Introduction to Power Distribution PCBs
Power distribution PCBs (Printed Circuit Boards) are essential components in electronic systems, responsible for efficiently distributing power from the source to various components on the board. Designing a reliable and efficient power distribution PCB requires careful consideration of several factors, such as current and voltage requirements, component placement, and thermal management.
In this comprehensive guide, we will delve into the best practices and techniques for designing power distribution PCBs, ensuring that your electronic projects are robust, reliable, and perform optimally.
Understanding the Basics of Power Distribution
Voltage and Current Requirements
Before starting your power distribution PCB design, it is crucial to determine the voltage and current requirements of your electronic system. This information will help you select the appropriate components, such as voltage regulators, capacitors, and connectors, and design the PCB layout accordingly.
Voltage Levels
Common voltage levels in electronic systems include:
- 3.3V: Used for low-power digital logic and microcontrollers
- 5V: Commonly used for USB devices and older digital logic
- 12V: Often used for motors, power supplies, and lighting systems
- 24V: Used in industrial control systems and some automotive applications
Current Requirements
To calculate the current requirements for your power distribution PCB, follow these steps:
- Identify the current consumption of each component in your system
- Add a safety margin (typically 20-30%) to account for any unexpected current spikes
- Sum up the current requirements of all components to determine the total current draw
Voltage Regulation
Voltage regulators play a vital role in power distribution PCBs by maintaining a stable voltage level for the connected components. There are two main types of voltage regulators:
-
Linear Regulators: These regulators provide a simple and cost-effective solution for low-power applications. However, they are less efficient and generate more heat compared to switching regulators.
-
Switching Regulators: These regulators offer higher efficiency and are suitable for high-power applications. They are more complex than linear regulators and may introduce noise into the system, requiring careful design considerations.
PCB Layout Considerations
Component Placement
Proper component placement is essential for optimizing power distribution and minimizing noise interference. Follow these guidelines when placing components on your power distribution PCB:
- Place voltage regulators close to the power input connector to minimize voltage drop
- Keep sensitive analog components away from noisy digital components
- Use ground planes to provide a low-impedance return path for currents
- Arrange components in a logical flow, following the power distribution path
Trace Width and Thickness
The width and thickness of PCB traces directly impact their current-carrying capacity and voltage drop. To ensure optimal power distribution, consider the following:
- Use wider traces for high-current paths to minimize voltage drop and heat generation
- Calculate the appropriate trace width based on the maximum current requirements using online tools or PCB design software
- Consider using thicker copper layers (e.g., 2 oz or 4 oz) for high-current applications
Vias and Connectors
Vias and connectors are critical components in power distribution PCBs, as they allow current to flow between layers and connect the PCB to external devices. When designing vias and selecting connectors, keep these factors in mind:
- Use multiple vias in parallel to increase current-carrying capacity and reduce inductance
- Select connectors with adequate current ratings and low contact resistance
- Place vias and connectors strategically to minimize voltage drop and improve power distribution efficiency
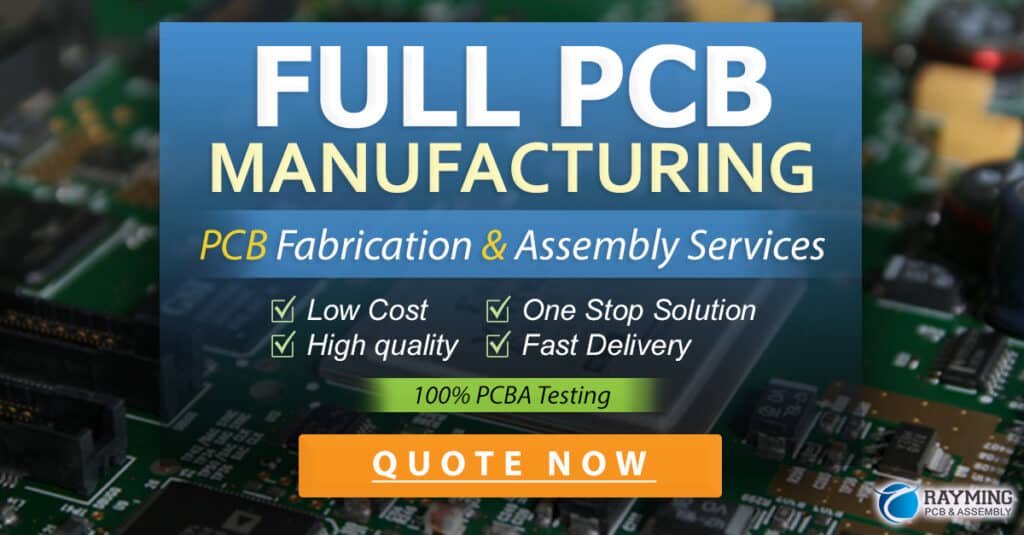
Thermal Management
Effective thermal management is crucial for ensuring the long-term reliability and performance of your power distribution PCB. Overheating can lead to component failure, reduced efficiency, and even fire hazards.
Heat Sinks and Thermal Pads
Heat sinks and thermal pads are commonly used to dissipate heat generated by power components, such as voltage regulators and power transistors. When incorporating heat sinks and thermal pads into your design, consider the following:
- Select heat sinks with appropriate thermal resistance and size for your components
- Use thermal pads or thermal adhesive to ensure proper contact between components and heat sinks
- Place heat sinks in areas with adequate airflow to facilitate heat dissipation
PCB Copper Pours
Copper pours are large areas of exposed copper on the PCB that help dissipate heat and improve power distribution. To effectively use copper pours in your design:
- Create large copper pours on both sides of the PCB, connected to ground or power planes
- Use thermal vias to transfer heat from the top layer to the bottom layer copper pour
- Ensure adequate spacing between copper pours and signal traces to avoid noise interference
Testing and Verification
Once your power distribution PCB design is complete, it is essential to thoroughly test and verify its performance before moving to production. This process helps identify and address any issues related to power integrity, signal quality, and thermal management.
Power Integrity Testing
Power integrity testing involves measuring voltage levels, ripple, and noise at various points on the PCB to ensure stable and clean power delivery. Use the following techniques to test power integrity:
- Measure voltage levels at the input and output of voltage regulators using a digital multimeter
- Use an oscilloscope to measure ripple and noise on power rails
- Verify that voltage levels remain within acceptable limits under various load conditions
Signal Integrity Testing
Signal integrity testing ensures that signals are transmitted accurately and reliably across the PCB without excessive distortion or interference. To test signal integrity:
- Use an oscilloscope to measure signal waveforms at critical points on the PCB
- Check for signal reflections, crosstalk, and other signal integrity issues
- Verify that signal levels and timing meet the requirements of your electronic system
Thermal Testing
Thermal testing helps verify that your power distribution PCB can effectively dissipate heat and operate within safe temperature limits. To conduct thermal testing:
- Use a thermal imaging camera or temperature sensors to measure the temperature of critical components and PCB areas
- Monitor temperature under various load conditions and ambient temperatures
- Ensure that component temperatures remain within their specified operating ranges
Best Practices for Power Distribution PCB Design
To optimize your power distribution PCB design and ensure reliable performance, follow these best practices:
- Use a star grounding topology to minimize ground loops and noise interference
- Implement proper decoupling capacitors near power pins of ICs to reduce high-frequency noise
- Use separate power and ground planes for analog and digital sections of the PCB
- Minimize the distance between power components and their decoupling capacitors
- Use solid ground planes instead of thin traces to provide a low-impedance return path
- Avoid running signal traces parallel to power traces to reduce crosstalk
- Use appropriate fuse ratings and protection circuits to safeguard against overcurrent and overvoltage conditions
FAQ
1. What is the difference between a power distribution PCB and a regular PCB?
A power distribution PCB is specifically designed to efficiently distribute power from the source to various components on the board, while a regular PCB focuses on the overall functionality of the electronic system. Power distribution PCBs typically have thicker copper layers, wider traces, and dedicated power and ground planes to handle higher currents and minimize voltage drop.
2. How do I select the appropriate voltage regulator for my power distribution PCB?
When selecting a voltage regulator, consider the following factors:
- Input and output voltage levels
- Maximum load current
- Efficiency requirements
- Thermal performance
- Cost and availability
Linear regulators are suitable for low-power applications with minimal heat generation, while switching regulators are more efficient and can handle higher power levels.
3. What is the importance of decoupling capacitors in power distribution PCBs?
Decoupling capacitors play a crucial role in reducing high-frequency noise and maintaining stable voltage levels on power rails. They act as local energy reservoirs, providing a low-impedance path for high-frequency currents and preventing noise from propagating throughout the system. Placing decoupling capacitors close to the power pins of ICs helps minimize the effects of power supply noise on sensitive components.
4. How can I minimize voltage drop in my power distribution PCB?
To minimize voltage drop in your power distribution PCB, consider the following techniques:
- Use wider traces for high-current paths
- Minimize the distance between power components and their loads
- Use thicker copper layers (e.g., 2 oz or 4 oz) for power traces
- Implement dedicated power and ground planes
- Use multiple vias in parallel to reduce resistance and inductance
By reducing voltage drop, you ensure that components receive the required voltage levels for optimal performance and reliability.
5. What are some common mistakes to avoid when designing power distribution PCBs?
Some common mistakes to avoid when designing power distribution PCBs include:
- Underestimating current requirements and using undersized traces
- Neglecting thermal management and allowing components to overheat
- Failing to use proper decoupling capacitors or placing them too far from ICs
- Routing high-current traces near sensitive analog components
- Overlooking the importance of ground planes and proper grounding techniques
By being aware of these common pitfalls and following best practices, you can create robust and reliable power distribution PCBs for your electronic projects.
Conclusion
Designing a power distribution PCB requires careful consideration of various factors, including voltage and current requirements, component placement, thermal management, and testing. By understanding the basics of power distribution, implementing proper PCB layout techniques, and following best practices, you can create reliable and efficient power distribution solutions for your electronic systems.
Remember to thoroughly test and verify your power distribution PCB design before moving to production, ensuring that it meets the required specifications and performs optimally under various operating conditions. With the knowledge and techniques outlined in this article, you can confidently tackle your next power distribution PCB project and achieve excellent results.
Component | Key Considerations |
---|---|
Voltage Regulators | – Select appropriate type (linear or switching) based on power requirements |
– Consider efficiency, thermal performance, and noise | |
Decoupling Capacitors | – Place close to IC power pins |
– Use appropriate values and types to reduce high-frequency noise | |
Traces | – Use wider traces for high-current paths |
– Minimize voltage drop by reducing trace length and increasing thickness | |
Ground Planes | – Implement solid ground planes for low-impedance return paths |
– Separate analog and digital ground planes to reduce noise | |
Connectors | – Select connectors with adequate current ratings and low contact resistance |
– Place connectors strategically to minimize voltage drop |
By focusing on these key components and their associated considerations, you can create a robust and efficient power distribution PCB that meets the needs of your electronic system.
Leave a Reply