Introduction
When designing and manufacturing printed circuit boards (PCBs), signal integrity is a crucial factor to consider. Signal distortions can lead to poor performance, reliability issues, and even complete failure of the electronic device. One effective technique to reduce signal distortions on PCBs is backdrilling, also known as controlled depth drilling or stub removal.
In this comprehensive article, we will explore the concept of backdrilling, its benefits, and the steps involved in implementing this technique to enhance the signal integrity of your PCBs.
What is Backdrilling?
Backdrilling is a PCB manufacturing process that involves removing the unused portion of a plated through-hole (PTH) via on a multilayer PCB. When a signal travels through a via, it encounters a discontinuity caused by the sudden change in the signal path. This discontinuity can lead to signal reflections and distortions, especially at high frequencies.
By removing the unused portion of the via, also known as the stub, backdrilling minimizes the discontinuity and reduces the signal distortions. The process involves drilling a larger diameter hole concentric to the original via hole, effectively removing the plating from the unused layers.
Benefits of Backdrilling
- Improved Signal Integrity: By reducing the stub length, backdrilling minimizes signal reflections and distortions, resulting in cleaner and more accurate signal transmission.
- Enhanced High-Speed Performance: Backdrilling is particularly beneficial for high-speed designs, where signal integrity is critical. It allows for faster signal propagation and reduces the impact of via stubs on signal quality.
- Reduced Crosstalk: Backdrilling helps in reducing crosstalk between adjacent vias by minimizing the coupling between the stubs.
- Increased Bandwidth: With reduced signal distortions, backdrilling enables higher bandwidth and data rates in high-speed applications.
- Improved Impedance Matching: Backdrilling helps in maintaining consistent impedance along the signal path, minimizing impedance mismatches caused by via stubs.
Implementing Backdrilling in PCB Design
To successfully implement backdrilling in your PCB design, follow these steps:
Step 1: Identify Critical Signals
Identify the high-speed signals in your design that are most susceptible to signal distortions caused by via stubs. These signals typically have fast rise times, high frequencies, or stringent signal integrity requirements.
Step 2: Determine Stub Length
Calculate the maximum allowable stub length for each critical signal based on the signal’s rise time and the PCB’s dielectric constant. The stub length should be kept as short as possible to minimize signal reflections. A common rule of thumb is to keep the stub length less than one-quarter of the signal’s rise time.
Step 3: Define Backdrilling Depth
Based on the stub length calculations, determine the depth to which the vias need to be backdrilled. The backdrilling depth should be sufficient to remove the unused portion of the via while maintaining the integrity of the signal layers.
Step 4: Create Backdrilling Specifications
Include clear and detailed backdrilling specifications in your PCB design files. Specify the vias that require backdrilling, the backdrilling depth, and any additional requirements such as drill diameter and tolerances.
Step 5: Communicate with PCB Manufacturer
Collaborate closely with your PCB manufacturer to ensure they understand and can execute the backdrilling requirements accurately. Provide them with the necessary design files, specifications, and any additional guidelines to ensure a smooth manufacturing process.
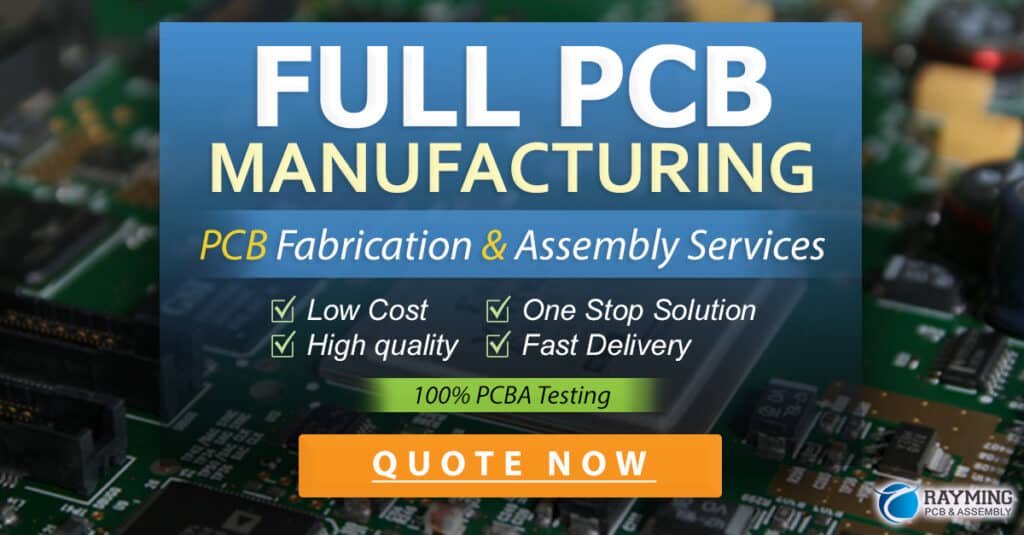
Backdrilling Techniques
There are different techniques used for backdrilling, each with its own advantages and considerations:
Conventional Backdrilling
Conventional backdrilling involves using a secondary drilling operation to remove the stub after the initial via drilling and plating process. This technique is widely used and offers flexibility in terms of backdrilling depth and diameter.
However, conventional backdrilling requires precise alignment and depth control to avoid damaging the signal layers. It also adds an additional manufacturing step, which can impact the overall production time and cost.
Sequential Lamination
Sequential lamination is an alternative to conventional backdrilling. In this technique, the PCB is fabricated in multiple lamination cycles, with each cycle adding a specific set of layers. The vias are drilled and plated only through the required layers, eliminating the need for backdrilling.
Sequential lamination eliminates the risk of damaging the signal layers during backdrilling and reduces the manufacturing complexity. However, it may increase the overall PCB thickness and require careful planning and design considerations.
Laser Drilling
Laser drilling is a precise and controlled method for removing the stub portion of the via. It uses a focused laser beam to selectively remove the plating from the unused layers without damaging the surrounding material.
Laser drilling offers high accuracy, speed, and repeatability compared to mechanical drilling methods. However, it requires specialized equipment and expertise, which may increase the manufacturing cost.
Backdrilling Considerations and Challenges
While backdrilling offers significant benefits for signal integrity, there are certain considerations and challenges to keep in mind:
- Manufacturing Complexity: Backdrilling adds an additional step to the PCB manufacturing process, requiring precise alignment and depth control. This complexity can impact the manufacturing time and cost.
- Risk of Damaging Signal Layers: If not executed properly, backdrilling can potentially damage the signal layers, leading to reliability issues. Proper process control and expertise are essential to mitigate this risk.
- Increased PCB Thickness: In some cases, backdrilling may require additional PCB layers to accommodate the backdrilled vias, resulting in increased overall thickness of the board.
- Limited Applicability: Backdrilling may not be suitable for all PCB designs, especially those with high-density interconnects or complex via structures.
- Cost Implications: Implementing backdrilling can add to the overall manufacturing cost of the PCB due to the additional processing steps and specialized equipment required.
Alternatives to Backdrilling
While backdrilling is an effective technique for reducing signal distortions, there are alternative approaches that can be considered:
blind and buried vias
Blind and buried vias are used to create interconnections between specific layers without extending through the entire PCB thickness. By strategically placing these vias, the stub length can be minimized, reducing signal distortions.
High-Performance Laminates
Using high-performance PCB laminates with low dielectric constant and dissipation factor can help in reducing signal distortions. These laminates offer better signal propagation characteristics and can mitigate the impact of via stubs.
Optimized Via Design
Careful design and optimization of via geometry, including via diameter, pad size, and anti-pad clearance, can help in reducing signal reflections and distortions. Simulation tools can be used to analyze and optimize the via design for improved signal integrity.
Frequently Asked Questions (FAQ)
-
What is the purpose of backdrilling in PCB manufacturing?
Backdrilling is used to remove the unused portion of a plated through-hole (PTH) via on a multilayer PCB. By removing the stub, backdrilling reduces signal reflections and distortions, improving signal integrity and high-speed performance. -
How does backdrilling improve signal integrity?
Backdrilling minimizes the discontinuity caused by the sudden change in the signal path when it travels through a via. By removing the unused portion of the via (stub), backdrilling reduces signal reflections, minimizes crosstalk, and improves impedance matching, resulting in cleaner and more accurate signal transmission. -
Is backdrilling necessary for all PCB designs?
Backdrilling is particularly beneficial for high-speed PCB designs where signal integrity is critical. However, it may not be necessary for all PCB designs, especially those with lower signal speeds or less stringent signal integrity requirements. The decision to implement backdrilling depends on the specific design requirements and performance goals. -
What are the challenges associated with backdrilling?
Some of the challenges associated with backdrilling include increased manufacturing complexity, the risk of damaging signal layers if not executed properly, potential impact on PCB thickness, limited applicability in certain designs, and cost implications due to additional processing steps and specialized equipment. -
Are there alternatives to backdrilling for reducing signal distortions?
Yes, there are alternative approaches to reduce signal distortions, such as using blind and buried vias, high-performance PCB laminates, and optimizing via design. These alternatives can be considered based on the specific design requirements, manufacturing capabilities, and cost considerations.
Conclusion
Backdrilling is a powerful technique for reducing signal distortions on multilayer PCBs, especially in high-speed applications. By removing the unused portion of the via, backdrilling minimizes signal reflections, enhances signal integrity, and improves overall system performance.
To successfully implement backdrilling, it is essential to identify critical signals, determine appropriate stub lengths, define backdrilling specifications, and collaborate closely with the PCB manufacturer. While backdrilling offers significant benefits, it is important to consider the manufacturing complexity, potential challenges, and alternative approaches based on the specific design requirements and constraints.
By understanding the principles of backdrilling and following best practices in PCB design and manufacturing, you can effectively reduce signal distortions and achieve optimal signal integrity in your electronic devices.
Technique | Advantages | Considerations |
---|---|---|
Conventional Backdrilling | – Widely used – Flexibility in depth and diameter |
– Precise alignment and depth control required – Additional manufacturing step |
Sequential Lamination | – Eliminates risk of damaging signal layers – Reduces manufacturing complexity |
– May increase PCB thickness – Requires careful planning and design |
Laser Drilling | – High accuracy and speed – Controlled stub removal |
– Specialized equipment and expertise required – Higher manufacturing cost |
Remember, reducing signal distortions is crucial for achieving optimal performance and reliability in high-speed PCB designs. By implementing backdrilling and considering alternative techniques, you can ensure the integrity of your signals and take your PCB designs to the next level.
Leave a Reply