Introduction to Altium s2 295 and TDR
Altium s2 295 is a powerful tool for mastering Time Domain Reflectometry (TDR) in PCB design. TDR is a technique used to analyze the integrity of high-speed signals in PCBs by measuring the reflections of a test signal sent through the transmission line. With the increasing demand for faster and more complex PCBs, mastering TDR has become essential for designers to ensure the reliability and performance of their designs.
What is Altium s2 295?
Altium s2 295 is a comprehensive solution for PCB designers to simulate, analyze, and optimize high-speed designs using TDR. It includes a range of features and tools specifically designed to help designers master TDR techniques and achieve optimal signal integrity in their PCBs.
Benefits of using Altium s2 295 for TDR
- Accurate simulation of high-speed signals
- Identification of signal integrity issues early in the design process
- Optimization of PCB layout for better signal quality
- Reduction of design iterations and time-to-market
- Compliance with industry standards and guidelines
Understanding Time Domain Reflectometry (TDR)
Principles of TDR
TDR works by sending a high-frequency test signal through a transmission line and measuring the reflections caused by impedance discontinuities along the line. These reflections can be analyzed to determine the location and nature of the discontinuities, such as vias, connectors, or changes in trace width.
TDR waveforms and their interpretation
The TDR waveform represents the voltage of the test signal as a function of time. The shape of the waveform can provide valuable information about the impedance profile of the transmission line.
Waveform Shape | Interpretation |
---|---|
Step | Ideal transmission line with no discontinuities |
Positive peak | Impedance increase (e.g., via or connector) |
Negative peak | Impedance decrease (e.g., trace necking or splitting) |
Ringing | Resonance or reflections from multiple discontinuities |
Common signal integrity issues detected by TDR
- Impedance mismatch
- Reflection and ringing
- Crosstalk
- propagation delay
- Attenuation and loss
Setting up TDR simulations in Altium s2 295
Defining stackup and material properties
The first step in setting up a TDR simulation is to define the PCB stackup and material properties. This includes specifying the number of layers, dielectric constants, and thicknesses of the materials used in the PCB.
Creating and configuring TDR test signals
Next, you need to create and configure the TDR test signals. This involves setting the rise time, amplitude, and duration of the test pulse, as well as the reference impedance for the simulation.
Specifying termination and boundary conditions
Proper termination and boundary conditions are critical for accurate TDR simulations. You need to specify the source and load impedances, as well as any termination resistors or caps used in the design.
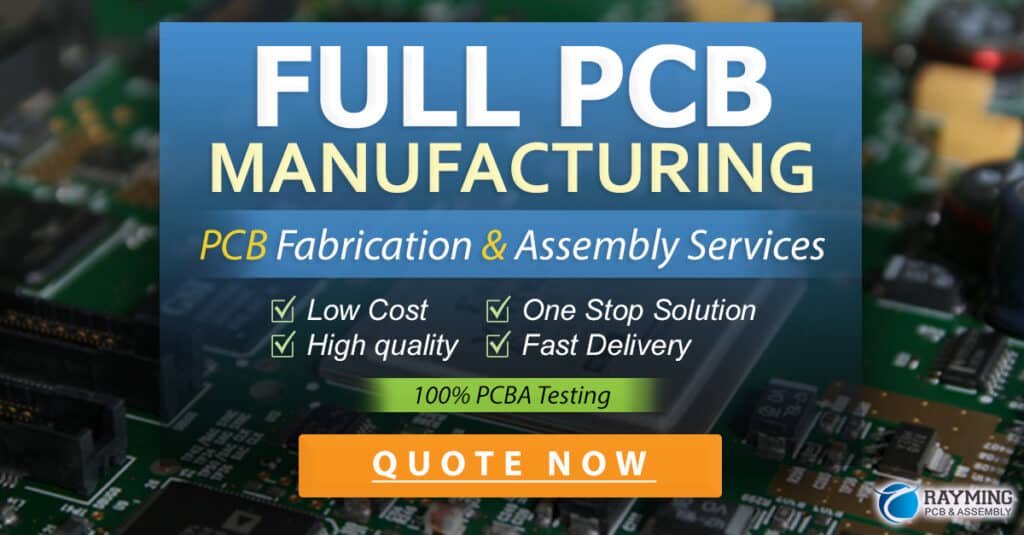
Analyzing TDR simulation results
Identifying impedance discontinuities
Once the TDR simulation is complete, you can analyze the results to identify impedance discontinuities along the transmission line. Look for peaks or dips in the TDR waveform that indicate changes in impedance.
Measuring reflection coefficients and propagation delay
The reflection coefficient is a measure of the amplitude of the reflected signal relative to the incident signal. It can be calculated from the TDR waveform using the following formula:
Γ = (Vr - V0) / (Vf - V0)
Where:
– Γ is the reflection coefficient
– Vr is the voltage of the reflected signal
– V0 is the initial voltage of the test signal
– Vf is the final voltage of the test signal
The propagation delay can be measured by the time difference between the incident and reflected signals.
Comparing simulation results with design rules and guidelines
It’s important to compare the TDR simulation results with the design rules and guidelines for your specific application. This includes checking for compliance with impedance tolerance, maximum reflection, and propagation delay requirements.
Optimizing PCB layout based on TDR results
Adjusting trace geometry and spacing
Based on the TDR simulation results, you may need to adjust the trace geometry and spacing to minimize impedance discontinuities. This can involve changing the trace width, thickness, or spacing, as well as adding or removing ground planes.
Inserting impedance matching structures
In some cases, it may be necessary to insert impedance matching structures, such as series or shunt resistors, to compensate for unavoidable discontinuities in the transmission line.
Validating the optimized design with TDR
After making the necessary adjustments to the PCB layout, it’s important to re-run the TDR simulation to validate the optimized design. This ensures that the changes have the desired effect on signal integrity and that the design meets all the required specifications.
Best practices for TDR-based PCB design
- Start with a well-defined stackup and material selection
- Use consistent trace geometry and spacing throughout the design
- Minimize the number of vias and layer transitions
- Provide adequate ground and power plane coverage
- Simulation early and often to catch issues before fabrication
- Validate the final design with physical TDR measurements
Frequently Asked Questions (FAQ)
1. What is the difference between TDR and TDT?
TDR (Time Domain Reflectometry) and TDT (Time Domain Transmission) are both techniques used to analyze the integrity of high-speed signals in PCBs. The main difference is that TDR measures the reflections of a test signal, while TDT measures the transmission of the signal through the PCB.
2. How does the rise time of the TDR test signal affect the simulation results?
The rise time of the TDR test signal determines the spatial resolution of the simulation. A faster rise time allows for the detection of smaller discontinuities, but it also requires a higher sampling rate and may be more sensitive to noise.
3. What is the significance of the reference impedance in TDR simulations?
The reference impedance is the characteristic impedance of the transmission line against which the TDR measurements are compared. It is typically set to the target impedance of the design, such as 50 ohms for most high-speed digital applications.
4. How do I interpret the TDR waveform if there are multiple reflections?
Multiple reflections in the TDR waveform can indicate the presence of multiple impedance discontinuities along the transmission line. To interpret the waveform, you need to analyze the timing and amplitude of each reflection and compare them with the expected locations and magnitudes of the discontinuities in the PCB layout.
5. What are some common causes of impedance mismatch in PCBs?
Common causes of impedance mismatch in PCBs include:
– Changes in trace width or thickness
– Layer transitions and vias
– Connectors and other components
– Improper termination or loading
– Coupling between adjacent traces
Conclusion
Mastering TDR is essential for designing high-speed PCBs with optimal signal integrity. Altium s2 295 provides a comprehensive solution for simulating, analyzing, and optimizing PCB layouts using TDR techniques. By understanding the principles of TDR, setting up accurate simulations, and interpreting the results, designers can identify and correct signal integrity issues early in the design process, reducing the risk of costly failures and improving the overall performance of their products.
Leave a Reply