Introduction to Buck Converters
A buck converter, also known as a step-down converter, is a type of DC-to-DC power converter that efficiently steps down voltage from its input to its output while stepping up current. Buck converters are widely used in power electronics applications to regulate voltage and provide a stable power supply to various electronic devices, such as smartphones, laptops, and embedded systems.
The basic working principle of a buck converter involves rapidly switching a series transistor on and off to control the connection of the input voltage to an inductor, which stores energy in its magnetic field. When the transistor is on, the input voltage is applied to the inductor, causing current to flow and energy to be stored. When the transistor is off, the inductor continues to provide current to the load through a diode or a second transistor, known as a synchronous rectifier.
By controlling the duty cycle of the switching transistor, the output voltage can be regulated to a desired level lower than the input voltage. The duty cycle is defined as the ratio of the on-time to the total switching period.
Key Components of a Buck Converter
The main components of a buck converter include:
- Power MOSFETs: Used as switching transistors to control the flow of current through the inductor.
- Inductor: Stores energy in its magnetic field and provides current to the load during the off-time of the switching transistor.
- Capacitor: Filters the output voltage ripple and provides a smooth, stable voltage to the load.
- Diode (optional): Acts as a freewheeling diode to provide a path for inductor current during the off-time of the switching transistor in non-synchronous buck converters.
- Control circuit: Generates the PWM (Pulse Width Modulation) signal to control the duty cycle of the switching transistor and regulate the output voltage.
Proper sizing of these components is crucial for achieving optimal performance, efficiency, and reliability of the buck converter.
Sizing the Inductor
The inductor is a key component in a buck converter, as it stores energy during the on-time of the switching transistor and releases it to the load during the off-time. The inductor value determines the ripple current, which in turn affects the output voltage ripple and the overall efficiency of the converter.
To size the inductor, the following parameters need to be considered:
- Input voltage range (Vin,min and Vin,max)
- Output voltage (Vout)
- Maximum output current (Iout,max)
- Switching frequency (fsw)
- Desired inductor ripple current (ΔIL)
The inductor value can be calculated using the following formula:
L = (Vout × (Vin,max – Vout)) / (fsw × ΔIL × Vin,max)
where:
– L is the inductor value in henries (H)
– Vout is the output voltage in volts (V)
– Vin,max is the maximum input voltage in volts (V)
– fsw is the switching frequency in hertz (Hz)
– ΔIL is the desired inductor ripple current in amperes (A)
The inductor ripple current is typically chosen as a percentage of the maximum output current, usually between 20% and 40%. A lower ripple current results in a larger inductor value, which reduces output voltage ripple and improves efficiency but increases the size and cost of the inductor.
Example: Inductor Sizing
Let’s consider an example where we need to size the inductor for a buck converter with the following specifications:
- Input voltage range: 12V to 24V
- Output voltage: 5V
- Maximum output current: 2A
- Switching frequency: 500kHz
- Desired inductor ripple current: 30% of maximum output current
Using the inductor sizing formula:
L = (5V × (24V – 5V)) / (500kHz × 0.3 × 2A × 24V) = 7.9µH
In this case, an 8µH inductor would be a suitable choice.
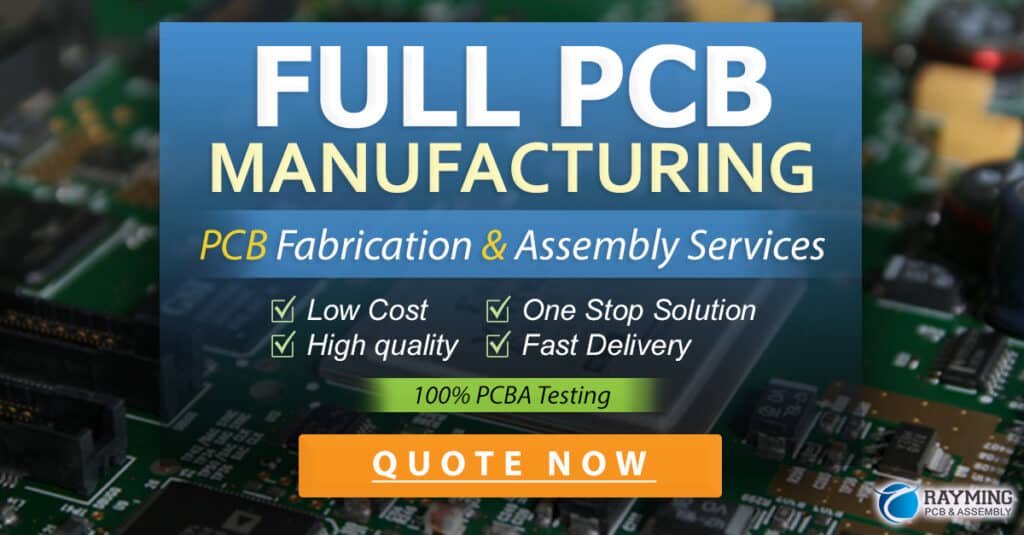
Sizing the Output Capacitor
The output capacitor in a buck converter serves two main purposes: filtering the output voltage ripple and providing transient response to load changes. The capacitor value determines the output voltage ripple and the converter’s ability to maintain a stable output voltage during load transients.
To size the output capacitor, the following parameters need to be considered:
- Output voltage (Vout)
- Maximum output current (Iout,max)
- Switching frequency (fsw)
- Desired output voltage ripple (ΔVout)
- Equivalent series resistance (ESR) of the capacitor
The capacitor value can be calculated using the following formula:
Cout = (Iout,max × (1 – Vout / Vin,min)) / (8 × fsw × ΔVout)
where:
– Cout is the output capacitor value in farads (F)
– Iout,max is the maximum output current in amperes (A)
– Vout is the output voltage in volts (V)
– Vin,min is the minimum input voltage in volts (V)
– fsw is the switching frequency in hertz (Hz)
– ΔVout is the desired output voltage ripple in volts (V)
The output voltage ripple is typically chosen as a small percentage of the output voltage, usually between 1% and 5%. A lower voltage ripple requires a larger capacitor value, which improves transient response but increases the size and cost of the capacitor.
In addition to the capacitance value, the ESR of the capacitor plays a crucial role in determining the output voltage ripple. The ESR-related ripple can be calculated using the following formula:
ΔVESR = Iout,max × ESR
where:
– ΔVESR is the ESR-related output voltage ripple in volts (V)
– Iout,max is the maximum output current in amperes (A)
– ESR is the equivalent series resistance of the capacitor in ohms (Ω)
To minimize the ESR-related ripple, low-esr capacitors such as ceramic or polymer capacitors are preferred.
Example: Output Capacitor Sizing
Let’s consider an example where we need to size the output capacitor for a buck converter with the following specifications:
- Input voltage range: 12V to 24V
- Output voltage: 5V
- Maximum output current: 2A
- Switching frequency: 500kHz
- Desired output voltage ripple: 2% of output voltage
- Capacitor ESR: 10mΩ
Using the capacitor sizing formula:
Cout = (2A × (1 – 5V / 12V)) / (8 × 500kHz × 0.02 × 5V) = 14.6µF
The ESR-related ripple:
ΔVESR = 2A × 10mΩ = 20mV
In this case, a 15µF low-ESR capacitor would be a suitable choice, and the total output voltage ripple would be the sum of the capacitance-related ripple and the ESR-related ripple.
Selecting the Power MOSFETs
Power MOSFETs are used as switching transistors in buck converters to control the flow of current through the inductor. The selection of the appropriate MOSFETs depends on several factors, including:
- Input voltage range (Vin,min and Vin,max)
- Maximum output current (Iout,max)
- Switching frequency (fsw)
- Desired efficiency
- Thermal considerations
When selecting MOSFETs, the following key parameters should be considered:
-
Breakdown voltage (VDSS): The maximum voltage that can be applied between the drain and source terminals of the MOSFET without causing avalanche breakdown. The breakdown voltage should be higher than the maximum input voltage with a safety margin.
-
Drain current rating (ID): The maximum continuous current that the MOSFET can conduct. The drain current rating should be higher than the maximum output current of the converter.
-
On-resistance (RDS(on)): The resistance between the drain and source terminals when the MOSFET is fully on. A lower on-resistance results in lower conduction losses and higher efficiency.
-
Gate charge (Qg): The amount of charge required to turn the MOSFET on and off. A lower gate charge results in faster switching and lower driving losses.
-
Thermal resistance (RθJA): The thermal resistance between the MOSFET’s junction and the ambient environment. A lower thermal resistance allows for better heat dissipation and higher power handling capability.
When selecting MOSFETs, it is essential to balance the trade-offs between these parameters to achieve the desired performance and efficiency.
Example: MOSFET Selection
Let’s consider an example where we need to select the power MOSFETs for a buck converter with the following specifications:
- Input voltage range: 12V to 24V
- Output voltage: 5V
- Maximum output current: 2A
- Switching frequency: 500kHz
For this application, we can choose MOSFETs with the following characteristics:
- Breakdown voltage: 40V (providing a safety margin over the maximum input voltage)
- Drain current rating: 5A (higher than the maximum output current)
- On-resistance: 10mΩ (low enough to minimize conduction losses)
- Gate charge: 10nC (low enough to minimize driving losses)
- Thermal resistance: 50°C/W (suitable for the power dissipation in this application)
Based on these requirements, suitable MOSFETs can be selected from various manufacturers, such as Infineon, ON Semiconductor, or Vishay.
Designing the Control Circuit
The control circuit in a buck converter generates the PWM signal to control the duty cycle of the switching transistor and regulate the output voltage. The main components of the control circuit include:
-
Error amplifier: Compares the output voltage with a reference voltage and generates an error signal proportional to the difference between the two.
-
Compensation network: Provides loop stability and determines the transient response of the converter. It typically consists of a combination of resistors and capacitors.
-
PWM comparator: Compares the error signal with a sawtooth or triangular waveform to generate the PWM signal.
-
Driver stage: Amplifies the PWM signal to drive the gate of the switching transistor.
When designing the control circuit, the following factors should be considered:
- Desired output voltage accuracy
- Transient response requirements
- Loop stability
- Noise immunity
There are several control IC manufacturers, such as Texas Instruments, Analog Devices, and Maxim Integrated, that offer dedicated buck converter control ICs with integrated error amplifiers, compensation networks, and PWM comparators. These ICs simplify the design process and provide optimized performance for various applications.
Example: Control Circuit Design
Let’s consider an example where we need to design the control circuit for a buck converter with the following specifications:
- Input voltage range: 12V to 24V
- Output voltage: 5V
- Maximum output current: 2A
- Switching frequency: 500kHz
- Desired output voltage accuracy: ±1%
For this application, we can use a dedicated buck converter control IC, such as the Texas Instruments TPS40170. This IC features:
- Integrated error amplifier and compensation network
- Programmable switching frequency up to 1.5MHz
- Programmable soft-start
- Cycle-by-cycle current limiting
- Thermal shutdown protection
The TPS40170 can be configured for the desired output voltage and switching frequency using external resistors and capacitors, as per the manufacturer’s datasheet.
Efficiency and Power Losses
Efficiency is a critical consideration in buck converter design, as it directly impacts the power dissipation, thermal management, and overall system performance. The main sources of power loss in a buck converter include:
-
Conduction losses: Caused by the on-resistance of the MOSFETs and the DC resistance of the inductor.
-
Switching losses: Caused by the finite switching time of the MOSFETs and the charge/discharge of the parasitic capacitances.
-
Diode losses: Caused by the forward voltage drop and the reverse recovery of the freewheeling diode (if used).
-
Control circuit losses: Caused by the quiescent current and the dynamic power consumption of the control IC and driver stage.
To maximize efficiency, the following strategies can be employed:
- Select MOSFETs with low on-resistance and gate charge.
- Use low-DC-resistance inductors.
- Increase the switching frequency to reduce the size of the passive components, but balance this against the increased switching losses.
- Use synchronous rectification (replacing the freewheeling diode with a second MOSFET) to reduce conduction losses.
- Optimize the control circuit for low quiescent current and efficient driving of the MOSFETs.
The overall efficiency of a buck converter can be calculated using the following formula:
η = (Pout / Pin) × 100%
where:
– η is the efficiency in percent (%)
– Pout is the output power in watts (W)
– Pin is the input power in watts (W)
Example: Efficiency Calculation
Let’s consider an example where we have a buck converter with the following measured parameters:
- Input voltage: 18V
- Output voltage: 5V
- Output current: 1.5A
- Input current: 0.5A
The output power can be calculated as:
Pout = 5V × 1.5A = 7.5W
The input power can be calculated as:
Pin = 18V × 0.5A = 9W
The efficiency of the converter is:
η = (7.5W / 9W) × 100% = 83.3%
In this case, the buck converter has an efficiency of 83.3%. By optimizing the component selection and design, the efficiency can be further improved.
Frequently Asked Questions (FAQ)
- What is the main advantage of using a buck converter over a linear regulator?
A buck converter offers higher efficiency compared to a linear regulator, especially when the difference between the input and output voltages is large. Linear regulators dissipate the excess power as heat, resulting in lower efficiency and higher thermal stress.
- Can a buck converter be used to step up voltage?
No, a buck converter is designed to step down voltage only. To step up voltage, a boost converter or a buck-boost converter should be used.
- What is the purpose of the inductor in a buck converter?
The inductor in a buck converter serves two main purposes: it stores energy during the on-time of the switching transistor and releases it to the load during the off-time, and it filters the output current, reducing the current ripple.
- What is the difference between continuous conduction mode (CCM) and discontinuous conduction mode (DCM) in a buck converter?
In CCM, the inductor current never drops to zero during the switching cycle, resulting in lower peak currents and lower output voltage ripple. In DCM, the inductor current drops to zero for a portion of the switching cycle, resulting in higher peak currents and higher output voltage ripple. CCM is preferred for higher power applications, while DCM is often used in low-power applications to simplify the control scheme.
- What is the role of the output capacitor in a buck converter?
The output capacitor in a buck converter serves two main purposes: it filters the output voltage ripple, providing a smooth, stable voltage to the load, and it provides transient response to load changes, helping to maintain a stable output voltage during sudden changes in load current.
Conclusion
Designing a buck converter involves careful selection and sizing of the key components, including the inductor, output capacitor, power MOSFETs, and control circuit. By understanding the principles behind component sizing and the trade
Leave a Reply