Introduction to PCB Manufacturing
Printed Circuit Boards (PCBs) are the backbone of modern electronics. They are used in almost every electronic device, from smartphones and computers to medical equipment and aerospace technology. PCB manufacturing is a complex process that involves several steps, each of which requires precision and attention to detail. In this ultimate guide, we will explore the PCB manufacturing process in depth, covering everything from PCB design to final inspection and testing.
What is a PCB?
A PCB is a flat board made of insulating materials, such as fiberglass or plastic, with conductive pathways printed on its surface. These pathways, known as traces, connect electronic components together to form a functional circuit. PCBs can be single-sided, double-sided, or multi-layered, depending on the complexity of the circuit and the space constraints of the device.
Why is PCB Manufacturing Important?
PCB manufacturing is crucial for the production of reliable and high-quality electronic devices. A well-designed and manufactured PCB ensures that the device functions as intended, with minimal risk of failure or malfunction. PCBs also allow for the miniaturization of electronic devices, as they can accommodate a large number of components in a small space.
The PCB Manufacturing Process
The PCB manufacturing process consists of several steps, each of which is critical to the quality and reliability of the final product. Let’s take a closer look at each step:
Step 1: PCB Design
The first step in PCB manufacturing is the design phase. This involves creating a schematic diagram of the circuit and laying out the components and traces on the PCB. pcb design software, such as Altium Designer or Eagle, is used to create the design files, which include the schematic, pcb layout, and bill of materials (BOM).
Step 2: Material Selection
Once the PCB design is complete, the next step is to select the appropriate materials for the PCB. The most common materials used in PCB manufacturing are:
- FR-4: A fiberglass-reinforced epoxy laminate that is the most widely used pcb material.
- Polyimide: A high-temperature, flexible material used in applications that require bendability or high heat resistance.
- Aluminum: Used in applications that require heat dissipation, such as LED lighting or power electronics.
The choice of material depends on the specific requirements of the application, such as temperature range, flexibility, and cost.
Step 3: pcb fabrication
The PCB fabrication process involves several sub-steps, including:
Copper Clad Laminate
The first step in PCB fabrication is to create the copper clad laminate (CCL). This is done by bonding a thin layer of copper foil to the chosen substrate material, such as FR-4 or polyimide. The copper foil is typically 1-2 oz in weight, which refers to the thickness of the copper layer.
Drilling
Once the CCL is created, the next step is to drill holes in the board for through-hole components and vias. The holes are drilled using a CNC drilling machine, which uses a drill file generated from the PCB design software.
Patterning
After drilling, the next step is to create the conductive traces on the PCB. This is done through a process called patterning, which involves applying a photoresist layer to the copper surface and exposing it to UV light through a photomask. The exposed areas of the photoresist are then developed and etched away, leaving behind the desired copper traces.
Lamination
For multi-layer PCBs, the individual layers are laminated together using heat and pressure. The layers are aligned using registration holes and bonded together with a layer of prepreg material between each layer.
Surface Finishing
The final step in PCB fabrication is to apply a surface finish to the exposed copper traces. The most common surface finishes are:
- HASL (Hot Air Solder Leveling): A tin-lead alloy is applied to the copper traces and then leveled using hot air.
- ENIG (Electroless Nickel Immersion Gold): A layer of nickel is applied to the copper traces, followed by a thin layer of gold.
- OSP (Organic Solderability Preservative): A thin, organic coating is applied to the copper traces to prevent oxidation.
The choice of surface finish depends on the specific requirements of the application, such as solderability, durability, and cost.
Step 4: Solder Mask Application
After PCB fabrication, a solder mask is applied to the board to protect the copper traces from oxidation and to prevent solder from bridging between traces during assembly. The solder mask is typically green in color, but other colors are available for specific applications.
Step 5: Silkscreen Printing
The final step in PCB manufacturing is to print the silkscreen layer on the board. This layer contains text and symbols that identify the components and their locations on the board. The silkscreen is typically white in color and is applied using a screen printing process.
Step 6: Electrical Testing
Once the PCB is complete, it undergoes electrical testing to ensure that it functions as intended. This includes continuity testing, which checks for open or short circuits, and functional testing, which verifies that the board performs its intended function.
PCB Assembly
After the PCB is manufactured, it undergoes the assembly process to add the electronic components to the board. The assembly process consists of several steps, including:
Step 1: Solder Paste Application
The first step in PCB assembly is to apply solder paste to the pads on the board where the components will be placed. This is typically done using a stencil and a solder paste printer.
Step 2: Component Placement
The next step is to place the components on the board using a pick-and-place machine. The machine uses computer vision to locate the pads on the board and place the components accurately.
Step 3: Reflow Soldering
After the components are placed, the board undergoes reflow soldering to permanently attach the components to the board. The board is heated in an oven to melt the solder paste and form a strong bond between the components and the pads.
Step 4: Inspection and Testing
The final step in PCB assembly is inspection and testing. The assembled board is visually inspected for any defects or misaligned components, and then undergoes functional testing to ensure that it performs as intended.
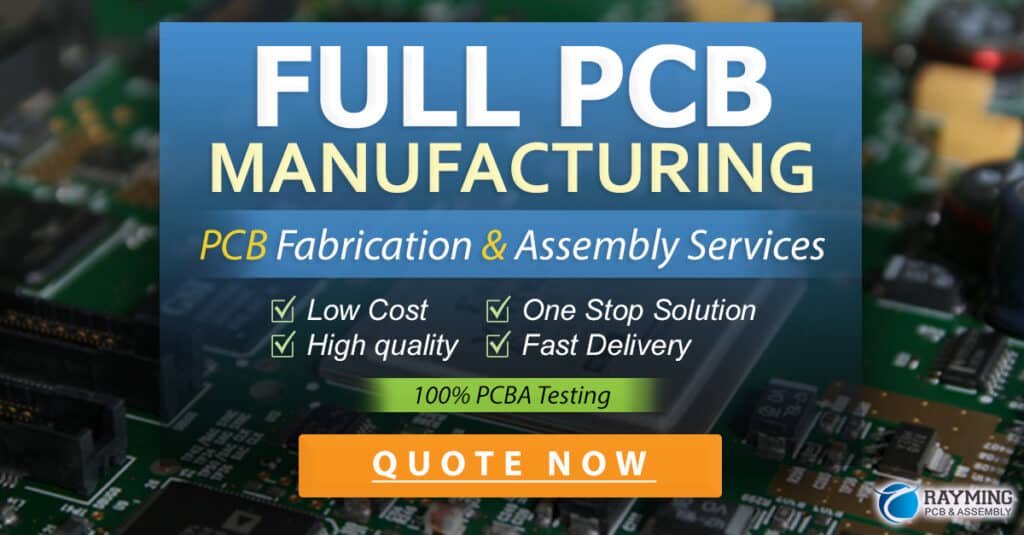
PCB Manufacturing Considerations
When designing and manufacturing a PCB, there are several considerations that must be taken into account to ensure the quality and reliability of the final product. These include:
Material Selection
As mentioned earlier, the choice of PCB material depends on the specific requirements of the application. Factors to consider include temperature range, flexibility, and cost.
Trace Width and Spacing
The width and spacing of the copper traces on the PCB must be carefully designed to ensure proper signal integrity and to prevent crosstalk between traces. The trace width and spacing also affect the manufacturing process, as narrower traces and smaller spacings require more precise manufacturing techniques.
Via Design
Vias are used to connect traces between layers in a multi-layer PCB. The size and placement of vias must be carefully designed to ensure proper signal integrity and to minimize the risk of manufacturing defects.
Component Placement
The placement of components on the PCB must be carefully planned to ensure proper signal routing and to minimize the risk of EMI (electromagnetic interference). Components should also be placed in a way that facilitates assembly and testing.
Design for Manufacturing (DFM)
DFM is a set of guidelines and best practices that are used to optimize the PCB design for manufacturing. This includes considerations such as minimum trace width and spacing, via size and placement, and component placement. Following DFM guidelines can help to minimize manufacturing defects and improve the overall quality and reliability of the PCB.
PCB Manufacturing Standards
There are several industry standards that govern the design and manufacture of PCBs. These standards ensure consistency and reliability across different manufacturers and applications. Some of the most common PCB manufacturing standards include:
IPC Standards
The IPC (Association Connecting Electronics Industries) is a global trade association that develops standards for the electronics industry. Some of the most relevant IPC standards for PCB manufacturing include:
- IPC-A-600: Acceptability of Printed Boards
- IPC-6012: Qualification and Performance Specification for Rigid Printed Boards
- IPC-2221: Generic Standard on Printed Board Design
UL Standards
Underwriters Laboratories (UL) is a global safety certification company that develops standards for electronic products. Some of the most relevant UL standards for PCB manufacturing include:
- UL 94: Standard for Safety of Flammability of Plastic Materials for Parts in Devices and Appliances
- UL 796: Standard for Safety of Printed-Wiring Boards
ISO Standards
The International Organization for Standardization (ISO) develops standards for various industries, including electronics. Some of the most relevant ISO standards for PCB manufacturing include:
- ISO 9001: Quality Management Systems
- ISO 14001: Environmental Management Systems
Frequently Asked Questions (FAQ)
What is the typical turnaround time for PCB manufacturing?
The turnaround time for PCB manufacturing varies depending on the complexity of the design and the manufacturing process used. For simple, single-layer PCBs, the turnaround time can be as short as 24 hours. For more complex, multi-layer PCBs, the turnaround time can be several weeks.
What is the minimum trace width and spacing for PCB manufacturing?
The minimum trace width and spacing for PCB manufacturing depends on the manufacturing process used and the capabilities of the manufacturer. For standard PCB manufacturing processes, the minimum trace width and spacing is typically 0.006 inches (0.15 mm). For high-density interconnect (HDI) processes, the minimum trace width and spacing can be as small as 0.003 inches (0.075 mm).
What is the difference between through-hole and surface-mount components?
Through-hole components have leads that are inserted into holes drilled in the PCB and soldered to pads on the opposite side of the board. Surface-mount components have leads that are soldered directly to pads on the surface of the board. Surface-mount components are smaller and can be placed more densely on the board, but they require more precise manufacturing techniques.
What is the difference between HASL and ENIG surface finishes?
HASL (hot air solder leveling) is a surface finish that involves applying a tin-lead alloy to the copper traces and then leveling it with hot air. ENIG (electroless nickel immersion gold) is a surface finish that involves applying a layer of nickel to the copper traces, followed by a thin layer of gold. ENIG provides better solderability and durability than HASL, but it is more expensive.
What is the purpose of a solder mask?
A solder mask is a layer of polymer that is applied to the PCB to protect the copper traces from oxidation and to prevent solder from bridging between traces during assembly. The solder mask also provides electrical insulation between traces and helps to prevent short circuits.
Conclusion
PCB manufacturing is a complex process that requires precision, attention to detail, and adherence to industry standards. By understanding the various steps involved in PCB manufacturing, from design to assembly, engineers and manufacturers can ensure the quality and reliability of their electronic products.
When designing a PCB, it is important to consider factors such as material selection, trace width and spacing, via design, and component placement. Adhering to industry standards such as IPC, UL, and ISO can also help to ensure consistency and reliability across different manufacturers and applications.
As technology continues to advance, the demand for high-quality, reliable PCBs will only continue to grow. By staying up-to-date with the latest manufacturing processes and design techniques, engineers and manufacturers can stay ahead of the curve and deliver innovative, high-performance electronic products to the market.
Leave a Reply