Introduction to Multilayer PCB Design
Multilayer PCB design is an essential aspect of modern electronics manufacturing. As technology advances and devices become more complex, the need for efficient and reliable circuit board layouts increases. Designing a multilayer PCB requires careful consideration of various factors, such as signal integrity, power distribution, and thermal management. In this article, we will explore the best multilayer PCB design tips to help you create optimal circuit board layouts.
Understanding the Basics of Multilayer PCB Design
What is a Multilayer PCB?
A multilayer PCB is a printed circuit board that consists of multiple layers of conductive material, typically copper, separated by insulating layers. These layers are interconnected through vias, which are small holes drilled through the board and plated with conductive material. Multilayer PCBs offer several advantages over single-layer boards, including:
- Increased component density
- Improved signal integrity
- Better power distribution
- Enhanced thermal management
Advantages of Multilayer PCB Design
- Space Savings: Multilayer PCBs allow for a higher component density, which means more functionality can be packed into a smaller space.
- Improved Signal Integrity: By separating signals on different layers and using proper grounding techniques, multilayer PCBs can minimize crosstalk and electromagnetic interference (EMI).
- Better Power Distribution: Dedicated power and ground planes in multilayer PCBs provide a low-impedance path for power distribution, reducing voltage drops and improving overall power delivery.
- Enhanced Thermal Management: Multilayer PCBs can dissipate heat more effectively by incorporating thermal vias and using metal cores or heat spreaders.
Best Practices for Multilayer PCB Design
1. Plan Your Layer Stack-up
A well-planned layer stack-up is crucial for the success of your multilayer PCB design. Consider the following factors when deciding on your layer stack-up:
- Signal layers: Determine the number of signal layers needed based on the complexity of your design and the required signal integrity.
- Power and ground planes: Dedicate layers for power and ground to provide a low-impedance path for power distribution and reduce noise.
- Dielectric materials: Choose appropriate dielectric materials based on their electrical properties, such as dielectric constant and loss tangent.
Here’s an example of a typical 6-layer PCB stack-up:
Layer | Material | Thickness (mm) |
---|---|---|
Top Solder Mask | Epoxy | 0.025 |
Top Copper | Copper | 0.035 |
Core | FR-4 | 0.2 |
Inner Copper 1 | Copper | 0.035 |
Prepreg | FR-4 | 0.2 |
Inner Copper 2 | Copper | 0.035 |
Core | FR-4 | 0.2 |
Bottom Copper | Copper | 0.035 |
Bottom Solder Mask | Epoxy | 0.025 |
2. Use Proper Grounding Techniques
Proper grounding is essential for maintaining signal integrity and reducing EMI in multilayer PCBs. Follow these grounding techniques:
- Use a solid ground plane: A continuous ground plane provides a low-impedance return path for signals and helps minimize ground loops.
- Implement a star grounding strategy: Connect all ground points to a single, central ground point to avoid creating ground loops.
- Use ground vias: Place ground vias near high-speed signals to provide a short return path and minimize inductance.
3. Minimize Crosstalk and EMI
Crosstalk and EMI can degrade signal quality and lead to system malfunctions. To minimize these issues:
- Route high-speed signals on inner layers: Placing high-speed signals on inner layers, surrounded by ground planes, helps contain EMI and reduces crosstalk.
- Use differential signaling: Differential signaling techniques, such as LVDS (Low-Voltage Differential Signaling), can help cancel out electromagnetic fields and reduce noise.
- Implement proper signal routing: Follow best practices for signal routing, such as avoiding sharp corners, maintaining consistent trace widths, and using appropriate spacing between signals.
4. Optimize Power Distribution
Efficient power distribution is crucial for maintaining signal integrity and preventing voltage drops. Consider these tips:
- Use dedicated power planes: Assign dedicated layers for power distribution to provide a low-impedance path for current flow.
- Implement power islands: Separate analog and digital power supplies to minimize noise coupling between the two domains.
- Use decoupling capacitors: Place decoupling capacitors close to power pins of ICs to suppress high-frequency noise and provide local energy storage.
5. Consider Thermal Management
Thermal management is critical for ensuring the long-term reliability of your multilayer PCB. Incorporate these techniques:
- Use thermal vias: Place thermal vias near high-power components to transfer heat from the component to the ground plane or heat spreader.
- Incorporate metal cores: For high-power applications, consider using metal core PCBs (MCPCBs) to improve heat dissipation.
- Use thermal interface materials: Apply thermal interface materials, such as thermal pads or paste, between components and heat spreaders to enhance heat transfer.
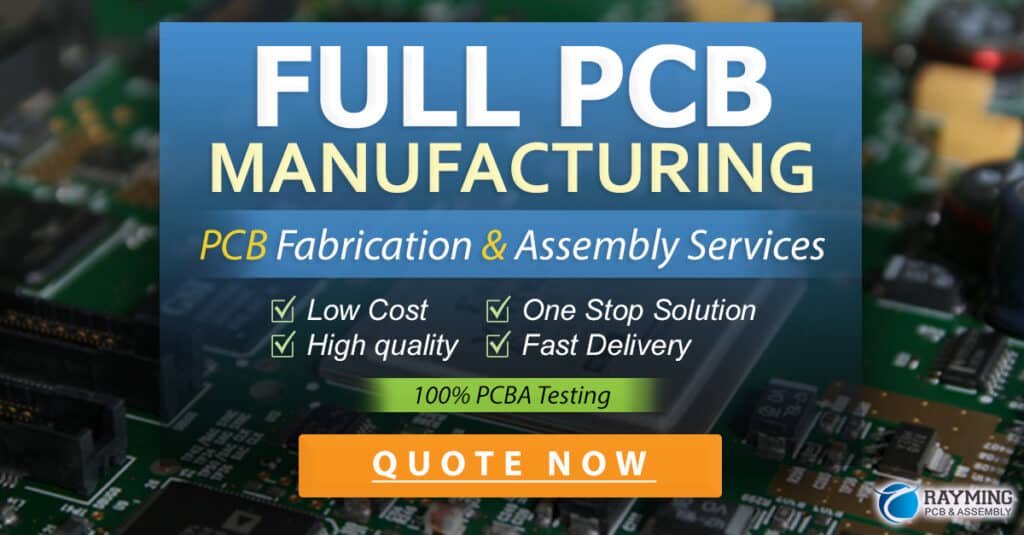
Advanced Multilayer PCB Design Techniques
High-Speed Design Considerations
When designing multilayer PCBs for high-speed applications, consider the following:
- Impedance control: Match the impedance of traces to the characteristic impedance of the system to minimize reflections and ensure signal integrity.
- Length matching: Match the lengths of critical signal paths to maintain signal synchronization and avoid timing issues.
- Via optimization: Minimize the use of vias and optimize their placement to reduce signal distortion and reflections.
Flex and Rigid-Flex PCB Design
Flex and rigid-flex PCBs offer unique advantages, such as increased flexibility and reduced space requirements. When designing these types of PCBs:
- Use appropriate materials: Choose flexible substrates, such as polyimide, that can withstand repeated bending and flexing.
- Consider bend radius: Ensure that the minimum bend radius of the flex PCB is compatible with your application requirements.
- Implement strain relief: Use strain relief techniques, such as stiffeners or anchors, to prevent damage to the flex circuit during bending.
Design for Manufacturing (DFM)
To ensure the manufacturability and reliability of your multilayer PCB, follow these DFM guidelines:
- Adhere to manufacturing constraints: Work closely with your PCB manufacturer to understand their capabilities and limitations, such as minimum trace widths, spacing, and hole sizes.
- Implement design rule checks (DRC): Use PCB design software with built-in DRC tools to identify and correct design issues before sending the board for manufacturing.
- Consider testability: Incorporate test points and other features that facilitate automated testing and inspection of the assembled PCB.
Frequently Asked Questions (FAQ)
- What is the ideal number of layers for a multilayer PCB?
-
The ideal number of layers depends on the complexity of your design and the specific requirements of your application. Typically, multilayer PCBs range from 4 to 12 layers, but some complex designs may require even more layers.
-
How can I ensure proper impedance control in my multilayer PCB design?
-
To ensure proper impedance control, calculate the required trace width and spacing based on the desired characteristic impedance and the properties of the dielectric material. Use a controlled impedance calculator or consult with your PCB manufacturer for guidance.
-
What are the benefits of using blind and buried vias in multilayer PCBs?
-
Blind and buried vias offer several benefits, such as increased component density, improved signal integrity, and reduced board size. Blind vias connect an outer layer to an inner layer, while buried vias connect two or more inner layers without reaching the outer layers.
-
How do I choose the right dielectric material for my multilayer PCB?
-
When choosing a dielectric material, consider factors such as the dielectric constant, loss tangent, thermal stability, and cost. Common dielectric materials include FR-4, Rogers, and Isola. Consult with your PCB manufacturer or material supplier for recommendations based on your specific application requirements.
-
What are some common pitfalls to avoid in multilayer PCB design?
- Some common pitfalls to avoid include improper grounding, inadequate power distribution, insufficient clearances between traces, and failure to consider manufacturability. By following best practices and guidelines, such as those outlined in this article, you can minimize the risk of these pitfalls and ensure a successful multilayer PCB design.
Conclusion
Designing a multilayer PCB requires careful consideration of various factors, such as signal integrity, power distribution, and thermal management. By following the best practices and tips outlined in this article, you can create optimal circuit board layouts that meet your application’s requirements and ensure reliable performance. Remember to plan your layer stack-up, use proper grounding techniques, minimize crosstalk and EMI, optimize power distribution, and consider thermal management. Additionally, stay up-to-date with advanced multilayer PCB design techniques, such as high-speed design, flex and rigid-flex PCBs, and design for manufacturing. By mastering these multilayer PCB design skills, you can unlock the full potential of your electronic devices and stay ahead in the ever-evolving world of electronics manufacturing.
Leave a Reply