Introduction to Grounded coplanar waveguide
A grounded coplanar waveguide (GCPW) is a type of transmission line used in high-frequency circuit design, particularly in printed circuit boards (PCBs) and integrated circuits (ICs). It is a variant of the coplanar waveguide (CPW) structure, which consists of a center conductor strip with ground planes on either side, all on the same plane. The key difference between a CPW and a GCPW is that the latter has an additional ground plane on the opposite side of the substrate, providing better field confinement and reduced radiation losses.
Advantages of Grounded Coplanar Waveguide
-
Low dispersion: GCPW exhibits low dispersion, which means that the signal propagation velocity remains relatively constant over a wide frequency range. This property is crucial for high-speed digital signals and broadband applications.
-
Reduced radiation losses: The presence of the additional ground plane in GCPW helps to confine the electromagnetic fields more effectively, reducing radiation losses compared to CPW.
-
Improved isolation: GCPW provides better isolation between adjacent signal lines due to the enhanced field confinement, which is essential for minimizing crosstalk in high-density circuits.
-
Compatibility with surface-mount components: The coplanar nature of GCPW allows for easy integration of surface-mount components, such as resistors, capacitors, and inductors, without the need for via holes.
Designing with Grounded Coplanar Waveguide
Characteristic Impedance
One of the most important parameters in GCPW design is the characteristic impedance (Z0). It is determined by the geometry of the transmission line, including the width of the center conductor (W), the gap between the center conductor and ground planes (G), the thickness of the substrate (H), and the dielectric constant of the substrate material (εr).
The characteristic impedance can be calculated using the following equation:
Z0 = (60 / √εeff) * ln[(4H + W) / W]
where:
– εeff is the effective dielectric constant, which depends on the substrate material and the geometry of the GCPW.
To achieve a specific characteristic impedance, such as 50 Ω or 75 Ω, designers must carefully choose the appropriate values for W, G, and H based on the available substrate material.
Substrate Material Selection
The choice of substrate material is crucial in GCPW design, as it affects the electrical properties of the transmission line, such as the characteristic impedance and the signal propagation velocity. Some common substrate materials used in high-frequency PCB design include:
-
FR-4: A low-cost, glass-reinforced epoxy laminate widely used in PCBs. However, its relatively high dielectric loss and variations in dielectric constant make it less suitable for high-frequency applications above a few gigahertz.
-
Rogers RO4000 series: A family of high-frequency laminate materials with low dielectric loss and stable dielectric constant over a wide frequency range. These materials are well-suited for applications up to millimeter-wave frequencies.
-
Alumina (Al2O3): A ceramic substrate material with excellent high-frequency properties, including low dielectric loss and high thermal conductivity. Alumina is often used in high-power and high-temperature applications.
Signal Integrity Considerations
When designing with GCPW, it is essential to consider signal integrity aspects to ensure reliable signal transmission. Some key factors to keep in mind include:
-
Discontinuities: Abrupt changes in the GCPW geometry, such as bends, transitions, and junctions, can introduce discontinuities that cause reflections and degrade signal quality. Designers should use smooth transitions and minimize discontinuities whenever possible.
-
Matching network design: To minimize reflections and ensure maximum power transfer, it is necessary to match the impedance of the GCPW to the source and load impedances. This can be achieved using matching networks, such as quarter-wave transformers or stub matching.
-
Frequency-dependent losses: As the operating frequency increases, losses in the GCPW also increase due to dielectric loss, conductor loss, and radiation loss. Designers must take these losses into account and choose appropriate materials and geometries to minimize their impact on signal integrity.
Simulating Grounded Coplanar Waveguide
To optimize the performance of GCPW in a design, it is essential to perform electromagnetic simulations using tools such as Altium Designer, Ansys HFSS, or CST Studio Suite. These simulations help designers to:
-
Validate the characteristic impedance and ensure that it matches the desired value across the operating frequency range.
-
Analyze the frequency-dependent behavior of the GCPW, including the insertion loss, return loss, and phase response.
-
Investigate the impact of discontinuities and optimize the geometry to minimize their effects on signal integrity.
-
Evaluate the radiation characteristics of the GCPW and ensure that the electromagnetic fields are well-confined to minimize interference with other components.
Example Simulation Setup
To set up a GCPW simulation in Altium Designer, follow these steps:
-
Create a new project and define the layer stack-up, including the substrate material, thickness, and dielectric constant.
-
Draw the GCPW geometry using the PCB layout tools, specifying the center conductor width (W), gap (G), and ground plane dimensions.
-
Define the ports at the input and output of the GCPW, specifying the port type (e.g., waveguide port) and the reference planes.
-
Set up the frequency sweep range and the desired output parameters, such as S-parameters, impedance, and field distributions.
-
Run the simulation and analyze the results to optimize the GCPW design.
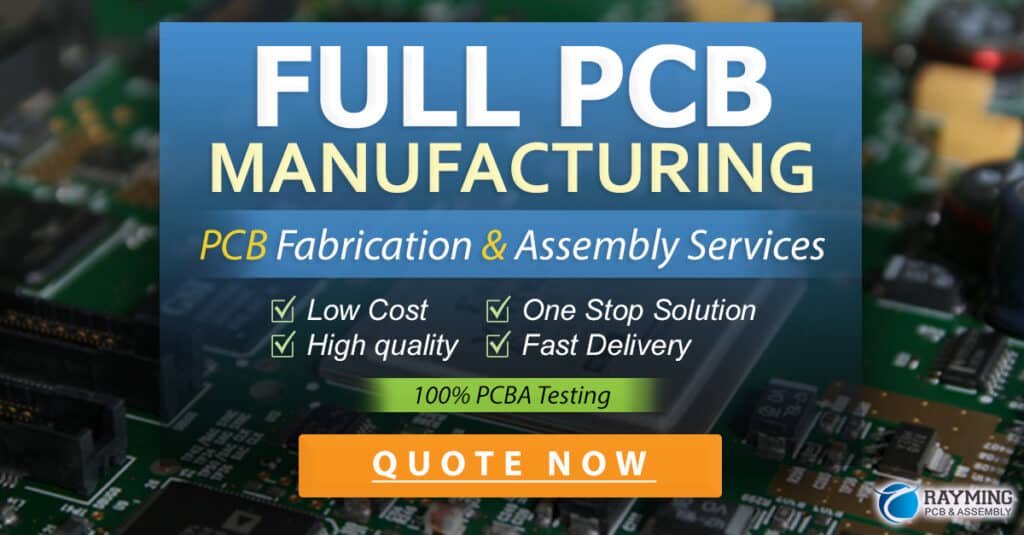
Grounded Coplanar Waveguide Applications
GCPW is widely used in various high-frequency applications, such as:
-
High-speed digital interconnects: GCPW is employed in high-speed digital systems, such as PCIe, USB, and HDMI, to provide low-loss, low-dispersion signal transmission between components.
-
RF and microwave circuits: In wireless communication systems, radar, and satellite applications, GCPW is used to implement filters, couplers, power dividers, and other passive components.
-
Millimeter-wave and terahertz devices: As the operating frequencies extend into the millimeter-wave and terahertz ranges, GCPW becomes an essential transmission line structure due to its low-loss and low-dispersion properties.
-
Monolithic microwave integrated circuits (MMICs): GCPW is commonly used in MMICs fabricated on semiconductor substrates, such as gallium arsenide (GaAs) and indium phosphide (InP), to interconnect active and passive components.
Frequently Asked Questions (FAQ)
- What is the difference between a coplanar waveguide (CPW) and a grounded coplanar waveguide (GCPW)?
-
A CPW consists of a center conductor strip with ground planes on either side, all on the same plane. A GCPW has an additional ground plane on the opposite side of the substrate, providing better field confinement and reduced radiation losses.
-
How does the characteristic impedance of a GCPW depend on its geometry?
-
The characteristic impedance of a GCPW is determined by the width of the center conductor (W), the gap between the center conductor and ground planes (G), the thickness of the substrate (H), and the dielectric constant of the substrate material (εr). It can be calculated using the equation:
Z0 = (60 / √εeff) * ln[(4H + W) / W]
-
What are some common substrate materials used for GCPW in high-frequency PCB design?
-
Common substrate materials for high-frequency PCB design include FR-4, Rogers RO4000 series, and alumina (Al2O3). The choice of substrate material depends on factors such as the operating frequency range, dielectric loss, and thermal properties.
-
Why is it important to perform electromagnetic simulations when designing with GCPW?
-
Electromagnetic simulations help designers to validate the characteristic impedance, analyze the frequency-dependent behavior, investigate the impact of discontinuities, and evaluate the radiation characteristics of the GCPW. These simulations are essential for optimizing the performance and ensuring the signal integrity of the design.
-
What are some typical applications of grounded coplanar waveguide?
- GCPW is widely used in high-speed digital interconnects, RF and microwave circuits, millimeter-wave and terahertz devices, and monolithic microwave integrated circuits (MMICs). Its low-loss, low-dispersion, and good field confinement properties make it suitable for a variety of high-frequency applications.
Conclusion
Grounded coplanar waveguide (GCPW) is a crucial transmission line structure for high-frequency circuit design, offering low dispersion, reduced radiation losses, and improved isolation compared to traditional coplanar waveguide (CPW). When designing with GCPW, it is essential to consider factors such as characteristic impedance, substrate material selection, and signal integrity aspects to ensure optimal performance.
Electromagnetic simulations play a vital role in GCPW design, allowing designers to validate the characteristic impedance, analyze the frequency-dependent behavior, and investigate the impact of discontinuities. By carefully optimizing the GCPW geometry and selecting appropriate substrate materials, designers can achieve reliable, high-performance signal transmission in various applications, including high-speed digital interconnects, RF and microwave circuits, and millimeter-wave devices.
As the demand for higher data rates and operating frequencies continues to grow, GCPW will remain an indispensable tool in the arsenal of high-frequency circuit designers, enabling the development of cutting-edge technologies in the fields of communication, sensing, and computing.
Leave a Reply