Introduction
In the world of high-speed electronic design, the proper configuration of the board layer stackup is crucial for ensuring optimal signal integrity, power delivery, and overall system performance. The board layer stackup refers to the arrangement of conductive layers, dielectric materials, and planes within a printed circuit board (PCB). This article will explore the key considerations and best practices for designing an effective board layer stackup for high-speed applications.
The Importance of Board Layer Stackup in High-Speed Design
Signal Integrity
One of the primary reasons for carefully designing the board layer stackup is to maintain signal integrity. In high-speed systems, signals are susceptible to various issues such as crosstalk, reflections, and electromagnetic interference (EMI). By strategically placing signal layers, ground planes, and power planes, designers can minimize these effects and ensure clean, undistorted signal propagation.
Power Delivery
Another critical aspect of board layer stackup design is power delivery. High-speed devices often require a stable and low-impedance power distribution network (PDN) to function correctly. The placement of power and ground planes, as well as the use of appropriate decoupling capacitors, helps to minimize voltage fluctuations and ensure a reliable power supply to the components.
Manufacturability and Cost
The choice of board layer stackup also impacts the manufacturability and cost of the PCB. Factors such as the number of layers, the thickness of the dielectric materials, and the copper weight of the conductive layers all contribute to the complexity and expense of the manufacturing process. Striking a balance between performance and cost is essential when deciding on the board layer stackup.
Key Elements of a Board Layer Stackup
Conductive Layers
Conductive layers in a PCB are typically made of copper and serve various purposes, such as carrying signals, providing power and ground, and acting as reference planes. The thickness of the copper, known as the copper weight, is usually specified in ounces per square foot (oz/ft²). Common copper weights include 0.5 oz/ft², 1 oz/ft², and 2 oz/ft². Thicker copper layers are often used for power and ground planes to minimize resistance and improve current-carrying capacity.
Dielectric Materials
Dielectric materials are the insulating layers that separate the conductive layers in a PCB. The choice of dielectric material significantly influences the electrical properties of the board, such as the dielectric constant (Dk) and the dissipation factor (Df). Common dielectric materials include FR-4, Rogers, and Isola. Each material has its own characteristics and is suitable for different applications based on factors such as frequency, loss, and cost.
Planes
Planes are large, continuous copper areas that serve specific purposes in a PCB. The two most common types of planes are power planes and ground planes. Power planes distribute the supply voltage to the components on the board, while ground planes provide a low-impedance return path for the signals. The placement and spacing of these planes are critical for maintaining signal integrity and minimizing EMI.
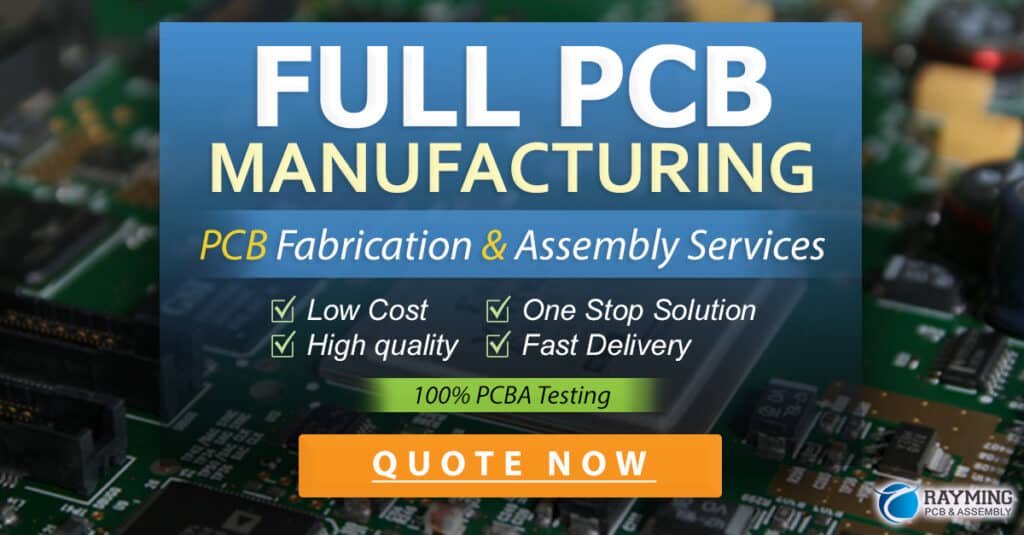
Designing an Effective Board Layer Stackup
Determining the Number of Layers
The first step in designing a board layer stackup is to determine the required number of layers. This decision is based on factors such as the complexity of the design, the number of components, and the routing requirements. High-speed designs often benefit from having more layers to accommodate dedicated signal, power, and ground planes. However, increasing the number of layers also increases the manufacturing cost and complexity.
Choosing the Dielectric Materials
The selection of dielectric materials is crucial for achieving the desired electrical performance. For high-speed applications, materials with low dielectric constant and dissipation factor are preferred to minimize signal loss and distortion. The thickness of the dielectric layers also plays a role in determining the impedance of the traces and the overall board thickness.
Placing the Signal Layers
Signal layers should be placed strategically to minimize crosstalk and interference. In general, it is recommended to route high-speed signals on inner layers, sandwiched between ground planes. This arrangement provides shielding and helps to control the impedance of the traces. Differential pairs should be routed together on the same layer to maintain signal integrity.
Allocating Power and Ground Planes
Power and ground planes should be placed close to the signal layers they serve to minimize inductance and provide a low-impedance return path. It is common practice to have dedicated power and ground planes for each supply voltage in the design. The spacing between the power and ground planes influences the capacitance and the effectiveness of the decoupling capacitors.
Incorporating Shielding and Isolation
In some cases, it may be necessary to incorporate shielding layers or isolation techniques in the board layer stackup. Shielding layers, such as continuous ground planes, help to reduce EMI and crosstalk between different sections of the board. Isolation techniques, such as split planes or moats, can be used to separate sensitive analog and digital circuits.
Best Practices for Board Layer Stackup Design
Symmetry and Balance
Maintaining symmetry and balance in the board layer stackup is essential for minimizing warpage and ensuring consistent electrical properties. This means having an equal number of layers on either side of the board centerline and using similar materials and thicknesses for the dielectric layers.
Consistent Dielectric Thickness
Keeping the dielectric thickness consistent throughout the stackup helps to maintain controlled impedance and reduce signal reflections. Variations in dielectric thickness can lead to impedance discontinuities and degrade signal quality.
Minimizing Layer Transitions
When routing signals, it is best to minimize the number of layer transitions. Each time a signal changes layers, it encounters a discontinuity that can cause reflections and degrade signal integrity. If layer transitions are unavoidable, they should be made through vias with appropriate size and placement to minimize their impact.
Proper Via Design
Vias are an essential component of the board layer stackup, providing electrical connections between layers. The size, placement, and type of vias can significantly affect signal integrity and power delivery. For high-speed signals, smaller vias with controlled impedance are preferred to minimize discontinuities. Blind and buried vias can be used to improve routing density and reduce layer transitions.
Decoupling capacitor placement
Decoupling capacitors play a critical role in maintaining power integrity and reducing noise in high-speed designs. The placement of these capacitors in relation to the power and ground planes is crucial for their effectiveness. Ideally, decoupling capacitors should be placed as close as possible to the devices they serve, with short and low-inductance connections to the planes.
Example Board Layer Stackups
To illustrate the concepts discussed in this article, let’s look at a few example board layer stackups for high-speed designs.
4-Layer Stackup
Layer | Material | Thickness | Purpose |
---|---|---|---|
Top | Copper | 1 oz/ft² | Signal |
2 | FR-4 | 0.2 mm | Core |
3 | Copper | 1 oz/ft² | Ground |
Bottom | Copper | 1 oz/ft² | Signal |
This simple 4-layer stackup is suitable for low-complexity designs with moderate speed requirements. The signal layers are on the top and bottom, while the inner layer serves as a ground plane. The FR-4 core provides the necessary dielectric separation between the layers.
8-Layer Stackup
Layer | Material | Thickness | Purpose |
---|---|---|---|
Top | Copper | 0.5 oz/ft² | Signal |
2 | FR-4 | 0.2 mm | Prepreg |
3 | Copper | 1 oz/ft² | Ground |
4 | FR-4 | 0.2 mm | Core |
5 | Copper | 1 oz/ft² | Power |
6 | FR-4 | 0.2 mm | Core |
7 | Copper | 1 oz/ft² | Ground |
Bottom | Copper | 0.5 oz/ft² | Signal |
This 8-layer stackup provides more flexibility and better signal integrity for high-speed designs. The signal layers are shielded by dedicated ground planes, and there is a separate power plane for improved power delivery. The use of thinner dielectrics and lower copper weights helps to control impedance and reduce overall board thickness.
12-Layer Stackup
Layer | Material | Thickness | Purpose |
---|---|---|---|
Top | Copper | 0.5 oz/ft² | Signal |
2 | Rogers | 0.2 mm | Prepreg |
3 | Copper | 1 oz/ft² | Ground |
4 | Rogers | 0.2 mm | Core |
5 | Copper | 1 oz/ft² | Signal |
6 | Rogers | 0.2 mm | Core |
7 | Copper | 1 oz/ft² | Power |
8 | Rogers | 0.2 mm | Core |
9 | Copper | 1 oz/ft² | Signal |
10 | Rogers | 0.2 mm | Core |
11 | Copper | 1 oz/ft² | Ground |
Bottom | Copper | 0.5 oz/ft² | Signal |
This advanced 12-layer stackup is suitable for high-performance, high-speed applications. The use of Rogers material with a lower dielectric constant and dissipation factor helps to minimize signal loss and distortion. The multiple signal layers, separated by ground and power planes, provide ample routing space and improved signal integrity. The symmetrical arrangement of layers helps to minimize warpage and ensure consistent performance.
Frequently Asked Questions (FAQ)
- What is the impact of increasing the number of layers in a board layer stackup?
-
Increasing the number of layers in a board layer stackup provides more routing space, allows for dedicated power and ground planes, and improves signal integrity. However, it also increases the manufacturing cost and complexity of the PCB.
-
How does the choice of dielectric material affect the performance of a high-speed design?
-
The choice of dielectric material significantly influences the electrical properties of the PCB, such as the dielectric constant and dissipation factor. For high-speed applications, materials with low dielectric constant and dissipation factor are preferred to minimize signal loss and distortion.
-
What is the purpose of having dedicated power and ground planes in a board layer stackup?
-
Dedicated power and ground planes serve to distribute the supply voltage to the components on the board and provide a low-impedance return path for the signals. They help to maintain power integrity, reduce noise, and improve overall system performance.
-
How can you minimize crosstalk and interference between signal layers in a board layer stackup?
-
To minimize crosstalk and interference between signal layers, it is recommended to route high-speed signals on inner layers, sandwiched between ground planes. This arrangement provides shielding and helps to control the impedance of the traces. Additionally, differential pairs should be routed together on the same layer to maintain signal integrity.
-
Why is it important to maintain symmetry and balance in a board layer stackup?
- Maintaining symmetry and balance in a board layer stackup is essential for minimizing warpage and ensuring consistent electrical properties. This means having an equal number of layers on either side of the board centerline and using similar materials and thicknesses for the dielectric layers. A symmetrical and balanced stackup helps to reduce mechanical stress and improves the reliability of the PCB.
Conclusion
Designing an effective board layer stackup is a critical aspect of high-speed electronic design. By carefully considering factors such as the number of layers, dielectric materials, signal layer placement, power and ground plane allocation, and shielding techniques, designers can optimize signal integrity, power delivery, and overall system performance. Following best practices, such as maintaining symmetry and balance, consistent dielectric thickness, minimizing layer transitions, proper via design, and strategic decoupling capacitor placement, further enhances the reliability and manufacturability of the PCB. As the demand for high-speed electronics continues to grow, a well-designed board layer stackup will remain a fundamental element in ensuring the success of these complex systems.
Leave a Reply