Introduction to High Density Interconnect PCBs
High Density Interconnect (HDI) PCBs are a type of printed circuit board that offers higher wiring density than traditional PCBs. This is achieved through the use of smaller vias, finer traces, and micro-vias, which allow for more connections to be made within a smaller area. HDI PCBs are becoming increasingly popular in the electronics industry due to their ability to accommodate the growing demand for smaller, more complex devices.
Advantages of HDI PCBs
- Increased wiring density
- Smaller device footprint
- Improved signal integrity
- Enhanced thermal management
- Reduced electromagnetic interference (EMI)
Applications of HDI PCBs
HDI PCBs are used in a wide range of applications, including:
– Smartphones and tablets
– Wearable devices
– Medical devices
– Automotive electronics
– Aerospace and defense systems
Skip Vias: A Key Technology in HDI PCBs
What are Skip Vias?
Skip vias are a type of via that allows a signal to “skip” one or more layers in a PCB stack-up. Unlike traditional through-hole vias, which extend through the entire thickness of the board, skip vias only connect the layers they need to, reducing the overall via count and improving signal integrity.
Benefits of Using Skip Vias in HDI PCBs
- Reduced via count, leading to increased wiring density
- Improved signal integrity due to shorter via lengths
- Better power delivery and thermal management
- Simplified PCB stack-up design
- Enhanced manufacturing yields
Types of Skip Vias
- Blind Vias
- Connect an outer layer to an inner layer
- Drilled from one side of the board and stop at a specified depth
- Buried Vias
- Connect two or more inner layers
- Not visible from the outer layers
- Micro Vias
- Smaller than traditional vias, typically less than 150 microns in diameter
- Can be stacked to create multi-level connections
Designing HDI PCBs with Skip Vias
PCB Stack-up Design Considerations
When designing an HDI PCB with skip vias, it’s essential to consider the following factors:
– Number of layers required
– Material selection (e.g., FR-4, Rogers, Isola)
– Dielectric thickness and constant
– Copper weight and trace width
– Via sizes and types
A well-designed PCB stack-up ensures optimal signal integrity, power delivery, and thermal management.
Signal Integrity and Power Delivery
To maintain signal integrity and ensure proper power delivery in HDI PCBs with skip vias, designers should:
– Use controlled impedance traces
– Minimize trace lengths and via counts
– Implement proper grounding and shielding techniques
– Use decoupling capacitors to reduce power supply noise
– Simulate and analyze the design using electronic design automation (EDA) tools
Thermal Management Strategies
HDI PCBs with skip vias can generate significant amounts of heat due to their high wiring density. To manage thermal issues, designers can employ the following strategies:
– Use thermal vias to transfer heat away from hot spots
– Implement copper pours and heat sinks
– Select materials with good thermal conductivity
– Optimize component placement for even heat distribution
– Use thermal simulation tools to identify and address potential issues
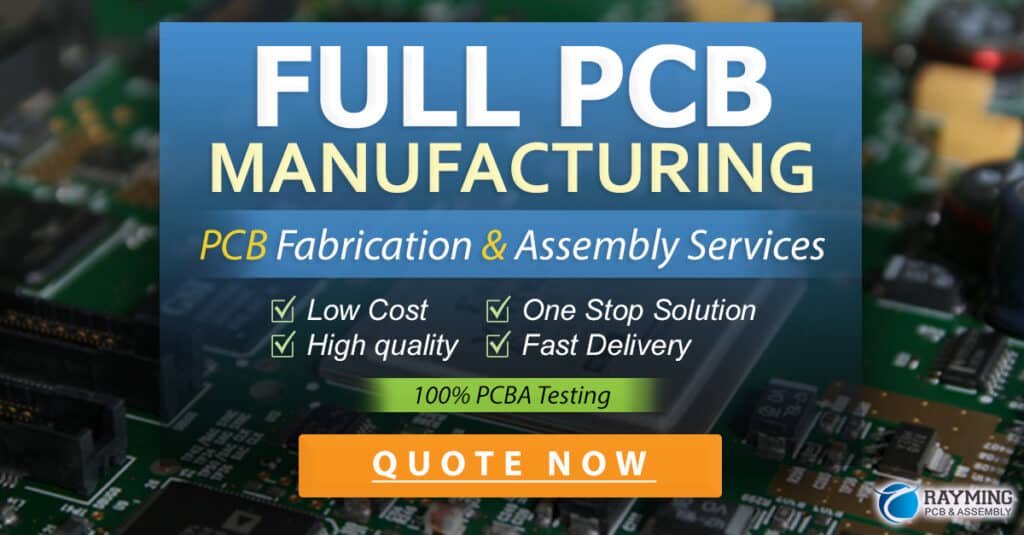
Manufacturing and Assembly of HDI PCBs with Skip Vias
Fabrication Processes
The fabrication of HDI PCBs with skip vias involves several specialized processes:
1. Laser Drilling
– Used to create micro vias and blind vias
– Offers high precision and minimal damage to surrounding areas
2. Plasma Etching
– Removes debris and prepares via walls for plating
– Ensures reliable electrical connections
3. Electroless Copper Plating
– Deposits a thin layer of copper on via walls
– Acts as a seed layer for subsequent electrolytic plating
4. Electrolytic Copper Plating
– Builds up the copper thickness in vias and on traces
– Provides the necessary conductivity for electrical connections
Assembly Techniques
Assembling HDI PCBs with skip vias requires specialized techniques to ensure proper component placement and soldering:
1. Surface Mount Technology (SMT)
– Components are placed on the surface of the PCB and soldered using reflow or wave soldering processes
– Allows for high-density component placement
2. Ball Grid Array (BGA)
– Uses an array of solder balls to connect the component to the PCB
– Provides a high-density, low-profile interconnect solution
3. Chip-on-Board (COB)
– Integrated circuits are directly mounted onto the PCB substrate
– Offers the highest level of miniaturization and performance
Quality Control and Testing
To ensure the reliability and performance of HDI PCBs with skip vias, manufacturers employ rigorous quality control and testing procedures:
– Automated Optical Inspection (AOI)
– X-ray Inspection
– Electrical Testing
– Thermal Cycling
– Microsectioning
– Reliability Testing (e.g., vibration, shock, humidity)
Case Studies and Applications
Smartphone PCB Design
Smartphones are a prime example of devices that benefit from HDI PCBs with skip vias. By using these technologies, smartphone manufacturers can:
– Reduce the overall device size and weight
– Integrate more features and functionality
– Improve battery life and thermal management
– Enhance signal integrity and performance
Medical Device PCB Design
Medical devices often require highly miniaturized and reliable PCBs. HDI PCBs with skip vias are well-suited for this application, as they offer:
– Increased wiring density for complex circuitry
– Improved signal integrity for sensitive measurements
– Enhanced thermal management for heat-generating components
– Reliable performance in demanding environments
Automotive Electronics PCB Design
As vehicles become more sophisticated, the demand for advanced automotive electronics grows. HDI PCBs with skip vias are used in various automotive applications, such as:
– Infotainment systems
– Advanced driver assistance systems (ADAS)
– Engine control units (ECUs)
– Sensors and actuators
These PCBs offer the necessary wiring density, signal integrity, and reliability required for automotive environments.
Future Trends and Developments
Advanced Materials
As HDI PCBs with skip vias continue to evolve, new materials are being developed to improve performance and reliability:
– Low-loss dielectrics for high-speed applications
– High-temperature materials for harsh environments
– Flexible and stretchable substrates for wearable devices
3D Printed Electronics
3D printing technology is emerging as a potential solution for creating complex, multi-layer HDI PCBs with skip vias. This technology offers:
– Rapid prototyping and customization
– Reduced waste and environmental impact
– Potential for new design geometries and functionalities
Artificial Intelligence in PCB Design
Artificial intelligence (AI) and machine learning (ML) are being applied to PCB design to optimize layouts, reduce design time, and improve manufacturability. These technologies can:
– Automate routine design tasks
– Identify and resolve design rule violations
– Predict and mitigate potential issues before fabrication
As AI and ML continue to advance, they will likely play an increasingly important role in the design of HDI PCBs with skip vias.
Frequently Asked Questions (FAQ)
- What is the difference between HDI PCBs and traditional PCBs?
-
HDI PCBs offer higher wiring density, smaller feature sizes, and more advanced via technologies compared to traditional PCBs. This allows for the creation of smaller, more complex devices with improved performance and reliability.
-
How do skip vias improve signal integrity in HDI PCBs?
-
Skip vias reduce the overall via count and length, which minimizes the discontinuities and reflections that can degrade signal quality. By connecting only the layers they need to, skip vias also reduce the capacitive and inductive loading on the signal path, resulting in cleaner, faster signals.
-
What are the challenges in manufacturing HDI PCBs with skip vias?
-
Manufacturing HDI PCBs with skip vias requires specialized equipment and processes, such as laser drilling, plasma etching, and advanced plating techniques. Ensuring proper alignment, plating uniformity, and via reliability can be challenging and requires strict process control and quality assurance measures.
-
How do I select the appropriate materials for my HDI PCB with skip vias?
-
When selecting materials for an HDI PCB with skip vias, consider factors such as dielectric constant, dissipation factor, thermal conductivity, and mechanical stability. Work with your PCB fabricator to choose materials that meet your application’s requirements for signal integrity, thermal management, and reliability.
-
What are the cost implications of using HDI PCBs with skip vias?
- HDI PCBs with skip vias typically cost more than traditional PCBs due to the advanced materials, specialized manufacturing processes, and increased complexity involved. However, the higher cost is often justified by the improved performance, reliability, and miniaturization benefits they offer. As HDI technologies become more widespread, costs are expected to decrease over time.
Conclusion
HDI PCBs with skip vias are a critical technology for meeting the growing demands of modern electronics. By offering increased wiring density, improved signal integrity, and enhanced thermal management, these advanced PCBs enable the creation of smaller, more complex devices with superior performance and reliability.
As designers and manufacturers continue to push the boundaries of what’s possible with HDI PCBs and skip vias, we can expect to see even more innovative applications and solutions in the future. From smartphones and medical devices to automotive electronics and beyond, HDI PCBs with skip vias will play a crucial role in shaping the electronics landscape for years to come.
Leave a Reply