Introduction to Electroless Nickel and Immersion Gold (ENIG)
Electroless nickel and immersion gold (ENIG) is a surface finish commonly used in printed circuit board (PCB) manufacturing. This finish consists of a thin layer of gold over a nickel-phosphorus alloy, which is deposited on the copper surface of the PCB using an electroless plating process. ENIG provides excellent solderability, corrosion resistance, and durability, making it a popular choice for high-reliability applications.
Advantages of ENIG
- Excellent solderability
- Good corrosion resistance
- Flat and smooth surface finish
- Suitable for fine-pitch components
- Compatible with various soldering processes
- Long shelf life
Disadvantages of ENIG
- Higher cost compared to other surface finishes
- Potential for black pad formation
- Requires strict process control
The Electroless Nickel Plating Process
Electroless nickel plating is a chemical process that deposits a nickel-phosphorus alloy on the copper surface of the PCB without the use of an external electrical current. The process involves several steps, including:
- Cleaning: The PCB is cleaned to remove any contaminants or oxides from the copper surface.
- Activation: The copper surface is activated using a palladium-based solution to promote the adhesion of the nickel-phosphorus alloy.
- Electroless nickel plating: The PCB is immersed in an electroless nickel plating bath containing nickel ions, a reducing agent (typically sodium hypophosphite), and other additives. The reducing agent reacts with the nickel ions, causing them to deposit on the activated copper surface.
- Rinsing: The PCB is rinsed with deionized water to remove any residual plating solution.
Factors Affecting Electroless Nickel Plating
- Bath composition and temperature
- pH and stability of the plating solution
- Plating time and deposition rate
- Agitation and filtration of the plating solution
- Substrate surface preparation
The Immersion Gold Plating Process
After the electroless nickel plating, a thin layer of gold is deposited on the nickel surface using an immersion gold plating process. This process involves the following steps:
- Cleaning: The nickel-plated PCB is cleaned to remove any contaminants or oxides.
- Immersion gold plating: The PCB is immersed in an immersion gold plating bath containing gold ions and a complexing agent. The gold ions displace some of the nickel atoms on the surface, resulting in a thin layer of pure gold.
- Rinsing: The PCB is rinsed with deionized water to remove any residual plating solution.
Factors Affecting Immersion Gold Plating
- Bath composition and temperature
- pH and stability of the plating solution
- Plating time and gold thickness
- Agitation and filtration of the plating solution
- Nickel surface preparation
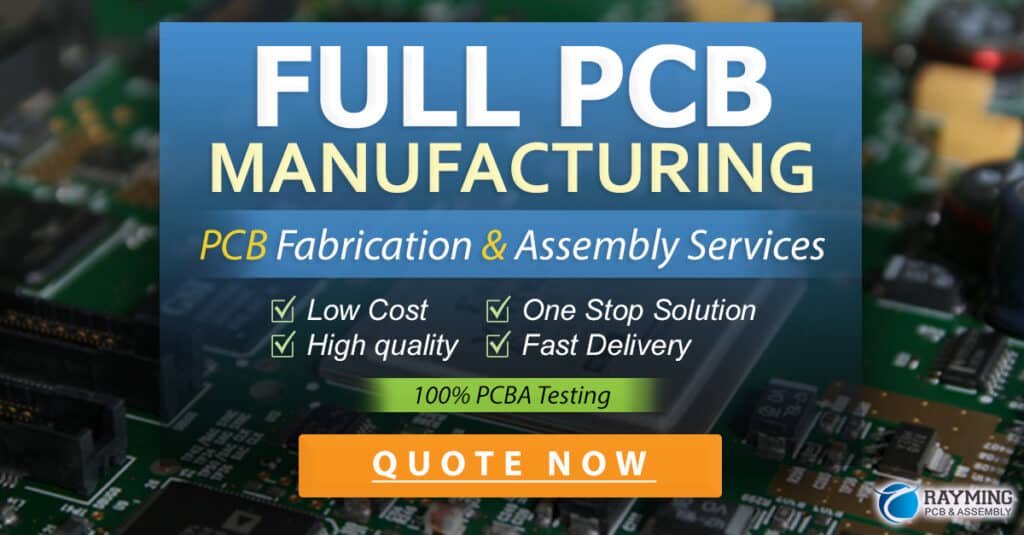
Black Pad Formation in ENIG
Black pad is a defect that can occur during the ENIG process, characterized by the formation of a thin, brittle layer of nickel oxide between the electroless nickel and immersion gold layers. This defect can lead to poor solderability, reduced joint strength, and potential joint failure.
Causes of Black Pad Formation
- Excessive immersion gold plating time
- High pH or contamination in the immersion gold bath
- Inadequate rinsing between the electroless nickel and immersion gold steps
- Exposure of the nickel surface to air before immersion gold plating
- Insufficient electroless nickel thickness or phosphorus content
Preventing Black Pad Formation
- Optimize the immersion gold plating time and bath parameters
- Maintain proper pH and cleanliness of the immersion gold bath
- Ensure adequate rinsing between the electroless nickel and immersion gold steps
- Minimize exposure of the nickel surface to air before immersion gold plating
- Control the electroless nickel thickness and phosphorus content
ENIG Process Control and Quality Assurance
To ensure consistent and reliable ENIG performance, it is essential to implement strict process control and quality assurance measures. Some key aspects include:
- Bath monitoring and maintenance: Regular monitoring and adjustment of bath composition, pH, temperature, and contaminant levels.
- Thickness and composition control: Measuring and controlling the thickness and composition of the electroless nickel and immersion gold layers using techniques such as X-ray fluorescence (XRF) or cross-sectional analysis.
- Visual inspection: Visually inspecting the ENIG surface for defects such as black pad, blistering, or discoloration.
- Solderability testing: Conducting solderability tests, such as wetting balance or surface insulation resistance (SIR) tests, to assess the ENIG performance.
- Documentation and traceability: Maintaining detailed records of process parameters, bath maintenance, and quality control results for traceability and continuous improvement.
Parameter | Recommended Range |
---|---|
Electroless Nickel Thickness | 3-6 μm |
Phosphorus Content in Electroless Nickel | 7-11 wt% |
Immersion Gold Thickness | 0.05-0.15 μm |
Electroless Nickel Bath Temperature | 80-90°C |
Electroless Nickel Bath pH | 4.6-5.2 |
Immersion Gold Bath Temperature | 70-85°C |
Immersion Gold Bath pH | 5.0-6.0 |
Troubleshooting ENIG Issues
Despite proper process control, issues may still arise during the ENIG process. Some common problems and their potential solutions include:
- Poor solderability: Check the immersion gold thickness, bath parameters, and storage conditions. Ensure proper cleaning and activation of the nickel surface before immersion gold plating.
- Black pad formation: Optimize the immersion gold plating time and bath parameters, ensure adequate rinsing, and minimize exposure of the nickel surface to air. Control the electroless nickel thickness and phosphorus content.
- Blistering or delamination: Check the electroless nickel bath composition and operating conditions, ensure proper substrate cleaning and activation, and optimize the plating time and deposition rate.
- Inconsistent thickness or composition: Regularly monitor and adjust bath parameters, maintain proper agitation and filtration, and calibrate thickness and composition measurement equipment.
- Contamination: Implement strict bath maintenance and filtration procedures, use high-purity chemicals and deionized water, and ensure proper equipment cleaning and maintenance.
Alternative Surface Finishes to ENIG
While ENIG is a widely used surface finish, there are several alternatives available for different applications and requirements:
- Immersion tin (ISn): A thin layer of pure tin deposited on the copper surface, providing good solderability and lower cost compared to ENIG.
- Organic solderability preservative (OSP): A thin, organic coating applied to the copper surface to prevent oxidation and maintain solderability. OSP is a low-cost option but has a limited shelf life.
- Electroless nickel electroless palladium immersion gold (ENEPIG): A surface finish consisting of electroless nickel, electroless palladium, and immersion gold layers. ENEPIG offers improved wire bonding performance and compatibility with both solder and gold wire bonding processes.
- Direct immersion gold (DIG): A thin layer of gold directly deposited on the copper surface, eliminating the need for the electroless nickel layer. DIG provides good solderability and is suitable for high-frequency applications.
- Hot air solder leveling (HASL): A process in which the PCB is dipped in molten solder and then blown with hot air to remove excess solder and create a flat surface. HASL is a low-cost option but may not be suitable for fine-pitch components.
Conclusion
Electroless nickel and immersion gold (ENIG) is a popular surface finish in PCB manufacturing, offering excellent solderability, corrosion resistance, and durability. However, the ENIG process requires strict process control and quality assurance measures to prevent defects such as black pad formation. By understanding the electroless nickel and immersion gold plating processes, implementing proper process control, and troubleshooting issues effectively, manufacturers can achieve consistent and reliable ENIG performance. Alternative surface finishes are also available for specific applications and requirements.
Frequently Asked Questions (FAQ)
-
What is the purpose of the electroless nickel layer in ENIG?
The electroless nickel layer serves as a barrier between the copper substrate and the immersion gold layer, preventing the diffusion of copper into the gold layer and improving the corrosion resistance and durability of the surface finish. -
How does black pad formation affect the solderability of ENIG?
Black pad formation results in a thin, brittle layer of nickel oxide between the electroless nickel and immersion gold layers, which can lead to poor solderability, reduced joint strength, and potential joint failure. -
What are the main factors affecting the formation of black pad in ENIG?
The main factors affecting black pad formation include excessive immersion gold plating time, high pH or contamination in the immersion gold bath, inadequate rinsing between the electroless nickel and immersion gold steps, exposure of the nickel surface to air before immersion gold plating, and insufficient electroless nickel thickness or phosphorus content. -
How can manufacturers prevent black pad formation in ENIG?
To prevent black pad formation, manufacturers should optimize the immersion gold plating time and bath parameters, maintain proper pH and cleanliness of the immersion gold bath, ensure adequate rinsing between the electroless nickel and immersion gold steps, minimize exposure of the nickel surface to air before immersion gold plating, and control the electroless nickel thickness and phosphorus content. -
What are some alternative surface finishes to ENIG?
Some alternative surface finishes to ENIG include immersion tin (ISn), organic solderability preservative (OSP), electroless nickel electroless palladium immersion gold (ENEPIG), direct immersion gold (DIG), and hot air solder leveling (HASL). Each alternative has its own advantages and disadvantages, and the choice depends on the specific application and requirements.
Leave a Reply