Introduction to Aspect Ratios in PCB Design
Aspect ratios play a crucial role in the design and manufacturing of multi-layered printed circuit boards (PCBs). In PCB design, aspect ratio refers to the relationship between the width and depth of a drilled hole or via. It is a critical factor that determines the manufacturability, reliability, and performance of a PCB.
In this article, we will delve into the importance of aspect ratios in multi-layered PCBs, discussing their impact on various aspects of PCB design and manufacturing. We will explore the challenges associated with high aspect ratios, the recommended guidelines for maintaining appropriate aspect ratios, and the techniques used to optimize PCB design while considering aspect ratios.
Understanding Aspect Ratios in PCBs
Definition of Aspect Ratio
Aspect ratio is defined as the ratio of the depth of a drilled hole or via to its width. In other words, it is the relationship between the thickness of the PCB and the diameter of the drilled hole. The formula for calculating aspect ratio is as follows:
Aspect Ratio = Depth of Hole / Diameter of Hole
For example, if a PCB has a thickness of 1.6mm and the diameter of a drilled hole is 0.2mm, the aspect ratio would be:
Aspect Ratio = 1.6mm / 0.2mm = 8:1
Importance of Aspect Ratios in Multi-Layered PCBs
Multi-layered PCBs consist of multiple layers of conductive and insulating materials stacked together to form a complex circuit board. These PCBs are commonly used in advanced electronic devices that require high density and functionality. Aspect ratios play a significant role in the design and manufacturing of multi-layered PCBs for several reasons:
-
Manufacturability: High aspect ratios can pose challenges during the drilling and plating processes. As the depth of the hole increases relative to its diameter, it becomes more difficult to achieve uniform plating throughout the hole. This can lead to issues such as incomplete plating, voids, or poor electrical connectivity.
-
Reliability: Proper aspect ratios ensure the structural integrity and reliability of the PCB. High aspect ratios can result in thin, fragile walls between the holes and the surrounding copper, making the PCB more susceptible to mechanical stress and damage. This can lead to compromised reliability and potential failures in the field.
-
Signal Integrity: Aspect ratios can impact the signal integrity of the PCB. High aspect ratios can cause impedance mismatches and signal reflections, leading to signal degradation and performance issues. Maintaining appropriate aspect ratios helps in minimizing signal integrity problems and ensuring optimal performance of the PCB.
-
Cost: Achieving high aspect ratios often requires specialized manufacturing processes and equipment, which can increase the overall cost of PCB production. Striking a balance between the desired aspect ratios and cost-effectiveness is essential for successful PCB design and manufacturing.
Challenges of High Aspect Ratios in PCB Manufacturing
Drilling Challenges
Drilling is a critical process in PCB manufacturing, and high aspect ratios can present several challenges:
-
Drill Bit Selection: High aspect ratio holes require the use of specialized drill bits with high length-to-diameter ratios. These drill bits are more prone to deflection, breakage, and wear, which can impact the accuracy and quality of the drilled holes.
-
Hole Alignment: As the aspect ratio increases, maintaining proper alignment of the drill bit becomes more challenging. Any misalignment can result in non-uniform hole diameters, shifted holes, or even drilling into adjacent copper traces, leading to manufacturing defects.
-
Drill Wander: High aspect ratio drilling is susceptible to drill wander, where the drill bit deviates from its intended path due to factors such as machine vibration, material properties, or tool wear. Drill wander can cause variations in hole diameter and position, affecting the overall quality and reliability of the PCB.
Plating Challenges
Plating is another critical process in PCB manufacturing that is impacted by high aspect ratios:
-
Uniform Plating: Achieving uniform plating throughout the entire depth of a high aspect ratio hole is challenging. As the aspect ratio increases, it becomes more difficult for the plating solution to flow and deposit evenly along the walls of the hole. This can result in thin or incomplete plating, leading to poor electrical connectivity and reliability issues.
-
Voids and Dimples: High aspect ratio plating is prone to the formation of voids and dimples. Voids are gaps or air pockets in the plating, while dimples are small indentations on the surface of the plating. Both voids and dimples can compromise the electrical and mechanical integrity of the PCB.
-
Plating Stress: High aspect ratio plating can induce significant stress on the PCB due to the thick layers of copper deposited in the holes. This stress can cause warping, delamination, or cracking of the PCB, especially during the thermal cycling and reflow processes.
Signal Integrity Challenges
High aspect ratios can also impact the signal integrity of the PCB:
-
Impedance Mismatch: As the aspect ratio increases, the impedance of the via or hole may deviate from the desired characteristic impedance of the PCB. This impedance mismatch can cause signal reflections, leading to signal degradation and performance issues.
-
Signal Attenuation: High aspect ratio vias or holes can introduce additional resistance and capacitance, leading to signal attenuation. This can result in reduced signal strength and compromised signal quality, especially for high-speed signals.
-
Crosstalk: High aspect ratio vias or holes in close proximity can increase the likelihood of crosstalk between adjacent signals. Crosstalk occurs when the electromagnetic field of one signal interferes with another, causing unwanted coupling and signal distortion.
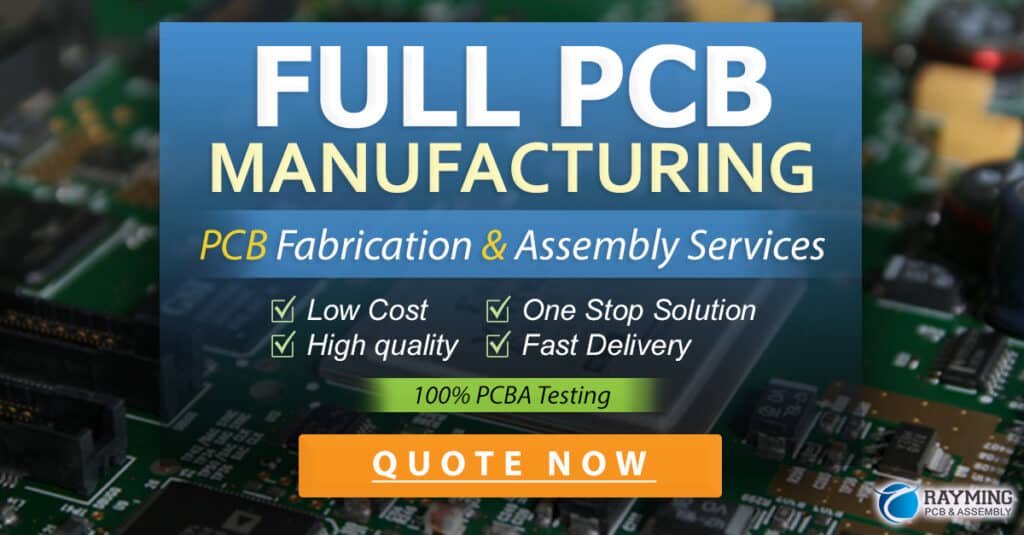
Recommended Aspect Ratio Guidelines
To mitigate the challenges associated with high aspect ratios and ensure manufacturability, reliability, and signal integrity, PCB designers and manufacturers follow recommended aspect ratio guidelines. These guidelines provide a framework for determining appropriate aspect ratios based on various factors such as PCB thickness, hole diameter, and manufacturing capabilities.
IPC Standards for Aspect Ratios
The IPC (Association Connecting Electronics Industries) is a global standards organization that provides guidelines and best practices for PCB design and manufacturing. IPC standards offer recommendations for aspect ratios based on the type of PCB and the manufacturing process.
For example, IPC-6012 (Qualification and Performance Specification for Rigid Printed Boards) provides the following guidelines for aspect ratios:
Aspect Ratio | Recommendation |
---|---|
Up to 6:1 | Standard |
6:1 to 8:1 | High |
8:1 to 10:1 | Very High |
Above 10:1 | Special |
These recommendations serve as a starting point for PCB designers to determine the appropriate aspect ratios for their specific designs.
Manufacturer Capabilities and Limitations
While IPC standards provide general guidelines, it is essential to consult with the specific PCB manufacturer to understand their capabilities and limitations regarding aspect ratios. Different manufacturers may have varying equipment, processes, and expertise that influence their ability to handle high aspect ratios.
PCB designers should communicate their aspect ratio requirements with the manufacturer early in the design process to ensure feasibility and manufacturability. The manufacturer can provide guidance on their recommended aspect ratio limits and suggest design modifications if necessary.
Design Considerations for Optimal Aspect Ratios
To achieve optimal aspect ratios in multi-layered PCBs, designers should consider the following:
-
PCB Thickness: The thickness of the PCB directly impacts the aspect ratios of the drilled holes. Thinner PCBs generally allow for lower aspect ratios, while thicker PCBs may require higher aspect ratios. Designers should strive to minimize the PCB thickness where possible to reduce the challenges associated with high aspect ratios.
-
Hole Diameter: The diameter of the drilled holes also affects the aspect ratios. Larger hole diameters provide more room for plating and reduce the challenges of high aspect ratios. However, larger holes also consume more space on the PCB, which can impact routing and component placement. Designers should find a balance between hole diameter and PCB real estate based on the specific requirements of the design.
-
Layer Count: The number of layers in a multi-layered PCB can influence the aspect ratios. As the layer count increases, the overall thickness of the PCB also increases, leading to higher aspect ratios. Designers should optimize the layer stackup and consider alternative routing strategies to minimize the need for high aspect ratio vias.
-
Via Placement: The placement of vias on the PCB can impact the aspect ratios and signal integrity. Vias should be placed strategically to minimize the distance between layers and reduce the overall via length. Additionally, designers should consider the spacing between vias to prevent crosstalk and signal interference.
-
Material Selection: The choice of PCB materials can also influence the aspect ratios. Some high-performance materials, such as low-loss or high-frequency laminates, may have specific requirements for aspect ratios to ensure optimal performance. Designers should consult with the manufacturer and material suppliers to select the most suitable materials for their design.
Techniques for Optimizing Aspect Ratios
To optimize aspect ratios in multi-layered PCBs, designers can employ various techniques and strategies. These techniques aim to reduce the challenges associated with high aspect ratios and improve the manufacturability, reliability, and signal integrity of the PCB.
Via Optimization Techniques
-
Via Sizing: Designers can optimize the size of the vias to strike a balance between aspect ratios and PCB real estate. By using larger via diameters where possible, designers can reduce the aspect ratios and improve the manufacturability and reliability of the PCB. However, larger vias also consume more space, so designers should carefully consider the trade-offs and use via sizing judiciously.
-
Via Stacking: Via stacking is a technique where multiple vias are stacked on top of each other to create a longer continuous connection between layers. By using via stacking, designers can reduce the overall aspect ratio of the connection compared to using a single long via. However, via stacking also introduces additional complexity and potential signal integrity challenges, so designers should use this technique selectively.
-
blind and buried vias: Blind vias and buried vias are specialized types of vias that do not extend through the entire thickness of the PCB. Blind vias are exposed on only one side of the PCB, while buried vias are completely internal and not exposed on either side. By using blind and buried vias, designers can reduce the overall via length and aspect ratios, improving manufacturability and signal integrity. However, these specialized vias also increase the manufacturing complexity and cost, so their use should be justified based on the specific design requirements.
Layer Stackup Optimization
-
Strategic Layer Arrangement: Designers can optimize the layer stackup of the multi-layered PCB to minimize the need for high aspect ratio vias. By carefully arranging the layers and placing components and signals on adjacent layers where possible, designers can reduce the distance between layers and minimize the via length. This approach can help in achieving lower aspect ratios and improving signal integrity.
-
Power and Ground Plane Placement: The placement of power and ground planes in the layer stackup can impact the aspect ratios and signal integrity. By placing power and ground planes adjacent to signal layers, designers can provide effective shielding and reduce the need for high aspect ratio vias. Additionally, using dedicated power and ground planes can help in maintaining a low-impedance return path and minimizing signal distortion.
-
Symmetrical Stackup: A symmetrical layer stackup can help in reducing warpage and ensuring even distribution of stresses during the manufacturing process. By designing a stackup with symmetrical arrangement of layers, designers can minimize the impact of high aspect ratio vias on the mechanical stability of the PCB.
High-Density Interconnect (HDI) Techniques
High-Density Interconnect (HDI) techniques involve the use of advanced manufacturing processes and design strategies to achieve high-density routing and component placement on the PCB. HDI techniques can help in reducing the aspect ratios and improving the overall performance of the PCB.
-
Microvias: Microvias are small-diameter vias that are typically laser-drilled and have a diameter of less than 150 microns. By using microvias, designers can achieve higher routing density and reduce the overall via length and aspect ratios. Microvias are commonly used in HDI designs to provide interconnections between fine-pitch components and high-density routing layers.
-
Sequential Lamination: Sequential lamination is an HDI manufacturing process where the PCB is built up in stages, with each stage consisting of a subset of layers. By using sequential lamination, designers can incorporate microvias and high-density routing in specific regions of the PCB while maintaining lower aspect ratios in other areas. This approach allows for a balance between high-density interconnects and manufacturability.
-
Via-in-Pad: Via-in-pad is an HDI technique where vias are placed directly in the component pads, eliminating the need for additional routing space. By using via-in-pad, designers can reduce the overall PCB size and improve the routing density. However, via-in-pad also introduces challenges related to aspect ratios and the filling and capping of vias, so designers should carefully consider the manufacturability and reliability implications.
FAQs
-
What is aspect ratio in PCB design?
Aspect ratio in PCB design refers to the ratio of the depth of a drilled hole or via to its width. It is a critical factor that determines the manufacturability, reliability, and performance of a PCB. -
Why are high aspect ratios challenging in PCB manufacturing?
High aspect ratios can pose challenges in PCB manufacturing due to difficulties in drilling, plating, and maintaining signal integrity. As the depth of the hole increases relative to its diameter, it becomes more challenging to achieve uniform plating, avoid voids and dimples, and ensure proper signal transmission. -
What are the recommended aspect ratio guidelines for PCBs?
The IPC (Association Connecting Electronics Industries) provides guidelines for aspect ratios based on the type of PCB and manufacturing process. Generally, aspect ratios up to 6:1 are considered standard, while ratios above 8:1 are considered very high or require special considerations. However, the specific recommendations may vary depending on the manufacturer’s capabilities and limitations. -
How can designers optimize aspect ratios in multi-layered PCBs?
Designers can optimize aspect ratios in multi-layered PCBs by employing techniques such as via optimization (via sizing, via stacking, blind and buried vias), layer stackup optimization (strategic layer arrangement, power and ground plane placement, symmetrical stackup), and high-density interconnect (HDI) techniques (microvias, sequential lamination, via-in-pad). -
What are the benefits of maintaining appropriate aspect ratios in PCBs?
Maintaining appropriate aspect ratios in PCBs offers several benefits, including improved manufacturability, increased reliability, better signal integrity, and cost-effectiveness. By adhering to recommended aspect ratio guidelines and employing optimization techniques, designers can ensure the successful fabrication and performance of multi-layered PCBs.
Conclusion
Aspect ratios play a crucial role in the design and manufacturing of multi-layered PCBs. Understanding the importance of aspect ratios and the challenges associated with high aspect ratios is essential for creating reliable, high-performance PCBs. By following recommended guidelines, working closely with manufacturers, and employing optimization techniques, designers can effectively manage aspect ratios and ensure the successful fabrication and operation of their PCBs.
As PCB technology continues to advance and the demand for high-density, high-performance electronics grows, the significance of aspect ratios will only increase. Designers must stay updated with the latest industry standards, manufacturing capabilities, and design strategies to navigate the complexities of aspect ratios in multi-layered PCBs.
By prioritizing aspect ratio considerations throughout the design process, collaborating with manufacturers, and leveraging advanced techniques such as HDI and via optimization, designers can overcome the challenges posed by high aspect ratios and deliver PCBs that meet the ever-increasing demands of modern electronics. The successful management of aspect ratios will continue to be a critical factor in driving innovation and reliability in the PCB industry.
Leave a Reply