What are High Dk PCB Materials?
High Dk PCB materials, also known as high dielectric constant materials, are a type of substrate used in the manufacturing of printed circuit boards (PCBs). These materials have a dielectric constant (Dk) higher than traditional FR-4 materials, which typically have a Dk value of around 4.5. High Dk PCB materials can have Dk values ranging from 6 to 100, depending on the specific material composition.
The dielectric constant is a measure of a material’s ability to store electrical energy in an electric field. Materials with higher Dk values have a greater capacity to store electrical energy, which can be beneficial in certain PCB applications.
Common High Dk PCB Materials
There are several types of high Dk PCB materials available, each with its own unique properties and advantages. Some of the most common high Dk PCB materials include:
-
Ceramic-filled PTFE: This material combines polytetrafluoroethylene (PTFE) with ceramic fillers, resulting in a high Dk value and excellent thermal stability.
-
High Dk epoxy: These materials are based on epoxy resin systems filled with high Dk ceramic powders, offering good processability and mechanical strength.
-
Polyimide: Polyimide-based high Dk materials offer excellent thermal stability and mechanical properties, making them suitable for high-temperature applications.
-
Polyphenylene oxide (PPO): PPO-based high Dk materials provide a balance of good electrical properties and mechanical strength.
Advantages of Using High Dk PCB Materials
Improved Signal Integrity
One of the primary benefits of using high Dk PCB materials is improved signal integrity. In high-speed digital circuits, signal integrity is crucial for ensuring reliable data transmission. High Dk materials can help reduce signal distortion and attenuation, leading to cleaner and more accurate signal propagation.
The improved signal integrity in high Dk PCBs is due to several factors:
-
Reduced dielectric loss: High Dk materials often have lower dielectric loss tangents (Df), which means less energy is dissipated as heat when an electrical signal passes through the material. This results in less signal attenuation and distortion.
-
Controlled impedance: High Dk materials allow for better control over the characteristic impedance of transmission lines on a PCB. By carefully designing the PCB layout and selecting the appropriate high Dk material, engineers can maintain consistent impedance throughout the signal path, minimizing reflections and signal distortion.
-
Shorter wavelengths: The wavelength of an electrical signal is inversely proportional to the square root of the dielectric constant. As a result, high Dk materials enable shorter wavelengths for a given frequency, allowing for more compact PCB designs without compromising signal integrity.
Enhanced Power Handling Capability
High Dk PCB materials also offer enhanced power handling capability compared to traditional FR-4 materials. This is particularly important in power electronics applications, such as switching power supplies, motor drives, and high-power RF circuits.
The improved power handling capability of high Dk PCBs is attributed to several factors:
-
Higher breakdown voltage: Many high Dk materials have higher dielectric breakdown voltages than FR-4, allowing them to withstand greater electrical stress without failure.
-
Better thermal conductivity: Some high Dk materials, particularly those filled with ceramic particles, have better thermal conductivity than FR-4. This allows for more efficient heat dissipation, reducing the risk of thermal damage to the PCB and its components.
-
Lower thermal expansion: High Dk materials often have lower coefficients of thermal expansion (CTE) than FR-4. This means they experience less dimensional change when subjected to temperature fluctuations, reducing the risk of mechanical stress and damage to the PCB and its components.
Miniaturization and Higher Component Density
High Dk PCB materials enable miniaturization and higher component density in PCB designs. This is because the shorter wavelengths associated with high Dk materials allow for smaller feature sizes and more compact layouts.
By using high Dk materials, PCB designers can:
-
Reduce trace widths and spacings: With shorter wavelengths, high Dk materials allow for narrower traces and smaller gaps between traces without compromising signal integrity. This enables more routing channels and higher component density on the PCB.
-
Decrease layer count: The ability to route more signals in a smaller area often means that fewer PCB layers are required to achieve the same functionality. This can lead to thinner, lighter, and more cost-effective PCB designs.
-
Implement advanced packaging technologies: High Dk materials are compatible with advanced packaging technologies, such as chip-on-board (COB), flip-chip, and ball grid array (BGA). These packaging techniques allow for higher component density and improved electrical performance compared to traditional through-hole and surface-mount technologies.
RF and Microwave Applications
High Dk PCB materials are particularly well-suited for RF and microwave applications, where signal integrity and power handling are critical. In these high-frequency applications, the benefits of high Dk materials are even more pronounced.
Some advantages of using high Dk PCBs in RF and microwave applications include:
-
Reduced wavelength: At high frequencies, the wavelength of electrical signals becomes very short. High Dk materials help to further reduce the wavelength, enabling the design of more compact RF and microwave circuits.
-
Improved impedance matching: Maintaining proper impedance matching is crucial in RF and microwave circuits to minimize signal reflections and ensure maximum power transfer. High Dk materials allow for better control over impedance, facilitating the design of well-matched circuits.
-
Enhanced antenna performance: High Dk materials can be used to design compact, high-performance antennas for RF and microwave applications. The shorter wavelengths enabled by high Dk materials allow for smaller antenna elements, making it possible to create arrays and other advanced antenna configurations in a limited space.
Challenges and Considerations
While high Dk PCB materials offer numerous benefits, there are also some challenges and considerations that designers must take into account when working with these materials.
Manufacturing Complexity
High Dk PCB materials can be more challenging to manufacture than traditional FR-4 laminates. Some of the manufacturing complexities include:
-
Specialized processing: High Dk materials may require specialized processing techniques, such as high-temperature lamination, controlled impedance routing, and advanced via formation methods. This can increase the cost and lead time of PCB fabrication.
-
Material availability: Not all PCB manufacturers have experience working with high Dk materials, and some materials may be less readily available than FR-4. This can limit supplier options and increase procurement costs.
-
Drilling and routing: Some high Dk materials, particularly those with ceramic fillers, can be more difficult to drill and route than FR-4. This can lead to increased wear on tools and slower production rates.
Cost Considerations
High Dk PCB materials are generally more expensive than traditional FR-4 laminates. The higher cost is due to several factors, including:
-
Raw material cost: The specialized components used in high Dk materials, such as ceramic fillers and high-performance resins, are more expensive than the materials used in FR-4.
-
Processing cost: The specialized processing techniques required for high Dk materials can increase the cost of PCB fabrication.
-
Lower demand: The demand for high Dk PCBs is lower than for FR-4 boards, which means that manufacturers may not benefit from the same economies of scale. This can contribute to higher prices for high Dk PCBs.
Despite the higher cost, the benefits of high Dk materials, such as improved signal integrity and power handling, can justify the investment in many applications.
Design Challenges
Designing with high Dk PCB materials can present some unique challenges compared to working with traditional FR-4 laminates. Some of these design challenges include:
-
Impedance control: While high Dk materials allow for better impedance control, designing controlled impedance traces can be more complex than with FR-4. Designers must carefully consider the dielectric constant and thickness of the material, as well as the width and spacing of the traces, to achieve the desired impedance.
-
Thermal management: Although some high Dk materials have better thermal conductivity than FR-4, designers must still carefully consider thermal management in their PCB layouts. This may involve the use of thermal vias, heat sinks, or other cooling techniques to dissipate heat effectively.
-
Material selection: With the wide range of high Dk materials available, designers must carefully select the appropriate material for their specific application. Factors to consider include the dielectric constant, loss tangent, thermal properties, mechanical strength, and cost.
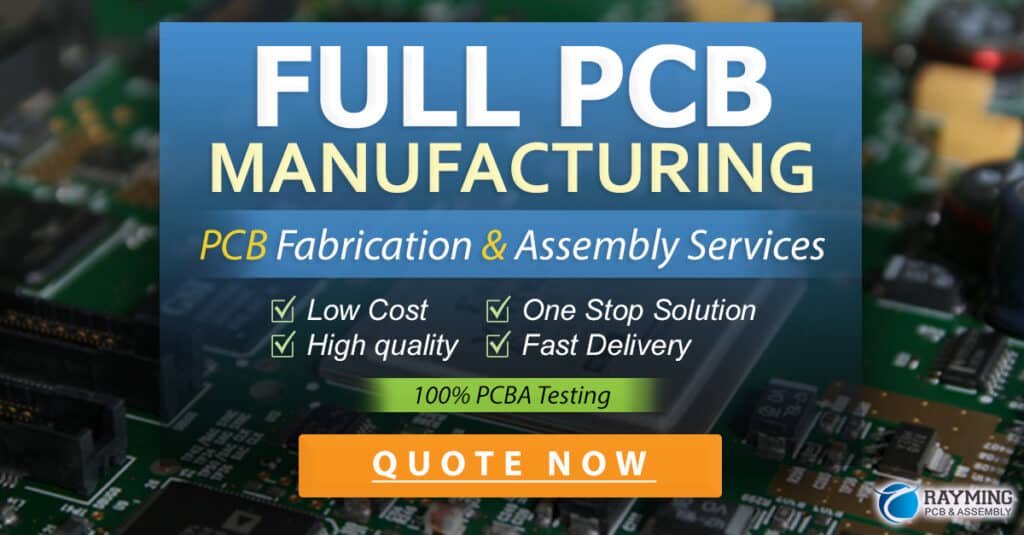
Applications of High Dk PCB Materials
High Dk PCB materials are used in a variety of applications where signal integrity, power handling, and miniaturization are critical. Some common applications include:
-
RF and microwave circuits: High Dk materials are widely used in the design of RF and microwave components, such as antennas, filters, couplers, and power amplifiers.
-
High-speed digital circuits: In applications such as high-speed networking, telecommunications, and data centers, high Dk PCBs help to maintain signal integrity and minimize signal distortion.
-
Power electronics: High Dk materials are used in power electronic applications, such as switching power supplies, motor drives, and renewable energy systems, due to their enhanced power handling capability and thermal stability.
-
Aerospace and defense: In aerospace and defense applications, where reliability and performance are paramount, high Dk PCBs are used to ensure robust signal transmission and power handling in harsh environments.
-
Medical equipment: High Dk materials are used in the design of advanced medical equipment, such as imaging systems and diagnostic devices, where signal integrity and miniaturization are essential.
Conclusion
High Dk PCB materials offer numerous benefits over traditional FR-4 laminates, including improved signal integrity, enhanced power handling capability, and the potential for miniaturization and higher component density. These advantages make high Dk materials an attractive choice for a wide range of applications, from RF and microwave circuits to high-speed digital systems and power electronics.
However, designing with high Dk materials also presents some challenges, such as manufacturing complexity, cost considerations, and unique design requirements. By carefully considering these factors and selecting the appropriate high Dk material for their specific application, PCB designers can unlock the full potential of these advanced materials and create high-performance, reliable electronic systems.
As the demand for faster, smaller, and more powerful electronic devices continues to grow, the use of high Dk PCB materials is likely to become increasingly common. By staying informed about the latest developments in high Dk materials and their applications, PCB designers and engineers can stay at the forefront of this exciting field and create innovative solutions for the electronic systems of tomorrow.
Frequently Asked Questions (FAQ)
-
What is the difference between high Dk and low Dk PCB materials?
High Dk PCB materials have a higher dielectric constant (typically greater than 4.5) compared to low Dk materials, which have a dielectric constant lower than 4.5. High Dk materials offer benefits such as improved signal integrity and power handling, while low Dk materials are often used in applications where lower dielectric loss and lower cost are priorities. -
Can high Dk PCB materials be used with standard PCB manufacturing processes?
In many cases, high Dk PCB materials can be used with standard PCB manufacturing processes, such as etching, drilling, and plating. However, some high Dk materials may require specialized processing techniques, such as high-temperature lamination or controlled impedance routing, which can increase manufacturing complexity and cost. -
How do I select the appropriate high Dk PCB material for my application?
When selecting a high Dk PCB material, consider factors such as the required dielectric constant, loss tangent, thermal properties, mechanical strength, and cost. Evaluate the specific requirements of your application, such as signal integrity, power handling, and environmental conditions, and consult with PCB material suppliers or manufacturers to determine the most suitable material. -
Are high Dk PCB materials more expensive than traditional FR-4 laminates?
Yes, high Dk PCB materials are generally more expensive than traditional FR-4 laminates. The higher cost is due to factors such as the specialized components used in high Dk materials, the need for specialized processing techniques, and lower demand compared to FR-4. However, the benefits of high Dk materials can justify the higher cost in applications where performance is critical. -
What are some common applications for high Dk PCB materials?
High Dk PCB materials are commonly used in applications where signal integrity, power handling, and miniaturization are important. Some examples include RF and microwave circuits, high-speed digital systems, power electronics, aerospace and defense applications, and advanced medical equipment.
Leave a Reply