Introduction to DFM and Professional Development in Design
Design for Manufacturing (DFM) is a crucial aspect of product development that focuses on optimizing the design of a product to make it easier, faster, and more cost-effective to manufacture. DFM involves considering the manufacturing processes, materials, and limitations during the design phase to minimize production costs and improve product quality. Professional development in design is essential for designers to stay up-to-date with the latest trends, technologies, and best practices in DFM.
The Importance of DFM in Product Development
DFM plays a vital role in product development by:
- Reducing manufacturing costs
- Improving product quality
- Shortening time-to-market
- Enhancing product reliability and durability
- Facilitating smooth transition from design to production
By incorporating DFM principles early in the design process, designers can avoid costly redesigns and production delays, ultimately leading to a more successful product launch.
Key Elements of DFM
To effectively implement DFM, designers should consider the following key elements:
- Material selection
- Choose materials that are easy to process, readily available, and cost-effective
-
Consider the material properties, such as strength, durability, and compatibility with the manufacturing processes
-
Manufacturing processes
- Select manufacturing processes that are suitable for the product design and production volume
- Optimize the design to leverage the capabilities of the chosen manufacturing processes
-
Minimize the number of manufacturing steps and operations to reduce costs and lead times
-
Tolerances and dimensions
- Specify realistic tolerances and dimensions that are achievable with the selected manufacturing processes
- Avoid overly tight tolerances that can increase production costs and lead times
-
Use standard tolerances and dimensions whenever possible to simplify manufacturing and reduce costs
-
Assembly and disassembly
- Design products that are easy to assemble and disassemble for maintenance and repair
- Minimize the number of parts and fasteners to reduce assembly time and costs
-
Use modular designs and standard components to facilitate assembly and disassembly
-
Design for testing and inspection
- Incorporate features that allow for easy testing and inspection during the manufacturing process
- Use non-destructive testing methods whenever possible to avoid damaging the product
- Design products with clear and accessible test points for efficient quality control
Professional Development Opportunities in DFM
To excel in DFM and stay competitive in the field, designers should continuously engage in professional development activities. Some of the key opportunities for professional development in DFM include:
1. Workshops and Seminars
Attending workshops and seminars on DFM is an excellent way for designers to learn about the latest trends, technologies, and best practices in the field. These events provide opportunities to network with other professionals, share experiences, and gain insights from industry experts.
2. Online Courses and Certifications
Online courses and certifications offer a flexible and convenient way for designers to enhance their skills and knowledge in DFM. Many universities, professional organizations, and online learning platforms offer courses and certifications in DFM, covering topics such as:
- Design for Assembly (DFA)
- Design for Manufacturability and Assembly (DFMA)
- Lean manufacturing
- Six Sigma
- Computer-Aided Design (CAD) and Computer-Aided Manufacturing (CAM)
3. Industry Conferences and Trade Shows
Industry conferences and trade shows provide valuable opportunities for designers to stay up-to-date with the latest developments in DFM and network with other professionals in the field. Some of the popular conferences and trade shows related to DFM include:
- International Forum on Design for Manufacture and Assembly (DFMA Forum)
- RAPID + TCT Conference
- Manufacturing Technology Show (MTS)
- Design & Manufacturing Midwest
4. Professional Organizations and Associations
Joining professional organizations and associations related to DFM can provide designers with access to valuable resources, networking opportunities, and professional development activities. Some of the relevant organizations include:
- American Society of Mechanical Engineers (ASME)
- Society of Manufacturing Engineers (SME)
- Institute of Industrial and Systems Engineers (IISE)
- Design Management Institute (DMI)
5. Mentorship and Coaching
Seeking mentorship and coaching from experienced professionals in the field of DFM can help designers accelerate their professional growth and navigate challenges in their careers. Mentors can provide guidance, advice, and support, helping designers to develop their skills, expand their network, and advance their careers.
Best Practices for Implementing DFM in Product Development
To successfully implement DFM in product development, designers should follow these best practices:
- Collaborate with cross-functional teams
- Involve manufacturing, quality, and supply chain experts early in the design process
-
Foster open communication and collaboration to identify and address potential manufacturing challenges
-
Use DFM software and tools
- Leverage CAD, CAM, and simulation software to analyze and optimize product designs for manufacturability
-
Use DFM guidelines and checklists to ensure that designs comply with manufacturing best practices
-
Conduct regular design reviews
- Schedule regular design reviews to assess the manufacturability of the product design
- Involve stakeholders from different functions to provide diverse perspectives and insights
-
Use a structured approach, such as the Design for Manufacturability and Assembly (DFMA) methodology, to guide the review process
-
Prototype and test early
- Build prototypes early in the design process to validate the design and identify potential manufacturing issues
- Use rapid prototyping techniques, such as 3D printing, to quickly iterate and refine the design
-
Conduct thorough testing to ensure that the product meets performance and quality requirements
-
Monitor and continuously improve
- Establish key performance indicators (KPIs) to monitor the effectiveness of the DFM process
- Collect and analyze data on manufacturing performance, quality, and costs
- Use the data to identify areas for improvement and implement corrective actions
- Continuously review and update DFM guidelines and best practices based on lessons learned and new technologies
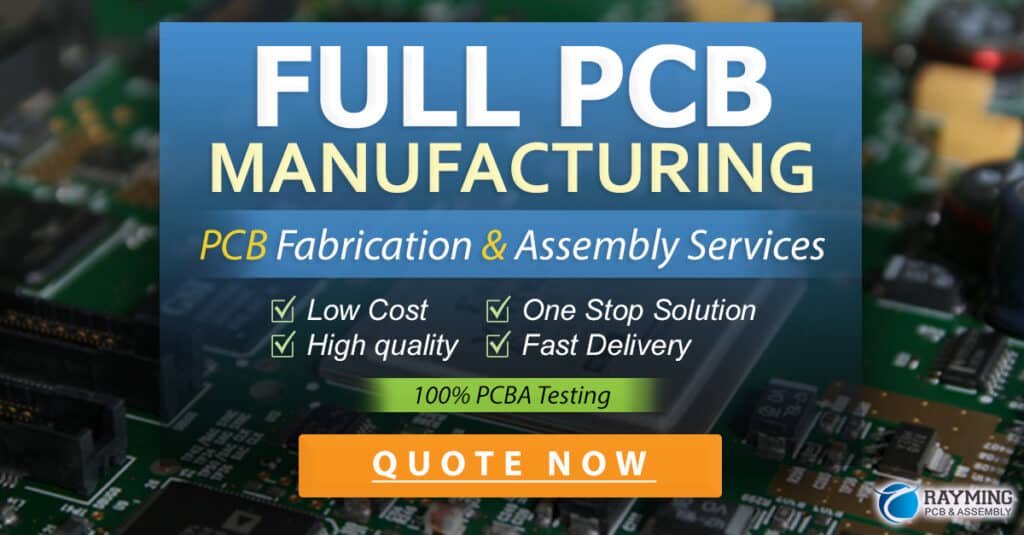
Case Studies: Successful DFM Implementation
Case Study 1: Apple’s iPhone
Apple is known for its innovative product designs and efficient manufacturing processes. The company’s success in the smartphone market can be attributed, in part, to its effective implementation of DFM principles. Some of the key DFM strategies used by Apple in the design and manufacturing of the iPhone include:
- Minimizing the number of parts and components
- Using standardized components and interfaces
- Designing for automated assembly
- Leveraging advanced manufacturing technologies, such as CNC machining and injection molding
- Collaborating closely with suppliers to ensure the availability and quality of components
By implementing these DFM strategies, Apple has been able to consistently produce high-quality iPhones at a large scale while maintaining competitive pricing.
Case Study 2: Tesla’s Model 3
Tesla’s Model 3 is an example of how DFM can be applied to the design and manufacturing of electric vehicles. Some of the key DFM strategies used by Tesla in the development of the Model 3 include:
- Using a modular platform design to simplify manufacturing and assembly
- Minimizing the number of parts and components
- Designing for automated assembly, including the use of robots and conveyor systems
- Leveraging advanced manufacturing technologies, such as aluminum casting and high-speed stamping
- Vertically integrating the production of key components, such as batteries and motors
By implementing these DFM strategies, Tesla has been able to ramp up production of the Model 3 and achieve its goal of making electric vehicles more accessible and affordable to a wider market.
Challenges and Future Trends in DFM
Despite the many benefits of DFM, there are still challenges that designers and manufacturers face in implementing these principles effectively. Some of the key challenges include:
- Balancing design innovation with manufacturing feasibility
- Keeping up with rapidly evolving technologies and materials
- Managing the complexity of global supply chains and logistics
- Ensuring the quality and reliability of products manufactured in different locations
- Addressing the skills gap and shortage of qualified professionals in DFM
To overcome these challenges and stay competitive in the future, designers and manufacturers will need to:
- Embrace digital technologies, such as AI, machine learning, and the Internet of Things (IoT), to optimize design and manufacturing processes
- Invest in the development of new materials and processes that enable greater design flexibility and manufacturing efficiency
- Foster a culture of continuous learning and professional development to keep up with the latest trends and best practices in DFM
- Collaborate more closely with suppliers, customers, and other stakeholders to create a more integrated and resilient supply chain
- Develop strategies to attract, retain, and upskill talent in the field of DFM
Frequently Asked Questions (FAQ)
- What is Design for Manufacturing (DFM)?
-
Design for Manufacturing (DFM) is a design approach that focuses on optimizing product designs to make them easier, faster, and more cost-effective to manufacture. DFM involves considering the manufacturing processes, materials, and limitations during the design phase to minimize production costs and improve product quality.
-
Why is DFM important in product development?
-
DFM is important in product development because it helps to reduce manufacturing costs, improve product quality, shorten time-to-market, enhance product reliability and durability, and facilitate a smooth transition from design to production. By incorporating DFM principles early in the design process, designers can avoid costly redesigns and production delays, ultimately leading to a more successful product launch.
-
What are some key elements of DFM that designers should consider?
-
Some key elements of DFM that designers should consider include material selection, manufacturing processes, tolerances and dimensions, assembly and disassembly, and design for testing and inspection. By optimizing these elements, designers can create products that are easier and more cost-effective to manufacture.
-
How can designers engage in professional development to enhance their skills in DFM?
-
Designers can engage in professional development to enhance their skills in DFM by attending workshops and seminars, taking online courses and certifications, participating in industry conferences and trade shows, joining professional organizations and associations, and seeking mentorship and coaching from experienced professionals in the field.
-
What are some best practices for implementing DFM in product development?
- Some best practices for implementing DFM in product development include collaborating with cross-functional teams, using DFM software and tools, conducting regular design reviews, prototyping and testing early, and monitoring and continuously improving the DFM process. By following these best practices, designers can create products that are optimized for manufacturability and deliver superior value to customers.
Conclusion
Design for Manufacturing (DFM) is a critical aspect of product development that can significantly impact the success of a product in the market. By considering the manufacturing processes, materials, and limitations during the design phase, designers can create products that are easier, faster, and more cost-effective to manufacture, ultimately leading to improved product quality, reduced costs, and shorter time-to-market.
To excel in DFM and stay competitive in the field, designers should continuously engage in professional development activities, such as attending workshops and seminars, taking online courses and certifications, participating in industry conferences and trade shows, joining professional organizations and associations, and seeking mentorship and coaching from experienced professionals.
By following best practices for implementing DFM, such as collaborating with cross-functional teams, using DFM software and tools, conducting regular design reviews, prototyping and testing early, and monitoring and continuously improving the DFM process, designers can create products that are optimized for manufacturability and deliver superior value to customers.
As technologies and materials continue to evolve, designers and manufacturers will need to stay up-to-date with the latest trends and best practices in DFM to overcome challenges and remain competitive in the future. By embracing digital technologies, investing in new materials and processes, fostering a culture of continuous learning and professional development, collaborating more closely with stakeholders, and developing strategies to attract and retain talent, the field of DFM will continue to play a vital role in driving innovation and success in product development.
Leave a Reply