What is EMI?
EMI is the unintentional generation of electromagnetic energy that can interfere with the operation of electronic devices. This interference can come from a variety of sources, including:
- External sources such as radio and television broadcasts, mobile phones, and other electronic devices
- Internal sources such as the switching of digital circuits, the operation of power supplies, and the movement of current through conductors
EMI can cause a range of problems in electronic devices, including:
- Signal integrity issues, such as distortion, attenuation, and crosstalk
- Reduced performance, such as slower data transmission speeds or reduced battery life
- Complete failure of the device, such as crashes or shutdowns
Why Address EMI Early in PCB Design?
Addressing EMI issues early in the PCB design stage is critical for several reasons:
-
Cost Savings: Identifying and fixing EMI issues early in the design process can save significant costs compared to fixing issues later in the development cycle or after the product has been released to market.
-
Improved Performance: By minimizing EMI, you can improve the overall performance of your electronic device, including signal integrity, data transmission speeds, and battery life.
-
Regulatory Compliance: Many industries have strict regulations regarding EMI emissions, and failure to comply can result in fines, product recalls, or even legal action.
-
Faster Time-to-Market: By addressing EMI issues early in the design process, you can avoid delays caused by redesigns or additional testing, allowing you to bring your product to market faster.
Strategies for Minimizing EMI in PCB Design
There are several strategies that you can use to minimize EMI in your PCB designs:
1. Proper Grounding
Proper grounding is essential for minimizing EMI in PCB design. A good grounding strategy should include:
- Using a solid ground plane on one or more layers of the PCB
- Connecting all ground pins of components to the ground plane using short, low-inductance paths
- Avoiding ground loops by ensuring that there is only one path for ground current to flow
2. Shielding
Shielding is another effective strategy for minimizing EMI in PCB design. Shielding involves enclosing sensitive components or circuits in a conductive enclosure to prevent EMI from entering or exiting the device. There are several types of shielding that can be used in PCB design, including:
- Metal enclosures or cans that completely enclose the PCB or sensitive components
- Conductive gaskets or tapes that provide a conductive seal around openings in the enclosure
- Conductive coatings or paints that can be applied to the inside of plastic enclosures to provide shielding
3. Filtering
Filtering is another important strategy for minimizing EMI in PCB design. Filtering involves adding passive or active components to the circuit to attenuate unwanted high-frequency signals. There are several types of filtering that can be used in PCB design, including:
- Decoupling capacitors placed near power pins of ICs to filter high-frequency noise on power supply lines
- Ferrite beads or inductors placed in series with signal lines to attenuate high-frequency noise
- EMI filters placed on input/output lines to attenuate high-frequency noise entering or exiting the device
4. Proper Layout Techniques
Proper layout techniques are also critical for minimizing EMI in PCB design. Some key layout techniques to consider include:
- Minimizing loop areas by keeping signal traces as short and direct as possible
- Avoiding routing high-speed signals near the edge of the PCB or near other high-speed signals
- Using differential signaling for high-speed signals to cancel out EMI
- Separating analog and digital circuits to minimize crosstalk and other interference
5. Simulation and Modeling
Simulation and modeling tools can be used to predict and analyze EMI in PCB designs before they are fabricated. These tools can help identify potential EMI issues early in the design process, allowing you to make changes to the design to minimize EMI. Some common simulation and modeling tools used in PCB design include:
- Electromagnetic field solvers that can simulate the fields generated by PCB traces and components
- Circuit simulators that can analyze the behavior of the circuit under different operating conditions
- 3D modeling tools that can help visualize the physical layout of the PCB and identify potential EMI issues
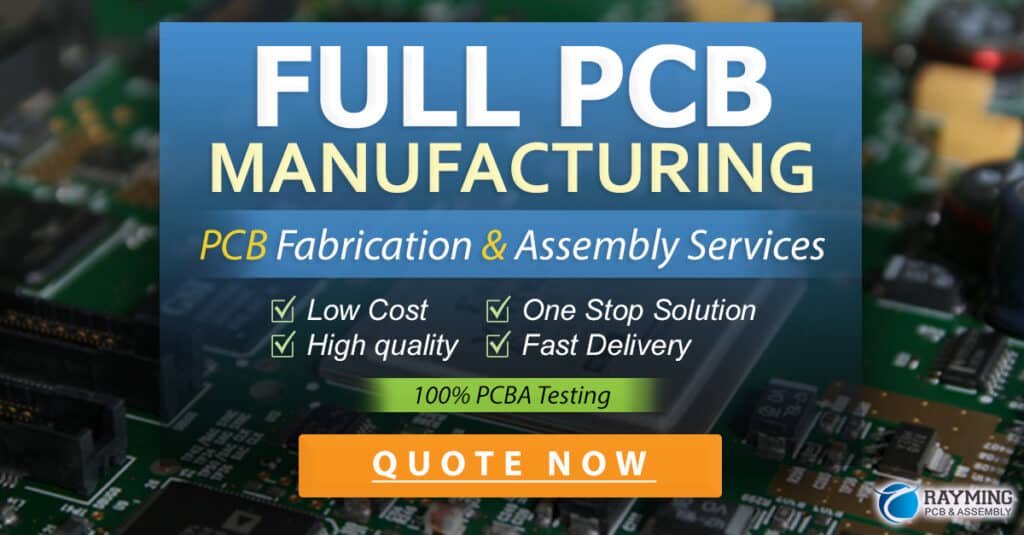
EMI Testing and Compliance
Once your PCB design is complete, it is important to test it for EMI compliance before releasing it to market. There are several types of EMI testing that can be performed, including:
- Radiated emissions testing, which measures the electromagnetic fields emitted by the device
- Conducted emissions testing, which measures the electromagnetic energy conducted along power and signal lines
- Susceptibility testing, which measures the ability of the device to operate correctly in the presence of external EMI
To ensure compliance with EMI regulations, it is important to work with a certified testing lab that has experience with the specific regulations and standards that apply to your industry and product.
FAQ
-
What is the difference between EMI and EMC?
EMI (electromagnetic interference) refers to the unwanted generation of electromagnetic energy that can interfere with the operation of electronic devices. EMC (electromagnetic compatibility) refers to the ability of an electronic device to operate correctly in the presence of EMI and to not generate EMI that can interfere with other devices. -
What are some common sources of EMI in PCB design?
Common sources of EMI in PCB design include switching power supplies, high-speed digital circuits, and unshielded cables or connectors. Other sources can include external factors such as nearby electronic devices or power lines. -
What is the purpose of a ground plane in PCB design?
A ground plane is a large area of copper on one or more layers of the PCB that is used to provide a low-impedance return path for current. The ground plane helps to minimize EMI by providing a stable reference voltage for signals and by minimizing the loop area of current paths. -
What is the difference between shielding and filtering?
Shielding involves enclosing sensitive components or circuits in a conductive enclosure to prevent EMI from entering or exiting the device. Filtering involves adding passive or active components to the circuit to attenuate unwanted high-frequency signals. -
What are some common EMI regulations and standards?
Some common EMI regulations and standards include the FCC (Federal Communications Commission) regulations in the United States, the CE (Conformité Européenne) marking in Europe, and the CISPR (Comité International Spécial des Perturbations Radioélectriques) standards used in many countries. The specific regulations and standards that apply to a particular product will depend on the industry and intended market.
Conclusion
EMI is a common issue in PCB design that can cause significant problems if not addressed early in the design process. By using strategies such as proper grounding, shielding, filtering, proper layout techniques, and simulation and modeling, you can minimize EMI in your PCB designs and ensure that your products meet regulatory requirements and perform optimally. Remember to work with a certified testing lab to ensure compliance with EMI regulations and standards before releasing your product to market.
Strategy | Description |
---|---|
Proper Grounding | Using a solid ground plane and connecting all ground pins to minimize ground loops and provide a low-impedance return path for current |
Shielding | Enclosing sensitive components or circuits in a conductive enclosure to prevent EMI from entering or exiting the device |
Filtering | Adding passive or active components to the circuit to attenuate unwanted high-frequency signals |
Proper Layout Techniques | Minimizing loop areas, avoiding routing high-speed signals near edges or other high-speed signals, using differential signaling, and separating analog and digital circuits |
Simulation and Modeling | Using electromagnetic field solvers, circuit simulators, and 3D modeling tools to predict and analyze EMI before fabrication |
By following these strategies and working with experienced professionals, you can minimize EMI issues in your PCB designs and ensure the success of your electronic products.
Leave a Reply