, such as the RF connector, to the board.
Testing and Characterizing the Patch Antenna
After fabricating the patch antenna, it is crucial to test and characterize its performance to ensure that it meets the desired specifications. Follow these steps to test the antenna:
-
Set up the test environment: Use a vector network analyzer (VNA) to measure the antenna’s return loss and bandwidth. Position the antenna in an anechoic chamber or a low-reflection environment to minimize interference.
-
Measure the return loss: Connect the antenna to the VNA and measure the return loss (S11) across the frequency range of interest. Verify that the return loss is below -10 dB at the resonant frequency and that the bandwidth meets the requirements.
-
Characterize the radiation pattern: Use an antenna measurement system, such as a far-field or near-field scanner, to measure the antenna’s radiation pattern. Compare the measured pattern with the simulated results to ensure they match.
-
Evaluate the antenna’s efficiency: Measure the antenna’s efficiency using the Wheeler cap method or the directivity/gain method. High efficiency indicates that the antenna is effectively radiating the input power.
-
Test the antenna in the intended application: Integrate the patch antenna into your PCB and test its performance in the target application, such as a wireless communication system or a GPS receiver.
Troubleshooting and Optimization
If the fabricated patch antenna does not meet the desired performance, consider the following troubleshooting and optimization steps:
-
Recheck the dimensions: Verify that the fabricated antenna’s dimensions match the optimized design. Manufacturing tolerances can affect the antenna’s performance.
-
Adjust the feeding technique: Experiment with different feeding techniques or optimize the microstrip line feed’s dimensions to improve impedance matching and bandwidth.
-
Modify the substrate: If the substrate properties differ from the simulation, consider using a different substrate material or adjusting the substrate thickness to improve the antenna’s performance.
-
Investigate the PCB layout: Ensure that the PCB layout, including the ground plane and surrounding components, does not adversely affect the antenna’s performance. Maintain proper grounding and minimize interference from other components.
-
Iterate the design: Based on the test results and troubleshooting, iterate the antenna design by modifying the dimensions, substrate, or feeding technique. Resimulate and fabricate the updated design to verify the improvements.
Applications and Future Developments
Patch antennas find applications in various wireless communication systems, such as:
- Wireless local area networks (WLANs)
- Cellular communication systems
- Global positioning systems (GPS)
- Radio-frequency identification (RFID)
- Satellite communication systems
As wireless technologies continue to evolve, patch antennas are being developed to meet new challenges and requirements. Some of the future developments in patch antenna design include:
-
Multi-band and broadband antennas: Designing patch antennas that operate efficiently across multiple frequency bands or provide wider bandwidths to support high-speed data transmission.
-
Reconfigurable antennas: Developing patch antennas with tunable elements, such as RF switches or varactors, to dynamically adjust the resonant frequency, polarization, or radiation pattern.
-
Antenna arrays and beamforming: Combining multiple patch antennas in array configurations to achieve higher gain, directivity, and beam steering capabilities.
-
Miniaturization techniques: Exploring novel techniques, such as metamaterials or fractal geometries, to reduce the size of patch antennas while maintaining their performance.
-
Integration with emerging technologies: Adapting patch antennas for integration with emerging wireless technologies, such as 5G, Internet of Things (IoT), and millimeter-wave communications.
Frequently Asked Questions (FAQ)
-
What is the typical size of a patch antenna?
The size of a patch antenna depends on the resonant frequency and the substrate material. For example, a rectangular patch antenna designed for the 2.4 GHz band on an FR-4 substrate (εr ≈ 4.4) would have dimensions of approximately 29 mm × 38 mm. -
Can I design a patch antenna for multiple frequency bands?
Yes, you can design a multi-band patch antenna by incorporating multiple resonant elements or using techniques such as slot loading or stacked patches. However, multi-band designs are more complex and may require additional optimization. -
How does the substrate material affect the patch antenna’s performance?
The substrate material’s dielectric constant (εr) and loss tangent (tan δ) influence the antenna’s size, bandwidth, and efficiency. A higher dielectric constant results in a smaller antenna but may reduce the bandwidth and efficiency. A lower loss tangent leads to better efficiency but may increase the antenna’s size. -
What is the typical bandwidth of a patch antenna?
The bandwidth of a patch antenna is relatively narrow, typically around 1-5% of the resonant frequency. However, the bandwidth can be enhanced using techniques such as increasing the substrate thickness, using low-permittivity substrates, or employing impedance matching networks. -
Can I fabricate a patch antenna on a flexible substrate?
Yes, patch antennas can be fabricated on flexible substrates, such as polyimide or liquid crystal polymer (LCP). Flexible antennas are suitable for wearable devices or applications that require conformity to non-planar surfaces. However, the substrate’s flexibility may affect the antenna’s performance and durability.
Conclusion
Designing and building your own patch antenna for your next PCB project can be a rewarding experience. By following the steps outlined in this article, you can create a custom patch antenna that meets your specific requirements. Remember to consider factors such as the resonant frequency, substrate material, and feeding technique during the design process. Simulate and optimize the antenna’s performance before fabrication, and thoroughly test the fabricated antenna to ensure it meets the desired specifications.
As wireless technologies continue to advance, patch antennas will play a crucial role in enabling efficient and reliable communication systems. By understanding the principles and techniques involved in patch antenna design, you can contribute to the development of innovative wireless solutions.
Leave a Reply