What are Fiducial Markers in PCB Manufacturing?
Fiducial markers, also known as fiducials or alignment marks, are small, precisely placed features on a PCB that serve as reference points for automated assembly equipment. These markers are typically copper pads or silkscreen designs that are easily recognizable by machine vision systems. The primary purpose of fiducial markers is to provide a consistent and accurate way for pick-and-place machines and other automated assembly equipment to locate and orient the PCB during the manufacturing process.
Types of Fiducial Markers
There are two main types of fiducial markers used in PCB manufacturing:
-
Global Fiducials: These markers are placed on the outer edges of the PCB panel and are used to determine the overall orientation and position of the board. Global fiducials are typically larger than local fiducials and are used by the assembly equipment to align the PCB before placing components.
-
Local Fiducials: These markers are placed near specific components or groups of components on the PCB. Local fiducials are used to ensure accurate placement of fine-pitch or high-precision components, such as ball grid array (BGA) packages or chip-scale packages (CSPs).
Fiducial Type | Location | Purpose |
---|---|---|
Global | Outer edges of PCB panel | Determine overall orientation and position of board |
Local | Near specific components | Ensure accurate placement of fine-pitch components |
The Importance of Fiducial Markers in Traditional PCB Manufacturing
In traditional PCB manufacturing, fiducial markers have been essential for ensuring the accuracy and reliability of the assembly process. The main benefits of using fiducial markers include:
-
Improved Alignment Accuracy: Fiducial markers provide a consistent reference point for automated assembly equipment, reducing the risk of misalignment and improving the overall accuracy of component placement.
-
Increased Manufacturing Efficiency: By enabling precise alignment, fiducial markers help to reduce the time required for manual adjustments and corrections during the assembly process. This leads to increased throughput and faster production times.
-
Reduced Assembly Errors: Fiducial markers minimize the occurrence of assembly errors, such as misplaced or rotated components, which can lead to device malfunctions or failures.
-
Compatibility with Automated Assembly Equipment: Fiducial markers are designed to be easily recognizable by machine vision systems, ensuring compatibility with a wide range of automated assembly equipment.
Advancements in Modern PCB Manufacturing Technologies
In recent years, PCB manufacturing technologies have undergone significant advancements, leading to improved accuracy, precision, and efficiency. Some of these advancements include:
-
High-Resolution Camera Systems: Modern machine vision systems feature high-resolution cameras with advanced image processing capabilities, enabling more precise recognition and alignment of components without the need for fiducial markers.
-
Advanced Algorithms and Software: Sophisticated algorithms and software solutions have been developed to enhance the accuracy and reliability of component placement, even in the absence of fiducial markers. These algorithms can account for variations in board design, component packaging, and other factors that may affect alignment.
-
Improved Motion Control Systems: Advancements in motion control technologies, such as linear encoders and servo motors, have enabled more precise positioning and movement of automated assembly equipment. This has resulted in higher placement accuracy and reduced reliance on fiducial markers.
-
Adaptive Manufacturing Processes: Modern manufacturing systems can adapt to variations in PCB design and component placement, using real-time data and feedback to make necessary adjustments on the fly. This adaptability reduces the need for strict reliance on fiducial markers.
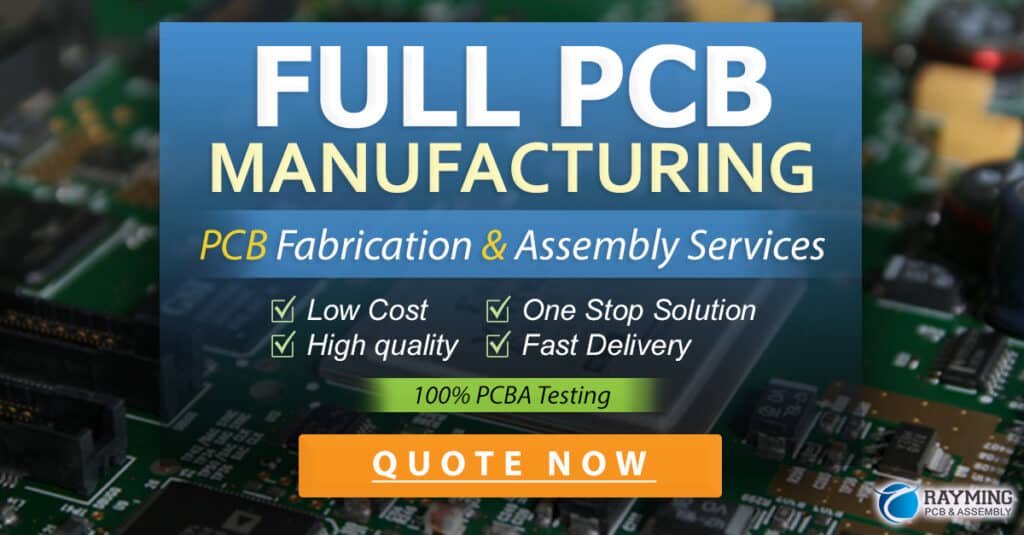
The Role of Fiducial Markers in Modern PCB Manufacturing
Despite the advancements in modern manufacturing technologies, fiducial markers still play a role in PCB manufacturing, particularly in certain situations:
-
High-Precision Applications: In applications where extremely high precision is required, such as in the aerospace, medical, or military industries, fiducial markers may still be necessary to ensure the utmost accuracy in component placement.
-
Complex PCB Designs: For PCBs with complex layouts, high component density, or irregular shapes, fiducial markers can provide additional reference points to aid in accurate assembly.
-
Legacy Equipment Compatibility: Some older automated assembly equipment may still rely on fiducial markers for alignment. In these cases, including fiducial markers on the PCB design ensures compatibility with legacy systems.
-
Redundancy and Error Prevention: Even with advanced manufacturing capabilities, including fiducial markers can provide an additional layer of redundancy and error prevention, particularly for critical applications where failure is not an option.
Best Practices for Fiducial Marker Placement on PCBs
When including fiducial markers on a PCB design, consider the following best practices:
-
Quantity: Use a minimum of three global fiducial markers, placed near the corners of the PCB panel. For local fiducials, use a minimum of two markers per component or group of components.
-
Size and Shape: Fiducial markers should be large enough to be easily recognizable by machine vision systems, typically 1-3 mm in diameter. Circular or cross-shaped markers are most common.
-
Placement: Fiducial markers should be placed in areas of the PCB that are free from other components or features that may interfere with their recognition. Avoid placing markers too close to the edges of the board or near tall components that may cast shadows.
-
Contrast: Ensure that fiducial markers have sufficient contrast against the PCB substrate to be easily detectable by camera systems. This can be achieved through copper pads or high-contrast silkscreen designs.
-
Consistency: Use a consistent fiducial marker design throughout the PCB panel to ensure reliable recognition by automated assembly equipment.
Frequently Asked Questions (FAQ)
-
Q: Are fiducial markers still necessary for all PCB designs?
A: No, fiducial markers are not always necessary for modern PCB manufacturing, particularly for simpler designs and less demanding applications. However, they may still be beneficial for high-precision applications, complex PCB layouts, or when using legacy assembly equipment. -
Q: Can I use non-standard shapes for fiducial markers?
A: While circular and cross-shaped fiducial markers are the most common, other shapes can be used as long as they are easily recognizable by machine vision systems. However, it is essential to ensure that the chosen shape is consistent throughout the PCB panel and compatible with the assembly equipment being used. -
Q: How do I determine the appropriate size for fiducial markers?
A: The size of fiducial markers depends on various factors, such as the resolution of the machine vision system, the size of the PCB, and the placement accuracy requirements. Generally, fiducial markers should be between 1-3 mm in diameter, but it is best to consult with your PCB manufacturer or assembly service provider for specific recommendations. -
Q: Can fiducial markers be placed on both sides of the PCB?
A: Yes, fiducial markers can be placed on both the top and bottom sides of the PCB if required. This is particularly useful for double-sided assemblies or when components need to be placed on both sides of the board with high accuracy. -
Q: What should I do if my PCB design doesn’t have space for global fiducial markers?
A: If your PCB design has limited space for global fiducial markers, you can consider using local fiducials near critical components or component groups. Alternatively, you can explore the possibility of using advanced manufacturing technologies that rely less on fiducial markers for alignment, such as high-resolution camera systems or adaptive manufacturing processes.
Conclusion
In conclusion, while fiducial marker placements on PCBs have been essential in traditional manufacturing processes, the necessity of their use has diminished with the advent of modern manufacturing capabilities. Advanced camera systems, sophisticated algorithms, improved motion control, and adaptive manufacturing processes have enabled more accurate and reliable component placement without strict reliance on fiducial markers.
However, fiducial markers still play a role in certain situations, such as high-precision applications, complex PCB designs, legacy equipment compatibility, and as a means of redundancy and error prevention. When including fiducial markers on a PCB design, it is essential to follow best practices regarding their quantity, size, shape, placement, contrast, and consistency.
Ultimately, the decision to include fiducial markers on a PCB should be based on a careful consideration of the specific manufacturing requirements, the capabilities of the assembly equipment being used, and the demands of the end application. By understanding the role of fiducial markers in modern PCB manufacturing and adopting the appropriate design practices, designers and manufacturers can ensure the production of high-quality, reliable PCBs that meet the needs of today’s complex electronic devices.
Leave a Reply