The Importance of PCBs in Medical Devices
PCBs are essential components in medical devices, as they provide the necessary electrical connections and support for various electronic components. These boards are designed to withstand the rigorous demands of medical applications, ensuring reliable performance and patient safety. Some of the key benefits of using PCBs in medical devices include:
-
Miniaturization: PCBs allow for the development of compact and lightweight medical devices, making them more portable and easier to use in various healthcare settings.
-
Reliability: Medical PCBs are manufactured to strict quality standards, ensuring they can withstand harsh environments and provide consistent performance over extended periods.
-
Customization: PCBs can be customized to meet the specific requirements of medical devices, allowing for the integration of unique features and functionalities.
-
Cost-effectiveness: The use of PCBs in medical devices helps reduce manufacturing costs, as they can be produced in large quantities with high precision and consistency.
Applications of PCBs in the Medical Industry
PCBs find applications in a wide range of medical devices and equipment. Some of the most common applications include:
1. Diagnostic Equipment
Medical PCBs are used in various diagnostic equipment, such as:
- Magnetic Resonance Imaging (MRI) machines
- Computed Tomography (CT) scanners
- X-ray machines
- Ultrasound devices
- Electrocardiogram (ECG) machines
These devices rely on PCBs to process and display diagnostic images and data, enabling healthcare professionals to make accurate diagnoses and develop effective treatment plans.
2. Monitoring Systems
PCBs are crucial components in patient monitoring systems, which continuously track vital signs and other health parameters. Some examples of monitoring systems that utilize medical PCBs include:
- Vital signs monitors
- Pulse oximeters
- Blood glucose monitors
- Fetal monitors
- Electroencephalogram (EEG) machines
These systems help healthcare providers monitor patients’ conditions in real-time, allowing for prompt intervention when necessary.
3. Implantable Devices
Implantable medical devices, such as pacemakers, defibrillators, and neurostimulators, rely on PCBs to function properly. These boards are designed to be compact, lightweight, and biocompatible, ensuring they can be safely implanted in the human body. PCBs in implantable devices are responsible for:
- Regulating electrical impulses
- Processing and storing data
- Communicating with external programming devices
4. Surgical Equipment
PCBs play a vital role in surgical equipment, enabling precise control and automation of various surgical procedures. Some examples of surgical equipment that incorporate medical PCBs include:
- Robotic surgical systems
- Electrosurgical units
- Surgical lasers
- Surgical navigation systems
These devices help surgeons perform complex procedures with greater accuracy and minimal invasiveness, leading to better patient outcomes and faster recovery times.
5. Therapeutic Devices
Medical PCBs are used in a variety of therapeutic devices designed to treat specific conditions or alleviate symptoms. Some examples include:
- Infusion pumps
- Ventilators
- Deep brain stimulation devices
- Transcutaneous electrical nerve stimulation (TENS) units
- Continuous positive airway pressure (CPAP) machines
These devices rely on PCBs to control the delivery of medications, regulate breathing, or provide targeted electrical stimulation for pain relief or symptom management.
Types of PCBs Used in Medical Devices
Medical devices employ various types of PCBs, each designed to meet specific requirements and performance criteria. Some of the most common types of medical PCBs include:
1. Rigid PCBs
Rigid PCBs are the most widely used type in medical devices. They are made from a solid substrate material, typically FR-4, and offer excellent dimensional stability and durability. Rigid PCBs are suitable for applications that require high reliability and long-term performance, such as:
- Diagnostic imaging equipment
- Patient monitoring systems
- Surgical navigation devices
2. Flexible PCBs
Flexible PCBs, also known as flex circuits, are made from thin, flexible materials like polyimide or polyester. They are designed to bend and fit into compact spaces, making them ideal for applications that require conformity to irregular shapes or motion. Some examples of medical devices that use flexible PCBs include:
- Wearable monitoring devices
- Endoscopic cameras
- Cochlear implants
- Catheter-based devices
3. Rigid-Flex PCBs
Rigid-flex PCBs combine the benefits of both rigid and flexible PCBs, offering a hybrid solution for medical devices that require both stability and flexibility. These boards consist of rigid sections connected by flexible interconnects, allowing for three-dimensional packaging and improved reliability. Rigid-flex PCBs are commonly used in:
- Implantable devices
- Portable medical equipment
- Wearable health monitors
4. High-Density Interconnect (HDI) PCBs
HDI PCBs feature finer trace widths, smaller vias, and higher component density compared to traditional PCBs. They enable the development of compact, high-performance medical devices with advanced functionality. HDI PCBs are particularly useful in applications such as:
- Miniaturized implantable devices
- Advanced diagnostic equipment
- Portable medical instruments
5. Microwave and RF PCBs
Microwave and RF PCBs are designed to handle high-frequency signals, making them essential for medical devices that utilize wireless communication or imaging technologies. These boards require specialized materials and design techniques to minimize signal loss and interference. Some examples of medical applications that use microwave and RF PCBs include:
- Wireless patient monitoring systems
- MRI machines
- Telemedicine devices
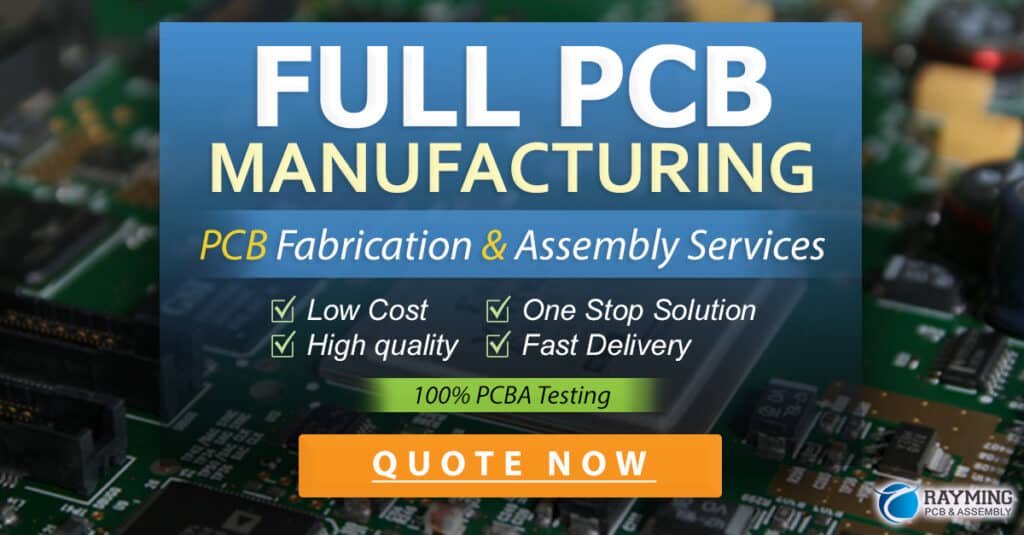
Manufacturing Considerations for Medical PCBs
The manufacturing of medical PCBs requires strict adherence to quality standards and regulations to ensure patient safety and device reliability. Some key considerations in the manufacturing process include:
1. Material Selection
Medical PCBs must be manufactured using biocompatible materials that can withstand sterilization processes and exposure to bodily fluids. Common materials used in medical PCBs include:
- FR-4
- Polyimide
- Liquid crystal polymer (LCP)
- Ceramic substrates
2. Cleanliness and Contamination Control
Medical PCBs must be manufactured in a clean environment to minimize the risk of contamination. This involves the use of specialized cleaning processes, such as:
- Ultrasonic cleaning
- Plasma cleaning
- Vapor degreasing
3. Sterilization Compatibility
Medical PCBs used in devices that come into contact with patients or sterile environments must be compatible with sterilization methods. Common sterilization methods include:
- Autoclave sterilization
- Ethylene oxide (EtO) sterilization
- Gamma radiation sterilization
4. Regulatory Compliance
Medical PCBs must comply with various regulatory standards to ensure patient safety and device performance. Some of the key standards and regulations include:
- ISO 13485: Quality management systems for medical devices
- IEC 60601: Safety and performance standards for medical electrical equipment
- FDA 21 CFR Part 820: Quality system regulations for medical devices
Future Trends in Medical PCBs
As medical technology continues to advance, PCBs will play an increasingly important role in enabling new and innovative devices. Some of the future trends in medical PCBs include:
1. Increased Miniaturization
The demand for smaller, more portable medical devices will drive the development of even more compact PCBs. This will involve the use of advanced manufacturing techniques, such as 3D printing and embedded components, to create highly integrated and space-efficient boards.
2. Wireless Connectivity
The growing adoption of wireless technologies in healthcare will require medical PCBs to incorporate advanced wireless capabilities, such as Bluetooth Low Energy (BLE), Wi-Fi, and 5G. This will enable the development of more connected and interoperable medical devices, improving patient monitoring and data sharing.
3. Flexible and Stretchable Electronics
The development of flexible and stretchable PCBs will enable the creation of new types of medical devices that can conform to the human body and provide continuous monitoring. These boards will be made from advanced materials, such as graphene and conductive polymers, that can withstand repeated stretching and bending.
4. Integration of Artificial Intelligence (AI)
The integration of AI and machine learning algorithms into medical devices will require PCBs to support high-performance computing and data processing. This will involve the use of advanced components, such as system-on-chip (SoC) solutions and high-bandwidth memory, to enable real-time data analysis and decision-making.
Conclusion
PCBs play a critical role in the development and functionality of medical devices, enabling healthcare professionals to provide accurate diagnoses, effective treatments, and improved patient care. The various types of medical PCBs, including rigid, flexible, rigid-flex, HDI, and microwave/RF boards, are designed to meet the specific requirements of different medical applications. As medical technology continues to advance, PCBs will evolve to support new and innovative devices, driving the future of healthcare.
Frequently Asked Questions (FAQ)
1. What are the key benefits of using PCBs in medical devices?
PCBs offer several benefits in medical devices, including miniaturization, reliability, customization, and cost-effectiveness. They enable the development of compact, lightweight devices that can withstand harsh environments and provide consistent performance over extended periods.
2. What are some common applications of PCBs in the medical industry?
PCBs find applications in a wide range of medical devices, such as diagnostic equipment (e.g., MRI machines, CT scanners), monitoring systems (e.g., vital signs monitors, pulse oximeters), implantable devices (e.g., pacemakers, neurostimulators), surgical equipment (e.g., robotic surgical systems, electrosurgical units), and therapeutic devices (e.g., infusion pumps, CPAP machines).
3. What types of PCBs are commonly used in medical devices?
The most common types of PCBs used in medical devices include rigid PCBs, flexible PCBs, rigid-flex PCBs, high-density interconnect (HDI) PCBs, and microwave/RF PCBs. Each type is designed to meet specific requirements and performance criteria for different medical applications.
4. What are the key manufacturing considerations for medical PCBs?
Manufacturing medical PCBs requires strict adherence to quality standards and regulations. Key considerations include material selection (using biocompatible materials), cleanliness and contamination control (specialized cleaning processes), sterilization compatibility (autoclave, EtO, gamma radiation), and regulatory compliance (ISO 13485, IEC 60601, FDA 21 CFR Part 820).
5. What are some future trends in medical PCBs?
Future trends in medical PCBs include increased miniaturization (using advanced manufacturing techniques), wireless connectivity (incorporating Bluetooth, Wi-Fi, 5G), flexible and stretchable electronics (using advanced materials like graphene and conductive polymers), and the integration of artificial intelligence (supporting high-performance computing and data processing).
Type of PCB | Key Features | Common Medical Applications |
---|---|---|
Rigid PCBs | Solid substrate, excellent dimensional stability and durability | Diagnostic imaging equipment, patient monitoring systems, surgical navigation devices |
Flexible PCBs | Thin, flexible materials, able to bend and fit into compact spaces | Wearable monitoring devices, endoscopic cameras, cochlear implants, catheter-based devices |
Rigid-Flex PCBs | Combination of rigid and flexible sections, allows for 3D packaging and improved reliability | Implantable devices, portable medical equipment, wearable health monitors |
HDI PCBs | Finer trace widths, smaller vias, higher component density | Miniaturized implantable devices, advanced diagnostic equipment, portable medical instruments |
Microwave and RF PCBs | Designed to handle high-frequency signals, minimizes signal loss and interference | Wireless patient monitoring systems, MRI machines, telemedicine devices |
Leave a Reply