Introduction
Supply chain disruptions can wreak havoc on electronics manufacturing, leading to production delays, increased costs, and frustrated customers. However, by leveraging variants, live BOMs, and intelligent part selection, companies can proactively mitigate supply chain risks. In this article, we’ll explore strategies and best practices for avoiding supply chain issues, ensuring a smoother production process and improved product reliability.
The Impact of Supply Chain Disruptions
Before diving into solutions, it’s crucial to understand the far-reaching consequences of supply chain disruptions:
Impact | Description |
---|---|
Production Delays | Supply shortages can halt production, leading to missed deadlines and customer dissatisfaction. |
Increased Costs | Scarcity drives up component prices, eroding profit margins and forcing price hikes. |
Quality Issues | Rushed orders or inferior substitute parts can compromise product quality and reliability. |
Reputational Damage | Consistently failing to meet customer expectations can tarnish a company’s reputation. |
Leveraging Variants for Flexibility
One powerful strategy for mitigating supply chain risks is the use of variants in your design. Variants allow you to create multiple versions of a design, each with different components or configurations, without maintaining separate project files.
Benefits of Using Variants
- Flexibility: Variants enable you to quickly adapt to component availability by swapping out hard-to-find parts with suitable alternatives.
- Streamlined Management: Maintaining a single project file with variants reduces the risk of errors and inconsistencies compared to managing multiple separate projects.
- Faster Time-to-Market: With variants, you can rapidly respond to supply chain disruptions and get your product to market faster.
Implementing Variants in Altium Designer
Altium Designer makes it easy to create and manage variants within your PCB design project. Here’s a step-by-step guide:
- Open your PCB design project in Altium Designer.
- In the Projects panel, right-click on your project and select “Add New Project > PCB Project.”
- Give your variant a name and click “OK.”
- In the new variant project, make the necessary component or configuration changes.
- Repeat steps 2-4 for each additional variant you need.
By creating variants for your design, you can quickly adapt to supply chain disruptions without starting from scratch.
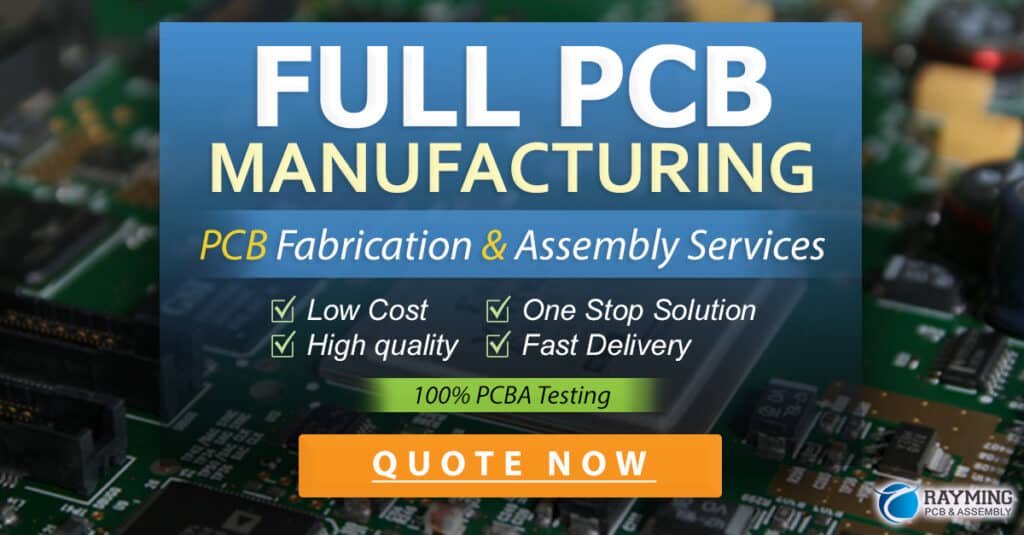
Harnessing the Power of Live BOM
A Bill of Materials (BOM) is a critical document that lists all the components needed to manufacture a product. However, traditional static BOMs can quickly become outdated as supply chain conditions change. This is where Live BOM comes in.
What is Live BOM?
Live BOM is a dynamic, real-time view of your bill of materials that automatically updates based on design changes and component availability. It integrates with your PCB design software and component supplier databases to provide up-to-date information on pricing, availability, and lead times.
Benefits of Live BOM
- Real-Time Updates: Live BOM ensures that you always have the most current information on component availability and pricing.
- Improved Collaboration: Live BOM facilitates better communication between design, procurement, and manufacturing teams.
- Proactive Risk Mitigation: By identifying potential supply chain issues early on, Live BOM helps you take proactive steps to avoid disruptions.
Implementing Live BOM with Altium Designer
Altium Designer’s ActiveBOM feature enables you to create a Live BOM for your PCB design project. Here’s how:
- Open your PCB design project in Altium Designer.
- In the Projects panel, right-click on your project and select “Add New to Project > ActiveBOM Document.”
- Give your ActiveBOM document a name and click “OK.”
- Configure your ActiveBOM settings, including supplier data sources and update frequency.
- As you make design changes or component availability shifts, your ActiveBOM will automatically update.
By leveraging Live BOM, you can stay on top of supply chain conditions and make informed decisions to keep your project on track.
Intelligent Part Selection Strategies
Careful component selection is another key strategy for avoiding supply chain issues. By choosing parts wisely, you can reduce the risk of shortages and ensure a more reliable product.
Factors to Consider When Selecting Components
Factor | Description |
---|---|
Availability | Choose components with stable supply and multiple sourcing options. |
Lifecycle Status | Avoid parts nearing end-of-life to prevent future obsolescence issues. |
Performance | Select components that meet your design’s performance requirements. |
Cost | Balance cost with other factors to ensure a cost-effective and reliable design. |
Best Practices for Part Selection
- Diversify Suppliers: Sourcing components from multiple suppliers reduces the risk of single-point failures in your supply chain.
- Monitor Market Conditions: Stay informed about industry trends, supply chain disruptions, and component lifecycle statuses.
- Design for Flexibility: Create designs that can accommodate alternative components with minimal changes.
- Collaborate with Procurement: Work closely with your procurement team to ensure that selected components are available and cost-effective.
By following these best practices and carefully considering component selection factors, you can design products that are more resilient to supply chain disruptions.
Case Study: XYZ Electronics
To illustrate the effectiveness of these strategies, let’s look at a real-world example. XYZ Electronics, a manufacturer of industrial control systems, faced significant supply chain challenges during the global chip shortage of 2021.
The Challenge
XYZ Electronics relied heavily on a specific microcontroller for their flagship product. When the chip shortage hit, they found themselves unable to source this critical component, forcing them to halt production.
The Solution
To overcome this challenge, XYZ Electronics implemented the following strategies:
- Variants: They created variants of their design that used alternative microcontrollers with similar performance characteristics.
- Live BOM: They adopted a Live BOM system to stay on top of component availability and pricing, enabling them to make informed decisions quickly.
- Part Selection: They diversified their supplier base and redesigned their product to use more readily available components.
The Result
By leveraging variants, Live BOM, and intelligent part selection, XYZ Electronics was able to:
- Resume production within weeks, minimizing downtime and lost revenue.
- Reduce their reliance on single-source components, improving supply chain resilience.
- Identify and mitigate potential supply chain risks proactively.
XYZ Electronics’ success story demonstrates the power of these strategies in overcoming supply chain challenges.
FAQ
-
Q: What if I can’t find a suitable alternative component for my design?
A: If you’re unable to find a direct replacement, consider redesigning that portion of your circuit to accommodate available components with similar performance characteristics. -
Q: How often should I update my Live BOM?
A: The frequency of updates depends on the complexity of your design and the volatility of the supply chain. In general, aim to update your Live BOM at least weekly, if not daily. -
Q: Can I use variants for more than just supply chain issues?
A: Absolutely! Variants are useful for creating different product configurations, such as regional variations or feature sets, without maintaining separate design files. -
Q: How do I balance component cost with other selection factors?
A: While cost is important, it shouldn’t be the sole deciding factor. Consider the total cost of ownership, including the potential costs of production delays or quality issues arising from inferior parts. -
Q: What if a component goes end-of-life during my product’s lifecycle?
A: This is where proactive lifecycle management comes into play. Monitor component lifecycles and plan for redesigns or last-time buys well in advance of obsolescence dates.
Conclusion
Supply chain disruptions are an inevitable part of electronics manufacturing, but they don’t have to derail your projects. By leveraging variants, live BOM, and intelligent part selection strategies, you can proactively mitigate supply chain risks and ensure a smoother production process.
As we’ve seen with XYZ Electronics’ success story, these strategies can make a significant difference in overcoming supply chain challenges. By staying informed, designing for flexibility, and collaborating closely with procurement and manufacturing teams, you can create products that are more resilient to supply chain disruptions.
At AltiumLive 2024, we’ll be diving deeper into these topics and exploring the latest tools and techniques for supply chain risk mitigation. Join us to learn from industry experts, connect with peers, and discover new strategies for avoiding supply chain issues in your designs.
Key Takeaways
- Use variants to create flexible designs that can adapt to component availability.
- Implement a Live BOM system to stay on top of real-time component information.
- Select components carefully, considering availability, lifecycle status, performance, and cost.
- Diversify your supplier base and design for flexibility to reduce supply chain risks.
- Collaborate closely with procurement and manufacturing teams to ensure a smooth production process.
By following these strategies and staying proactive, you can navigate the challenges of supply chain disruptions and create more resilient, reliable products. See you at AltiumLive 2024!
Leave a Reply