Introduction to PCB Parameters
Printed Circuit Boards (PCBs) are the backbone of modern electronics. They provide a platform for mounting and interconnecting electronic components, enabling the creation of complex circuits and systems. To ensure that a PCB functions as intended, it is crucial to understand and control the various parameters that govern its design and fabrication. In this article, we will explore the basic PCB parameters that every engineer and designer should be familiar with.
Key PCB Parameters
1. Board Size and Thickness
The size and thickness of a PCB are fundamental parameters that determine its physical characteristics and performance. The board size is typically defined by its length and width, measured in inches or millimeters. The thickness of a PCB is measured in mils (thousandths of an inch) or millimeters.
Common PCB thicknesses include:
Thickness (mils) | Thickness (mm) | Application |
---|---|---|
31.5 | 0.8 | Single-sided and double-sided boards |
39.4 | 1.0 | Double-sided and multilayer boards |
62.9 | 1.6 | Multilayer boards |
94.5 | 2.4 | High-power and high-reliability boards |
Choosing the appropriate board size and thickness depends on factors such as the available space, component sizes, and the intended application of the PCB.
2. Copper Thickness
Copper thickness refers to the thickness of the copper layer on the PCB, which is responsible for carrying electrical signals and providing a conductive path for current flow. Copper thickness is typically measured in ounces per square foot (oz/ft²) or microns (µm).
Common copper thicknesses include:
Copper Thickness (oz/ft²) | Copper Thickness (µm) |
---|---|
0.5 | 17.5 |
1 | 35 |
2 | 70 |
3 | 105 |
Thicker copper layers offer lower resistance and higher current-carrying capacity, making them suitable for power-hungry applications and high-speed signals. However, thicker copper also increases the weight and cost of the PCB.
3. Trace Width and Spacing
Trace width and spacing are critical parameters that determine the electrical characteristics and signal integrity of a PCB. Trace width refers to the width of the conductive paths on the PCB, while spacing refers to the distance between adjacent traces.
Factors influencing trace width and spacing include:
- Current-carrying capacity
- Signal integrity
- Impedance matching
- Manufacturing capabilities
Smaller trace widths and tighter spacing allow for higher component density and more compact designs. However, they also increase the manufacturing complexity and cost of the PCB.
4. Drill Sizes and Hole Tolerances
Drill sizes and hole tolerances are essential parameters for creating vias and mounting holes on a PCB. Vias are used to connect different layers of a multilayer PCB, while mounting holes are used to attach components and provide mechanical support.
Common drill sizes include:
Drill Size (mils) | Drill Size (mm) |
---|---|
10 | 0.254 |
12 | 0.305 |
16 | 0.406 |
20 | 0.508 |
Hole tolerances define the acceptable variation in hole size and position. Tighter tolerances ensure better alignment and reliability but also increase manufacturing costs.
5. Solder Mask and Silkscreen
Solder mask and silkscreen are additional layers applied to the PCB to improve its functionality and usability. Solder mask is a protective coating that covers the copper traces, preventing accidental short circuits and protecting the board from environmental factors. Silkscreen is a printed layer that contains text, symbols, and component outlines, aiding in the assembly and identification of components on the PCB.
Solder mask and silkscreen parameters include:
- Color (e.g., green, red, blue, black, white)
- Thickness
- Clearance from pads and vias
- Minimum font size for silkscreen text
PCB Material Selection
The choice of PCB material is another crucial parameter that affects the performance, reliability, and cost of the final product. The most common PCB material is FR-4, a glass-reinforced epoxy laminate. However, other materials may be used depending on the specific requirements of the application.
Common PCB materials include:
- FR-4: General-purpose, cost-effective, and widely available
- High-Tg FR-4: Improved thermal stability and suitable for lead-free soldering processes
- Polyimide: High-temperature resistance and flexibility
- Rogers materials: Low dielectric constant and loss, suitable for high-frequency applications
- Aluminum: Excellent thermal conductivity for heat dissipation
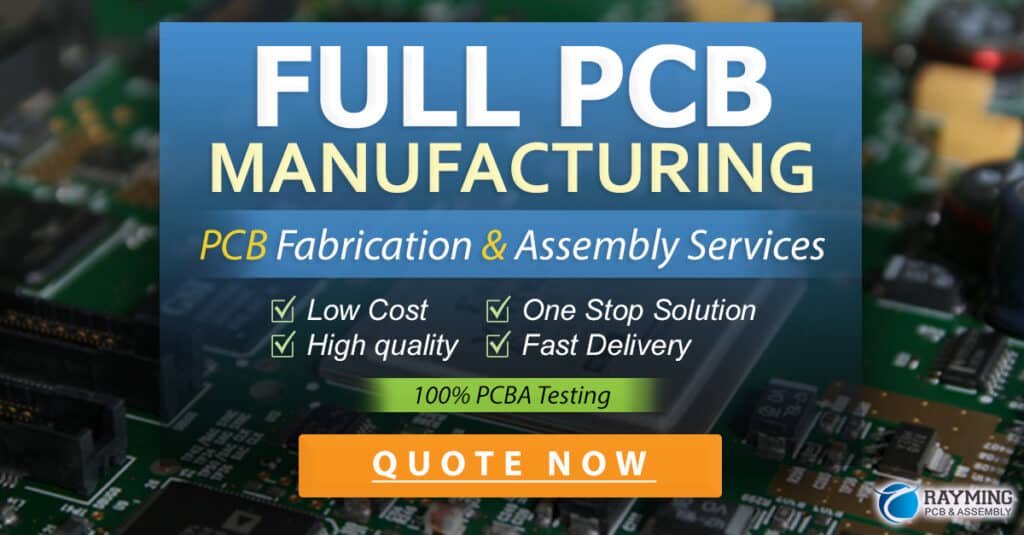
PCB Layer Stack-up
The layer stack-up of a PCB refers to the arrangement of copper layers, insulating layers, and other materials that make up the board. The choice of layer stack-up depends on factors such as signal integrity, power distribution, and manufacturing constraints.
Common layer stack-ups include:
- Single-sided: One copper layer on one side of the substrate
- Double-sided: Two copper layers, one on each side of the substrate
- Multilayer: Three or more copper layers, separated by insulating layers
Proper layer stack-up design is essential for maintaining signal integrity, minimizing crosstalk, and ensuring reliable power distribution.
Frequently Asked Questions (FAQ)
1. What is the difference between a single-sided and double-sided PCB?
A single-sided PCB has copper traces on only one side of the substrate, while a double-sided PCB has copper traces on both sides. Double-sided PCBs offer more design flexibility and higher component density compared to single-sided PCBs.
2. How does copper thickness affect PCB performance?
Thicker copper layers offer lower resistance and higher current-carrying capacity, making them suitable for power-hungry applications and high-speed signals. However, thicker copper also increases the weight and cost of the PCB.
3. What is the purpose of solder mask on a PCB?
Solder mask is a protective coating that covers the copper traces on a PCB. It prevents accidental short circuits and protects the board from environmental factors such as moisture and dust.
4. How do I choose the appropriate PCB material for my application?
The choice of PCB material depends on factors such as the operating temperature, frequency range, and environmental conditions of the application. FR-4 is a general-purpose material suitable for most applications, while specialized materials like Rogers or polyimide may be used for high-frequency or high-temperature applications.
5. What is the importance of layer stack-up in PCB design?
Proper layer stack-up design is crucial for maintaining signal integrity, minimizing crosstalk, and ensuring reliable power distribution. The arrangement of copper layers, insulating layers, and other materials in the stack-up affects the electrical characteristics and performance of the PCB.
Conclusion
Understanding and controlling basic PCB parameters is essential for designing and manufacturing reliable, high-performance electronic products. By considering factors such as board size, copper thickness, trace width and spacing, drill sizes, solder mask, silkscreen, material selection, and layer stack-up, engineers and designers can create PCBs that meet the specific requirements of their applications.
As PCB technology continues to evolve, staying up-to-date with the latest advancements and best practices in PCB design is crucial for staying competitive in the electronics industry. By mastering the fundamental PCB parameters discussed in this article, you will be well-equipped to tackle the challenges of modern PCB design and create innovative, reliable, and cost-effective electronic products.
Leave a Reply