Understanding PCB Trace Length and Its Importance
Printed Circuit Boards (PCBs) are the backbone of modern electronics, connecting various components to ensure proper functionality. One crucial aspect of PCB design is the trace length, which refers to the physical length of the conductive paths that carry signals between components. Trace length plays a significant role in determining the overall performance and reliability of a PCB.
In this comprehensive article, we will delve into the intricacies of PCB trace length, discussing its importance, factors affecting it, and guidelines for optimal trace length design. Whether you are a seasoned PCB designer or a curious electronics enthusiast, understanding the concepts surrounding PCB trace length is essential for creating high-quality and efficient circuit boards.
The Role of Trace Length in PCB Design
Trace length is a critical parameter in PCB design because it directly impacts several aspects of the circuit’s performance, including:
-
Signal Integrity: Longer traces are more susceptible to signal degradation, noise, and crosstalk, which can lead to compromised signal quality and potential malfunctions.
-
Timing and Synchronization: Trace length variations can introduce timing delays and skew, affecting the synchronization of signals across the board.
-
Electromagnetic Interference (EMI): Longer traces act as antennas, potentially radiating or picking up unwanted electromagnetic interference, which can disrupt the circuit’s operation.
-
Power Integrity: Trace length also influences the voltage drop and current-carrying capacity of the traces, impacting the power delivery to components.
By carefully considering and optimizing trace lengths, PCB designers can mitigate these issues and ensure the proper functioning of the circuit.
Factors Affecting PCB Trace Length
Several factors influence the determination of appropriate trace lengths in PCB design. Understanding these factors is crucial for making informed decisions and striking the right balance between performance and manufacturability.
Signal Frequency and Rise Time
The frequency and rise time of the signals propagating through the traces are primary considerations when determining trace lengths. High-frequency signals and fast rise times require shorter traces to minimize signal distortion and maintain signal integrity. As a general rule of thumb, the higher the frequency or the faster the rise time, the shorter the traces should be.
Dielectric Constant and Impedance Matching
The dielectric constant of the PCB substrate material affects the propagation speed of signals along the traces. Materials with higher dielectric constants result in slower signal propagation, which can impact trace length calculations. Additionally, impedance matching is crucial for ensuring proper signal transmission and minimizing reflections. Trace lengths must be carefully designed to maintain the desired characteristic impedance throughout the signal path.
Component Placement and Board Size
The placement of components on the PCB directly influences trace lengths. Optimal component placement involves minimizing the distance between interconnected components, reducing overall trace lengths, and improving signal integrity. However, this must be balanced with other design considerations, such as thermal management, mechanical constraints, and manufacturability.
The size of the PCB also plays a role in determining trace lengths. Larger boards naturally require longer traces to connect components, while smaller boards allow for more compact routing and shorter traces. Designers must find the right balance between board size and trace length optimization to meet the specific requirements of the application.
Manufacturing Constraints and Design Rules
PCB manufacturing capabilities and design rules imposed by the fabrication process can limit the minimum and maximum trace lengths achievable. Factors such as the minimum trace width, spacing, and via size dictate the routing density and, consequently, the trace lengths. Designers must adhere to these constraints to ensure the manufacturability and reliability of the PCB.
Guidelines for Optimal Trace Length Design
To achieve optimal trace length design in PCBs, designers can follow these guidelines:
-
Keep traces as short as possible: Minimize the distance between interconnected components to reduce trace lengths and improve signal integrity.
-
Match trace lengths for critical signals: Ensure that traces carrying critical signals, such as clock or data lines, have matched lengths to maintain proper timing and synchronization.
-
Use serpentine routing for length matching: Employ serpentine routing techniques to add controlled amounts of trace length for length matching purposes.
-
Consider the impact of vias: Vias introduce additional trace length and can affect signal integrity. Minimize the number of vias and strategically place them to optimize trace lengths.
-
Utilize PCB design software: Leverage the capabilities of modern PCB design software, which often include tools for trace length calculation, optimization, and length matching.
-
Perform signal integrity simulations: Conduct signal integrity simulations to analyze the impact of trace lengths on signal quality and make necessary adjustments.
-
Adhere to manufacturing constraints: Ensure that trace lengths comply with the manufacturing capabilities and design rules specified by the PCB fabricator.
By following these guidelines, designers can effectively manage trace lengths and optimize the performance and reliability of their PCB designs.
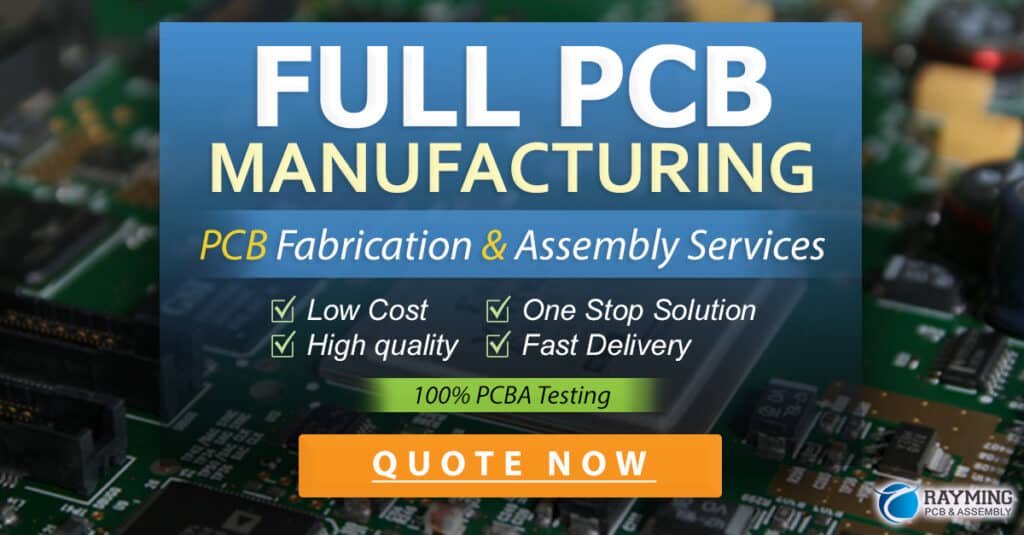
PCB Trace Length Calculation and Tools
Accurately calculating trace lengths is essential for ensuring proper signal propagation and timing. Several methods and tools are available to assist designers in determining the appropriate trace lengths for their PCB designs.
Manual Calculation Methods
One approach to calculating trace lengths is through manual methods using basic geometry and the PCB layout dimensions. Designers can measure the physical distance between components and calculate the trace length based on the routing path. However, this method can be time-consuming and prone to errors, especially for complex designs with numerous traces.
PCB Design Software Tools
Modern PCB design software packages offer built-in tools and features for trace length calculation and optimization. These tools automate the process of measuring trace lengths, considering factors such as via lengths and layer transitions. They also provide capabilities for length matching, allowing designers to easily adjust trace lengths to achieve matched delays.
Some popular PCB design software tools with trace length calculation and optimization features include:
- Altium Designer
- Cadence Allegro
- Mentor Graphics PADS
- KiCad
- Eagle PCB
These tools significantly streamline the trace length calculation process and enable designers to make informed decisions based on accurate measurements and simulations.
Online Trace Length Calculators
In addition to PCB design software, there are online trace length calculators available that provide quick and easy estimations of trace lengths based on various parameters. These calculators typically require inputs such as the PCB material, trace width, copper thickness, and desired characteristic impedance. While not as comprehensive as dedicated PCB design tools, online calculators can be useful for rough estimations and preliminary design work.
Common Pitfalls and Misconceptions
When dealing with PCB trace lengths, designers should be aware of common pitfalls and misconceptions that can lead to suboptimal designs:
-
Neglecting the impact of vias: Vias introduce additional trace length and can affect signal integrity if not properly accounted for. Designers should consider via lengths when calculating overall trace lengths.
-
Overemphasis on short traces: While shorter traces are generally preferred, excessively short traces can lead to manufacturing challenges and increased costs. Designers should strike a balance between trace length optimization and manufacturability.
-
Ignoring the importance of length matching: Mismatched trace lengths can cause timing issues and signal integrity problems. Designers should prioritize length matching for critical signals to ensure proper synchronization.
-
Overlooking the impact of PCB materials: The choice of PCB substrate material affects signal propagation speed and, consequently, trace length calculations. Designers should consider the dielectric constant of the material when determining appropriate trace lengths.
By being aware of these pitfalls and misconceptions, designers can make informed decisions and avoid common mistakes in PCB trace length design.
Frequently Asked Questions (FAQ)
-
Q: What is considered a long trace in PCB design?
A: The definition of a long trace depends on various factors, such as the signal frequency, rise time, and PCB material. As a general guideline, traces longer than a quarter wavelength of the signal’s highest frequency component can be considered long traces. -
Q: How does trace length affect signal integrity?
A: Longer traces are more susceptible to signal degradation, noise, and crosstalk. As the trace length increases, the signal becomes more attenuated, and the risk of signal reflections and distortions increases. Minimizing trace lengths helps maintain signal integrity. -
Q: What is the importance of length matching in PCB design?
A: Length matching ensures that critical signals, such as clock or data lines, have equal trace lengths to maintain proper timing and synchronization. Mismatched trace lengths can introduce timing skew and lead to signal integrity issues, potentially causing malfunctions or performance degradation. -
Q: How can I optimize trace lengths in my PCB design?
A: To optimize trace lengths, consider the following strategies:- Place interconnected components as close as possible to minimize trace lengths.
- Use serpentine routing techniques for length matching.
- Minimize the number of vias and strategically place them.
- Utilize PCB design software tools for trace length calculation and optimization.
- Perform signal integrity simulations to analyze the impact of trace lengths.
-
Q: Are there any industry standards or guidelines for PCB trace lengths?
A: While there are no universal industry standards for PCB trace lengths, various organizations and manufacturers provide guidelines and recommendations based on specific applications and technologies. It is essential to consult the relevant standards and guidelines for your specific industry or application, such as ipc standards for pcb design and manufacturing.
Conclusion
PCB trace length is a critical aspect of PCB design that significantly impacts the overall performance and reliability of electronic circuits. By understanding the factors affecting trace lengths, following best practices for optimal trace length design, and utilizing the right tools and techniques, designers can create high-quality PCBs that meet the desired specifications and performance requirements.
Designers should keep in mind the importance of signal integrity, timing, and manufacturability when determining appropriate trace lengths. Leveraging the capabilities of modern PCB design software and conducting thorough simulations can greatly assist in optimizing trace lengths and ensuring the success of the final product.
As technology advances and the demand for high-speed and high-frequency electronics grows, the significance of PCB trace length will only continue to increase. By staying informed about the latest developments and best practices in trace length design, PCB designers can stay ahead of the curve and deliver cutting-edge solutions that meet the evolving needs of the electronics industry.
Leave a Reply