Introduction to H-Bridge Full Wave Rectifiers
An H-bridge full wave rectifier is a crucial component in many electronic applications, particularly in power supply circuits. It is designed to convert alternating current (AC) into direct current (DC) by utilizing a specific arrangement of diodes and transformers. In this comprehensive guide, we will delve into the fundamentals of H-bridge full wave rectifiers, their design principles, and how to simulate their performance using popular software tools.
What is an H-Bridge Full Wave Rectifier?
An H-bridge full wave rectifier is a type of rectifier circuit that converts AC input voltage into DC output voltage. It is named “H-bridge” due to the arrangement of four diodes in an H-shaped configuration. This configuration allows the rectifier to produce a full wave rectified output, meaning that both the positive and negative half-cycles of the AC input are utilized to generate a unidirectional DC output.
Advantages of H-Bridge Full Wave Rectifiers
H-bridge full wave rectifiers offer several advantages over other types of rectifier circuits:
- Higher efficiency: By utilizing both half-cycles of the AC input, H-bridge full wave rectifiers achieve higher efficiency compared to half wave rectifiers.
- Smoother DC output: The full wave rectification process results in a smoother DC output with less ripple, reducing the need for extensive filtering.
- Improved power handling: H-bridge rectifiers can handle higher power levels compared to other rectifier topologies.
Components of an H-Bridge Full Wave Rectifier
To understand the design and simulation of an H-bridge full wave rectifier, it is essential to familiarize oneself with the key components that make up the circuit.
Diodes
Diodes are the primary components responsible for the rectification process in an H-bridge full wave rectifier. Four diodes are arranged in an H-shaped configuration, with two diodes conducting during each half-cycle of the AC input. The diodes used in the H-bridge must have a sufficient forward current rating and reverse voltage rating to withstand the maximum input voltage and current.
Transformers
Transformers play a crucial role in stepping down the AC input voltage to a suitable level for rectification. In an H-bridge full wave rectifier, a center-tapped transformer is commonly used. The center tap of the secondary winding serves as the common point for the rectified output, while the two outer taps are connected to the diodes.
Filter Capacitors
Filter capacitors are used to smooth out the ripple in the rectified DC output. The capacitor is connected in parallel with the load, storing energy during the peaks of the rectified waveform and releasing it during the valleys. The size of the filter capacitor depends on the desired level of ripple reduction and the load current requirements.
Load Resistance
The load resistance represents the device or circuit that the rectified DC output will power. It is important to consider the maximum current and voltage requirements of the load when designing the H-bridge full wave rectifier.
Designing an H-Bridge Full Wave Rectifier
Designing an H-bridge full wave rectifier involves several key steps and considerations. Let’s walk through the design process step by step.
Step 1: Determine Input and Output Specifications
Before starting the design, it is crucial to determine the input and output specifications of the rectifier. This includes the AC input voltage, frequency, and the desired DC output voltage and current. These specifications will guide the selection of components and the overall design of the circuit.
Step 2: Select the Transformer
The transformer is a critical component in the H-bridge full wave rectifier design. The primary winding of the transformer should be rated for the AC input voltage and frequency, while the secondary winding should provide the necessary voltage for rectification. A center-tapped transformer is typically used, with the secondary winding having a voltage rating twice that of the desired DC output voltage.
Step 3: Choose the Diodes
The diodes used in the H-bridge must be capable of handling the maximum forward current and reverse voltage of the circuit. The forward current rating of the diodes should be higher than the maximum load current, and the reverse voltage rating should be at least twice the peak voltage of the transformer’s secondary winding. Fast-recovery diodes or ultrafast diodes are commonly used in H-bridge rectifiers to minimize switching losses.
Step 4: Calculate Filter Capacitor Value
The filter capacitor value is determined based on the desired level of ripple reduction and the load current requirements. A larger capacitor value will result in a smoother DC output but will also increase the size and cost of the circuit. The capacitor value can be calculated using the following formula:
C = (I_load) / (2 × f × V_ripple)
Where:
– C is the capacitor value in farads (F)
– I_load is the maximum load current in amperes (A)
– f is the frequency of the AC input in hertz (Hz)
– V_ripple is the desired peak-to-peak ripple voltage in volts (V)
Step 5: Select the Load Resistance
The load resistance should be chosen based on the maximum current and voltage requirements of the device or circuit being powered by the rectifier. It is important to ensure that the rectifier can supply sufficient current to the load without exceeding the ratings of the components.
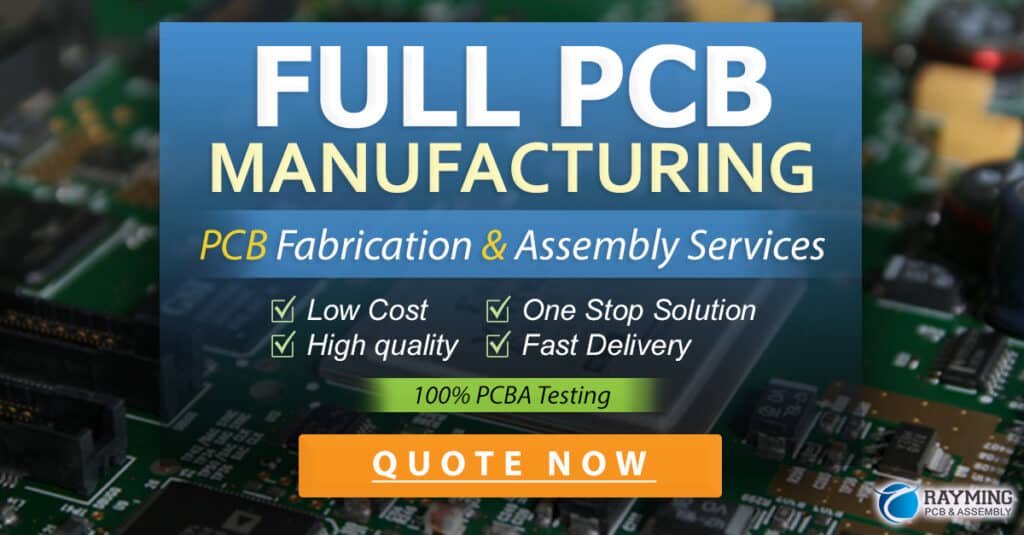
Simulating an H-Bridge Full Wave Rectifier
Simulation is an essential tool for verifying the design and performance of an H-bridge full wave rectifier before physical implementation. Popular simulation software, such as SPICE (Simulation Program with Integrated Circuit Emphasis) or Multisim, can be used to simulate the rectifier circuit.
Setting Up the Simulation
To set up the simulation, follow these steps:
- Create a new project in your chosen simulation software.
- Place the necessary components (diodes, transformer, filter capacitor, and load resistance) on the schematic canvas.
- Connect the components according to the H-bridge full wave rectifier topology.
- Set the values of the components based on your design calculations.
- Apply the AC input voltage source to the primary winding of the transformer.
Running the Simulation
Once the simulation is set up, you can run the simulation to observe the behavior of the H-bridge full wave rectifier. The simulation software will generate waveforms and data that can be analyzed to evaluate the performance of the circuit.
Analyzing the Simulation Results
When analyzing the simulation results, pay attention to the following key parameters:
- DC output voltage: Verify that the DC output voltage matches your design specifications.
- Ripple voltage: Check the peak-to-peak ripple voltage and ensure it is within acceptable limits.
- Diode currents: Observe the current waveforms through the diodes to ensure they are operating within their ratings.
- Load current: Verify that the rectifier can supply the required load current without exceeding component ratings.
Troubleshooting and Optimization
If the simulation results do not meet your design specifications or if issues are observed, you may need to troubleshoot and optimize the circuit. Common troubleshooting steps include:
- Checking component values and connections for accuracy.
- Adjusting component values (e.g., filter capacitor) to achieve the desired performance.
- Investigating alternative diode types or ratings if necessary.
- Modifying the transformer specifications if the output voltage or current is insufficient.
Practical Considerations and Applications
When implementing an H-bridge full wave rectifier in a practical application, there are several considerations to keep in mind.
PCB Layout and Component Placement
Proper PCB layout and component placement are crucial for the optimal performance of the H-bridge full wave rectifier. Consider the following guidelines:
- Minimize the trace lengths between components to reduce parasitic inductance and resistance.
- Provide adequate spacing between high-voltage components to prevent arcing or insulation breakdown.
- Use appropriate trace widths to handle the expected currents without excessive heating.
- Place the filter capacitor close to the rectifier output to minimize ripple and improve transient response.
Heatsinking and Thermal Management
The diodes and transformer in an H-bridge full wave rectifier dissipate power in the form of heat. Proper heatsinking and thermal management are essential to prevent overheating and ensure reliable operation. Consider the following:
- Use heatsinks with sufficient thermal dissipation capacity for the diodes.
- Provide adequate ventilation around the transformer to prevent heat buildup.
- Monitor the temperature of critical components during operation and take appropriate measures if overheating occurs.
Applications of H-Bridge Full Wave Rectifiers
H-bridge full wave rectifiers find applications in various fields, including:
- Power supplies: H-bridge rectifiers are commonly used in DC power supply circuits to convert AC mains voltage into DC voltage for electronic devices.
- Battery chargers: H-bridge rectifiers are employed in battery charging systems to convert AC input into DC voltage suitable for charging batteries.
- Motor drives: In motor drive applications, H-bridge rectifiers are used to convert AC voltage into DC voltage for controlling the speed and direction of DC motors.
- Renewable energy systems: H-bridge rectifiers are utilized in solar and wind energy systems to convert the generated AC voltage into DC voltage for storage or further processing.
Frequently Asked Questions (FAQ)
-
What is the difference between a half wave rectifier and a full wave rectifier?
A half wave rectifier utilizes only one half-cycle of the AC input, resulting in a pulsating DC output with significant ripple. In contrast, a full wave rectifier utilizes both half-cycles of the AC input, producing a more stable and smoother DC output with less ripple. -
Can an H-bridge full wave rectifier be used with a single-phase AC input?
Yes, an H-bridge full wave rectifier can be used with a single-phase AC input. The center-tapped transformer converts the single-phase AC input into a two-phase AC output, which is then rectified by the diodes in the H-bridge configuration. -
What is the purpose of the filter capacitor in an H-bridge full wave rectifier?
The filter capacitor serves to smooth out the ripple in the rectified DC output. It stores energy during the peaks of the rectified waveform and releases it during the valleys, reducing the voltage fluctuations and improving the quality of the DC output. -
How do I select the appropriate diodes for an H-bridge full wave rectifier?
When selecting diodes for an H-bridge full wave rectifier, consider the following factors: - Forward current rating: Choose diodes with a forward current rating higher than the maximum load current.
- Reverse voltage rating: Select diodes with a reverse voltage rating at least twice the peak voltage of the transformer’s secondary winding.
-
Recovery time: Use fast-recovery or ultrafast diodes to minimize switching losses and improve efficiency.
-
Can an H-bridge full wave rectifier be used for high-power applications?
Yes, H-bridge full wave rectifiers can be used for high-power applications. However, proper component selection, heatsinking, and thermal management become increasingly important as the power level increases. It may be necessary to use multiple diodes in parallel or employ specialized high-power rectifier modules to handle the required current and voltage ratings.
Conclusion
In this comprehensive guide, we have explored the fundamentals of H-bridge full wave rectifiers, their design principles, and simulation techniques. By understanding the components, design steps, and practical considerations involved in H-bridge rectifier circuits, you can effectively design and simulate these rectifiers for various applications.
Remember to carefully select components based on the input and output specifications, consider the thermal management aspects, and optimize the circuit through simulation and practical testing. With the knowledge gained from this guide, you are well-equipped to tackle H-bridge full wave rectifier design and simulation projects with confidence.
Happy designing and simulating!
Leave a Reply