Introduction to Aluminum PCB Manufacturing
Aluminum Printed Circuit Boards (PCBs) are a specialized type of PCB that utilizes aluminum as the base material instead of the traditional FR-4 or other insulating materials. Aluminum PCBs, also known as Metal Core PCBs (MCPCBs), offer unique advantages over standard PCBs, making them ideal for applications that require efficient heat dissipation, such as high-power electronics, LED lighting, and automotive systems.
As an experienced aluminum PCB manufacturer, we understand the importance of delivering high-quality, reliable, and cost-effective solutions to our clients. In this article, we will explore the benefits of aluminum PCBs, their manufacturing process, and the various applications where they excel.
Benefits of Aluminum PCBs
- Enhanced thermal management
- Improved electrical performance
- Increased durability and reliability
- Lightweight and cost-effective
The Aluminum PCB Manufacturing Process
Step 1: Material Selection
The first step in manufacturing aluminum PCBs is selecting the appropriate materials. The key components include:
- Aluminum base plate
- Dielectric layer
- Copper foil
The aluminum base plate serves as the foundation for the PCB and is chosen based on factors such as thermal conductivity, thickness, and surface finish. The dielectric layer is applied on top of the aluminum to provide electrical insulation, while the copper foil is used for the conductive circuit layer.
Step 2: Circuit Design and Fabrication
Once the materials are selected, the circuit design is created using specialized software. The design is then used to fabricate the copper circuit layer on top of the dielectric layer. This process involves several sub-steps:
- Copper foil lamination
- Photoresist application
- Exposure and development
- Etching
- Photoresist removal
Step 3: Drilling and Plating
After the copper circuit layer is fabricated, holes are drilled through the aluminum PCB to accommodate components and vias. The drilled holes are then plated with copper to ensure electrical connectivity between layers.
Step 4: Solder Mask Application
A solder mask is applied to the aluminum PCB to protect the copper traces from oxidation and prevent short circuits during soldering. The solder mask also provides a visual guide for component placement.
Step 5: Surface Finish
The final step in the aluminum PCB manufacturing process is applying a surface finish to the exposed copper areas. Common surface finishes include:
- HASL (Hot Air Solder Leveling)
- ENIG (Electroless Nickel Immersion Gold)
- OSP (Organic Solderability Preservative)
The choice of surface finish depends on the specific requirements of the application, such as solderability, durability, and cost.
Applications of Aluminum PCBs
Aluminum PCBs are used in a wide range of industries and applications where thermal management and reliability are critical. Some common applications include:
- Power electronics
- Motor drives
- Inverters
-
Power supplies
-
LED lighting
- Streetlights
- Automotive lighting
-
Grow lights
-
Automotive electronics
- Engine control units
- Braking systems
-
Infotainment systems
-
Telecommunications
- Base stations
- Routers
-
Switches
-
Medical devices
- Imaging equipment
- Surgical instruments
- Wearable devices
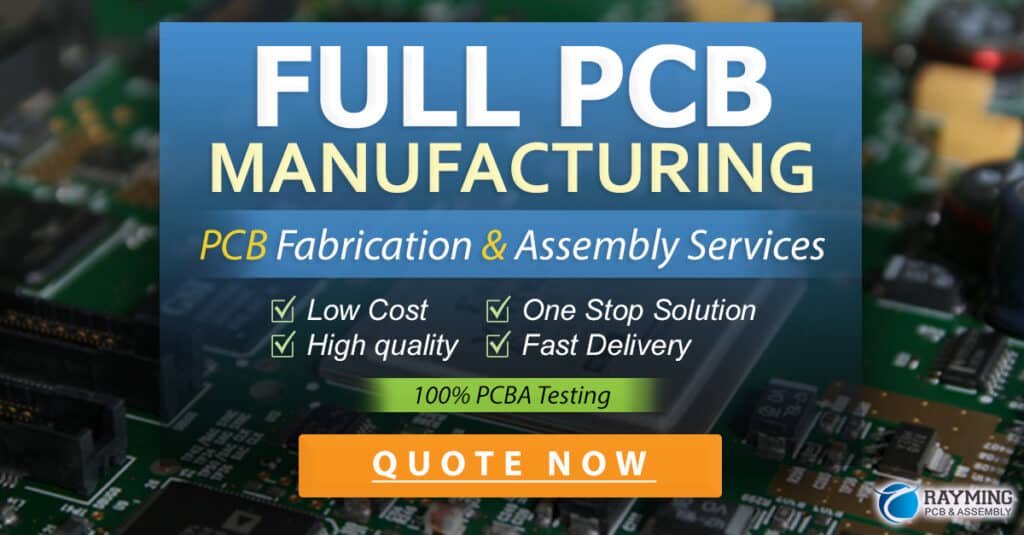
Advantages of Working with an Experienced Aluminum PCB Manufacturer
Partnering with an experienced aluminum PCB manufacturer offers several benefits:
- Expertise in material selection and design optimization
- State-of-the-art manufacturing facilities and equipment
- Strict quality control processes to ensure reliability
- Rapid prototyping and volume production capabilities
- Customized solutions tailored to specific application requirements
Frequently Asked Questions (FAQ)
1. What is the difference between aluminum PCBs and standard PCBs?
Aluminum PCBs use an aluminum base plate as the substrate, while standard PCBs use materials like FR-4. The aluminum base provides better thermal conductivity, allowing for more efficient heat dissipation.
2. Can aluminum PCBs be used in high-frequency applications?
Yes, aluminum PCBs can be used in high-frequency applications. The dielectric layer between the aluminum base and copper circuit layer helps maintain signal integrity and reduces electromagnetic interference (EMI).
3. Are aluminum PCBs more expensive than standard PCBs?
The cost of aluminum PCBs depends on several factors, such as the size, complexity, and volume of the order. While the raw materials for aluminum PCBs may be more expensive, their superior thermal management and durability can lead to cost savings in the long run.
4. What surface finishes are available for aluminum PCBs?
Common surface finishes for aluminum PCBs include HASL, ENIG, and OSP. The choice of surface finish depends on the specific requirements of the application, such as solderability, durability, and cost.
5. How long does it take to manufacture aluminum PCBs?
The lead time for manufacturing aluminum PCBs varies depending on the complexity of the design and the volume of the order. Typically, prototype orders can be completed within 1-2 weeks, while volume production may take 4-6 weeks.
Conclusion
Aluminum PCBs offer a superior solution for applications that demand efficient thermal management, reliability, and high performance. By partnering with an experienced aluminum PCB manufacturer, you can ensure that your projects benefit from expert design support, state-of-the-art manufacturing processes, and customized solutions tailored to your specific needs.
As a leading aluminum PCB manufacturer, we are committed to delivering the highest quality products and services to our clients. Contact us today to discuss your project requirements and learn how our aluminum PCB solutions can help you achieve your goals.
Leave a Reply