Introduction to Parallel Track Routing
Parallel track routing is a technique used in printed circuit board (PCB) design where tracks or traces are routed in parallel on adjacent layers of the PCB. While this method can be useful in certain situations, it can also lead to several issues that can compromise the integrity and performance of the PCB. In this article, we will explore the concept of parallel track routing, its advantages and disadvantages, and the best practices for avoiding adjacent layer parallel track routing.
What is Parallel Track Routing?
Parallel track routing involves placing tracks or traces on adjacent layers of a PCB in a parallel fashion. This means that the tracks are routed in the same direction and are positioned directly above or below each other on different layers. The main purpose of this technique is to save space on the PCB and to reduce the overall length of the tracks.
Advantages of Parallel Track Routing
-
Space Savings: By routing tracks in parallel on adjacent layers, designers can save valuable space on the PCB. This is particularly useful in high-density designs where board real estate is limited.
-
Reduced Track Length: Parallel track routing can help reduce the overall length of the tracks, which can be beneficial in terms of signal integrity and timing. Shorter tracks generally have lower resistance, capacitance, and inductance, which can improve signal quality and reduce propagation delays.
-
Simplified Routing: In some cases, parallel track routing can simplify the routing process by allowing designers to route multiple tracks in the same direction without the need for complex routing patterns.
Disadvantages of Parallel Track Routing
-
Crosstalk: One of the main issues with parallel track routing is the potential for crosstalk between adjacent tracks. Crosstalk occurs when the signal on one track interferes with the signal on a nearby track, leading to signal integrity issues and potential errors in the circuit.
-
Electromagnetic Interference (EMI): Parallel track routing can also contribute to increased EMI, as the parallel tracks can act as antennas and radiate electromagnetic energy. This can cause interference with other electronic devices and may violate EMI regulations.
-
Impedance Mismatch: When tracks are routed in parallel on adjacent layers, there is a risk of impedance mismatch. This occurs when the impedance of the tracks does not match the impedance of the connected components or devices, leading to signal reflections and distortions.
-
Manufacturing Challenges: Parallel track routing can pose challenges during the manufacturing process, particularly when it comes to the alignment and registration of the layers. Any misalignment can result in shorts or opens between the parallel tracks, compromising the reliability of the PCB.
Best Practices for Avoiding Adjacent Layer Parallel Track Routing
To mitigate the risks associated with parallel track routing, designers should follow these best practices:
1. Maintain Adequate Spacing
One of the most effective ways to reduce crosstalk and EMI is to maintain adequate spacing between parallel tracks. The specific spacing requirements will depend on factors such as the signal frequency, track width, and dielectric material. As a general rule, the spacing should be at least three times the track width for high-speed signals and two times the track width for lower-speed signals.
Signal Type | Minimum Spacing |
---|---|
High-speed | 3x track width |
Low-speed | 2x track width |
2. Use Guard Tracks
Guard tracks are grounded or power tracks that are placed between parallel signal tracks to provide shielding and reduce crosstalk. By placing guard tracks between sensitive signals, designers can effectively isolate the tracks and minimize interference. The width of the guard tracks should be at least equal to the width of the signal tracks for optimal shielding.
3. Stagger Tracks on Adjacent Layers
Instead of routing tracks directly above or below each other on adjacent layers, designers can stagger the tracks to reduce the coupling between them. By offsetting the tracks, the overlap between them is minimized, which can help reduce crosstalk and EMI. The amount of staggering required will depend on the specific design requirements and the spacing between the tracks.
4. Use Differential Pairs
For high-speed signals, using differential pairs can be an effective way to reduce crosstalk and EMI. Differential pairs consist of two tracks that carry complementary signals, with the signal being the difference between the two tracks. By using differential pairs, the electromagnetic fields generated by the tracks tend to cancel each other out, reducing the overall EMI and crosstalk.
5. Consider Alternative Routing Techniques
In some cases, it may be necessary to use alternative routing techniques to avoid adjacent layer parallel track routing. Some options include:
-
Microstrip Routing: This technique involves routing tracks on the outer layers of the PCB, with a ground plane on the adjacent layer. This can help reduce crosstalk and EMI by providing a reference plane for the signals.
-
Stripline Routing: Stripline routing involves routing tracks between two ground planes, which provides excellent shielding and reduces crosstalk and EMI. However, this technique requires additional layers and can increase the overall thickness of the PCB.
-
coplanar waveguide Routing: This technique involves routing tracks on the same layer, with ground planes on either side of the track. This can help reduce crosstalk and EMI by providing a reference plane for the signals and can be useful in high-frequency designs.
Conclusion
Adjacent layer parallel track routing can be a useful technique in PCB design, but it comes with several risks that can compromise the integrity and performance of the circuit. By understanding the advantages and disadvantages of parallel track routing and following best practices such as maintaining adequate spacing, using guard tracks, staggering tracks, using differential pairs, and considering alternative routing techniques, designers can effectively mitigate these risks and ensure the reliability and functionality of their PCBs.
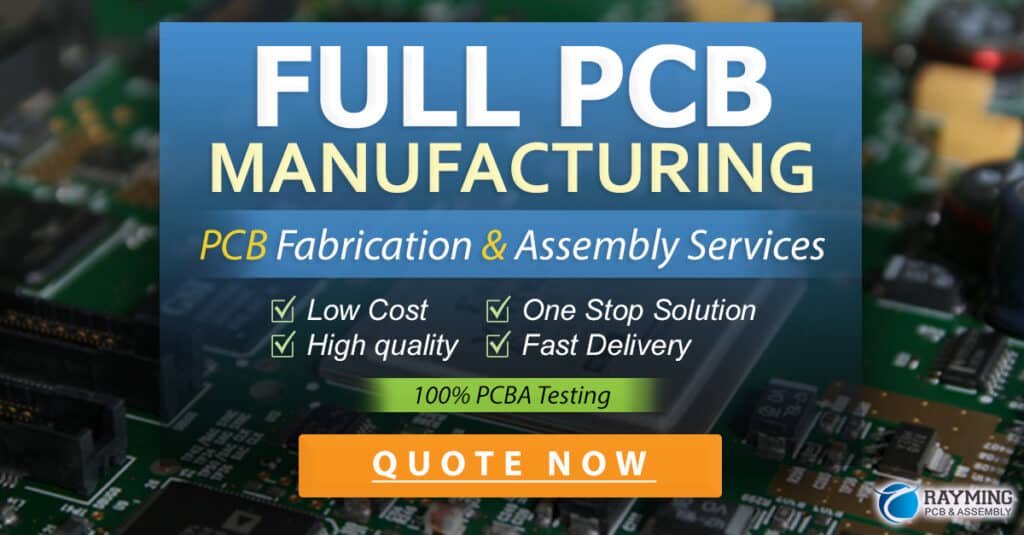
Frequently Asked Questions (FAQ)
- What is the main issue with adjacent layer parallel track routing?
-
The main issue with adjacent layer parallel track routing is the potential for crosstalk between the parallel tracks, which can lead to signal integrity issues and errors in the circuit.
-
How can designers reduce crosstalk and EMI in parallel track routing?
-
Designers can reduce crosstalk and EMI by maintaining adequate spacing between parallel tracks, using guard tracks, staggering tracks on adjacent layers, and using differential pairs for high-speed signals.
-
What is the recommended minimum spacing between parallel tracks?
-
The recommended minimum spacing between parallel tracks is three times the track width for high-speed signals and two times the track width for lower-speed signals.
-
What are guard tracks, and how do they help in parallel track routing?
-
Guard tracks are grounded or power tracks that are placed between parallel signal tracks to provide shielding and reduce crosstalk. They should have a width at least equal to the width of the signal tracks for optimal shielding.
-
What are some alternative routing techniques to avoid adjacent layer parallel track routing?
- Some alternative routing techniques include microstrip routing, stripline routing, and coplanar waveguide routing. These techniques involve routing tracks on outer layers, between ground planes, or with ground planes on either side of the track to reduce crosstalk and EMI.
Leave a Reply