What are PCB tooling holes?
PCB tooling holes, also known as tooling vias, registration holes, or alignment holes, are small holes drilled into a printed circuit board (PCB) that are used for alignment and positioning during the manufacturing process. These holes are not electrically connected to the circuit and do not have any functional purpose in the final product. Instead, they serve as reference points for the various machines and tools used in PCB fabrication.
Types of PCB tooling holes
There are two main types of PCB tooling holes:
-
Tooling holes for alignment: These holes are used to align the PCB with the various machines and tools used in the manufacturing process, such as drill machines, solder paste printers, and pick-and-place machines. They ensure that the PCB is correctly positioned and oriented during each step of the fabrication process.
-
Tooling holes for panelization: These holes are used to hold the PCB in place when it is part of a larger panel. PCBs are often manufactured in panels, which are larger boards containing multiple individual PCBs. The tooling holes are used to secure the panel to the machines and to ensure proper alignment during the fabrication process.
Where are PCB tooling holes located?
PCB tooling holes are typically located outside of the main circuit area, usually in the corners or along the edges of the board. The exact location and number of tooling holes depend on the size and shape of the PCB, as well as the specific requirements of the manufacturing process.
Standard placement of PCB tooling holes
In most cases, PCB tooling holes are placed in a standardized pattern, such as:
- Two holes: One hole in each of two opposite corners of the board.
- Three holes: One hole in each of three corners of the board, forming a right-angled triangle.
- Four holes: One hole in each corner of the board.
The distance between the tooling holes and the edge of the board is typically standardized as well, usually ranging from 5mm to 10mm.
Custom placement of PCB tooling holes
In some cases, the placement of PCB tooling holes may need to be customized to accommodate specific manufacturing requirements or board designs. For example:
- Irregular board shapes: If the PCB has an irregular or non-rectangular shape, the tooling holes may need to be placed in different locations to ensure proper alignment.
- Large or complex boards: For larger or more complex PCBs, additional tooling holes may be necessary to ensure adequate support and alignment during the manufacturing process.
- Panelization requirements: The placement of tooling holes may need to be adjusted to accommodate the panelization layout and to ensure that the individual PCBs can be easily separated from the panel after fabrication.
Designing PCBs with tooling holes
When designing a PCB, it is important to consider the placement and size of the tooling holes to ensure compatibility with the manufacturing process. Most PCB design software includes tools for adding and positioning tooling holes automatically.
Standard tooling hole sizes
The size of PCB tooling holes is typically standardized, with the most common sizes being:
- 2.0mm: This is the most common size for tooling holes and is suitable for most standard PCB designs.
- 2.4mm: This size is often used for larger or thicker PCBs that require more support during the manufacturing process.
- 3.0mm: This size is less common and is typically used for very large or heavy boards.
Tooling Hole Size | Typical Use |
---|---|
2.0mm | Standard PCBs |
2.4mm | Larger or thicker PCBs |
3.0mm | Very large or heavy boards |
Adding tooling holes to your PCB design
To add tooling holes to your PCB design, follow these general steps:
- Determine the appropriate size and placement of the tooling holes based on your PCB’s size, shape, and manufacturing requirements.
- In your PCB design software, locate the tool for adding tooling holes. This is usually found in the mechanical or manufacturing section of the software.
- Place the tooling holes in the desired locations on your PCB design. Make sure to maintain the proper distance from the board edges and other components.
- Specify the size of the tooling holes according to the standardized sizes or your specific manufacturing requirements.
- Review your design to ensure that the tooling holes do not interfere with any other components or features of the PCB.
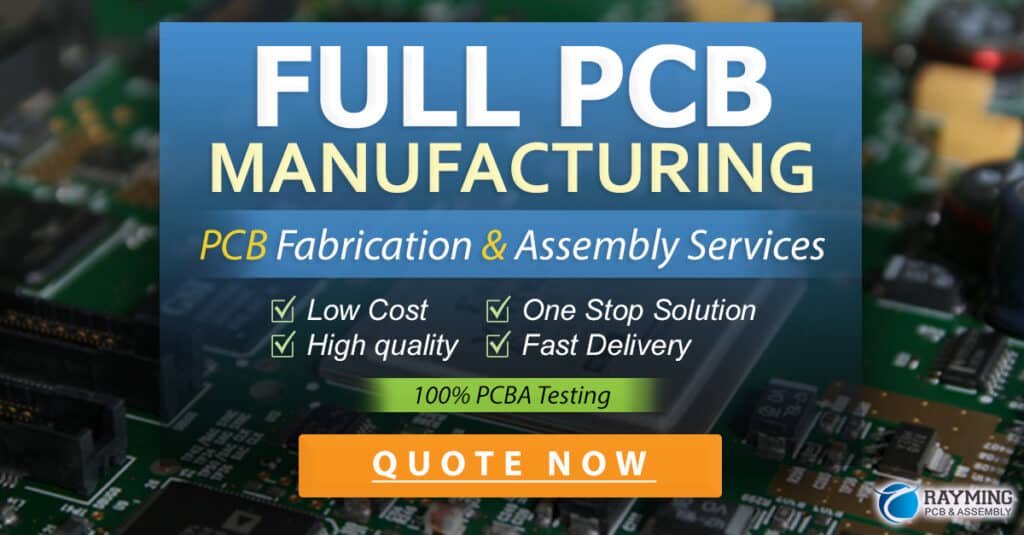
Importance of PCB tooling holes in manufacturing
PCB tooling holes play a crucial role in the manufacturing process, ensuring accurate alignment, positioning, and support for the board throughout the various stages of fabrication.
Alignment and positioning
Tooling holes serve as reference points for the machines and tools used in PCB manufacturing, guaranteeing that the board is correctly aligned and positioned during each step of the process. This is particularly important for the following stages:
- Drilling: Tooling holes ensure that the drill machine accurately positions the holes for vias and component leads on the PCB.
- Solder paste printing: The solder paste printer uses the tooling holes to align the stencil and apply the solder paste precisely on the pads.
- Component placement: Pick-and-place machines use the tooling holes to position the PCB correctly, ensuring that components are placed accurately on their designated pads.
Support during fabrication
In addition to alignment and positioning, tooling holes also provide support for the PCB during the manufacturing process. This is especially important when the board is part of a larger panel, as the tooling holes help to secure the panel and prevent it from warping or shifting during handling and processing.
Quality control and consistency
By ensuring accurate alignment and support throughout the manufacturing process, PCB tooling holes contribute to the overall quality and consistency of the final product. Properly placed tooling holes help to minimize errors, reduce waste, and improve the reliability of the manufactured PCBs.
FAQ
-
What happens to PCB tooling holes after the manufacturing process?
After the PCB manufacturing process is complete, the tooling holes serve no further purpose. They remain on the board but do not affect the functionality or performance of the circuit. -
Can I use tooling holes for other purposes, such as mounting the PCB?
While it is possible to use tooling holes for mounting purposes, it is generally not recommended. Tooling holes are not designed to provide mechanical support for the PCB, and using them for mounting can potentially weaken the board or cause damage. It is better to include dedicated mounting holes in your PCB design. -
Are tooling holes necessary for all PCB designs?
In most cases, yes. Tooling holes are essential for ensuring accurate alignment and support during the PCB manufacturing process. However, for very small or simple PCBs, tooling holes may not be necessary if the board can be adequately supported and aligned without them. -
Can I specify custom tooling hole sizes or placements?
Yes, it is possible to specify custom tooling hole sizes and placements based on your specific PCB design and manufacturing requirements. However, it is important to consult with your PCB manufacturer to ensure that your custom specifications are feasible and compatible with their processes. -
Do tooling holes affect the cost of PCB manufacturing?
In general, the presence of tooling holes does not significantly impact the cost of PCB manufacturing. The cost is primarily determined by factors such as the size, complexity, and quantity of the boards being produced. However, if you require custom tooling hole specifications that deviate from standard practices, there may be additional costs associated with accommodating those requirements.
Conclusion
PCB tooling holes are a small but essential component of the PCB manufacturing process. By providing accurate alignment, positioning, and support for the board throughout the fabrication stages, tooling holes contribute to the quality, consistency, and reliability of the final product. When designing a PCB, it is important to consider the placement, size, and quantity of tooling holes to ensure compatibility with the manufacturing process and to optimize the performance of the finished board.
As PCB technology continues to advance and evolve, the role of tooling holes remains crucial in ensuring the successful fabrication of high-quality printed circuit boards. By understanding the purpose, placement, and design considerations for PCB tooling holes, engineers and manufacturers can work together to create reliable, efficient, and cost-effective electronic products.
Leave a Reply