Introduction to Green PCBs
Green PCBs, also known as solder mask green PCBs, have become increasingly popular in the electronics industry. These printed circuit boards feature a green solder mask that covers the copper traces, providing insulation and protection against oxidation. The green color is the most common and widely used solder mask color in PCB manufacturing. In this article, we will explore the cost implications of choosing green PCBs and compare them to other solder mask color options.
What is a Solder Mask?
A solder mask, also referred to as a solder resist or solder stop, is a thin layer of polymer applied to the surface of a printed circuit board. Its primary purpose is to protect the copper traces from oxidation and prevent solder bridges from forming during the soldering process. The solder mask also provides electrical insulation between the copper traces, ensuring proper circuit functionality.
Why Choose Green PCBs?
Green PCBs have become the industry standard for several reasons:
-
Visibility: The green color provides excellent contrast against the copper traces, making it easier for manufacturers to inspect the PCB for defects and ensuring higher quality control.
-
Aesthetics: Green PCBs have a professional and clean appearance, which is appealing to many customers.
-
Availability: Due to their popularity, green PCBs are widely available and can be sourced from numerous PCB manufacturers worldwide.
Cost Comparison of Green PCBs vs. Other Solder Mask Colors
When considering the cost of green PCBs, it is essential to compare them to other solder mask color options. The most common solder mask colors include:
- Green
- Red
- Blue
- Black
- White
- Yellow
Factors Affecting PCB Cost
Several factors influence the cost of PCB manufacturing, including:
-
PCB Size: Larger PCBs require more material and processing time, resulting in higher costs.
-
Layer Count: Multi-layer PCBs are more complex and expensive to manufacture than single-layer or double-layer boards.
-
Quantity: Higher order quantities often result in lower per-unit costs due to economies of scale.
-
Material: The choice of PCB substrate material, such as FR-4, Rogers, or polyimide, can significantly impact the overall cost.
-
Surface Finish: The type of surface finish, such as HASL, ENIG, or OSP, affects the PCB’s cost.
Cost Comparison Table
Solder Mask Color | Relative Cost | Availability | Minimum Order Quantity (MOQ) |
---|---|---|---|
Green | Lowest | High | Low |
Red | Low | High | Low |
Blue | Low | High | Low |
Black | Medium | Medium | Medium |
White | High | Low | High |
Yellow | High | Low | High |
As shown in the table above, green PCBs are generally the most cost-effective option due to their widespread availability and low minimum order quantities (MOQs). Red and blue solder masks are also relatively inexpensive and readily available. However, black, white, and yellow solder masks may incur higher costs and have limited availability, with higher MOQs.
Advantages of Green PCBs
Apart from their cost-effectiveness, green PCBs offer several advantages:
-
Durability: The green solder mask provides excellent protection against oxidation and mechanical stress, ensuring the longevity of the PCB.
-
Ease of Inspection: The high contrast between the green solder mask and copper traces allows for easier visual inspection, reducing the likelihood of defects and improving overall quality control.
-
Compatibility: Green PCBs are compatible with a wide range of components and soldering techniques, making them suitable for various applications.
-
Thermal Stability: The green solder mask exhibits good thermal stability, allowing the PCB to withstand high temperatures during the soldering process and operation.
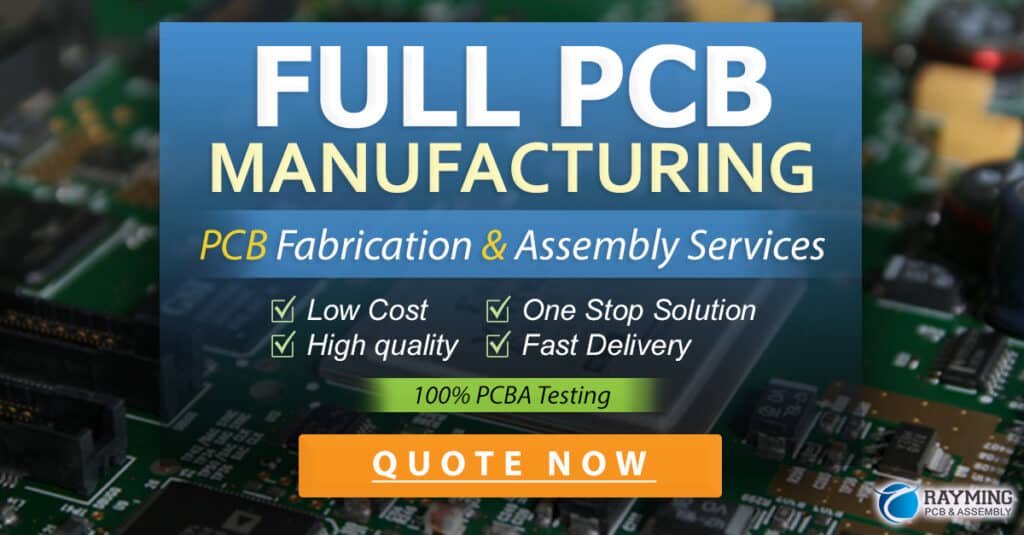
Disadvantages of Green PCBs
While green PCBs offer numerous benefits, there are a few potential drawbacks to consider:
-
Limited Design Options: The green color may not be suitable for certain aesthetic or branding requirements, limiting design options for some applications.
-
Potential for Color Variation: Slight variations in the green color may occur between different batches or manufacturers, which could be a concern for projects requiring strict color consistency.
-
Reflectivity: Green solder masks may exhibit higher reflectivity compared to darker colors, which could potentially impact the performance of optical sensors or cameras in certain applications.
FAQ
-
Q: Are green PCBs always the cheapest option?
A: In most cases, green PCBs are the most cost-effective option due to their widespread availability and low minimum order quantities. However, the overall cost of a PCB depends on various factors, such as size, layer count, and material, so it’s essential to consider all aspects when determining the most economical choice for a specific project. -
Q: Can I use green PCBs for high-frequency applications?
A: Yes, green PCBs can be used for high-frequency applications. The solder mask color does not directly impact the PCB’s electrical performance. However, the choice of substrate material, such as Rogers or polyimide, is crucial for high-frequency applications. -
Q: Are there any environmental concerns associated with green PCBs?
A: Modern green solder masks are typically made from environmentally friendly materials and comply with RoHS (Restriction of Hazardous Substances) regulations. However, it’s essential to verify the specific materials used by the PCB manufacturer to ensure compliance with environmental standards. -
Q: Can I mix different solder mask colors on the same PCB?
A: Yes, it is possible to have different solder mask colors on the same PCB, such as using green for the top layer and black for the bottom layer. However, this may increase the overall cost and complexity of the manufacturing process, and not all PCB manufacturers offer this option. -
Q: How do I choose the right solder mask color for my project?
A: When selecting a solder mask color, consider factors such as cost, availability, design requirements, and the intended application. Green PCBs are a popular choice for their cost-effectiveness and ease of inspection, but other colors may be more suitable for specific aesthetic or functional requirements.
Conclusion
Green PCBs have become the industry standard due to their cost-effectiveness, widespread availability, and excellent visual inspection capabilities. When compared to other solder mask colors, green PCBs offer the lowest relative cost and lowest minimum order quantities, making them an attractive option for many electronics projects.
However, it’s crucial to consider the specific requirements of each project, such as design aesthetics, environmental concerns, and application-specific needs, when deciding on the most suitable solder mask color. In some cases, other colors like red, blue, or black may be more appropriate, despite potentially higher costs or limited availability.
By understanding the factors that influence PCB cost and the advantages and disadvantages of green PCBs, engineers and project managers can make informed decisions when selecting the most appropriate solder mask color for their projects, balancing cost, functionality, and aesthetics.
Leave a Reply