IPC-7351 Land Pattern Standard
One of the most widely used standards for PCB pad design is IPC-7351, a document published by IPC (Association Connecting Electronics Industries). IPC-7351 provides recommended land patterns and design guidelines for a variety of component types and package styles.
The land pattern dimensions in IPC-7351 are derived from both empirical data and mathematical calculations based on the component manufacturer’s specifications. They take into account factors like:
- Component package dimensions
- Lead pitch
- Placement tolerances
- Soldering process (reflow vs wave)
- Solder joint reliability requirements
For each component type, IPC-7351 specifies a range of recommended pad sizes and shapes, as well as minimum, nominal, and maximum dimensions. Here is an example of the pad dimensions for a SOIC (Small Outline Integrated Circuit) component from IPC-7351:
Dimension | Minimum | Nominal | Maximum |
---|---|---|---|
Pad length | 0.66 mm | 0.91 mm | 1.16 mm |
Pad width | 0.66 mm | 0.91 mm | 1.16 mm |
PCB design tools like Altium Designer, Eagle, and KiCad include IPC-7351 compliant footprints in their libraries, allowing you to easily apply the recommended pad dimensions to your design.
While IPC-7351 provides a good starting point, it’s important to note that the final pad dimensions may need to be adjusted based on the specific needs of your design. Factors like the PCB manufacturer’s capabilities, assembly process, and operating environment can all influence the optimal pad size.
Calculations Based on Solder Joint Area
Another approach to determining pad size is to calculate the required solder joint area for a strong and reliable connection. The solder joint area is a function of the pad size, component lead size, and solder fillet geometry.
A common rule of thumb is that the solder joint area should be at least as large as the cross-sectional area of the component lead. This ensures that there is enough solder to fully wet the lead and form a strong mechanical connection.
For example, consider a resistor with a lead diameter of 0.5 mm. The cross-sectional area of the lead is:
A = πr^2 = π(0.25 mm)^2 = 0.196 mm^2
To provide an equivalent solder joint area on the PCB side, the pad should have a surface area of at least 0.196 mm^2. If the pad is circular, the minimum diameter would be:
d = sqrt(4A/π) = sqrt(4*0.196/π) = 0.56 mm
In practice, you would likely specify a somewhat larger pad to account for variations in the soldering process and ensure a reliable joint. A common approach is to make the pad diameter 1.5 to 2 times the lead diameter.
For surface mount components, the calculation is similar but must account for the flat geometry of the component leads. The width of the pad should be at least as large as the lead width, and the length should be sufficient to provide the necessary solder joint area.
Manufacturer Recommendations
In addition to industry standards and solder joint calculations, it’s always a good idea to consult the component manufacturer’s datasheets and application notes for pad size recommendations.
Many component manufacturers provide detailed drawings and dimensions for recommended PCB land patterns. These take into account the specific geometry and tolerances of the component package, as well as the intended use case and reliability requirements.
For example, Texas Instruments provides the following recommended pad dimensions for their SOT-23 package:
Dimension | Minimum | Nominal | Maximum |
---|---|---|---|
Pad length | 0.90 mm | 1.00 mm | 1.10 mm |
Pad width | 0.60 mm | 0.70 mm | 0.80 mm |
Manufacturer recommendations are a valuable resource, as they are based on extensive testing and experience with the specific component. However, it’s still important to consider the needs of your particular design and assembly process when selecting final pad dimensions.
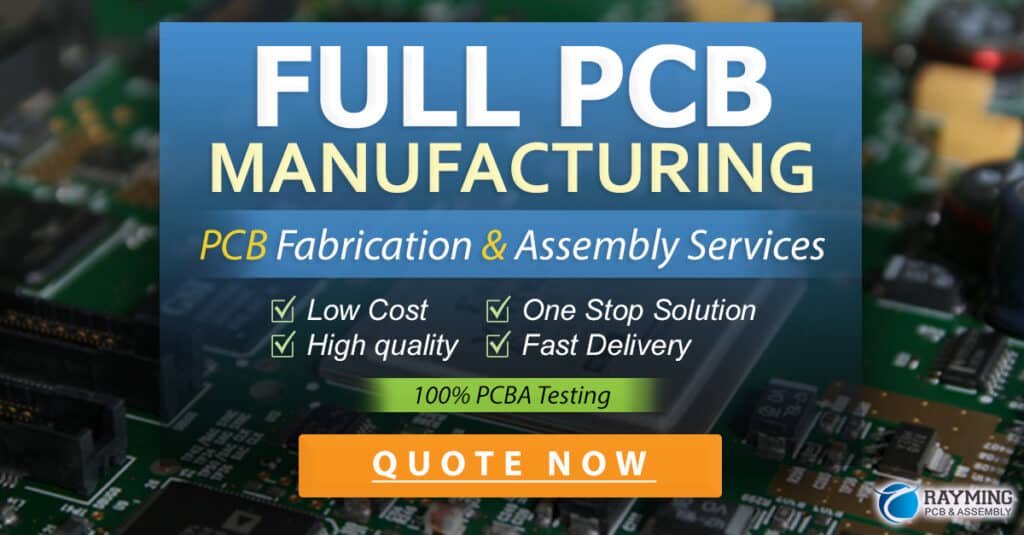
Prototyping and Testing
While standards, calculations, and manufacturer recommendations provide a solid starting point, the ultimate validation of pad size comes from prototyping and testing.
Before committing to a final design, it’s a good idea to fabricate prototype boards with the proposed pad dimensions and assemble them using the intended manufacturing process. This allows you to evaluate the solder joint quality, mechanical strength, and reliability in a real-world scenario.
During prototyping, pay close attention to factors like:
- Solder wetting and filleting
- Voiding or incomplete solder coverage
- Component alignment and shifting
- Mechanical stress or cracking of solder joints
Based on the results of your prototyping and testing, you can make adjustments to the pad dimensions as needed to optimize performance and reliability.
FAQ
- What happens if PCB pads are too small?
If PCB pads are too small, there may not be enough surface area for the solder to properly wet and form a strong joint. This can lead to issues like poor mechanical strength, high electrical resistance, or intermittent connections. In extreme cases, the component may not be able to be soldered to the board at all.
- What happens if PCB pads are too large?
Overly large PCB pads can waste valuable board space and increase the risk of bridging or short circuits between adjacent pads. They can also lead to issues like tombstoning, where the surface tension of the molten solder pulls the component up off the board.
- How do PCB design tools handle pad size?
Most PCB design tools include libraries of standard component footprints with recommended pad sizes based on industry standards like IPC-7351. These footprints can be used as a starting point and then modified as needed for the specific design. Many tools also include calculators and wizards to help determine optimal pad dimensions based on factors like solder joint area and component geometry.
- What factors influence the optimal pad size for a design?
The optimal pad size for a PCB design depends on several factors, including:
- Component package dimensions and lead geometry
- Soldering process (reflow vs wave)
- PCB manufacturing capabilities and tolerances
- Assembly process and equipment
- Operating environment and reliability requirements
It’s important to consider all of these factors and consult with the PCB manufacturer and assembly team to determine the best pad dimensions for a given design.
- Can pad size affect signal integrity?
Pad size can have an impact on signal integrity, particularly at high frequencies. Larger pads can add unwanted capacitance and inductance to the signal path, leading to reflections, distortions, and increased EMI. In high-speed designs, it’s important to carefully consider pad size and placement to minimize these effects and maintain signal integrity.
Conclusion
Proper pad size is essential for ensuring reliable and robust solder joints in PCB assembly. There are several methods and guidelines available for calculating optimal pad dimensions, including industry standards like IPC-7351, solder joint area calculations, and manufacturer recommendations.
However, the final validation of pad size must come from prototyping and testing to evaluate real-world performance and reliability. By carefully considering all of the relevant factors and iterating on the design as needed, you can arrive at the ideal pad dimensions for your specific PCB design.
Leave a Reply