Introduction to ORAN and PCB Design
Open Radio Access Networks (ORAN) are revolutionizing the way wireless networks are built and operated. ORAN is an initiative that aims to create open, interoperable, and standardized interfaces for radio access networks (RAN). This approach enables network operators to mix and match components from different vendors, fostering innovation and reducing costs. As a result, PCB designers play a crucial role in the development of ORAN-compliant hardware.
In this comprehensive guide, we will explore the key aspects of ORAN and provide valuable insights for PCB designers working on ORAN projects. We will cover the architecture of ORAN, the role of PCB design in ORAN, design considerations, best practices, and future trends in the industry.
ORAN Architecture and Components
ORAN Architecture Overview
ORAN architecture is based on a disaggregated approach, where the traditional RAN is split into several functional blocks. These blocks are connected through open and standardized interfaces, allowing for interoperability and flexibility. The main components of ORAN architecture include:
- Radio Unit (RU)
- Distributed Unit (DU)
- Centralized Unit (CU)
- RAN Intelligent Controller (RIC)
Radio Unit (RU)
The Radio Unit is responsible for transmitting and receiving radio signals. It consists of the antenna, RF front-end, and digital front-end. The RU is connected to the DU through the fronthaul interface, which is typically based on the eCPRI (Enhanced Common Public Radio Interface) protocol.
Distributed Unit (DU)
The Distributed Unit performs baseband processing functions, such as modulation, demodulation, and channel coding. It is connected to the RU through the fronthaul interface and to the CU through the midhaul interface. The DU can be implemented as a standalone unit or integrated with the RU.
Centralized Unit (CU)
The Centralized Unit handles higher-layer functions, such as radio resource management, mobility management, and user plane processing. It is connected to the DU through the midhaul interface and to the core network through the backhaul interface. The CU can be implemented as a virtualized function running on commercial off-the-shelf (COTS) hardware.
RAN Intelligent Controller (RIC)
The RAN Intelligent Controller is a new component introduced in ORAN architecture. It enables real-time and near-real-time control and optimization of the RAN. The RIC consists of two main components:
- Near-Real-Time RIC (nRT-RIC): Responsible for near-real-time control and optimization, with a control loop of 10-100 ms.
- Non-Real-Time RIC (NRT-RIC): Responsible for non-real-time control and optimization, with a control loop of seconds to minutes.
Role of PCB Design in ORAN
PCB design plays a critical role in the development of ORAN-compliant hardware. PCB designers are responsible for creating the physical layout of the electronic components and ensuring that the design meets the performance, reliability, and cost requirements of ORAN.
Key Considerations for ORAN PCB Design
When designing PCBs for ORAN, several key considerations must be taken into account:
- High-speed design: ORAN interfaces, such as eCPRI and midhaul, operate at high data rates, requiring careful attention to signal integrity and power integrity.
- Thermal management: ORAN hardware, particularly the RU and DU, may generate significant heat, necessitating efficient thermal management solutions.
- Electromagnetic compatibility (EMC): ORAN hardware must meet strict EMC requirements to ensure proper operation and avoid interference with other devices.
- Mechanical design: ORAN hardware may be deployed in harsh environments, requiring robust mechanical design and protection against environmental factors.
- Cost optimization: ORAN aims to reduce the cost of RAN deployment, making cost optimization a critical consideration in PCB design.
Best Practices for ORAN PCB Design
To ensure successful ORAN PCB design, designers should follow these best practices:
- Adhere to ORAN specifications and guidelines: Follow the relevant ORAN specifications and guidelines for the specific component being designed.
- Collaborate with other stakeholders: Work closely with system architects, software developers, and mechanical engineers to ensure a holistic approach to design.
- Use simulation and modeling tools: Employ simulation and modeling tools to analyze signal integrity, power integrity, and thermal performance.
- Implement robust power distribution: Design a robust power distribution network to ensure stable and clean power supply to all components.
- Optimize layout for manufacturability: Consider manufacturing constraints and optimize the layout for ease of fabrication and assembly.
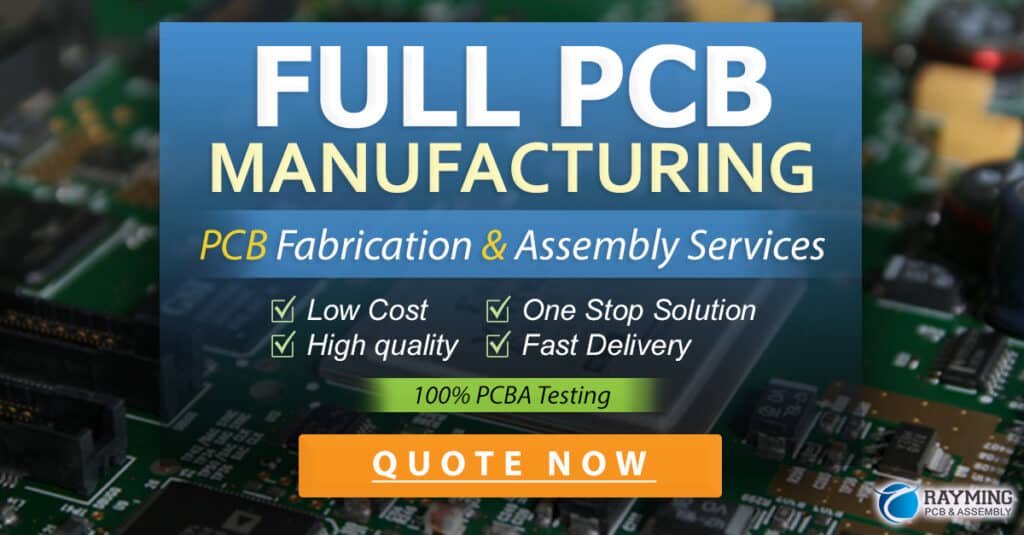
ORAN PCB Design Challenges and Solutions
Designing PCBs for ORAN presents several challenges that must be addressed to ensure successful implementation. Some of the key challenges and their potential solutions are:
Signal Integrity
Challenge: High-speed interfaces in ORAN, such as eCPRI and midhaul, require careful attention to signal integrity to ensure reliable data transmission.
Solutions:
– Use controlled impedance traces and proper termination techniques.
– Implement differential signaling for high-speed interfaces.
– Minimize crosstalk through proper trace spacing and shielding.
Power Integrity
Challenge: ORAN hardware requires stable and clean power supply to ensure proper operation and prevent noise-related issues.
Solutions:
– Design a robust power distribution network with adequate decoupling capacitors.
– Use power planes and proper grounding techniques to minimize impedance and noise.
– Implement power sequencing and monitoring to ensure proper power-up and power-down.
Thermal Management
Challenge: ORAN hardware, particularly the RU and DU, may generate significant heat, requiring efficient thermal management solutions.
Solutions:
– Use thermal simulation tools to analyze heat distribution and identify hot spots.
– Implement heatsinks, cooling fans, or other thermal management solutions as needed.
– Consider the use of thermally conductive materials and thermal vias in the PCB design.
Electromagnetic Compatibility (EMC)
Challenge: ORAN hardware must meet strict EMC requirements to ensure proper operation and avoid interference with other devices.
Solutions:
– Follow EMC design guidelines, such as proper grounding, shielding, and filtering.
– Use EMI simulation tools to analyze and optimize the design for EMC compliance.
– Conduct EMC testing to validate the design and ensure compliance with relevant standards.
Future Trends in ORAN PCB Design
As ORAN continues to evolve and gain traction in the industry, several trends are expected to shape the future of ORAN PCB design:
- Increased adoption of advanced packaging technologies, such as system-in-package (SiP) and multi-chip modules (MCM), to enable higher integration and miniaturization.
- Growing use of high-frequency materials, such as low-loss laminates and high-performance substrates, to support higher data rates and bandwidth.
- Incorporation of artificial intelligence (AI) and machine learning (ML) techniques in PCB design automation tools to optimize layouts and improve design efficiency.
- Emphasis on sustainable and eco-friendly PCB design practices, such as the use of halogen-free materials and the implementation of design for recyclability (DfR) principles.
Frequently Asked Questions (FAQ)
- What is ORAN, and how does it differ from traditional RAN architecture?
-
ORAN is an initiative that aims to create open, interoperable, and standardized interfaces for radio access networks. It differs from traditional RAN architecture by adopting a disaggregated approach, where the RAN is split into several functional blocks connected through open interfaces.
-
What are the main components of ORAN architecture?
-
The main components of ORAN architecture include the Radio Unit (RU), Distributed Unit (DU), Centralized Unit (CU), and RAN Intelligent Controller (RIC).
-
What are the key considerations for ORAN PCB design?
-
Key considerations for ORAN PCB design include high-speed design, thermal management, electromagnetic compatibility (EMC), mechanical design, and cost optimization.
-
What are some best practices for ORAN PCB design?
-
Best practices for ORAN PCB design include adhering to ORAN specifications and guidelines, collaborating with other stakeholders, using simulation and modeling tools, implementing robust power distribution, and optimizing layout for manufacturability.
-
What are some future trends in ORAN PCB design?
- Future trends in ORAN PCB design include increased adoption of advanced packaging technologies, growing use of high-frequency materials, incorporation of AI and ML techniques in design automation tools, and emphasis on sustainable and eco-friendly design practices.
Conclusion
ORAN is transforming the way radio access networks are designed and deployed, offering a more open, flexible, and cost-effective approach. PCB designers play a crucial role in the development of ORAN-compliant hardware, and understanding the key considerations, best practices, and challenges involved is essential for successful ORAN PCB design.
By following the guidelines and recommendations outlined in this comprehensive guide, PCB designers can create robust, high-performance, and cost-effective ORAN hardware that meets the demands of the rapidly evolving wireless industry. As ORAN continues to gain momentum, staying up-to-date with the latest trends and technologies will be crucial for PCB designers to remain competitive and contribute to the advancement of open radio access networks.
Component | Function |
---|---|
Radio Unit (RU) | Transmits and receives radio signals, consists of antenna, RF front-end, and digital front-end |
Distributed Unit (DU) | Performs baseband processing functions, such as modulation, demodulation, and channel coding |
Centralized Unit (CU) | Handles higher-layer functions, such as radio resource management, mobility management, and user plane processing |
RAN Intelligent Controller (RIC) | Enables real-time and near-real-time control and optimization of the RAN, consists of Near-Real-Time RIC (nRT-RIC) and Non-Real-Time RIC (NRT-RIC) |
Table 1: Main components of ORAN architecture and their functions.
Consideration | Description |
---|---|
High-speed design | Careful attention to signal integrity and power integrity for high data rate interfaces |
Thermal management | Efficient thermal management solutions for heat-generating components like RU and DU |
Electromagnetic compatibility (EMC) | Meeting strict EMC requirements to ensure proper operation and avoid interference |
Mechanical design | Robust mechanical design and protection against environmental factors for harsh deployment environments |
Cost optimization | Optimizing design for cost reduction, a critical consideration in ORAN deployment |
Table 2: Key considerations for ORAN PCB design.
Leave a Reply