Introduction
Bob Martin, a renowned software engineer and author, has recently embarked on a new project that showcases the versatility and power of Arduino boards. In this article, we will explore how Bob Martin successfully transitioned from a prototype to a production-ready device using an Arduino board as the core component.
What is an Arduino Board?
An Arduino board is a small, single-board microcontroller that is designed to be easy to use and program. It consists of a processor, memory, and input/output pins that allow it to interact with various sensors, actuators, and other electronic components. Arduino boards are popular among hobbyists, students, and professionals alike due to their affordability, flexibility, and extensive community support.
Feature | Description |
---|---|
Processor | ATmega328P (8-bit AVR microcontroller) |
Clock Speed | 16 MHz |
Digital I/O Pins | 14 (6 provide PWM output) |
Analog Input Pins | 6 |
Flash Memory | 32 KB |
SRAM | 2 KB |
EEPROM | 1 KB |
Operating Voltage | 5V |
Table 1: Key specifications of the Arduino Uno board, one of the most popular Arduino boards.
Bob Martin’s Prototype
Ideation and Planning
Bob Martin’s journey began with a simple idea: to create a device that could monitor and control the temperature and humidity levels in his home office. He wanted a solution that was not only effective but also easy to build and maintain. After researching various options, Bob decided to use an Arduino board as the foundation for his project.
Hardware Selection
To bring his idea to life, Bob needed to select the appropriate hardware components. He chose the following:
- Arduino Uno board
- DHT11 temperature and humidity sensor
- LCD display (16×2 characters)
- Potentiometer (for adjusting LCD contrast)
- Breadboard and jumper wires
Wiring and Assembly
With the hardware components in hand, Bob began the process of wiring and assembling his prototype. He followed these steps:
- Connect the DHT11 sensor to the Arduino Uno board:
- VCC pin to 5V
- GND pin to GND
- DATA pin to digital pin 2
- Connect the LCD display to the Arduino Uno board:
- RS pin to digital pin 12
- EN pin to digital pin 11
- D4 pin to digital pin 5
- D5 pin to digital pin 4
- D6 pin to digital pin 3
- D7 pin to digital pin 2
- VCC pin to 5V
- GND pin to GND
- Connect the potentiometer to the LCD display:
- Wiper pin to LCD VO pin
- Other pins to GND and 5V
Software Development
With the hardware assembled, Bob turned his attention to software development. He used the Arduino IDE to write the code that would read data from the DHT11 sensor, display it on the LCD, and trigger actions based on predefined thresholds.
#include <DHT.h>
#include <LiquidCrystal.h>
#define DHTPIN 2
#define DHTTYPE DHT11
DHT dht(DHTPIN, DHTTYPE);
LiquidCrystal lcd(12, 11, 5, 4, 3, 2);
void setup() {
lcd.begin(16, 2);
dht.begin();
}
void loop() {
float temperature = dht.readTemperature();
float humidity = dht.readHumidity();
lcd.clear();
lcd.setCursor(0, 0);
lcd.print("Temp: ");
lcd.print(temperature);
lcd.print(" C");
lcd.setCursor(0, 1);
lcd.print("Humidity: ");
lcd.print(humidity);
lcd.print("%");
delay(2000);
}
Code snippet: Reading data from the DHT11 sensor and displaying it on the LCD.
Testing and Refinement
With the prototype assembled and programmed, Bob began testing its functionality. He observed the temperature and humidity readings on the LCD display and compared them to a commercial thermometer and hygrometer to ensure accuracy. Bob also experimented with different threshold values to trigger actions, such as turning on a fan or humidifier when the temperature or humidity exceeded certain levels.
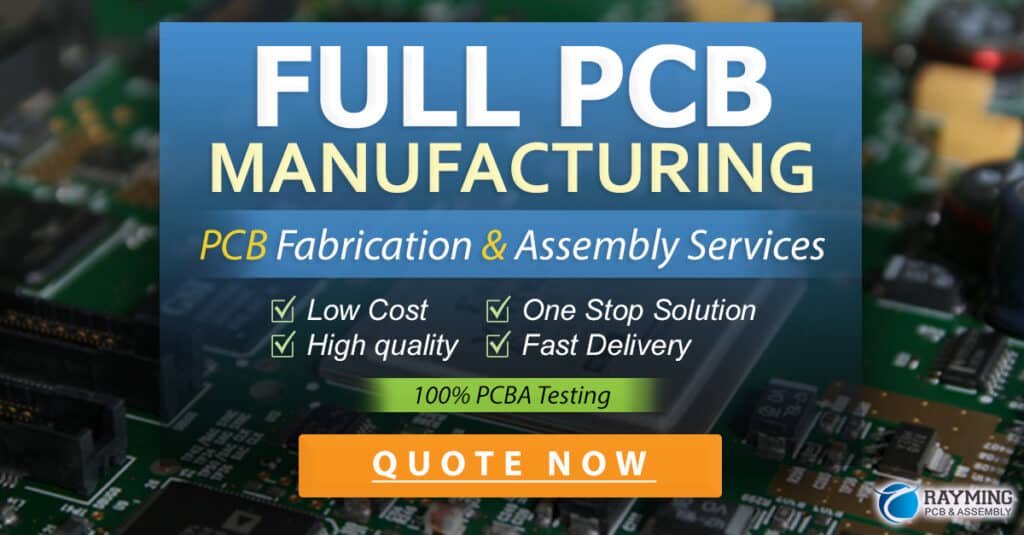
Transitioning to Production
PCB Design
Having validated the functionality of his prototype, Bob decided to transition his project to a production-ready device. The first step was to design a custom PCB (Printed Circuit Board) that would replace the breadboard and jumper wires, making the device more compact and reliable.
Bob used a PCB design software to create a schematic and layout for his board. He carefully positioned the components, routed the traces, and added mounting holes for the Arduino Uno board, DHT11 sensor, and LCD display.
Component Selection
To ensure the longevity and reliability of his production device, Bob selected high-quality components that were rated for the expected operating conditions. He chose:
- Industrial-grade DHT11 sensor with improved accuracy and stability
- High-contrast LCD display with a wide viewing angle
- Precision potentiometer for fine-tuning the LCD contrast
- Durable connectors and headers for secure connections
Manufacturing and Assembly
With the PCB design finalized and components selected, Bob sent his files to a PCB manufacturing service. Upon receiving the fabricated boards, he carefully soldered the components in place, following best practices for electronic assembly.
Enclosure Design
To protect the electronics and provide a professional appearance, Bob designed a custom enclosure for his device. He used a 3D modeling software to create a two-part enclosure that would snap together, with openings for the LCD display, sensor, and power connections. Bob 3D printed the enclosure using a durable and heat-resistant filament.
Final Testing and Calibration
Before considering his production device complete, Bob conducted thorough testing and calibration. He:
- Verified the accuracy of the temperature and humidity readings against calibrated instruments
- Tested the device under various environmental conditions to ensure reliable operation
- Fine-tuned the threshold values for triggering actions based on user preferences
- Conducted stress tests to identify and address any potential weaknesses or failure points
Conclusion
Bob Martin’s journey from prototype to production demonstrates the power and versatility of Arduino boards in bringing ideas to life. By leveraging the Arduino ecosystem and following a structured development process, Bob was able to create a reliable and effective device for monitoring and controlling the temperature and humidity levels in his home office.
This project serves as an inspiration for anyone looking to embark on their own Arduino-based endeavors, whether for personal use or commercial applications. With the right tools, knowledge, and perseverance, the possibilities are endless.
Frequently Asked Questions (FAQ)
-
Q: What is the difference between an Arduino board and a microcontroller?
A: An Arduino board is a development board that incorporates a microcontroller, along with other components such as voltage regulators, crystal oscillators, and USB interfaces. A microcontroller, on the other hand, is the central processing unit (CPU) of the Arduino board, responsible for executing the programmed instructions. -
Q: Can I use other sensors with the Arduino board in this project?
A: Yes, the Arduino board is compatible with a wide range of sensors. You can easily swap out the DHT11 sensor with other temperature and humidity sensors, such as the DHT22 or BME280, by making minor modifications to the wiring and code. -
Q: How can I extend the functionality of this project?
A: There are numerous ways to extend the functionality of this project. Some ideas include adding a real-time clock module to log data over time, incorporating wireless connectivity (e.g., Wi-Fi or Bluetooth) to remotely monitor and control the device, or integrating additional sensors to measure other environmental parameters such as air quality or light levels. -
Q: Can I power the Arduino board using batteries?
A: Yes, you can power the Arduino board using batteries. The Arduino Uno board, for example, can be powered using a 9V battery connected to the VIN and GND pins. However, keep in mind that the voltage regulator on the board will drop the voltage to 5V, which may result in shorter battery life compared to using a 5V power source directly. -
Q: What are some best practices for designing and manufacturing a custom PCB?
A: When designing and manufacturing a custom PCB, consider the following best practices: - Use a reliable PCB design software and follow the manufacturer’s design guidelines
- Choose appropriate component footprints and pad sizes for easy soldering
- Ensure proper trace width and spacing to minimize signal interference and maintain signal integrity
- Include mounting holes and connectors for secure and stable assembly
- Perform thorough testing and inspection of the fabricated boards before assembling the components
By following these best practices and continually refining your skills, you can create high-quality, production-ready devices using Arduino boards as the foundation.
Leave a Reply