Introduction to Annular Rings in PCB Design
In the world of printed circuit board (PCB) design, annular rings are a crucial component that plays a significant role in ensuring the reliability and functionality of the board. Annular rings, also known as “annular ring PCB,” refer to the copper area surrounding the drilled hole on a PCB. These rings provide a connection between the drilled hole and the copper trace, allowing for electrical continuity and mechanical stability.
The Importance of Annular Rings
Annular rings serve several essential functions in PCB design:
-
Electrical Connection: The primary purpose of annular rings is to establish an electrical connection between the drilled hole and the copper trace. This connection allows for the flow of electrical signals through the board, enabling the various components to communicate and function as intended.
-
Mechanical Stability: Annular rings also contribute to the mechanical stability of the PCB. They help to anchor the drilled hole to the surrounding copper area, preventing the hole from shifting or becoming disconnected during the manufacturing process or when the board is subjected to physical stress.
-
Manufacturing Tolerance: Annular rings provide a margin of error during the drilling process. The presence of annular rings ensures that even if the drill bit slightly deviates from the intended location, there will still be sufficient copper contact to maintain electrical continuity.
Nonfunctional Pads: Understanding Their Role
Nonfunctional pads, also referred to as “non-functional pads” or “NFPs,” are copper pads on a PCB that do not serve any electrical purpose. These pads are intentionally included in the PCB design for various reasons, despite not being connected to any electrical components or traces.
The Purpose of Nonfunctional Pads
Nonfunctional pads serve several purposes in PCB design:
-
Mechanical Support: Nonfunctional pads can provide additional mechanical support to the PCB. They can be strategically placed to improve the overall structural integrity of the board, especially in areas that are prone to physical stress or vibration.
-
Thermal Management: In some cases, nonfunctional pads are used for thermal management purposes. They can help dissipate heat generated by nearby components, preventing overheating and ensuring optimal performance of the PCB.
-
Manufacturing Consistency: Nonfunctional pads can be added to maintain consistency in the manufacturing process. They can help balance the copper distribution across the board, reducing the risk of warping or other manufacturing defects.
-
Aesthetics: In certain designs, nonfunctional pads are included for aesthetic reasons. They can contribute to a visually appealing and symmetrical layout of the PCB, enhancing its overall appearance.
Annular Rings vs. Nonfunctional Pads: Key Differences
While both annular rings and nonfunctional pads are important elements in PCB design, they serve distinct purposes and have key differences:
Feature | Annular Rings | Nonfunctional Pads |
---|---|---|
Purpose | Electrical connection and mechanical stability | Mechanical support, thermal management, manufacturing consistency, aesthetics |
Electrical Functionality | Essential for electrical connectivity | No electrical functionality |
Location | Surrounding drilled holes | Can be placed anywhere on the PCB |
Manufacturing Considerations | Critical for drilling and plating processes | Not critical for manufacturing, but can impact overall board quality |
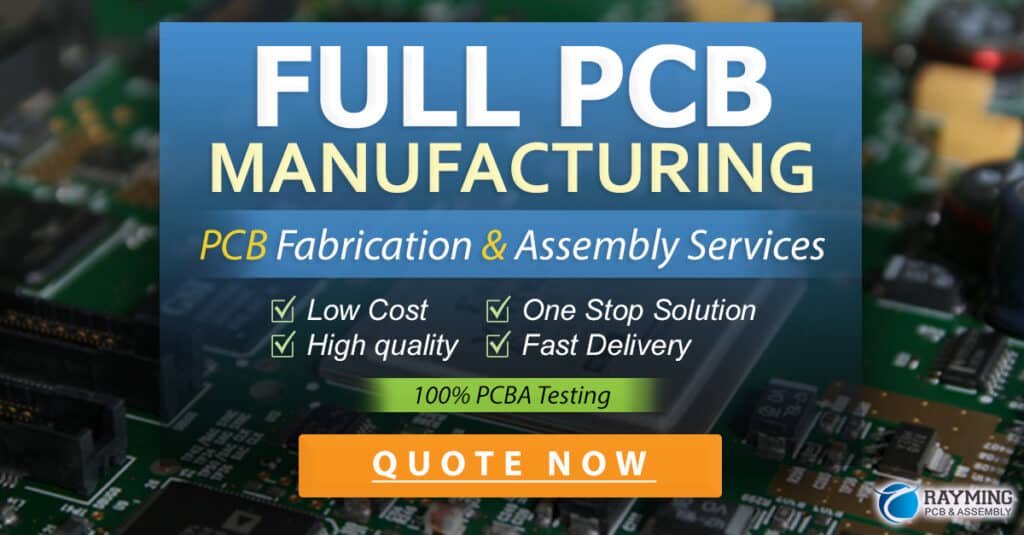
Designing with Annular Rings and Nonfunctional Pads
When designing a PCB, it is essential to consider the use of annular rings and nonfunctional pads to ensure optimal performance, reliability, and manufacturability.
Annular Ring Design Considerations
-
Size: The size of the annular ring should be appropriate for the drilled hole size and the manufacturing capabilities. Insufficient annular ring size can lead to poor electrical connections and mechanical instability, while excessively large annular rings can waste valuable board space.
-
Spacing: Annular rings should be spaced appropriately to prevent shorting between adjacent holes. The spacing requirements may vary depending on the PCB fabrication capabilities and the specific design requirements.
-
Plating: Annular rings should be adequately plated to ensure good electrical conductivity and mechanical strength. The plating thickness and material should be chosen based on the application and the environmental conditions the PCB will be exposed to.
Nonfunctional Pad Design Considerations
-
Placement: Nonfunctional pads should be strategically placed to provide the desired mechanical support, thermal management, or aesthetic effects without interfering with the electrical functionality of the board.
-
Size: The size of nonfunctional pads should be appropriate for their intended purpose. Larger pads may provide better mechanical support or thermal dissipation, while smaller pads may be sufficient for aesthetic purposes.
-
Clearance: Nonfunctional pads should maintain sufficient clearance from other components and traces to prevent unintended electrical connections or interference.
-
Manufacturing Compatibility: The inclusion of nonfunctional pads should be compatible with the chosen manufacturing process. Some manufacturing techniques may have limitations or specific requirements for nonfunctional pads.
Best Practices for Using Annular Rings and Nonfunctional Pads
To effectively incorporate annular rings and nonfunctional pads into your PCB design, consider the following best practices:
-
Follow Manufacturing Guidelines: Consult with your PCB manufacturer to understand their specific guidelines and capabilities regarding annular rings and nonfunctional pads. Adhere to their recommended sizes, spacings, and other requirements to ensure successful manufacturing.
-
Use Appropriate Software Tools: Utilize PCB design software that supports the creation and management of annular rings and nonfunctional pads. These tools can help you define the necessary parameters and ensure compliance with design rules.
-
Perform Design Reviews: Conduct thorough design reviews to verify the correct placement, size, and spacing of annular rings and nonfunctional pads. Collaborate with experienced PCB designers or engineers to identify any potential issues or improvements.
-
Consider Signal Integrity: When placing annular rings and nonfunctional pads, consider their impact on signal integrity. Ensure that they do not introduce unwanted capacitance, crosstalk, or other signal integrity issues that could affect the performance of the PCB.
-
Document and Communicate: Clearly document the purpose and specifications of annular rings and nonfunctional pads in your PCB design files and communication with the manufacturing team. This helps ensure that everyone involved in the project understands their significance and can take appropriate actions during fabrication and assembly.
Frequently Asked Questions (FAQ)
-
What is the minimum annular ring size required for reliable PCB manufacturing?
The minimum annular ring size depends on the specific manufacturing capabilities and the hole size. Generally, a minimum annular ring of 0.15mm to 0.20mm is recommended, but it is best to consult with your PCB manufacturer for their specific requirements. -
Can nonfunctional pads be used for grounding purposes?
While nonfunctional pads are not primarily intended for grounding, they can be connected to the ground plane if needed. However, it is important to clearly communicate this requirement to the manufacturing team to ensure proper connections are made. -
How do annular rings affect the impedance of a PCB?
Annular rings can introduce additional capacitance and inductance to the PCB, which can impact the impedance of the traces. Designers should consider the effect of annular rings on impedance-controlled traces and make necessary adjustments to maintain the desired impedance values. -
Can nonfunctional pads be removed from a PCB design to save space?
Yes, nonfunctional pads can be removed if they are not serving any specific purpose and if their removal does not compromise the mechanical stability, thermal management, or manufacturing consistency of the PCB. However, it is important to evaluate the impact of their removal on the overall design before making any changes. -
What are the common issues encountered with annular rings during PCB manufacturing?
Common issues with annular rings include insufficient annular ring size, poor plating adhesion, and breakouts or cracks in the annular ring. These issues can lead to electrical discontinuity, mechanical weakness, and reduced reliability of the PCB. Proper design, manufacturing process control, and quality inspection can help mitigate these issues.
Conclusion
Annular rings and nonfunctional pads are essential elements in PCB design that contribute to the overall functionality, reliability, and manufacturability of the board. Annular rings provide critical electrical connections and mechanical stability, while nonfunctional pads serve various purposes such as mechanical support, thermal management, manufacturing consistency, and aesthetics.
When designing a PCB, it is crucial to understand the roles and differences between annular rings and nonfunctional pads and to consider their specific design requirements. By following best practices, collaborating with experienced professionals, and adhering to manufacturing guidelines, designers can effectively incorporate these elements into their PCB layouts to achieve optimal performance and reliability.
As technology advances and PCB designs become more complex, the proper use of annular rings and nonfunctional pads will continue to play a vital role in ensuring the success of electronic products. By staying informed about the latest design techniques and industry standards, PCB designers can navigate the challenges and opportunities presented by these critical components, ultimately delivering high-quality and robust PCBs that meet the demands of modern electronics.
Leave a Reply