Introduction to Product Lifecycle Management for PCBs
Product lifecycle management (PLM) is a holistic approach to managing the entire lifecycle of a product from inception through design, manufacturing, service, and disposal. PLM integrates people, data, processes and business systems to provide a product information backbone for companies and their extended enterprise.
In the context of printed circuit board (PCB) design, PLM encompasses the management of the PCB throughout its lifecycle, from initial concept and design, through prototyping, testing, manufacturing, and end-of-life. Effective PLM for PCBs requires close collaboration between various teams, including design, engineering, manufacturing, and supply chain.
The benefits of implementing PLM for PCB design include:
- Reduced time-to-market
- Improved product quality and reliability
- Lower development and manufacturing costs
- Enhanced collaboration and communication
- Better management of product data and intellectual property
Traditional vs Agile PLM Methodologies
Traditionally, PLM for PCBs followed a linear, waterfall-style approach where each phase of the product lifecycle was completed sequentially. However, this approach often led to long development cycles, inflexibility to changes, and a lack of collaboration between teams.
In recent years, there has been a shift towards agile PLM methodologies for PCB design. Agile PLM is based on the principles of agile software development, which emphasize iterative and incremental development, frequent delivery of working products, close collaboration between teams, and responsiveness to change.
The key differences between traditional and agile PLM are summarized in the table below:
Aspect | Traditional PLM | Agile PLM |
---|---|---|
Approach | Linear, waterfall | Iterative, incremental |
Development cycle | Long | Short |
Flexibility to changes | Low | High |
Team collaboration | Limited | Extensive |
Delivery frequency | Low | High |
Agile PLM enables PCB design teams to break down the product development process into smaller, manageable chunks, and deliver working prototypes and designs more frequently. This approach allows for faster feedback loops, early detection and resolution of issues, and greater flexibility to accommodate changes in requirements or market conditions.
Implementing Agile PLM for PCB Design
1. Establish Cross-Functional Teams
One of the core principles of agile PLM is close collaboration between cross-functional teams. For PCB design, this means bringing together designers, engineers, manufacturers, and other stakeholders to work together throughout the product lifecycle.
Cross-functional teams should be co-located whenever possible to facilitate face-to-face communication and collaboration. When physical co-location is not feasible, teams can use virtual collaboration tools such as video conferencing, instant messaging, and shared workspaces.
2. Define Product Requirements and Backlogs
In agile PLM, product requirements are captured in the form of user stories or features that describe the desired functionality from an end-user perspective. These requirements are prioritized and maintained in a product backlog, which serves as a centralized repository for all product-related information.
The product backlog is regularly groomed and updated based on feedback from stakeholders and changes in market conditions. The most important and valuable features are prioritized for development in each iteration or sprint.
3. Implement Iterative Development
Agile PLM relies on iterative and incremental development, where the product is developed in short cycles called sprints. Each sprint typically lasts 2-4 weeks and focuses on delivering a set of working features or prototypes.
For PCB design, this means breaking down the design process into smaller, manageable tasks that can be completed within a sprint. The team collaborates closely to design, prototype, test, and validate each feature before moving on to the next one.
At the end of each sprint, the team demonstrates the working features to stakeholders and gathers feedback. This feedback is then incorporated into the next sprint, allowing for continuous improvement and refinement of the product.
4. Use Collaborative Design Tools
Agile PLM requires close collaboration between PCB designers, engineers, and manufacturers. To facilitate this collaboration, it is essential to use design tools that enable real-time sharing, version control, and co-design.
Some examples of collaborative pcb design tools include:
- Cloud-based PCB design software
- Version control systems (e.g., Git, SVN)
- Design data management systems
- Real-time collaboration and co-design platforms
These tools allow team members to work together seamlessly, regardless of their location, and ensure that everyone has access to the latest design data and revisions.
5. Implement Continuous Integration and Delivery
Continuous integration (CI) and continuous delivery (CD) are key practices in agile PLM that enable frequent and reliable releases of PCB designs.
CI involves automatically building, testing, and validating PCB designs whenever changes are made to the codebase. This helps catch errors and integration issues early in the development cycle, reducing the risk of costly rework later on.
CD takes this a step further by automating the release and deployment process, allowing PCB designs to be delivered to manufacturing or customers as soon as they are ready.
Implementing CI/CD for PCB design requires the use of automated build, test, and deployment tools, as well as a robust version control system to manage design revisions.
6. Foster a Culture of Continuous Improvement
Agile PLM is not just a set of practices and tools, but also a mindset and culture of continuous improvement. PCB design teams should embrace a culture of experimentation, learning, and adaptation, and continuously seek ways to improve their processes and products.
This can be achieved through regular retrospectives, where the team reflects on what worked well, what didn’t, and what can be improved in the next iteration. The insights gained from these retrospectives should be used to refine the team’s processes, tools, and practices.
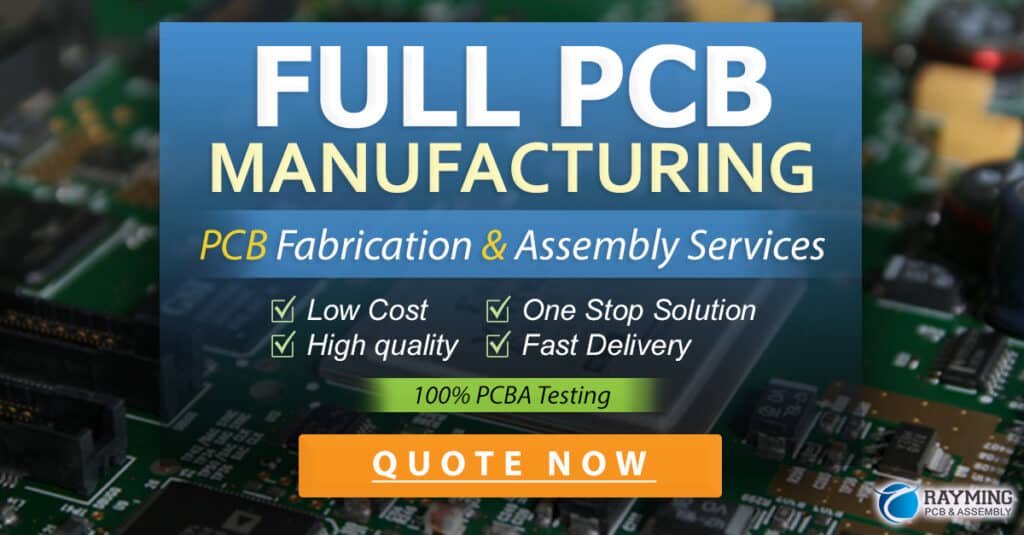
Best Practices for Agile PLM in PCB Design
To ensure the success of agile PLM in PCB design, consider the following best practices:
-
Start small and scale gradually: Agile PLM is a significant shift from traditional methods, and trying to implement it all at once can be overwhelming. Start with a small pilot project and gradually scale up as the team becomes more comfortable with the new approach.
-
Communicate frequently and transparently: Agile PLM relies on open and frequent communication between team members and stakeholders. Encourage regular stand-up meetings, demos, and retrospectives to keep everyone informed and aligned.
-
Embrace change and adaptability: Agile PLM is designed to be flexible and responsive to change. Encourage the team to embrace change and be open to adapting their plans and processes as needed.
-
Focus on delivering value: The ultimate goal of agile PLM is to deliver value to customers and stakeholders. Prioritize features and requirements based on their value and regularly seek feedback to ensure that the product meets the needs of the end-users.
-
Continuously improve and automate processes: Look for opportunities to streamline and automate processes, such as design validation, testing, and deployment. Use metrics and data to identify areas for improvement and track progress over time.
FAQ
1. What are the benefits of agile PLM for PCB design?
Agile PLM offers several benefits for PCB design, including faster time-to-market, improved product quality, lower development costs, enhanced collaboration, and better management of product data.
2. How does agile PLM differ from traditional PLM?
Agile PLM is based on iterative and incremental development, with short development cycles and frequent delivery of working products. Traditional PLM follows a linear, waterfall approach with longer development cycles and limited flexibility to changes.
3. What tools are used in agile PLM for PCB design?
Agile PLM for PCB design relies on collaborative design tools such as cloud-based PCB design software, version control systems, design data management systems, and real-time collaboration platforms.
4. How can I implement agile PLM in my PCB design team?
To implement agile PLM, start by establishing cross-functional teams, defining product requirements and backlogs, implementing iterative development, using collaborative design tools, implementing CI/CD, and fostering a culture of continuous improvement. Start small and scale gradually, communicating frequently and transparently throughout the process.
5. What are some best practices for successful agile PLM in PCB design?
Best practices for agile PLM in PCB design include starting small and scaling gradually, communicating frequently and transparently, embracing change and adaptability, focusing on delivering value, and continuously improving and automating processes.
Conclusion
Agile PLM is a powerful approach for managing the complexity and challenges of PCB design in today’s fast-paced and dynamic market. By embracing iterative development, collaboration, and continuous improvement, PCB design teams can deliver high-quality products faster and more efficiently.
Implementing agile PLM requires a significant shift in mindset and culture, as well as the adoption of new tools and practices. However, the benefits of agile PLM far outweigh the challenges, and more and more PCB design teams are making the transition to this approach.
By following the best practices and principles outlined in this article, PCB design teams can successfully implement agile PLM and reap the benefits of faster time-to-market, improved product quality, and enhanced collaboration and innovation.
Leave a Reply