What is ESD and Why is ESD Protection Important in PCB Design?
Electrostatic discharge (ESD) is a sudden flow of electricity between two electrically charged objects. It can be caused by direct contact or induced by an electrostatic field. ESD events can generate very high voltages, sometimes in excess of several kilovolts, but the duration is short, typically nanoseconds.
ESD poses a serious threat to electronic components and printed circuit boards (PCBs). The high voltage spikes can cause immediate catastrophic failures, like junction burnout or oxide breakdown in semiconductor devices. ESD can also cause latent damage that may escape factory testing but lead to early field failures.
With the continuous scaling of semiconductor technology and the prevalence of electronics in our daily lives, ESD protection has become a critical aspect of PCB design. Proper ESD protection circuit design helps to:
- Enhance the reliability and service life of electronic products
- Reduce warranty costs and customer returns
- Comply with industry ESD standards and regulations
- Improve customer satisfaction and brand reputation
Understanding the ESD Threat Models and Test Methods
To design effective ESD protection circuits, it’s important to understand the various ESD threat models and the corresponding test methods. The most common ESD models include:
Human Body Model (HBM)
HBM simulates the ESD event when a charged human body discharges to a grounded device. It is the most widely used model for component level ESD testing. The typical test circuit consists of a 100 pF capacitor discharging through a 1500 Ω resistor.
HBM Class | Voltage Range |
---|---|
0 | <250 V |
1A | 250 V to <500 V |
1B | 500 V to <1000 V |
1C | 1000 V to <2000 V |
2 | 2000 V to <4000 V |
3A | 4000 V to <8000 V |
3B | ≥8000 V |
Machine Model (MM)
MM represents the ESD from a charged machine or tool to a grounded device. It has a higher current and faster rise time compared to HBM. The test circuit typically uses a 200 pF capacitor and a 0.75 μH inductor.
Charged Device Model (CDM)
CDM simulates the event when a charged device discharges to a grounded object. It features very high peak current (up to tens of amperes) but short duration (nanoseconds). CDM testing is component-level and uses a specialized tester.
CDM Class | Voltage Range |
---|---|
C1 | <125 V |
C2 | 125 V to <250 V |
C3 | 250 V to <500 V |
C4 | 500 V to <1000 V |
C5 | 1000 V to <1500 V |
C6 | 1500 V to <2000 V |
C7 | ≥2000 V |
System-Level ESD
System-level ESD tests, like IEC 61000-4-2, evaluate the ESD immunity of the final products. They involve applying ESD pulses to various points on the product enclosure and checking for malfunctions or failures.
On-Chip vs. Off-Chip ESD Protection
ESD protection can be implemented on-chip and/or off-chip. The choice depends on factors like the required protection level, system constraints, cost, and board space.
On-Chip ESD Protection
On-chip protection refers to the ESD structures built into the IC by the chip manufacturer. These structures are designed to provide a low-impedance discharge path and clamp the high voltage during an ESD event. Common on-chip ESD devices include:
- Diodes
- Bipolar junction transistors (BJTs)
- Grounded-gate NMOS (GGNMOS)
- Silicon controlled rectifiers (SCRs)
While on-chip protection offers the first line of defense, it may not be sufficient for all applications. High-speed interfaces, like USB, HDMI, etc., often require additional off-chip protection.
Off-Chip ESD Protection
Off-chip protection is implemented on the PCB using discrete components or integrated protection devices. It supplements the on-chip protection and provides a higher level of robustness. Key advantages of off-chip protection include:
- Ability to handle higher ESD levels
- Flexibility in component selection and placement
- Easier to replace or upgrade
- Less dependence on IC process technology
Off-chip protection components can be divided into three main categories:
- Voltage suppression devices: Metal oxide varistors (MOVs), transient voltage suppressors (TVSs), Zener diodes, etc.
- Current limiting devices: Series resistors, ferrite beads, inductors, etc.
- Filters: Common mode chokes, LC filters, π filters, T filters, etc.
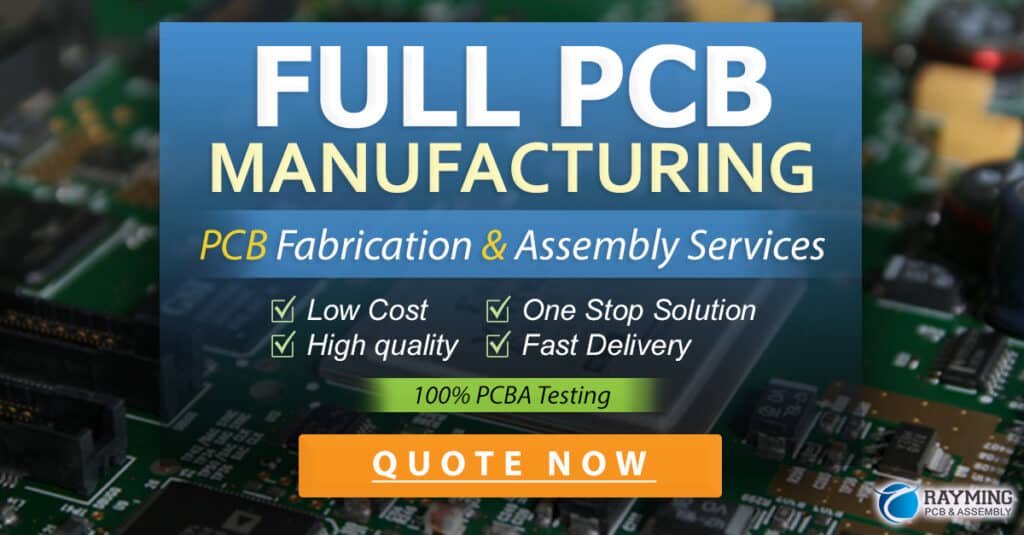
ESD Protection Device Selection and Placement Guidelines
Proper selection and placement of ESD protection devices are crucial for achieving optimal protection performance. Here are some key guidelines:
TVS Diode Selection
TVS diodes are the most commonly used off-chip ESD protection devices. When selecting a TVS diode, consider the following parameters:
- Stand-off voltage: Should be higher than the maximum operating voltage of the protected line.
- Breakdown voltage: Should be lower than the failure voltage of the protected component.
- Clamping voltage: Should be low enough to prevent damage to the protected component.
- Peak pulse current: Should exceed the expected ESD current level.
- Capacitance: Should be minimized to reduce signal attenuation and maintain signal integrity.
Protection Device Placement
The placement of ESD protection devices on the PCB is equally important. Follow these guidelines:
- Place the protection devices as close to the protected pins as possible to minimize the discharge path.
- For multi-pin interfaces, use a “star” topology with the protection devices placed at the center.
- Avoid placing protection devices near high-speed signal traces to prevent coupling.
- Use ground planes to provide a low-impedance return path for ESD currents.
- For connectors, place the protection devices near the connector pins and before any series elements like resistors or ferrites.
PCB Layout Techniques for Improved ESD Immunity
In addition to using protection devices, proper PCB layout techniques can greatly enhance the ESD immunity of the system. Some key techniques include:
Grounding and Shielding
- Use a solid ground plane to minimize the ground impedance and provide a low-impedance return path for ESD currents.
- Implement a single-point grounding scheme to avoid ground loops and potential differences.
- Use shielding techniques, like shielding cans or conductive gaskets, to protect sensitive components from radiated ESD fields.
Trace Routing and Spacing
- Keep sensitive signal traces away from the board edges and connectors to minimize direct coupling of ESD.
- Maintain adequate spacing between traces to reduce crosstalk and coupling.
- Use guard rings or guard traces to isolate sensitive traces from noisy or ESD-prone areas.
Component Placement and Orientation
- Place sensitive components away from the board edges and connectors.
- Orient components to minimize the coupling of ESD fields.
- Use physical barriers, like slots or cut-outs, to isolate sensitive areas from the rest of the board.
Filtering and Transient Suppression
- Use filters, like ferrites or RC filters, to suppress high-frequency ESD transients.
- Implement transient suppression techniques, like adding decoupling capacitors or using TVS diodes, at the power supply inputs.
Case Studies and Application Examples
To illustrate the application of ESD protection techniques, let’s look at a few case studies:
USB Interface Protection
USB interfaces are susceptible to ESD due to their exposed connectors and high-speed data lines. A typical USB ESD protection scheme includes:
- TVS diodes on the VBUS, D+, and D- lines. The diodes should have low capacitance (< 1 pF) to minimize signal distortion.
- A series resistor (10-100 Ω) on the VBUS line to limit the inrush current during plug-in.
- A ferrite bead on the VBUS line to suppress high-frequency transients.
- Proper grounding of the USB connector shield to the PCB ground plane.
Ethernet Port Protection
Ethernet ports can be exposed to cable discharge events and require robust ESD protection. A common protection scheme for Ethernet includes:
- A multi-layer varistor (MLV) or a gas discharge tube (GDT) on each differential pair for common-mode protection.
- A TVS diode array for differential-mode protection. The diodes should have low capacitance and fast response time.
- Common-mode chokes on each differential pair to suppress common-mode noise and ESD.
- A series resistor or ferrite bead on the transformer center tap to limit the current during an ESD event.
LCD Display Protection
LCD displays are prone to ESD damage due to their large surface area and exposed electrodes. To protect an LCD display:
- Use a transparent conductive coating, like indium tin oxide (ITO), on the display surface to dissipate the ESD charge.
- Implement a conductive frame or bezel around the display to shield it from ESD fields.
- Use TVS diodes or varistors on the display driver lines to clamp the ESD voltage.
- Ensure proper grounding of the display chassis and the PCB ground plane.
FAQ
1. What is the difference between ESD and EMI/EMC?
ESD (Electrostatic Discharge) refers to the sudden flow of electricity between two objects at different electrical potentials. It is a single, fast, high-current event. EMI (Electromagnetic Interference) and EMC (Electromagnetic Compatibility), on the other hand, deal with the ongoing interference between electronic devices and their ability to operate without affecting each other. EMI/EMC issues are typically associated with radiated or conducted noise over a wide frequency range.
2. Can I use a regular diode for ESD protection?
While regular diodes can provide some level of ESD protection, they are not optimized for this purpose. ESD protection diodes, like TVS (Transient Voltage Suppression) diodes, are specifically designed to handle high-voltage, high-current transients. They have a faster response time, lower clamping voltage, and higher power dissipation capability compared to regular diodes.
3. What is the role of series resistors in ESD protection?
Series resistors are often used in conjunction with ESD protection devices to limit the current during an ESD event. They help to absorb the ESD energy and reduce the stress on the protected components. However, the value of the series resistor should be carefully chosen to balance the protection level and the impact on the signal integrity.
4. How do I choose the right TVS diode for my application?
When selecting a TVS diode, consider the following factors:
1. Stand-off voltage: It should be higher than the maximum operating voltage of the protected line.
2. Breakdown voltage: It should be lower than the failure voltage of the protected component.
3. Clamping voltage: It should be low enough to prevent damage to the protected component.
4. Peak pulse current: It should exceed the expected ESD current level.
5. Capacitance: It should be minimized to reduce signal attenuation and maintain signal integrity.
5. Can ESD protection be tested during PCB development?
Yes, ESD protection can and should be tested during PCB development. Various tests can be performed, such as:
1. ESD gun testing: Applying ESD pulses to the PCB using an ESD gun and checking for failures.
2. Transmission line pulse (TLP) testing: Injecting fast, high-current pulses into the protection devices and measuring their response.
3. System-level ESD testing: Testing the final product according to standards like IEC 61000-4-2 to ensure compliance.
Early testing helps to identify and fix any weaknesses in the ESD protection design before the product is released to the market.
Conclusion
ESD protection is a critical aspect of PCB design that ensures the reliability and longevity of electronic products. By understanding the ESD threat models, selecting appropriate protection devices, and implementing proper PCB layout techniques, designers can create robust systems that can withstand ESD events.
When designing ESD protection circuits, it’s important to consider both on-chip and off-chip protection measures. TVS diodes are the most commonly used off-chip protection devices, and their selection and placement are crucial for optimal performance. PCB layout techniques, such as grounding, shielding, trace routing, and component placement, also play a significant role in enhancing ESD immunity.
Comprehensive ESD testing during PCB development helps to validate the protection design and ensure compliance with industry standards. By following best practices and continuously improving ESD protection strategies, designers can create products that are reliable, safe, and meet the evolving needs of the market.
Leave a Reply