Introduction to Signal Integrity Analysis
Signal integrity analysis is a crucial aspect of PCB design that ensures the proper functioning and reliability of electronic systems. It involves the study and optimization of electrical signals as they propagate through interconnects, such as traces, vias, and connectors, on a printed circuit board (PCB). With the ever-increasing speed and complexity of modern electronic devices, signal integrity analysis has become a critical step in the PCB design process.
Why is Signal Integrity Analysis Important?
Signal integrity issues can lead to various problems in electronic systems, including:
- Signal distortion and degradation
- Crosstalk and electromagnetic interference (EMI)
- Timing issues and synchronization errors
- Reduced system performance and reliability
By addressing these issues early in the design stage, signal integrity analysis helps to minimize the risk of costly redesigns, manufacturing delays, and product failures.
Key Concepts in Signal Integrity Analysis
To effectively perform signal integrity analysis, it is essential to understand the following key concepts:
1. Transmission Lines
Transmission lines are the pathways that carry electrical signals between components on a PCB. At high frequencies, the behavior of these lines becomes more complex, and they must be treated as distributed elements with impedance, delay, and loss characteristics.
2. Impedance Matching
Impedance matching is the practice of ensuring that the impedance of the source, transmission line, and load are matched to minimize signal reflections and distortions. Proper impedance matching is critical for maintaining signal integrity in high-speed designs.
3. Reflections and Terminations
When a signal encounters an impedance mismatch, a portion of the signal is reflected back to the source, causing distortions and ringing. Termination techniques, such as series termination and parallel termination, are used to absorb these reflections and improve signal quality.
4. Crosstalk
Crosstalk is the unintended coupling of signals between adjacent traces or layers on a PCB. It can cause signal distortion, noise, and interference, leading to system malfunctions. Crosstalk can be minimized through proper trace spacing, shielding, and layer stack-up design.
5. Electromagnetic Compatibility (EMC)
EMC refers to the ability of an electronic system to function correctly in its electromagnetic environment without causing or being susceptible to electromagnetic interference. Signal integrity analysis plays a vital role in ensuring EMC compliance by minimizing EMI and susceptibility to external noise sources.
Tools and Techniques for Signal Integrity Analysis
Several tools and techniques are used in signal integrity analysis to simulate, measure, and optimize the performance of PCB designs:
1. SPICE Simulation
SPICE (Simulation Program with Integrated Circuit Emphasis) is a widely used tool for simulating the electrical behavior of circuits and interconnects. It allows designers to model transmission lines, terminations, and other signal integrity elements to predict and optimize system performance.
2. Time-Domain Reflectometry (TDR)
TDR is a measurement technique that uses high-speed pulses to characterize the impedance and reflections of transmission lines. It helps to identify impedance discontinuities, trace length mismatches, and other signal integrity issues.
3. Vector Network Analyzer (VNA)
A VNA is an instrument that measures the scattering parameters (S-parameters) of a network, providing information about its frequency response, impedance, and loss characteristics. VNAs are essential for characterizing high-frequency components, such as connectors, filters, and antennas.
4. Eye Diagrams
Eye diagrams are graphical representations of the quality and stability of digital signals. They display the overlapped waveforms of a signal, allowing designers to assess parameters such as jitter, rise/fall times, and signal-to-noise ratio (SNR).
5. Electromagnetic Field Solvers
Electromagnetic field solvers, such as finite-element method (FEM) and method of moments (MoM), are used to simulate the electromagnetic behavior of PCBs and packages. They help to analyze issues such as crosstalk, EMI, and antenna performance.
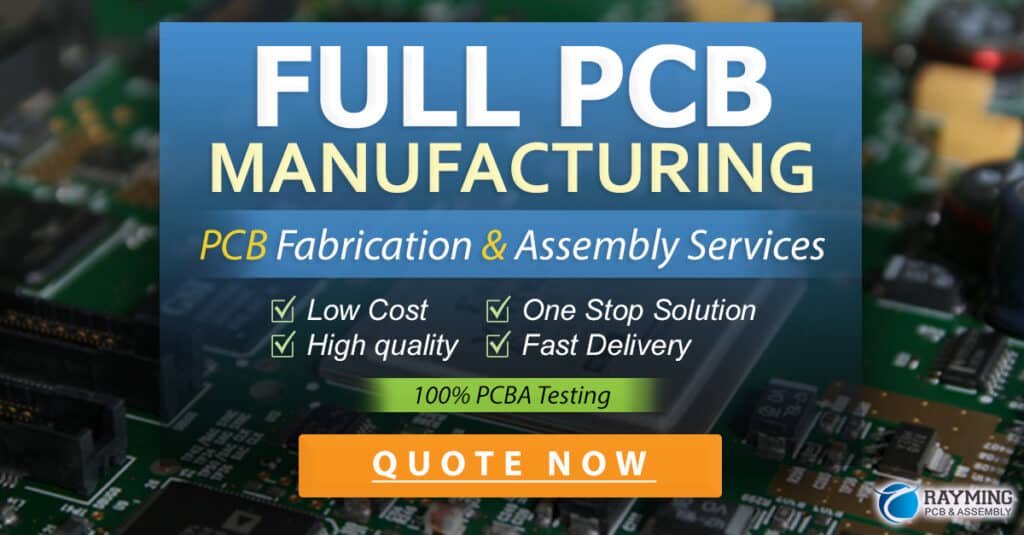
Best Practices for Signal Integrity Analysis
To ensure the success of your signal integrity analysis efforts, consider the following best practices:
1. Start Early in the Design Process
Signal integrity analysis should be integrated into the early stages of the PCB design process to identify and address potential issues before they become costly to fix. By collaborating with signal integrity experts from the beginning, you can optimize your design for performance, reliability, and manufacturability.
2. Use Accurate Models and Data
The accuracy of your signal integrity simulations depends on the quality of the models and data used. Ensure that you have accurate models for your components, materials, and interconnects, and verify their performance through measurements and validation.
3. Follow Design Guidelines and Standards
Adhering to established design guidelines and standards, such as those provided by IPC (Association Connecting Electronics Industries), can help to minimize signal integrity issues and ensure the compatibility and reliability of your PCB design.
4. Perform Sensitivity Analysis
Sensitivity analysis involves studying the impact of design parameters, such as trace width, spacing, and dielectric thickness, on signal integrity. By identifying the most critical parameters and their optimal ranges, you can make informed design decisions and trade-offs.
5. Validate and Test Your Design
After completing your signal integrity simulations, it is crucial to validate and test your PCB design through measurements and prototyping. This helps to verify the accuracy of your simulations, identify any unforeseen issues, and ensure that your design meets its performance and reliability targets.
Common Signal Integrity Issues and Their Solutions
Despite the best efforts in signal integrity analysis, some common issues may still arise in PCB designs. Here are a few examples and their potential solutions:
1. Impedance Mismatch
Problem: Impedance mismatches can cause signal reflections, distortions, and reduced signal quality.
Solution: Ensure proper impedance matching by designing transmission lines with controlled impedance and using appropriate termination techniques, such as series or parallel termination.
2. Crosstalk
Problem: Crosstalk between adjacent traces can lead to signal distortion, noise, and interference.
Solution: Minimize crosstalk by increasing the spacing between traces, using guard traces or ground planes, and optimizing the layer stack-up for better signal isolation.
3. EMI and EMC Issues
Problem: EMI and EMC problems can cause system malfunctions, regulatory compliance failures, and interference with other devices.
Solution: Implement EMI mitigation techniques, such as shielding, filtering, and proper grounding, and follow EMC design guidelines to ensure compliance with relevant standards.
4. Timing and Synchronization Errors
Problem: Timing and synchronization issues can occur due to signal delays, skew, and jitter, leading to system failures and data corruption.
Solution: Perform timing analysis to ensure that all signals meet their required timing constraints, and use techniques such as delay matching, clock distribution, and synchronization to minimize timing errors.
FAQs
- What is the difference between signal integrity and power integrity?
-
Signal integrity focuses on the quality and stability of electrical signals as they propagate through interconnects, while power integrity deals with the distribution and regulation of power supplies to ensure stable and clean power delivery to components.
-
How does the rise time of a signal affect signal integrity?
-
Faster rise times can exacerbate signal integrity issues, such as reflections, crosstalk, and EMI, as they contain higher-frequency components that are more susceptible to these problems. It is essential to consider the rise time of signals when designing for signal integrity.
-
What is the role of a signal integrity engineer?
-
A signal integrity engineer is responsible for analyzing, simulating, and optimizing the electrical performance of PCBs and systems to ensure the proper functioning and reliability of electronic devices. They work closely with PCB designers, hardware engineers, and other stakeholders to identify and mitigate signal integrity issues.
-
How can I learn more about signal integrity analysis?
-
There are various resources available to learn about signal integrity analysis, including books, online courses, webinars, and conferences. Some popular books include “High-Speed Digital Design: A Handbook of Black Magic” by Howard Johnson and Martin Graham, and “Signal Integrity: Simplified” by Eric Bogatin. Online resources, such as the Signal Integrity Journal and the Mentor Graphics Signal Integrity Academy, also provide valuable information and training.
-
What are some advanced topics in signal integrity analysis?
- Advanced topics in signal integrity analysis include:
- Jitter analysis and decomposition
- Channel equalization and signal conditioning
- Power-aware signal integrity analysis
- Electromagnetic band-gap (EBG) structures for signal integrity improvement
- Multiphysics simulation, incorporating thermal and mechanical effects on signal integrity
Conclusion
Signal integrity analysis is a critical aspect of PCB design that ensures the proper functioning and reliability of electronic systems. By understanding the key concepts, tools, and techniques involved in signal integrity analysis, and following best practices and guidelines, you can effectively identify and mitigate signal integrity issues in your PCB designs.
As the complexity and speed of electronic devices continue to increase, the importance of signal integrity analysis will only grow. By staying up-to-date with the latest advancements and techniques in this field, you can create robust, high-performance PCBs that meet the demands of today’s challenging applications.
Leave a Reply