Introduction to PCB Interconnects
Printed circuit board (PCB) interconnects are a critical aspect of modern electronics design and manufacturing. PCBs form the foundation of almost all electronic devices, from smartphones and laptops to industrial controls and aerospace systems. As electronics continue to advance in complexity and functionality, PCBs often need to be split into multiple boards that are connected together. This is where PCB interconnect solutions come into play.
PCB interconnects allow multiple PCB boards to be electrically and mechanically connected in a reliable and efficient manner. There are various types of interconnects available, each with their own advantages and best practices for implementation. Choosing the right interconnect solution for a specific application depends on factors such as:
- Number of connections required
- Space constraints
- Operating environment (temperature, humidity, vibration, etc.)
- Power and signal integrity requirements
- Ease of assembly and disassembly
- Cost
In this article, we will dive deep into the world of PCB interconnects, with a focus on multi-board design best practices. We’ll cover the different types of interconnects available, their key characteristics, and guidelines for selecting and implementing them effectively. Whether you’re a seasoned electronics engineer or just starting out, this article will provide valuable insights to help you create robust and reliable multi-board PCB designs.
Types of PCB Interconnects
There are several types of PCB interconnects available, each with their own strengths and weaknesses. Here are some of the most common types:
Board-to-Board Connectors
Board-to-board (B2B) connectors are used to directly connect two PCBs together. They come in various form factors and pitches to suit different applications. Some popular types of B2B connectors include:
-
Pin headers and sockets: These are simple and cost-effective solutions for low-density connections. The male pin header is soldered onto one board, while the female socket is soldered onto the mating board.
-
Edge connectors: These connectors have contacts on one or both sides of a PCB edge. The mating board has a slot that the edge connector plugs into. Edge connectors are commonly used in computer peripherals and expansion cards.
-
Mezzanine connectors: These are high-density connectors that allow boards to be stacked vertically. They are often used in space-constrained applications where a compact form factor is required.
Here’s a table comparing the key characteristics of these B2B connector types:
Connector Type | Density | Pitch | Stacking Height | Typical Applications |
---|---|---|---|---|
Pin Headers | Low | 2.54mm, 2.00mm | 5-10mm | Prototyping, low-density connections |
Edge Connectors | Medium | 1.27mm, 1.00mm | N/A | Computer peripherals, expansion cards |
Mezzanine | High | 0.5mm, 0.4mm | 5-20mm | Space-constrained, high-density applications |
Cable Assemblies
Cable assemblies are used to connect PCBs that are physically separated from each other. They offer flexibility in positioning the boards and can span longer distances than B2B connectors. Some common types of cable assemblies include:
-
Ribbon cables: These are flat cables with multiple conductors arranged side-by-side. They are often used for parallel data transmission and are terminated with IDC (insulation displacement contact) connectors.
-
Coaxial cables: These cables have a central conductor surrounded by an insulating layer and a metallic shield. They are used for high-frequency signals and provide good noise immunity.
-
Flexible flat cables (FFC): These are thin, flexible cables with flat conductors laminated between insulating layers. They are commonly used in applications where a low profile and flexibility are required, such as connecting displays or cameras to a main board.
Here’s a table summarizing the characteristics of these cable assembly types:
Cable Type | Conductor Arrangement | Insulation | Typical Applications |
---|---|---|---|
Ribbon Cable | Parallel | PVC | Parallel data transmission, IDC connectors |
Coaxial Cable | Coaxial | Dielectric | High-frequency signals, noise immunity |
FFC | Flat, parallel | Polyester, PET | Low-profile, flexible connections |
PCB-Mounted Connectors
PCB-mounted connectors are soldered directly onto the PCB and provide a means to connect external devices or cables. They come in various types, such as:
-
USB connectors: These are used to interface with USB devices and come in different form factors like Type-A, Type-B, and Type-C.
-
HDMI connectors: These are used for high-definition video and audio transmission and are commonly found in consumer electronics.
-
Modular jacks (RJ45): These are used for Ethernet connectivity and are often seen in networking equipment.
Here’s a table listing some common PCB-mounted connectors and their applications:
Connector Type | Description | Typical Applications |
---|---|---|
USB | Universal Serial Bus | Computer peripherals, mobile devices |
HDMI | High-Definition Multimedia Interface | HD video and audio transmission |
RJ45 | Registered Jack 45 (Ethernet) | Networking equipment, IP cameras |
Multi-Board PCB Design Best Practices
When designing multi-board PCB systems, there are several best practices to follow to ensure reliability, performance, and manufacturability. Let’s go through some of these guidelines:
Planning and Partitioning
-
Functional partitioning: Divide the system into logical functional blocks and assign each block to a separate PCB. This modular approach makes the design more manageable and allows for easier debugging and upgrades.
-
Physical partitioning: Consider the physical size and shape constraints of the enclosure when deciding how to partition the boards. Aim for a compact and efficient layout while leaving enough room for connectors and cable routing.
-
Signal integrity: Analyze the signal integrity requirements of each functional block and group high-speed or sensitive signals together on the same board to minimize cross-board signal routing.
Board Interconnect Selection
-
Connector selection: Choose connectors that are rated for the required number of mating cycles, operating environment, and signal integrity. Consider the connector’s pitch, height, and orientation to ensure compatibility with the PCB layout and enclosure.
-
Cable selection: Select cables based on the signal characteristics, length, and flexibility requirements. Use shielded cables for high-frequency or noise-sensitive signals, and choose the appropriate gauge for power transmission.
-
Mating features: Include guide pins, polarization keys, or asymmetric connector designs to prevent incorrect mating and potential damage to the boards or connectors.
Signal Integrity and Power Integrity
-
Cross-board signal routing: Minimize the number of signals that need to cross board boundaries. When routing signals between boards, use appropriate techniques such as impedance matching, termination, and length matching to maintain signal integrity.
-
Power distribution: Provide adequate power distribution and decoupling capacitors on each board to minimize noise and ensure stable power delivery. Use separate power and ground planes for analog and digital sections to reduce crosstalk.
-
Grounding: Implement a consistent grounding scheme across all boards, using techniques like star grounding or ground planes. Avoid creating ground loops by properly connecting the ground references of the interconnected boards.
Mechanical Considerations
-
Board mounting: Use appropriate mounting techniques, such as standoffs, screws, or snap-fit features, to securely fasten the boards to the enclosure or chassis. Consider the mechanical stress and vibration that the boards may be subjected to in the operating environment.
-
Strain relief: Provide strain relief for cables and connectors to prevent damage due to mechanical stress. Use cable ties, clamps, or adhesive pads to secure cables and prevent them from pulling on the connectors.
-
Serviceability: Design the multi-board system with serviceability in mind. Make sure that connectors and cables are easily accessible for maintenance or replacement without having to disassemble the entire system.
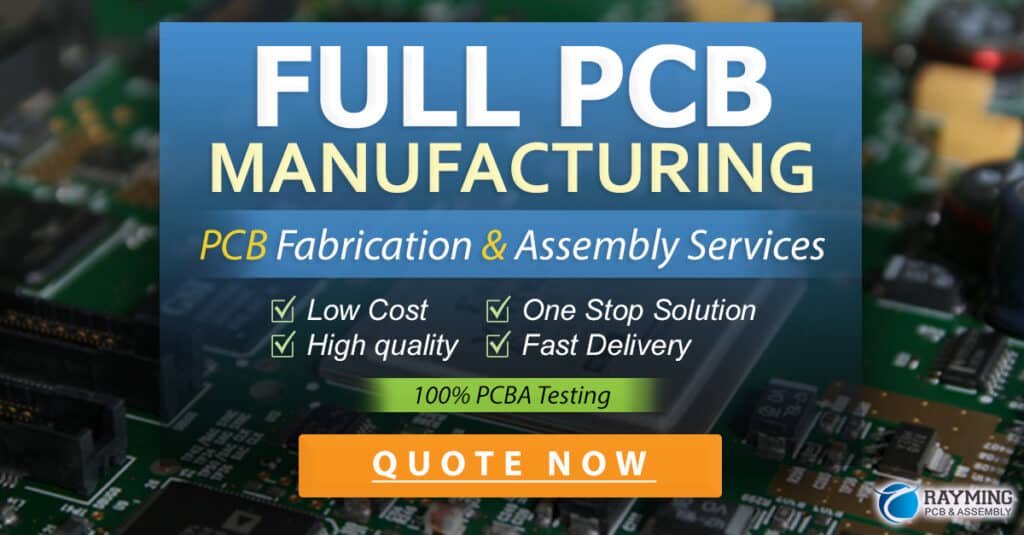
FAQ
What are the advantages of using board-to-board connectors over cable assemblies?
A: Board-to-board connectors offer several advantages over cable assemblies:
– They provide a more direct and compact connection between boards, saving space and reducing the overall system size.
– They typically have lower signal loss and better impedance control compared to cables, making them suitable for high-speed signals.
– They are generally more reliable and have a longer lifespan than cable assemblies, as they are not subject to the same mechanical stress and wear.
However, cable assemblies still have their place in multi-board systems, particularly when the boards need to be physically separated or when flexibility in positioning is required.
How do I ensure proper signal integrity when routing signals between multiple boards?
A: To ensure proper signal integrity when routing signals between multiple boards, follow these guidelines:
– Minimize the number of signals that need to cross board boundaries. Group related signals together on the same board whenever possible.
– Use appropriate interconnect solutions, such as high-speed board-to-board connectors or shielded cable assemblies, to maintain signal integrity across the boards.
– Implement proper termination techniques, such as series termination or differential termination, to minimize reflections and signal distortion.
– Match the length and delay of signal paths that are part of the same bus or interface to prevent timing skew and ensure synchronous operation.
– Provide adequate ground and power referencing between the boards, using techniques like ground planes or low-impedance power distribution networks.
What are some common pitfalls to avoid when designing multi-board PCB systems?
A: Here are some common pitfalls to avoid when designing multi-board PCB systems:
– Inadequate planning and partitioning of the system, leading to suboptimal board division and inefficient interconnects.
– Choosing connectors or cables that are not rated for the required operating environment, signal integrity, or mating cycles.
– Failing to provide proper strain relief for cables and connectors, resulting in mechanical stress and potential damage.
– Inadequate power distribution and decoupling, causing noise and signal integrity issues across the boards.
– Inconsistent grounding schemes or creating ground loops, which can introduce noise and degrade system performance.
– Neglecting mechanical considerations, such as board mounting and serviceability, leading to difficulties in assembly and maintenance.
By being aware of these pitfalls and following best practices in multi-board PCB design, you can create reliable and high-performance systems that meet the specific requirements of your application.
How can I select the right board-to-board connector for my application?
A: When selecting a board-to-board connector for your application, consider the following factors:
– Number of contacts: Choose a connector with sufficient contacts to accommodate all the necessary signals and power connections between the boards.
– Pitch: Select a connector pitch that is appropriate for your PCB layout and manufacturing capabilities. Finer pitches allow for higher density connections but may require more advanced PCB fabrication and assembly techniques.
– Stacking height: Consider the available space in your enclosure and choose a connector with a stacking height that fits within those constraints. Low-profile connectors are available for space-constrained applications.
– Signal integrity: If you have high-speed or sensitive signals, choose connectors with good signal integrity characteristics, such as controlled impedance, shielding, or differential pairs.
– Mating cycles: Select a connector that is rated for the expected number of mating cycles in your application. Some connectors are designed for high-reliability applications and can withstand thousands of mating cycles.
– Operating environment: Make sure the connector is rated for the expected operating temperature, humidity, and vibration levels in your application.
– Cost: Consider the cost of the connector in relation to your overall budget and the expected production volume. Some high-end connectors may offer better performance but come at a higher price point.
By carefully evaluating these factors and consulting with connector manufacturers or distributors, you can select the most suitable board-to-board connector for your specific application.
What are some best practices for ensuring mechanical reliability in multi-board PCB systems?
A: To ensure mechanical reliability in multi-board PCB systems, follow these best practices:
– Use appropriate board mounting techniques, such as standoffs, screws, or snap-fit features, to securely fasten the boards to the enclosure or chassis. Make sure the mounting points are strong enough to withstand the expected mechanical stresses.
– Provide adequate strain relief for cables and connectors to prevent damage due to mechanical stress. Use cable ties, clamps, or adhesive pads to secure cables and prevent them from pulling on the connectors.
– Consider the expected operating environment and choose components, materials, and coatings that can withstand the anticipated temperature, humidity, and vibration levels.
– Design the enclosure or chassis to provide proper support and protection for the PCBs and interconnects. Use guide rails, slots, or other features to ensure precise alignment and prevent unintended movement.
– Conduct thorough mechanical testing and validation, including vibration, shock, and thermal cycling tests, to verify the robustness of your multi-board system.
– Design for serviceability by making sure that connectors and cables are easily accessible for maintenance or replacement. Use modular designs and quick-release fasteners to facilitate servicing without having to disassemble the entire system.
– Follow industry standards and guidelines, such as IPC or military specifications, for PCB design, fabrication, and assembly to ensure consistency and reliability.
By incorporating these best practices into your multi-board PCB design process, you can create systems that are mechanically robust and reliable, even in demanding operating environments.
Conclusion
PCB interconnect solutions play a vital role in multi-board electronics systems, enabling reliable and efficient connectivity between boards. By understanding the different types of interconnects available and following best practices in multi-board PCB design, engineers can create high-performance and robust systems that meet the specific requirements of their applications.
Key considerations in multi-board PCB design include proper planning and partitioning, selection of appropriate interconnects, signal and power integrity, and mechanical reliability. By carefully evaluating these factors and leveraging the strengths of different interconnect technologies, designers can overcome the challenges associated with multi-board systems and create products that are both functionally and mechanically sound.
As electronics continue to evolve and become more complex, the importance of effective PCB interconnect solutions will only grow. By staying up-to-date with the latest technologies and best practices, electronics engineers can push the boundaries of multi-board design and create innovative products that meet the ever-increasing demands of the market.
Leave a Reply