Understanding DNI/DNP Entries in PCB BOMs
When creating a bill of materials (BOM) for a printed circuit board (PCB), it’s common to come across the terms “DNI” and “DNP.” These acronyms stand for “Do Not Install” and “Do Not Place,” respectively. DNI/DNP entries are used to indicate components that are included in the BOM but should not be physically installed or placed on the PCB during the manufacturing process.
Why Use DNI/DNP Entries?
There are several reasons why designers might choose to include DNI/DNP entries in their PCB BOMs:
-
Future expandability: DNI/DNP entries allow for the inclusion of components that may be needed for future upgrades or expansions of the PCB design, without requiring immediate installation.
-
Variant management: When designing a PCB with multiple variants, DNI/DNP entries can be used to differentiate between components that are specific to each variant, simplifying the manufacturing process.
-
Cost optimization: By using DNI/DNP entries, designers can include optional components in the BOM that may be installed based on customer requirements or cost considerations, without having to create separate BOMs for each configuration.
-
Testing and debugging: DNI/DNP entries can be used to include test points or debugging components that are not required for the final product but are necessary during the development and testing phases.
Best Practices for Implementing DNI/DNP Entries
To effectively use DNI/DNP entries in your PCB BOM, consider the following best practices:
1. Clear Communication with Manufacturers
Ensure that your PCB manufacturer is aware of and understands the DNI/DNP entries in your BOM. Provide clear instructions on which components should be installed and which should be omitted. This can be done through notes in the BOM itself or by providing separate assembly instructions.
2. Consistent Nomenclature
Use consistent and clear nomenclature when designating DNI/DNP entries in your BOM. Some common conventions include:
- Appending “DNI” or “DNP” to the component reference designator (e.g., “R1 – DNI”)
- Adding a separate “DNI” or “DNP” column in the BOM
- Using a specific value in the “Quantity” column (e.g., “0” for DNI/DNP components)
Choose a convention that is easily understandable and maintain consistency throughout your BOM.
3. Distinct Visual Identification
In addition to clear nomenclature, it’s helpful to visually distinguish DNI/DNP components on your PCB layout. This can be achieved by:
- Using a different color or layer for DNI/DNP components
- Applying a unique graphical marker or symbol to DNI/DNP footprints
- Placing DNI/DNP components in a separate area of the PCB layout
Distinct visual identification helps prevent confusion during the manufacturing process and reduces the likelihood of errors.
4. BOM Organization and Grouping
Organize your BOM in a logical manner, grouping components based on their function or location on the PCB. This makes it easier to identify and manage DNI/DNP entries. Consider creating separate sections or tabs in your BOM for DNI/DNP components, making them easily distinguishable from the components to be installed.
5. Thorough Documentation
Provide comprehensive documentation that explains the purpose and reasoning behind each DNI/DNP entry in your BOM. This documentation should include:
- The specific function of the DNI/DNP component
- The conditions under which the component should be installed (if applicable)
- Any special instructions for handling DNI/DNP components during the manufacturing process
Clear documentation ensures that all stakeholders, including designers, manufacturers, and assembly teams, have a shared understanding of the DNI/DNP entries and their implications.
Managing DNI/DNP Entries in Your PCB BOM
Effective management of DNI/DNP entries is crucial to streamline the PCB manufacturing process and avoid potential issues. Here are some strategies to help you manage DNI/DNP entries effectively:
1. Regular BOM Reviews
Conduct regular reviews of your PCB BOM to ensure that DNI/DNP entries are up to date and accurate. As your design evolves, the status of certain components may change, requiring updates to the DNI/DNP designations. Regularly reviewing and updating your BOM helps maintain its integrity and prevents confusion during manufacturing.
2. Version Control
Implement a robust version control system for your PCB BOM. This allows you to track changes to DNI/DNP entries over time and ensures that all team members are working with the most current version of the BOM. Version control also facilitates collaboration and helps maintain a clear history of revisions.
3. Automated bom management tools
Consider using automated BOM management tools to streamline the process of handling DNI/DNP entries. These tools can help you:
- Automatically generate and update BOMs based on your PCB design files
- Enforce consistent nomenclature and formatting for DNI/DNP entries
- Detect and flag discrepancies or conflicts in DNI/DNP designations
- Collaborate with team members and share BOM information securely
Automated BOM management tools can save time, reduce errors, and ensure consistency throughout your PCB design and manufacturing workflow.
4. Supply Chain Considerations
When including DNI/DNP entries in your BOM, consider the impact on your supply chain. Ensure that your suppliers and manufacturers are aware of the DNI/DNP components and can accommodate any special handling or storage requirements. If DNI/DNP components have long lead times or are subject to minimum order quantities, factor this into your planning and inventory management strategies.
5. Testing and Validation
Incorporate DNI/DNP entries into your testing and validation processes. Develop test plans and procedures that account for the presence or absence of DNI/DNP components. This may involve creating separate test configurations or using specialized test fixtures that accommodate DNI/DNP entries. Thorough testing and validation help ensure that your PCB functions as intended, regardless of the presence or absence of DNI/DNP components.
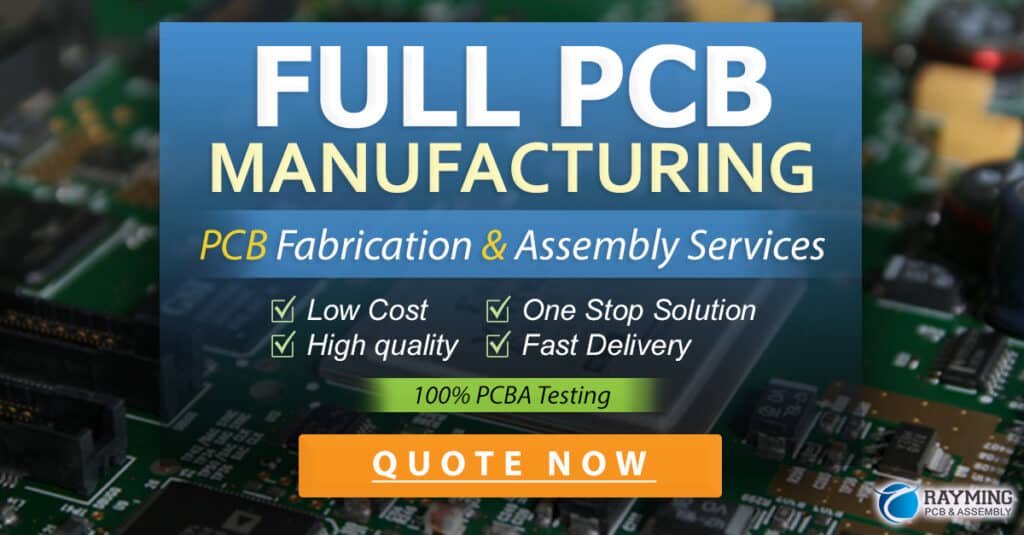
FAQ
1. What is the difference between DNI and DNP?
DNI (Do Not Install) and DNP (Do Not Place) are similar concepts, but with a slight distinction:
- DNI indicates that a component should not be physically installed on the PCB during the assembly process.
- DNP suggests that the component footprint should not be placed on the PCB layout at all.
In practice, both terms are often used interchangeably to indicate components that are included in the BOM but should not be installed on the PCB.
2. Can DNI/DNP entries be used for components that are optional or configurable?
Yes, DNI/DNP entries are commonly used for optional or configurable components in a PCB design. By designating these components as DNI/DNP, designers can create a single BOM that covers multiple product variations or configurations, simplifying the manufacturing process and reducing the need for separate BOMs.
3. How do I indicate DNI/DNP entries in my PCB design files?
There are several ways to indicate DNI/DNP entries in your PCB design files:
- Use a specific layer or color to distinguish DNI/DNP components visually
- Apply a unique graphical marker or symbol to the component footprints
- Include a note or comment in the design files indicating the DNI/DNP status of specific components
Consult your PCB design software’s documentation for specific instructions on how to implement DNI/DNP designations in your design files.
4. What should I do if a DNI/DNP component is accidentally installed on a PCB?
If a DNI/DNP component is accidentally installed on a PCB, the appropriate course of action depends on the specific component and its impact on the PCB’s functionality and safety. In some cases, the component may need to be physically removed from the PCB. In other cases, it may be possible to disable or isolate the component through firmware or software modifications. Consult with your design and engineering teams to determine the best approach for handling accidentally installed DNI/DNP components.
5. How can I ensure that my contract manufacturer understands and follows my DNI/DNP instructions?
To ensure that your contract manufacturer understands and follows your DNI/DNP instructions:
- Clearly communicate the presence and purpose of DNI/DNP entries in your BOM and assembly instructions
- Use consistent and unambiguous nomenclature for DNI/DNP designations
- Provide visual aids, such as annotated PCB layout images or assembly drawings, to highlight DNI/DNP components
- Establish a clear line of communication with your manufacturer and be available to answer any questions or clarify any uncertainties regarding DNI/DNP entries
By following these guidelines, you can minimize the risk of misinterpretation and ensure that your manufacturer adheres to your DNI/DNP requirements.
Aspect | Best Practice |
---|---|
Communication | Clearly communicate DNI/DNP entries to manufacturers and provide explicit instructions |
Nomenclature | Use consistent and clear nomenclature for DNI/DNP entries, such as appending “DNI” or “DNP” to component reference designators |
Visual Identification | Visually distinguish DNI/DNP components on PCB layouts using different colors, layers, or graphical markers |
BOM Organization | Organize the BOM logically, grouping components based on function or location, and consider creating separate sections for DNI/DNP entries |
Documentation | Provide comprehensive documentation explaining the purpose and reasoning behind each DNI/DNP entry, including any special instructions |
Regular Reviews | Conduct regular reviews of the PCB BOM to ensure DNI/DNP entries are up to date and accurate |
Version Control | Implement a robust version control system to track changes to DNI/DNP entries and maintain a clear history of revisions |
Automation | Consider using automated BOM management tools to streamline the handling of DNI/DNP entries, enforce consistency, and reduce errors |
Supply Chain | Ensure suppliers and manufacturers are aware of DNI/DNP components and can accommodate any special handling or storage requirements |
Testing and Validation | Incorporate DNI/DNP entries into testing and validation processes, developing test plans and procedures that account for the presence or absence of DNI/DNP components |
By adhering to these best practices, designers can effectively manage DNI/DNP entries in their PCB BOMs, streamline the manufacturing process, and ensure the successful realization of their PCB designs.
Leave a Reply