Introduction to Annular Rings in PCB Design
Annular rings, also known as copper rings or pads, are critical components in the design of printed circuit boards (PCBs). These rings surround the drilled holes on a PCB and provide a conductive surface for soldering components or connecting layers through vias. In multilayer PCB design, annular rings play a crucial role in ensuring proper electrical connectivity and mechanical stability.
The Importance of Annular Rings
Annular rings serve several essential functions in PCB design:
-
Electrical connectivity: Annular rings provide a conductive surface for soldering components or connecting layers through vias, ensuring proper electrical connectivity throughout the PCB.
-
Mechanical stability: The presence of annular rings around drilled holes helps to reinforce the mechanical strength of the PCB, preventing damage during handling or operation.
-
Manufacturing reliability: Adequate annular ring sizes and tolerances are essential for reliable PCB manufacturing processes, such as drilling, plating, and soldering.
Annular Ring Sizes and Tolerances
When designing annular rings for multilayer PCBs, it is crucial to consider the appropriate sizes and tolerances to ensure proper functionality and manufacturability. The size of an annular ring is typically measured by its inner diameter (ID) and outer diameter (OD).
Parameter | Description |
---|---|
Inner Diameter (ID) | The diameter of the drilled hole in the center of the annular ring |
Outer Diameter (OD) | The outer diameter of the annular ring, including the copper pad |
The difference between the outer diameter and inner diameter is known as the annular ring width. Minimum annular ring width is a critical design parameter that ensures sufficient copper around the drilled hole for proper electrical connection and mechanical stability.
Annular ring tolerances are equally important, as they account for potential variations in the manufacturing process, such as drill wander or misalignment. Tight tolerances are essential to maintain the minimum annular ring width and prevent issues like breakout or insufficient copper coverage.
Designing Annular Rings for Multilayer PCBs
Factors Affecting Annular Ring Design
Several factors influence the design of annular rings in multilayer PCBs:
-
PCB layer count: As the number of layers in a PCB increases, the complexity of annular ring design also increases. Ensuring proper alignment and connectivity between layers becomes more challenging.
-
Via types: Different types of vias, such as through-hole, blind, or buried vias, require specific annular ring designs to ensure proper connectivity and manufacturability.
-
PCB material: The choice of PCB material, such as FR-4, high-frequency laminates, or flexible substrates, can impact the annular ring design due to different thermal expansion coefficients and mechanical properties.
-
Manufacturing capabilities: The manufacturing capabilities of the PCB fabricator, such as minimum drill sizes, copper plating thicknesses, and registration accuracy, must be considered when designing annular rings.
Best Practices for Annular Ring Design
To ensure optimal performance and manufacturability of multilayer PCBs, consider the following best practices when designing annular rings:
-
Adhere to minimum annular ring width: Maintain the minimum annular ring width as specified by the PCB manufacturer or industry standards, such as IPC-6012. This ensures sufficient copper coverage around the drilled holes for proper connectivity and mechanical stability.
-
Account for drill tolerances: Consider the potential variations in drill sizes and positions when designing annular rings. Incorporate appropriate tolerances to prevent issues like breakout or insufficient copper coverage.
-
Optimize via placement: Carefully plan the placement of vias and their associated annular rings to minimize the impact on signal integrity and routing density. Avoid placing vias too close to component pads or in areas with high-speed signals.
-
Consider via filling: In high-density designs or when using via-in-pad techniques, consider filling the vias with conductive or non-conductive materials to improve reliability and avoid solder wicking issues during assembly.
-
Collaborate with PCB manufacturers: Work closely with your PCB manufacturer to understand their capabilities, limitations, and recommended design guidelines for annular rings. Their expertise can help optimize your design for manufacturability and reliability.
Common Challenges and Solutions
Drill Wander and Misalignment
One of the most common challenges in annular ring design is drill wander or misalignment. This occurs when the drilled holes deviate from their intended positions, causing the annular rings to be off-center or partially exposed.
To mitigate drill wander and misalignment:
-
Use larger annular rings: Increasing the annular ring size provides more tolerance for drill wander and misalignment, ensuring sufficient copper coverage around the holes.
-
Implement tighter tolerances: Work with your PCB manufacturer to implement tighter tolerances for drilling and layer registration. This minimizes the impact of drill wander and misalignment on annular ring integrity.
-
Utilize advanced drilling techniques: Employ advanced drilling techniques, such as controlled-depth drilling or laser drilling, to achieve higher precision and reduce the occurrence of drill wander.
Copper Plating Thickness Variations
Variations in copper plating thickness can impact the integrity of annular rings, especially in multilayer PCBs. Insufficient copper plating can lead to weak connections or even open circuits, while excessive plating can cause issues with via filling or solder wicking.
To address copper plating thickness variations:
-
Specify appropriate plating thicknesses: Work with your PCB manufacturer to determine the appropriate copper plating thicknesses for your design, considering the number of layers, via sizes, and electrical requirements.
-
Implement plating thickness controls: Ensure that your PCB manufacturer has robust process controls in place to maintain consistent copper plating thicknesses across the board and within specified tolerances.
-
Consider alternative via protection methods: In some cases, alternative via protection methods, such as via tenting or filling, can be used to mitigate the impact of copper plating thickness variations on annular ring integrity.
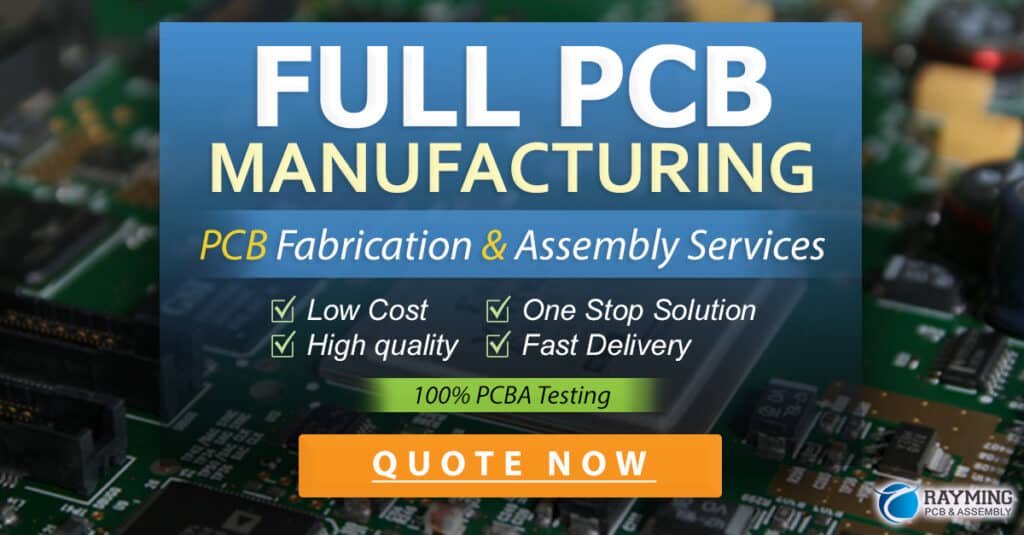
FAQ
-
Q: What is the minimum annular ring width recommended for multilayer PCBs?
A: The minimum annular ring width depends on various factors, such as the PCB material, layer count, and manufacturing capabilities. Typically, a minimum annular ring width of 0.15mm to 0.2mm is recommended for standard multilayer PCBs, but it is always best to consult with your PCB manufacturer for their specific guidelines. -
Q: How do I account for drill tolerances when designing annular rings?
A: To account for drill tolerances, consider adding an appropriate buffer to your annular ring dimensions. For example, if the minimum annular ring width is 0.15mm and the drill tolerance is ±0.1mm, design your annular rings with a width of at least 0.25mm to ensure sufficient copper coverage even in the worst-case scenario. -
Q: Can I use different annular ring sizes for different layers in a multilayer PCB?
A: Yes, you can use different annular ring sizes for different layers in a multilayer PCB, depending on the specific requirements of each layer. For example, power layers may require larger annular rings compared to signal layers to accommodate higher currents. However, ensure that the minimum annular ring width is maintained across all layers. -
Q: What are the consequences of insufficient annular ring width?
A: Insufficient annular ring width can lead to several issues, such as poor electrical connectivity, reduced mechanical strength, and increased risk of copper breakout during drilling or soldering processes. These issues can compromise the reliability and functionality of the PCB, leading to potential failures or performance degradation. -
Q: How can I optimize my annular ring design for high-density PCBs?
A: To optimize annular ring design for high-density PCBs, consider the following techniques: - Use via-in-pad or via-on-pad designs to maximize routing space and component placement.
- Employ microvias or blind vias to reduce the overall via size and improve layer-to-layer connectivity.
- Implement via filling or tenting to improve reliability and avoid solder wicking issues.
- Work closely with your PCB manufacturer to understand their capabilities and design guidelines for high-density PCBs.
Conclusion
Annular rings play a critical role in the design and manufacturing of multilayer PCBs, ensuring proper electrical connectivity, mechanical stability, and reliability. By understanding the importance of annular ring sizes, tolerances, and best practices, PCB designers can create robust and manufacturable designs that meet the required specifications.
When designing annular rings for multilayer PCBs, consider factors such as PCB layer count, via types, material properties, and manufacturing capabilities. Adhere to minimum annular ring widths, account for drill tolerances, optimize via placement, and collaborate with PCB manufacturers to ensure the best possible outcomes.
By staying within the specified tolerances and following industry guidelines, PCB designers can overcome common challenges like drill wander, misalignment, and copper plating thickness variations, ultimately delivering high-quality and reliable multilayer PCBs.
Leave a Reply