Introduction to Double Sided PCB Soldering
Double sided PCB soldering is a process of assembling electronic components on both sides of a printed circuit board (PCB). This technique is widely used in the electronics industry to create compact and efficient electronic devices. With the increasing demand for smaller and more complex electronic devices, double sided PCB soldering has become an essential skill for electronics engineers and technicians.
Advantages of Double Sided PCB Soldering
- Space-saving: Double sided PCB soldering allows for more components to be placed on a single board, reducing the overall size of the device.
- Improved performance: By placing components on both sides of the board, the distance between them is reduced, leading to better signal integrity and faster operation.
- Cost-effective: Double sided PCB soldering can reduce the number of boards required for a device, lowering production costs.
Designing for Double Sided PCB Soldering
Component Placement
When designing a double sided PCB, it’s crucial to consider the placement of components. Here are some best practices for component placement:
- Place components on opposite sides of the board to minimize interference and crosstalk.
- Group related components together to reduce the length of traces and improve signal integrity.
- Avoid placing large components near the edges of the board to prevent damage during handling and assembly.
Trace Routing
Proper trace routing is essential for ensuring the reliability and performance of a double sided PCB. Here are some guidelines for trace routing:
- Use appropriate trace widths based on the current requirements of the components.
- Maintain adequate spacing between traces to prevent short circuits and signal interference.
- Use ground planes and power planes to provide a low-impedance path for current and reduce EMI.
Vias and Through-Hole Components
Vias and through-hole components are used to connect traces on opposite sides of the board. Here are some best practices for using vias and through-hole components:
- Use the appropriate size and type of via for the current requirements and board thickness.
- Place vias strategically to minimize the length of traces and improve signal integrity.
- Use thermal relief pads for through-hole components to prevent thermal stress during soldering.
Soldering Techniques for Double Sided PCB
Surface Mount Device (SMD) Soldering
SMD soldering is the most common method used for double sided PCB soldering. Here are some tips for successful SMD soldering:
- Use a fine-tipped soldering iron with adjustable temperature control.
- Apply a small amount of solder paste to the pads using a stencil or syringe.
- Place the components on the pads using tweezers or a pick-and-place machine.
- Reflow the solder paste using a reflow oven or hot air gun.
Through-Hole Component Soldering
Through-hole components are still used in some applications, particularly for large components or those that require mechanical stability. Here are some tips for soldering through-hole components on a double sided PCB:
- Insert the component leads through the holes in the board and bend them slightly to hold the component in place.
- Apply flux to the leads and pads to improve solder wetting and prevent oxidation.
- Use a soldering iron with a chisel tip to apply solder to the leads and pads.
- Trim the excess leads flush with the board surface using wire cutters.
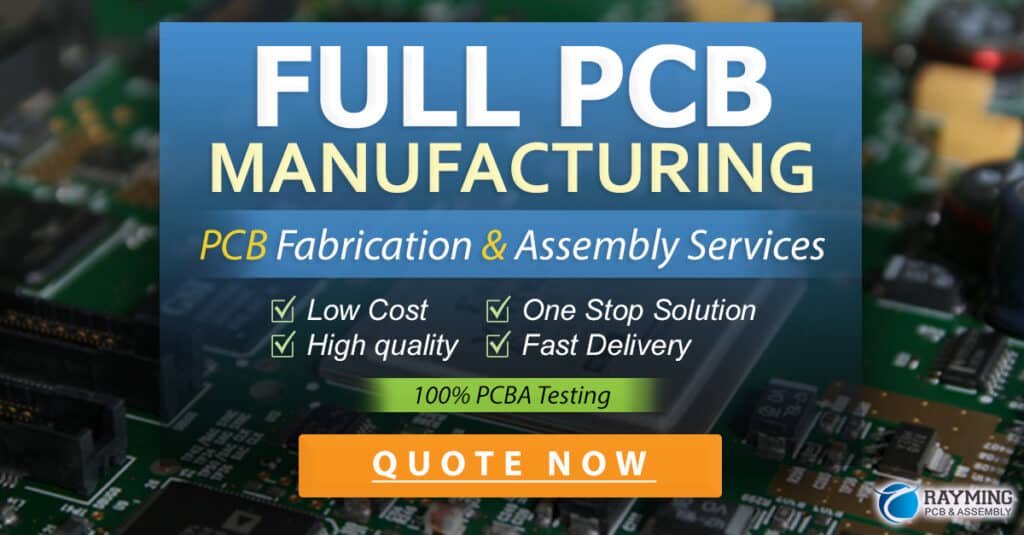
Inspection and Testing
After soldering, it’s essential to inspect and test the board to ensure proper functionality and reliability. Here are some methods for inspecting and testing a double sided PCB:
Visual Inspection
Visual inspection is the first step in checking the quality of the soldering. Here are some things to look for:
- Solder bridges: Check for short circuits caused by excess solder bridging adjacent pads or traces.
- Cold solder joints: Look for dull, grainy, or cracked solder joints that may indicate poor wetting or insufficient heat.
- Component alignment: Verify that all components are properly aligned and seated on the pads.
Automated Optical Inspection (AOI)
AOI uses cameras and image processing software to automatically inspect the board for defects. AOI can detect a wide range of defects, including:
- Missing or misaligned components
- Solder bridges and short circuits
- Insufficient or excess solder
- Damaged or lifted pads
Electrical Testing
Electrical testing is the final step in verifying the functionality of the board. Here are some common electrical tests:
- Continuity testing: Check for open circuits or short circuits using a multimeter or continuity tester.
- Functional testing: Apply power to the board and test its functionality using a test fixture or oscilloscope.
- Boundary scan testing: Use a boundary scan tool to test the interconnections between components and detect faults.
Common Challenges and Solutions
Double sided PCB soldering presents some unique challenges that require special attention. Here are some common challenges and their solutions:
Tombstoning
Tombstoning occurs when a component stands up on one end due to uneven heating or surface tension. To prevent tombstoning:
- Use a solder paste with a higher melting point and a wider process window.
- Ensure that the pads are the same size and shape on both sides of the component.
- Use a reflow profile with a slower ramp-up rate and a longer soak time.
Solder Bridging
Solder bridging occurs when excess solder flows between adjacent pads or traces, creating a short circuit. To prevent solder bridging:
- Use a solder mask to cover the areas between pads and traces.
- Reduce the amount of solder paste applied to the pads.
- Use a finer-pitch stencil or syringe for applying solder paste.
Thermal Damage
Thermal damage can occur when the board or components are exposed to excessive heat during soldering. To prevent thermal damage:
- Use a temperature-controlled soldering iron or reflow oven.
- Follow the recommended reflow profile for the solder paste and components.
- Use a heat sink or thermal relief pad for large components or those with high thermal mass.
Conclusion
Double sided PCB soldering is a complex process that requires careful design, precise soldering techniques, and thorough inspection and testing. By following the best practices outlined in this article, you can ensure the reliability and performance of your double sided PCBs.
Frequently Asked Questions
1. What is the difference between SMD and through-hole soldering?
SMD soldering involves soldering components directly onto the surface of the board, while through-hole soldering involves inserting component leads through holes in the board and soldering them on the opposite side.
2. Can I use a regular soldering iron for SMD soldering?
While it’s possible to use a regular soldering iron for SMD soldering, it’s recommended to use a fine-tipped iron with adjustable temperature control for better precision and control.
3. How do I prevent solder bridging when soldering fine-pitch components?
To prevent solder bridging, use a solder mask to cover the areas between pads and traces, reduce the amount of solder paste applied to the pads, and use a finer-pitch stencil or syringe for applying solder paste.
4. What is the purpose of a reflow oven in double sided PCB soldering?
A reflow oven is used to melt and solidify the solder paste on the board, creating a strong and reliable solder joint between the components and the pads.
5. How can I test the functionality of a double sided PCB after soldering?
You can test the functionality of a double sided PCB using continuity testing to check for open or short circuits, functional testing to verify the board’s operation, and boundary scan testing to detect faults in the interconnections between components.
Soldering Technique | Advantages | Disadvantages |
---|---|---|
SMD Soldering | Allows for smaller components and higher density layouts | Requires specialized equipment and skills |
Through-Hole Soldering | Provides mechanical stability and ease of replacement | Takes up more space and limits component density |
Leave a Reply